Abstract
Objective
The compliance for tooth cavity preparations is not yet fully described in the literature. Thus, the objectives were to present a finite element (FE) method for calculating compliance and to apply this to peak shrinkage stress regions in model cavities restored with resin-composite.
Methods
Three groups of FE-models were created, with all materials considered linear, homogeneous, elastic and isotropic: (a) a pair of butt-joint bonded cubic prisms (dentin/resin-composite), with dentin of known compliance (0.0666 μm/N). Free ends were fixed in the Z -axis direction. A 1% volumetric shrinkage was simulated for the resin-composite. Mean displacements in the Z direction at each node at the dentin–resin interface were calculated and divided by the sum of normal contact forces in Z for each node. (b) A series of more complex restored cavity configurations for which their compliances were calculated. (c) A set of 3D-FE beam models, of 4 mm × 2 mm cross-section with lengths from 2 to 10 mm, were also analyzed under both tensile and bending modes.
Results
The compliance calculated by FEM for the butt-joint prisms was 0.0652 μm/N and corresponded well to the analytical value (0.0666 μm/N). For more accurate representations of the phenomenon, such as the compliance of a cavity or any other complex structure, the use of the displacement–magnitude was recommended, as loading by isotropic contraction also produces transversal deformations. For the beam models, the compliance was strongly dependent upon the loading direction and was greater under bending than in tension.
Significance
The method was validated for the compliance calculation of complex structures subjected to shrinkage stress such as Class I ‘cavities’. The same FEM parameters could be applied to calculate the real compliance of any interface of complex structures. The compliance concept is improved by considering specific load directions.
1
Introduction
The stress magnitude in restored teeth developed by restorative material shrinkage depends upon several factors: the shape of the cavity; the magnitude and the load application mode; the mechanical properties of the substrate (enamel and dentin) and the restorative material; and the compliance of the substrate. Efforts have been made to investigate these factors and understand their interfacial stress magnitude . The shrinkage stress seems to be lower if the restoration has a higher ratio of unbonded/bonded area. This concept is already expressed by the relationship between C-Factor and stress . The influence of the resin-composite mass, or equivalently the volume was also reported (the higher the volume, the higher the stress) .
Compliance is the inverse of stiffness and it is dependent upon several other characteristics of the substrate (teeth) and the resin-composite properties, including the elastic modulus. In general, elastic modulus is not the same as stiffness as first it is a property of the constituent material, while stiffness is a property of a structure, and it is thus dependent on the material and the shape and boundary conditions. It is therefore evident that the compliance is not a material property, nor a simple combination of material properties and the shape of the object. In solid mechanics it may be defined as the ratio of strain to stress, and so takes the units of reciprocal stress. Considering the substrate structural deformability, both C-Factor and resin-composite mass or volume would be the main influences on the substrate compliance: if the substrate was only slightly deformable, the increase of the stress might well correlate with the C-Factor; if the compliance was higher, the resin-composite volume would better correlate with the stress . A correlation between the C-Factor and microleakage has also been identified by some authors , but there is still controversy because there are cases where this correlation was absent. In these last cases, the authors suggest that an increase of the cavity preparation size (volume) and the C-Factor (which would increase the stress) would act in opposite directions .
Evaluating the cavity compliance as a single number remains a challenge ( Fig. 1 ), since the deformability of a structure is not uniform and depends on its geometry, elastic modulus and the remaining structure as well as the loading direction to which the structure is subjected. In tensilometers, the axial compliance of the system, the inverse of stiffness, is defined as the ease of separating its parallel walls (expressed in μm/N), that is: the axial elongation of the substrate divided by the load developed by the shrinkage of the composite. In this definition, any non-aligned stress is ignored and the higher the compliance of the system, the lower is the shrinkage stress expected. Specimens of the same composite with identical dimensions will develop different stresses if measured under different conditions of tensilometer compliance. Each region of each wall will present its own compliance. While it is possible to obtain the compliance for specimens subjected to tensilometer measurements that apply only axial loading, for cavity preparations restored with resin-composites under shrinkage, loadings and displacements will occur in multiple directions, which cannot therefore be expressed as a single value. Table 1 presents low and high compliance data from previous studies. The range of these values suggests there is no single characteristic value that can be extrapolated as the compliance of each cavity.

Low compliance | 9.9 × 10 −3 μm/N (glass rod – tensilometer) |
High compliance | 0.15 μm/N (PMMA – tensilometer) 3.34 μm/N (cusp) |
The compliance in cavities has not been properly identified, because there was no agreed method for its calculation. However, the cuspal deflection associated with cavity walls has been used as a parameter of compliance and thus an indicator of shrinkage stress at the dentin/composite interface (but only for comparing cases of cavities with the same compliance) . For any tooth, with a complex geometry, it is difficult to isolate the compliance as a variable in experimental measurements. So, the extrapolation of results from studies using tensilometers to clinical reality has to be done with caution .
It would be valuable to find a method for calculating substrate compliance for predicting the stress generated in a real case. Neither the compliance nor the stress is uniform over the entire cavity preparation so minimally we need to know at least the compliance of the region subjected to maximum stress (stress peak). The test hypotheses of this study were: (i) the compliance calculated by FEM is comparable to the compliance calculated analytically and (ii) if the first hypothesis is confirmed, the FE method used to calculate the compliance of a cubic prism of dentin bonded to a composite can be also used to estimate the compliance and the peak stress in model ‘cavity’ preparations restored with resin-composite.
2
Materials and methods (I): FE analysis of a pair of bonded (dentin/composite) cubic prisms
Compliance is usually calculated analytically from experimental load and displacement measurements, considering the object dimensions. A 3D-FE model was created of a cubic dentin prism (1 × 1 × 1 mm 3 ) with defined compliance (0.0666 μm/N) bonded to a same sized resin-composite prism. This was performed by using MSC.Patran ® (pre- and post-processor) and MSC Marc ® (post-processor) to calculate the compliance numerically from the displacement and load information for a group of nodes ( Fig. 2 ). The model was obtained by the uniform extrusion of 2D four-node quadrilateral elements ( Quad 4 ) in the Z axis of the global coordinate, generating 350 eight-node hexagonal elements ( Hex 8 ), and 576 nodes (determined by a mesh convergence test). The resultant edge length for all elements was approximately 0.15 mm. For the prism pair, the lower half represented dentin (the bonding substrate) and the upper half was resin-composite ( E = 21 GPa), mutually bonded via a butt joint (FE-glue contact). This condition established perfect bonding at all interfacial nodes of the two contact bodies (dentin and composite).
Nodes corresponding to the top and bottom faces of the prism (dentin + composite) pair were fixed in the Z direction. One of the nodes of the bottom (indicated by the red arrow in Fig. 2 ) was considered totally constrained. Simulation of polymerization shrinkage of the resin-composite was performed by using the thermal analogy. A thermal-expansion coefficient of 3.33 × 10 −3 °C −1 , associated with a temperature drop of 1 °C produced a 1% volumetric shrinkage .
As already mentioned, compliance, by definition, is the inverse of stiffness. The axial (longitudinal) stiffness, k z , of the cubic prism is a measure of the resistance offered by the elastic body to deformation induced by an applied force. For an elastic body with a single degree of freedom (as for a cubic prism simulating the tensilometer condition), the stiffness is thus defined as:
k z = F z Δ L = ( A ) × ( E ) l 0
where F is the force applied on the cubic prism; Δ L is the displacement produced by the force along the same degree of freedom; A is its cross-sectional area and E is its elastic modulus and l 0 is the initial height of the dentin substrate.
The longitudinal compliance for the cubic prism of dentin is also defined analytically as the inverse of Eq. (1) :
C A = l 0 ( A ) × ( E )
where C A is compliance, l 0 is the initial height of the dentin substrate, A is its cross-sectional area and E is its elastic modulus.
The analytical compliance calculation for the dentin portion was then compared with the calculation made by FEM. The calculation made by FEM ( C FE ), was obtained by the mean displacements in each node at the dentin–resin interface in the axial ( Z ) direction ( <SPAN role=presentation tabIndex=0 id=MathJax-Element-3-Frame class=MathJax style="POSITION: relative" data-mathml='u¯z’>u¯zu¯z
u ¯ z
) divided by the sum of normal contact forces in the same Z direction ( <SPAN role=presentation tabIndex=0 id=MathJax-Element-4-Frame class=MathJax style="POSITION: relative" data-mathml='NCz’>NCzNCz
N C z
) for each node, as follows:
C F E = u ¯ z ∑ N C z
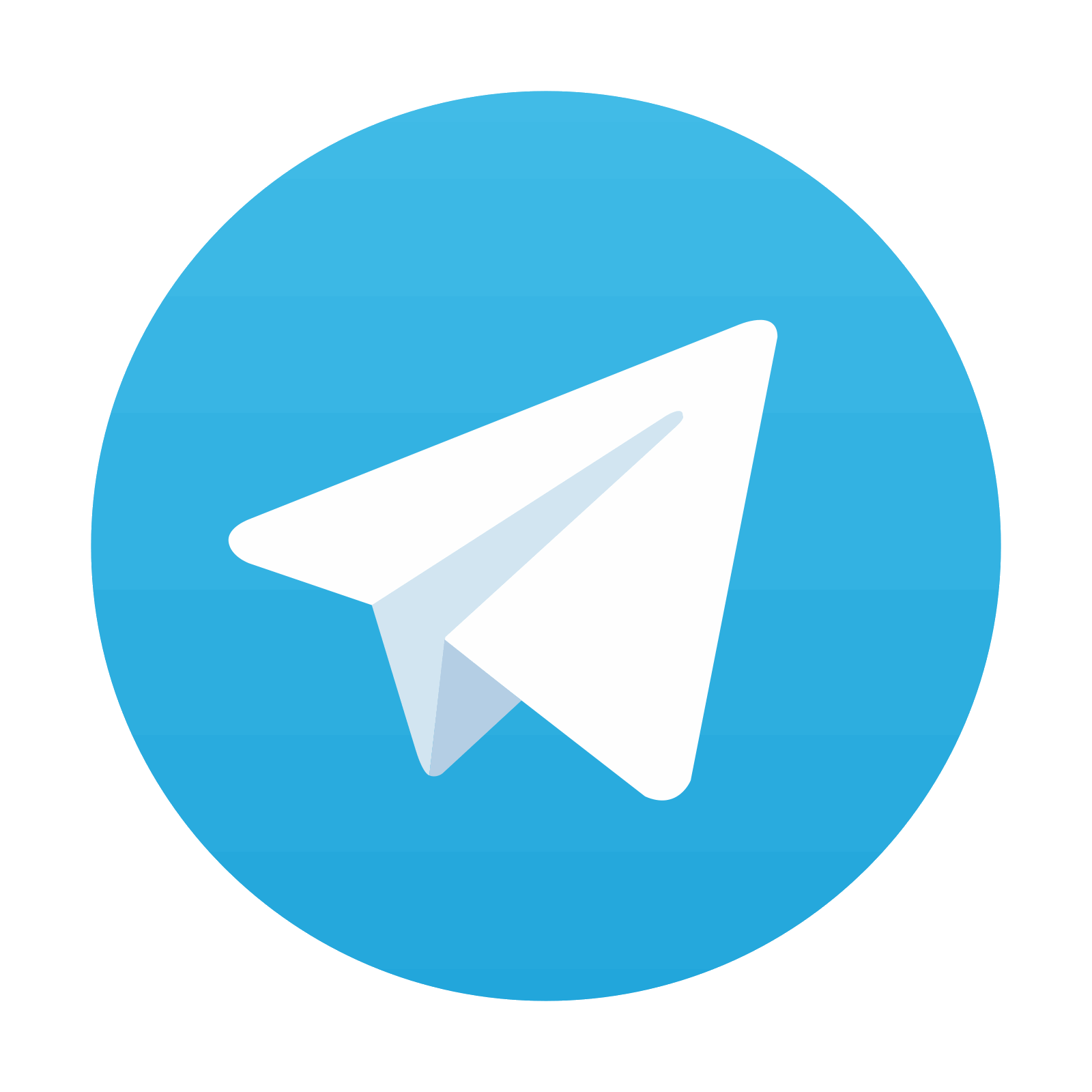
Stay updated, free dental videos. Join our Telegram channel

VIDEdental - Online dental courses
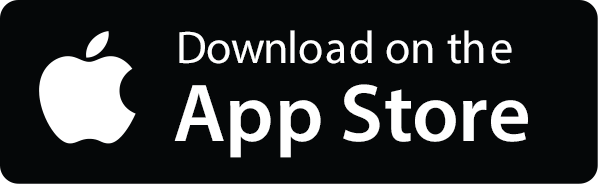
