Chapter 8
Dental cements
DEFINITION
A luting cement is a material that bonds, seals or cements objects together (Figure 8.1a–c). It should have low solubility, low viscosity and high fracture resistance. Luting cements are used in dentistry in order to cement crowns, bridges and appliances (e.g. orthodontic appliances) either temporarily or permanently. Depending on the needs of the treatment, the operator will choose the cement based on strength, antibacterial properties, ability to create a good marginal seal, ability to be used with an adhesive, solubility, tensile strength, resistance to wear, ease of manipulation, translucency and operator’s preference. There is not one luting agent that will meet the desired needs in all situations, hence the reason for a large number of products available for this use.
ZINC PHOSPHATE
Although zinc phosphate has a function as a base (see Chapter 7), it may also be used as a luting cement. It will be discussed in this context in this chapter.
Material constituents/composition
Powder | Liquid |
Zinc oxide | Phosphoric acid |
Magnesium oxide | Water |
Aluminium and zinc ions |
Properties
Once the powder and liquid are mixed together, heat is produced, i.e. an exothermic reaction takes place. This reaction speeds up the setting of the material. To control the setting of zinc phosphate, it should always be mixed on a cool, dry glass slab, and the whole surface area of the slab should be used during the mix to minimise heat production. The manipulation technique is very important, as a warm slab, mixing too fast, or contamination by water may speed up the setting time of the material. Incorporating the powder increments too fast or too slow will also affect the setting of zinc phosphate. Zinc phosphate is fast setting and has a moderate to high solubility and low acidity (once set). The pH is 1–2 but the acidity decreases over time (about 24 hours).
Figure 8.1 (a) Teeth prepared for crowns. (b) Crowns cemented in place with a luting cement. (c) Operator holding the crowns in place until the initial set of the desired luting cement. (Photos courtesy of Dr. Shuichitsubura).
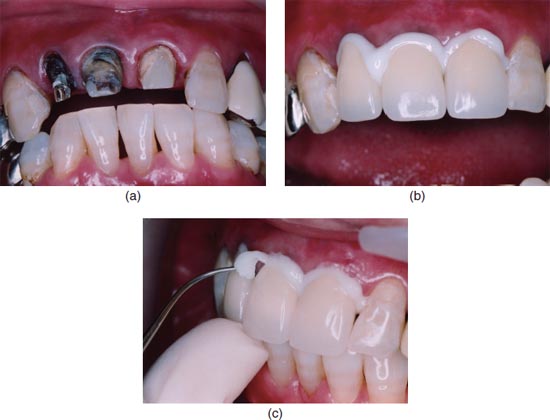
- Acidic
- Gives off an exothermic reaction (gives out heat when mixed)
- Strong material (reaches two-thirds of strength in less than one hour)
- May be used as a base (thicker mix) or a luting cement (thinner mix)
- Mixing times may be extended by mixing the material over a large surface area (dissipates the heat given off as a result of the exothermic reaction)
- Mixing on a cool glass slab can also extend the working time and allow for greater powder incorporation (gives the material a higher strength and reduces solubility)
- Care must be taken to not reduce the ratio of powder to liquid as this results in a more soluble, more irritant and weaker material
- 50% of the strength of the material is reached after 10 minutes, reaching its final strength after 24 hours
- Moderate solubility when used as a base and high solubility when used as a luting cement
Advantages
- Long shelf-life
- Low thermo-conductivity
- Rapid setting time
- Low cost
- Long clinical history
Disadvantages
- Does not release fluoride
- Freshly mixed material has a high acidity (reduces with setting), but has the potential to cause pulpal irritation
- Moisture sensitive
- Slight shrinkage during setting
- No adhesive properties
- Brittle
Indications and contraindications for use
Indications
- Permanent cementation of crowns, bridges, inlays, onlays, orthodontic appliances and orthodontic bands
Contraindications
- Zinc phosphate is acidic at the time of placement, and care should be taken to protect the pulp
Trade names
Trade name | Manufacturer |
DeTray® (Figure 8.2a) | Dentsply |
Flecks® (Figure 8.2b) | Keystone Group |
Zinc Cement (Figure 8.2c) | SSWhite |
Zinc Phosphate Cement (Figure 8.2d) | Bosworth |
Figure 8.2 (a) DeTray® – Dentsply. (b) Flecks® – Keystone group. (c) Zinc Cement – SS White. (d) Zinc Phosphate Cement – Bosworth.
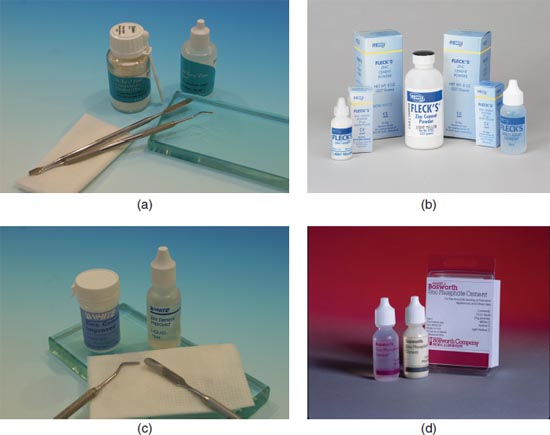
Manipulation (Figures 8.3a–8.3e)
This is the same manipulation technique as mixing zinc phosphate as a base, except with altered powder/liquid ratios, mixing times and final consistency.
Wearing personal protective equipment:
- Tooth is appropriately prepared and isolated
- Ensure you have a clean, disinfected, cool, dry glass mixing slab
- If the chosen method is to cool the glass slab under cold water, ensure that all moisture is removed prior to dispensing materials
- Fluff the zinc phosphate powder in the bottle (shake the bottle, ensuring the lid is securely in place)
- Dispense the powder on the glass slab according to the manufacturer’s instructions, replacing the cap immediately after dispensing
- Dispense liquid as per the manufacturer’s instructions, according to the appropriate amount of powder dispensed (more liquid is added for a luting consistency than a base)
- To ensure uniform drops of the liquid, hold the bottle perpendicular to the glass slab during dispensing and immediately replace the cap
- Care must be taken to replace the cap on the liquid once it has been dispensed. The zinc phosphate material is water based, and the water will evaporate if the cap is left off, which will prolong the setting time
- Section powder into increments according to the manufacturer’s instructions (two techniques are shown)
- Mix in powder increments at 15-second intervals
- Using a Weston spatula (thin, flexible spatula) incorporate the first mound of powder into the liquid, spatulating in a figure-of-eight motion over the entire surface area of the slab for 15 seconds
- Ensure that all the powder has been incorporated into the liquid and add the second powder increment, following the same mixing technique for 15 seconds
- Repeat steps 5 and 6 until you have achieved the desired creamy consistency (the mixed material should form a ‘string’ from the spatula to the glass slab when the spatula is lifted approximately an inch (2 cm) above the glass slab)
- Using the spatula, gather the material into one area and use a flat plastic instrument to load the restoration or prosthesis to be cemented under the direction of the operator, alternatively pass the material and the flat plastic instrument to the operator for loading
- Have some gauze at hand to wipe away excess cement from the flat plastic instrument
- Immediately clean the spatula and glass slab; if there is not enough time to clean immediately, immerse the slab and spatula in water until cleaning can take place
- 60–90 seconds
- 3–6 minutes
- 5–14 minutes
Figure 8.3 (a) Zinc phosphate set-up. (b) Step 4 – Zinc phosphate dispensed – powder divided into six equal portions. (c) Step 4 – Zinc phosphate dispensed – powder divided into fractional portions (8.3b and 8.3c are two different techniques for dispensing zinc phosphate powder). (d) Step 5 – figure-of-eight mixing motion. (e) Step 7 – luting consistency of zinc phosphate (2cm ‘string’ from glass slab to spatula).
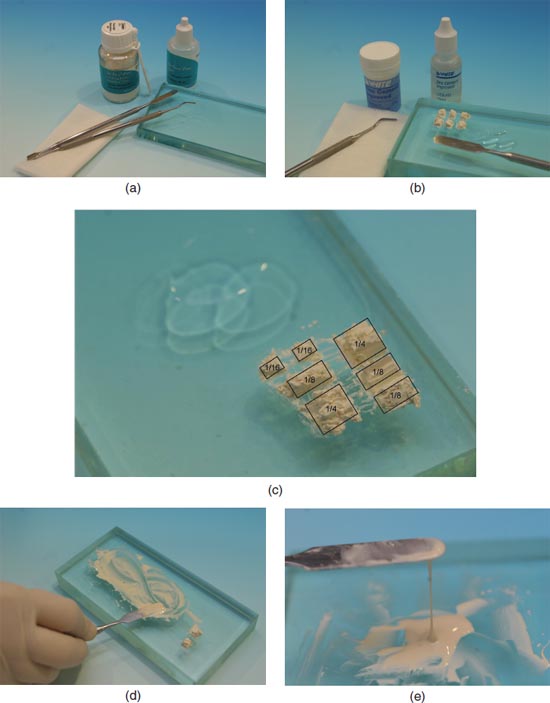
Instruments and materials used in set-up
- Zinc phosphate powder and liquid
- Weston spatula
- Cool, dry glass slab
- Gauze
- Flat plastic instrument
POLYCARBOXYLATE CEMENTS (ZINC POLYCARBOXYLATE CEMENTS)
Polycarboxylate cement is a derivative of zinc phosphate cement in which the zinc phosphate has been replaced with a polyacrylic acid. It has the ability to bond to both enamel and dentine.
Material constituents/composition
Supplied in powder and liquid forms:
Powder | Liquid |
Zinc oxide | Polyacrylic acid |
Magnesium oxide | Water |
Properties
- Acceptable to mix polycarboxylate cement on either a waxed paper pad or a glass slab
- Mixing polycarboxylate cement on a cooled glass slab enables extension of the working time
- Reaches 80% of its final setting in one hour
- Do not store the liquid in the fridge as this will cause it to gel
Advantages
- Does not release fluoride, although some materials have added properties which allow fluoride release
- Bonds to enamel, dentine and alloys
- Low irritation
- Easy manipulation
Disadvantages
- Short mixing/working times
- Sensitive to manipulation techniques
- Lower compressive strength when compared to zinc phosphate
Indications and contraindications for use
Indications
- Cementation of metal crowns and bridges (also suitable for porcelain fused to metal crowns and bridges)
- Orthodontic bands and appliances
Contraindications
- Does not bond well to untreated gold restorations
Trade names
Trade name | Manufacturer |
Poly-F® Plus (Figure 8.4) (this material has | Dentsply |
added properties to release fluoride) |
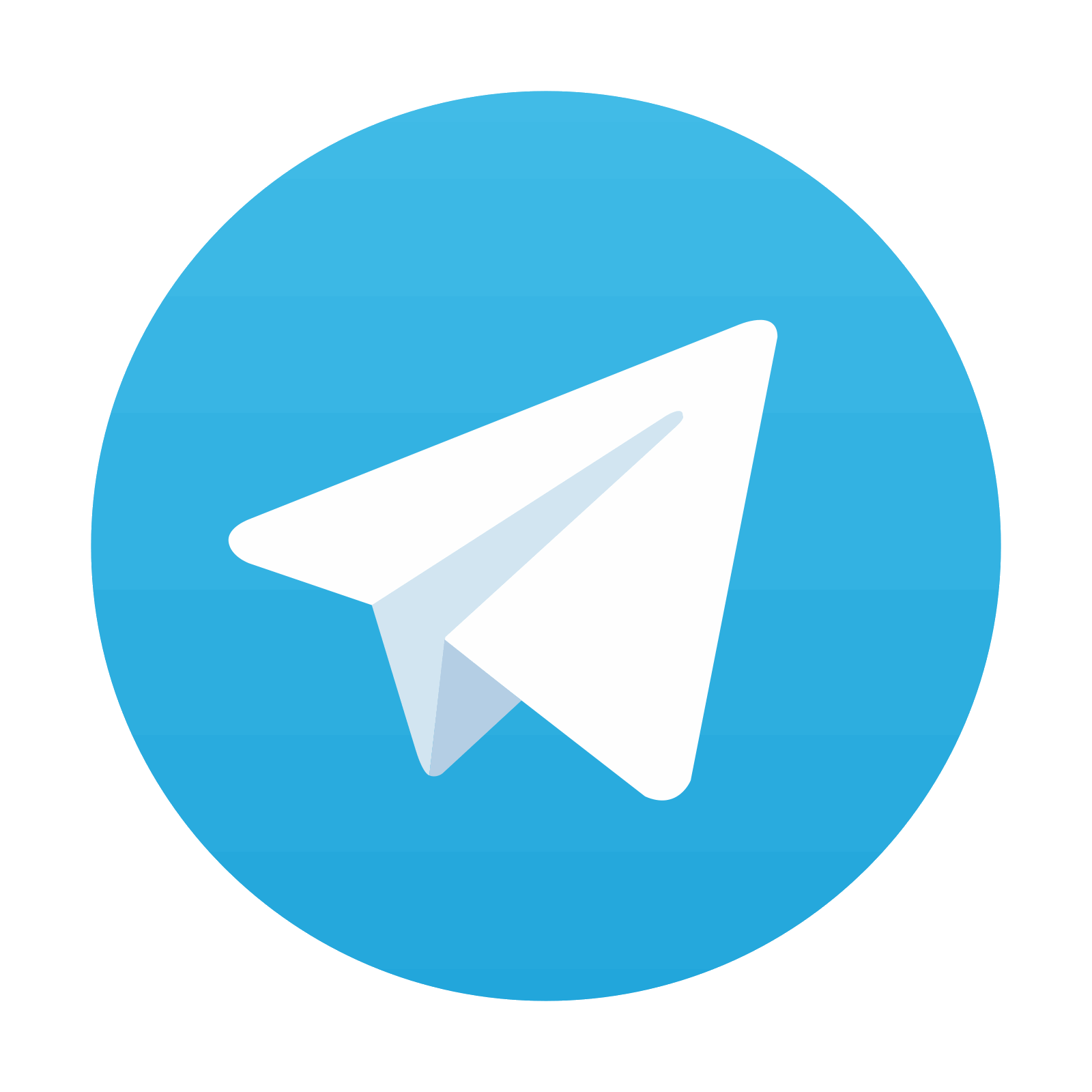
Stay updated, free dental videos. Join our Telegram channel

VIDEdental - Online dental courses
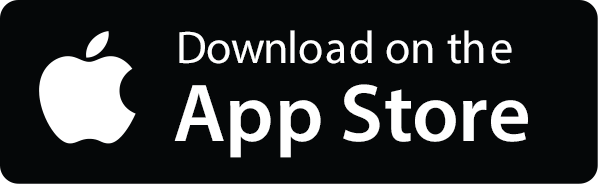
