Acrylic
Poly(methyl methacrylate) – so–called ‘acrylic resin’ – is usually the material of choice for full denture bases and ‘gumwork’ for removable devices. It has also been the chemical model for many other material developments in dentistry, such as restorative materials. The properties, behaviour and handling of poly(methyl methacrylate) likewise form a basis for understanding those other materials.
A polymerization reaction is performed as part of the normal dental procedures in the laboratory, and the proper control of this is important for controlling the properties of the product. It is essential to understand both the heat-cured and cold-cured types, whose properties and limitations differ because of their processing differences.
Since the methyl methacrylate monomer is a very reactive compound, storage is a problem. Its chemistry has a bearing on a number of issues.
The mechanical properties are the ultimate concern in determining suitability to task, and the relationship of these to processing and service conditions are clearly important. This topic is dependent on the special behaviour of polymers. The properties of the plain product are not ideal, however, and various modifications to the chemistry are possible to obtain better behaviour.
Dental acrylic resin represents a case study in polymer science of wide interest in itself. Even so, there are many points which are relevant in other dental materials contexts, and a grounding in this type of product as a model is therefore essential to the understanding of the more advanced and complicated materials which are, in a very direct sense, derived from it.
Polymers based on methyl methacrylate, broadly termed ‘acrylic resins’, are used in very large quantities for full denture base fabrication and for adding ‘gum work’ to cast metal frameworks. Indeed, despite much effort to find alternatives with better properties, it remains essentially the only polymer system in current use for these applications. In modified forms, such polymers may be used as direct restoratives, denture repair materials, soft liners and denture teeth. Whilst plain poly(methyl methacrylate) or ‘PMMA’ is a typical polymer in many mechanical and physical respects, it can be considered the archetype for a very large number of related products as many aspects of its chemistry are relevant in those as well. Indeed, its importance in dentistry is such that it warrants detailed treatment.[1]
§1 Polymerization Reactions
•1.1 Initiation
Acrylic resins are prepared by a free radical addition polymerization chain reaction, where the opening of one double bond results in the formation of another free radical which can attack and join at another double bond, resulting in yet another free radical. The mechanism is straightforward. The vinyl group of methyl methacrylate is susceptible to attack by a free radical, resulting in the opening of the π-bond, the formation of a new σ-bond to one carbon, and the creation of a lone (that is, unpaired) electron on the central carbon atom (Fig. 1.1); this constitutes the initiation reaction in the sense that the polymerization chain has been started. The attack is selective on the more-exposed carbon atom, as opposed to that leading to a terminal position for the free radical electron. This is driven by the steric hindrance of the methylcarboxyl and methyl groups – it is simply easier to get at. It is conceivable that some attacks may take the less-favoured route, and indeed a small proportion do, since collisions are random and not ‘intentional’. However, the resulting radical is also extremely unstable and suffers a rapid reaction, probably by hydrogen abstraction (§1.4), so that it is not a significant species in the overall chain reaction.
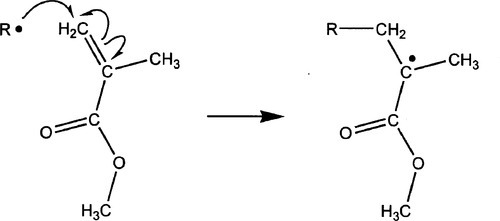
•1.2 Propagation
The new free radical is equally capable of attacking another double bond in exactly the same way, and the resulting radical another bond, and so on. This process of repeated reaction of the same type is termed chain propagation (Fig. 1.2). It can be seen that because of the bulk of the parts of the molecule surrounding the new lone electron, steric hindrance effects for attack on the next double bond are now even greater, and it may be supposed that nearly all attacks now result in the methyl methacrylate residues being linked by methylene bridges, -CH2-. Polymer chains carrying an active free radical in this way are termed growing or live chains.
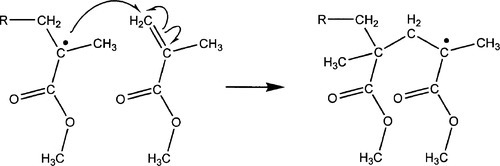
•1.3 Termination
Chain termination can occur at any time. It is not a direct function of the chain length already created (which cannot affect the reactivity of the radical nor be ‘seen’ by incoming monomer or radical), but it depends on the concentration of free radicals in the system. This step, which accounts for the self-limitation of the reaction, is the simple mutual annihilation of two free radicals which happen to come close enough together (Fig. 1.3). This could be as easily by another chain as another initiator radical. There is a third possibility.
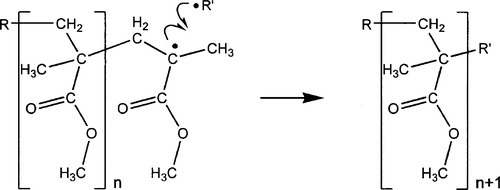
•1.4 Chain transfer
Free radicals tend to be high energy, reactive species, and one of the reactions that may occur in systems such as this is hydrogen abstraction. This is the simple transfer of a hydrogen atom, from nearly anywhere at all, to the attacking radical. Of course, this leaves a free radical residing on the attacked species, which may then itself go on to attack methyl methacrylate double bonds. The important thing about this kind of reaction is that the hydrogen may have been removed not just from a monomer molecule but from any of the possible sites on existing polymer, such as the esteric methyl group. In this case, a branch will have been introduced into the polymer chain, the active site then continuing to propagate as before to create a new polymer chain. Since one chain is stopped, and another begun, this process is called chain transfer (Fig. 1.4). This random reaction tends to limit the average chain length that may be obtained in the final product.
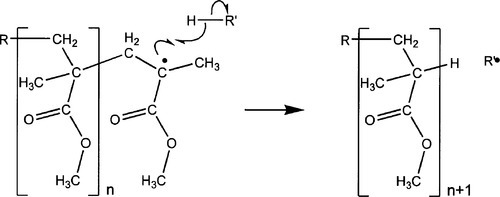
•1.5 Tacticity
When, as is usual for the steric reasons mentioned above, the result of attack on the monomer is a free radical residing on the central carbon atom, there are two possible outcomes to the next step, depending on which ‘side’ of that atom the single electron happens to be lying at the time that it attacks the next double bond (Fig. 1.5). Bear in mind that the free radical part, which has sp3-hybridized orbitals in a the usual tetrahedral arrangement (Fig. 3§2.1), will naturally be ‘flipping’ back and forth between the two forms (as well as rotation about the bond to the carboxyl group) at a very great rate. The configuration is easily invertible to its mirror image because the lone electron is mobile. So, even if there is a preference initially (which is unlikely), there will soon be a scrambling and equal numbers of both forms available for attack. The free radical species is asymmetric (3§2.2), and so therefore must also be the result of attack on the next double bond. There is no steric guidance operating in this system, and the resulting polymer is therefore atactic (3§2.3). This prevents crystallization, but it also affects the glass transition temperature of the resulting polymer. For anhydrous PMMA, the Tg has the following values: isotactic, ~ 60 °C; atactic, ~ 110 °C, syndiotactic, ~ 130 °C. This indicates the subtleties of the interplay between chain packing (and thus free volume) and ease of chain segment rotation, bearing in mind that the molecule is polar and so has appreciable intermolecular interactions.
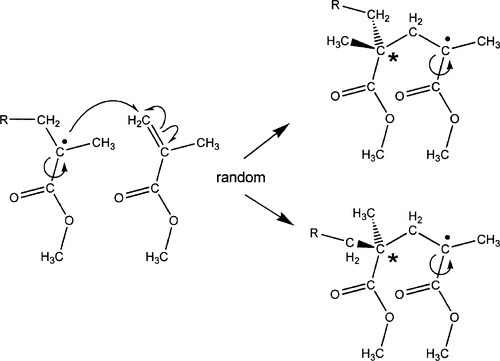
In addition to the tacticity issue, the fact that the site of attack can vary, as indicated in §1.1, albeit heavily biassed, means that there is a further source of irregularity in the chain. Chain transfer reactions can also lead to branching and other irregularity. PMMA as used in dentistry therefore does not – and cannot – crystallize.
The question that has not been addressed is, how to start the process of polymerization? The identity of that first radical has not been stated. What is apparently required is a reaction initiator.
§2 Heat-cured Acrylic
As is commonly the case in many such practical polymerization systems, the reaction for the resins used for dentures is generally initiated by benzoyl peroxide1 (Fig. 2.1) (often abbreviated ‘BPO’). The central O-O bond is weakened by the electron-withdrawing power of the adjacent oxygen and carbonyl groups. Thus, this compound readily dissociates simply on heating to produce a pair of benzoate (or, benzoyloxy) radicals. These are themselves not very stable, and will break down further. Even at room temperature, solutions of this compound slowly liberate carbon dioxide and produce phenyl radicals in the process. Either of these radicals – benzoate or phenyl – may attack any compounds that are available, extracting hydrogen atoms and creating a new radical in the process. It will be seen later that the phenyl radical will not be very effective in such reactions, due to delocalization. However, the most important reaction, and the one that proceeds most readily in the present context, is the attack on one carbon atom of the acrylic double bond, which results in an unpaired electron on the second carbon atom. This, in turn, is more likely to attack another double bond although, as we have seen, chain transfer and termination reactions can also proceed. Although benzoyl peroxide does dissociate at room temperature, the rate is too low to be of practical use and heating must be used to generate radicals at a sufficiently high rate that the polymerization occurs within a suitably short time. This then is the basis of the normal dental laboratory process for preparing acrylic devices – and why such products are commonly referred to as heat-cured acrylic.
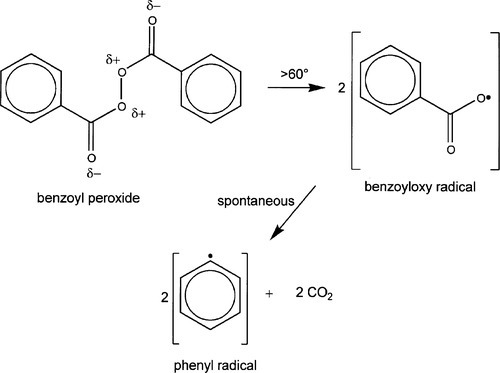
•2.1 Manufacture
This reaction is also the basis of the industrial manufacture of denture acrylic powders, a process often called emulsion polymerization, but more accurately suspension polymerization. A suspension of methyl methacrylate is prepared and maintained in water containing some surfactant (10§8) by vigorous stirring to obtain very small globules. A small amount of benzoyl peroxide in solution in, say, ethanol is then added, the temperature raised slowly, with a reflux condenser fitted to the reaction vessel to prevent loss of the monomer. If the stirring is maintained properly and the concentration of monomer is not too high, the product which is filtered off, washed and then dried is a fine powder consisting of nearly spherical and nearly uniformly-sized polymer beads2.
•2.2 Laboratory technique
It is the same polymerization reaction that is used, in a slightly modified form, in fabricating a denture base. The supplied PMMA powder has had added to it a small amount of benzoyl peroxide. In this form it is stable more or less indefinitely, and such powders do not, therefore, spoil or ‘go off’. When the monomer is added to the powder to make the dough, the benzoyl peroxide dissolves slowly, but because the dissociation of benzoyl peroxide is so slow at room temperature, virtually no polymerization occurs during the normal preparatory stages. (However, the dough cannot be kept too long – it will eventually harden. The dissociation rate of benzoyl peroxide in solution at room temperature is not zero.) The changes that are observed in the dough result solely from the physical processes of the monomer dissolving in the resin beads and the resin dissolving, more quickly, in the monomer. Initially, the polymer beads are merely wet, giving the appearance of ‘wet sand’. As polymer dissolves in the monomer, so the viscosity of the liquid rises and the mixture becomes sticky. As the concentration of dissolved polymer continues to rise so this stickiness is lost. Meanwhile, some monomer dissolves in the polymer, and although these particles are plasticized by that, the presence in the fully-cured resin of spherical structures identifiable as the original beads shows that they are not destroyed by the manipulation of the dough. The mutual solution of the two components assists in obtaining a good bond between them by entanglement, in addition to the covalent bonds that would be obtained by chain transfers.
•2.3 Mixing volume
It is usually said that when making up an acrylic dough enough monomer should be present to completely ‘wet’ the polymer powder. A little thought will show that this is quite incorrect: only a very little monomer is in fact required actually to wet the surface of even a fine powder, if wetting means to create a continuous film of a liquid on a surface (cf. 2§2.5). What must be meant, and what is clearly required in this context to minimize the porosity in the final product, is that the free space in the bulk powder be completely filled by liquid: that is, the gauging volume must be supplied so that the bulk powder is saturated (2§2.5). However, systems such as this are still dilatant (4§7.6), despite the spherical particles (Fig. 2.2). This arises because to move any single particle past another it must “rise up” slightly. This means that adjacent particles must on average be moved further apart than their equilibrium, ‘settled’ positions. Some dilution may also be necessary to obtain sufficient plasticity in the dough. The minimum mixing volume is necessarily a little larger than the gauging volume (2§2.4). But this begs the question of why powder and liquid are used in these systems. There are two main reasons.
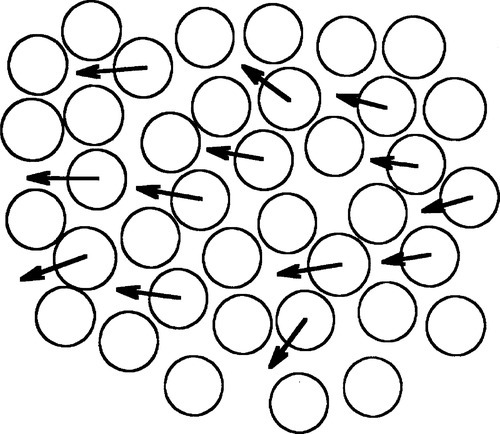
•2.4 Shrinkage
Firstly, polymerization shrinkage is reduced. Each single monomer molecule has an effective volume, due to its thermal motion, larger than its actual size (Fig. 2.3). However, a monomer residue – a mer – at a polymer chain end is less free to move because of the chain to which it is attached; its corresponding free volume is therefore less than that of the equivalent unreacted monomer molecule. Thus, for each new bond formed (i.e., each mer added to the chain), there is a reduction in the total free volume in the mixture. In the case of PMMA, the total change in volume which occurs with complete polymerization from pure monomer amounts to some 21% of the original volume (22.5 mL/mol). Such a shrinkage would be very difficult to handle in practical denture base moulding. Hence, the more polymerization that can be done before moulding, the better. However, the commonest industrial method for fabrication with polymers, injection moulding (where the material injected is all polymer, no monomer), has so far quite failed to produce a viable denture under dental laboratory conditions, the construction of a strong enough mould with sufficient accuracy being a major problem. The practical compromise used in dentistry is to mix polymer and monomer, then polymerize the monomer. The ratio of the two is limited by the minimum mixing volume requirement, so the best that can be achieved in practice is a net volumetric shrinkage of about 6 or 7%. Denture fabrication techniques must take this into account.
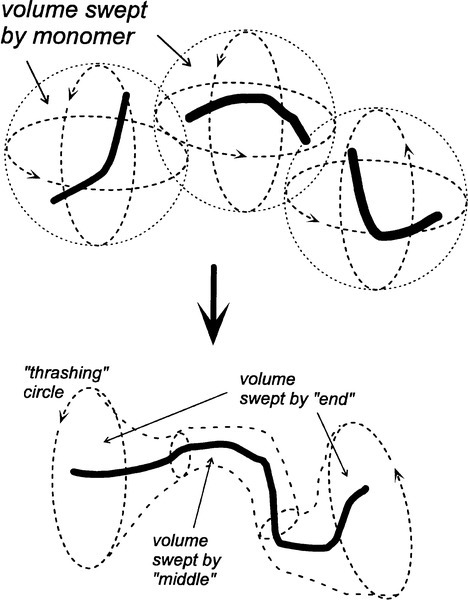
•2.5 Heat dissipation
Secondly, by reducing the number of covalent σ-bonds to be made, the amount of heat to be dissipated is reduced in proportion. The C-C σ-bond has an energy of about 350 kJ/mol, while the π-bond is at about 270 kJ/mol; thus some 80 kJ/mol would be expected to be evolved as heat on polymerization (in fact, the actual figure is about 56 kJ/mol because other factors are involved as well, but this is still substantial). Thus, by using a proportion of polymer in the mixture, the risk of overheating and the amount of thermal contraction to be experienced are both reduced as well.
Other reasons which could be cited, such as the ease of handling a plastic mass as opposed to a mobile, volatile liquid; avoidance of mould leakage problems; absence of the need to handle benzoyl peroxide (a strong oxidizing agent) in bulk or high concentration, are all important but are of less practical significance than the main two. All such considerations, to a greater or lesser extent, apply to cold-cure materials as well, including direct restorative (filling) materials.
•2.6 Heating
The polymerization reaction is activated by immersing the packed flask in water and raising its temperature. As indicated above, the reaction is strongly exothermic, and because the thermal conductivity of acrylic material is low (as is that of the gypsum mould) there comes a point in the heating of the dough when more heat is being produced by the reaction than can be conducted away (Fig. 2.4)[2]. Since the decomposition of the peroxide is an activated process, the rate has an Arrhenius-like dependency on temperature, and the ensuing rise in temperature accelerates the reaction further. The temperature of the mixture therefore rises very quickly. Notice that initially the flask and the dough are at successively lower temperatures than the external water bath, limited by the rate of conduction of heat inwards. But at about 70 °C the reaction rate becomes so high that the reaction ‘runs away’ and the internal temperature may reach 130 °C or more. This is potentially undesirable for two reasons:
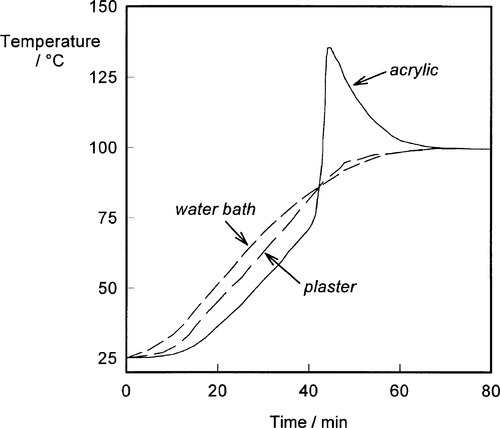
• The stresses induced in the now-solid polymer as it cooled again might result in severe distortion of the denture.
Accordingly, several steps are taken to avoid these problems. The first is the controlled heating of the flask (Fig. 2.5). As the heating rate of the flask is reduced so the onset of the strongly exothermic ‘run away’ stage is delayed, allowing more reaction heat to be dissipated so that the peak temperature is reduced. By choosing a suitably low heating rate, the peak temperature can be controlled to just about 100 °C or less, although this depends on the thickness of the section (the thicker, the hotter). Alternatively, heating to only, say, 70 °C will limit the peak temperature, although this has other problems, as we shall see.
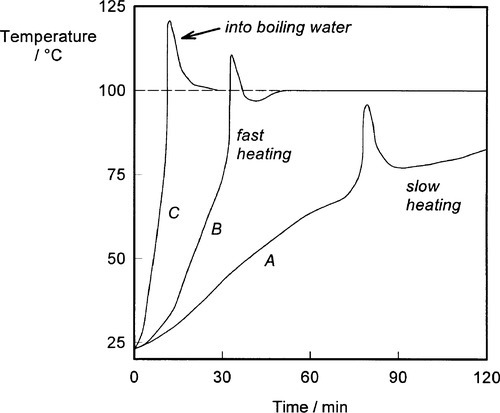
There is a simple solution to this first problem: pressure. The boiling point of a liquid is, by definition, the temperature at which its vapour pressure is equal to the local ambient pressure: raising the pressure raises the boiling point. This behaviour is described approximately by a form of the Clausius-Clapeyron equation:
< ?xml:namespace prefix = "mml" ns = "http://www.w3.org/1998/Math/MathML" />
where T1 is the (absolute temperature) boiling point at normal atmospheric pressure, P1, and T2 the boiling point at the pressure of interest, P2. Hvap is the heat of vaporization (37.5 kJ/mol), and R the molar gas constant. This is plotted in Fig. 2.6.
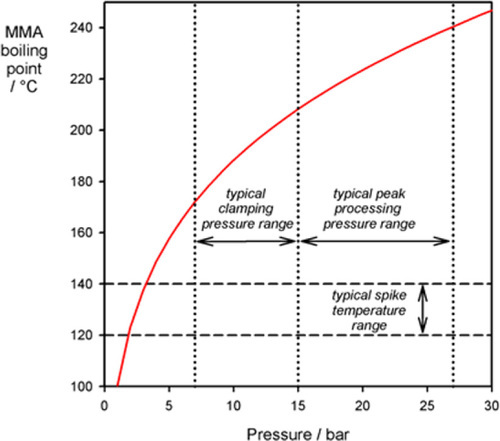
Since a denture base mould is normally overfilled somewhat, when this is clamped for processing the internal pressure can be elevated substantially, given that the flow of the very viscous dough through the very small space between the mould halves will be slow. The pressure increases further on heating due to the thermal expansion of the dough, which is over six times greater than that of the mould (Fig. 3§4.14; 18§4.7). Consequently, if the clamping is done properly, even the temperature spike from typically rapid heating will not cause porosity (Fig. 2.6).[3]
The clamping also ensures that the denture base remains constrained by the mould, minimizing distortion. Some stress relief occurs by viscous flow while the material remains above the glass transition temperature.
•2.7 Residual monomer
It is important to recognize that polymerization is not complete once the exotherm has passed. It has long been known that there is always residual monomer present in processed acrylic.[4] There are two factors operating here. Firstly, as in any simple chemical reaction between two species, the concentration of each is important. Thus, the concentration of free radicals [R•] and the concentration of monomer [M] need to be considered, the rate of reaction being expected to depend on the product of the two: [R•][M]. But, of course, the value of [M] is falling steadily as reaction occurs, and [R•] also falls because of termination reactions (§1.3). However, the viscosity of the medium is rising as the degree of polymerization increases and simultaneously the plasticizing effect of monomer is decreasing as [M] falls. Hence, the diffusion of monomer becomes the rate-limiting step as this is essential for reaction to occur: the live polymer ends are more or less fixed in location because they have very limited diffusibility. As diffusion is an activated process, it is temperature-dependent (3§3.3), and it takes time for any such reaction to approach completion. We can expect, therefore, at a given temperature, that the concentration of monomer falls asymptotically; to a first approximation this would be in the form of a declining exponential (similar to that of Fig. 11§2.9).
Free-radical polymerization is, however, not a one-way, irreversible process. It is in fact an equilibrium:
and the equilibrium concentration of monomer is temperature-dependent because the rate constants, k, are for activated processes (Fig/>
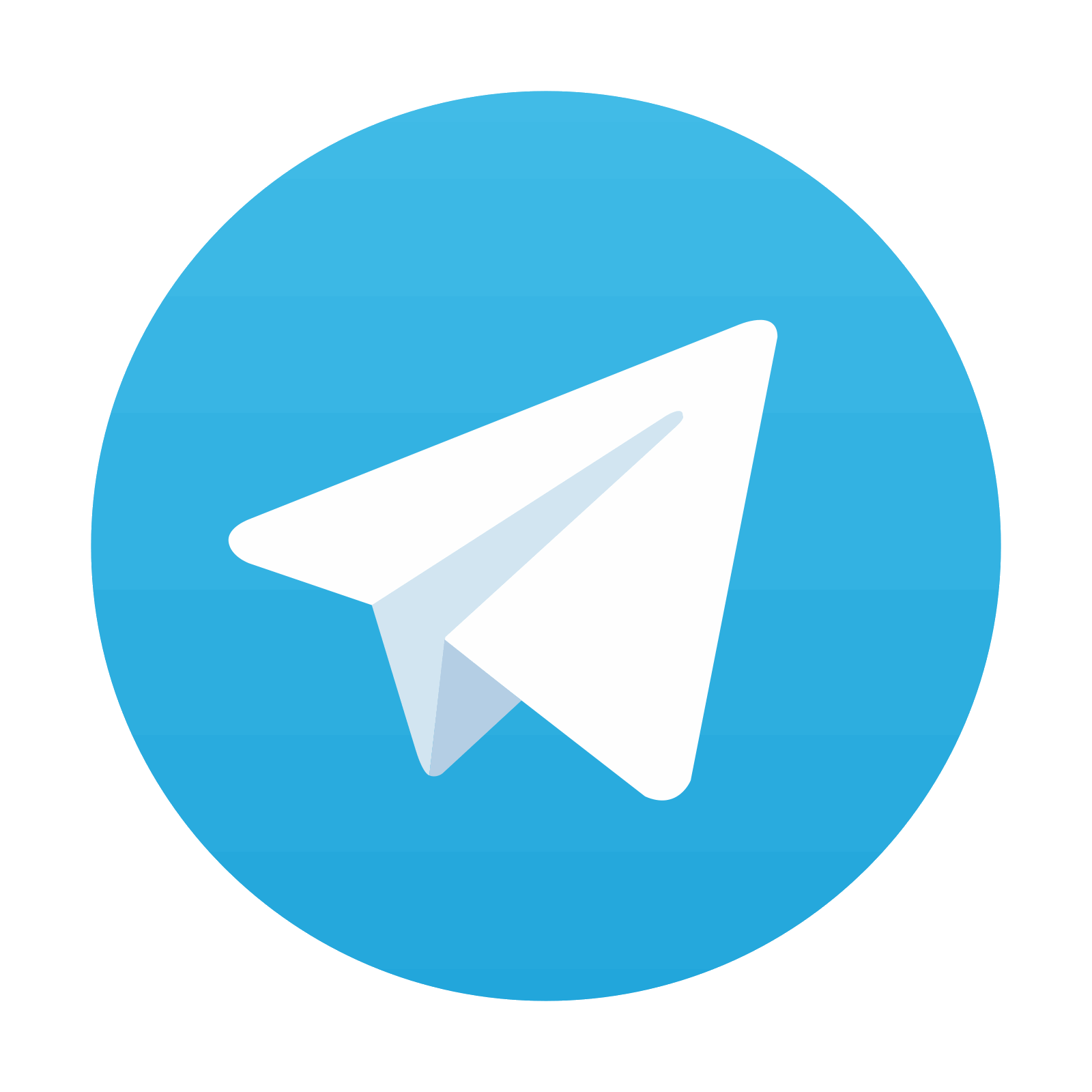
Stay updated, free dental videos. Join our Telegram channel

VIDEdental - Online dental courses
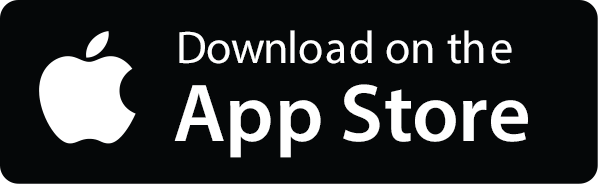
