Abstract
Objective
The present study aimed at a better understanding of the internal shrinkage patterns within different cavity sizes.
Methods
Ten cylindrical cavities in two sizes were filled with a flowable composite and scanned using X-ray micro-computed tomography (μ-CT) before filling, before and after polymerization. Three-dimensional (3D) non-rigid image registration was applied to sets of two subsequent μ-CT images, before and after polymerization in order to calculate the displacements and strains caused by polymerization shrinkage.
Results
3D volumetric displacement analysis disclosed a main vertical component for both the small and large cavities, however in the latter the downward direction reversed to an upward direction from a depth of approximately 2 mm due to debonding at the bottom. Air bubbles and voids in the restorations increased upon polymerization, causing a reverse in strain in the surrounding areas.
Significance
Polymerization-induced shrinkage stress in composite restorations cannot be measured directly. This exploratory study revealed more information on cavity-size dependent shrinkage patterns and opens the way to more extensive studies using different composite materials and varying geometric cavity configurations.
1
Introduction
Polymerization shrinkage is an undesired, yet inherent property of dental composites that causes a discrepancy in dimensions between the restoration as it was placed right before light-curing and its final solidified state after polymerization. This results in a disparity at the interface, which results in either residual strains at the interface or in gap formation in case the bond strength is exceeded, both affecting the longevity of the restored tooth .
Shrinkage strains within a resin composite are non-uniformly distributed. First, they are influenced by the complex geometry of a restoration and the quality of the bonding . Second, the curing-light intensity throughout the restoration changes due to attenuation and scattering of the light that enters from the irradiated surface . Consequently, the polymerization rate and degree of conversion vary within the bulk of the restoration and thus composite properties cannot be expected to be homogeneous throughout the restoration bulk.
While many studies investigated the overall shrinkage parameters , only a few studies focused on localized shrinkage and strain. Among the latter studies, for example, digital image correlation (DIC) of CCD-captured images has been used to visualize the regional strains at the surface of the material . Typically, a random speckle pattern is spray-painted on the surface, which provides the surface contrast needed for DIC. When two cameras were used, the out-of-plane strains could also be measured . Recently, a more advanced form of DIC, making use of a fluorescent particle suspension and laser illumination of the specimen, was developed. This enabled particle tracking in real time, thus providing additional information about the shrinkage kinetics. However, this method is limited to registrations at the surface, and has so far only been carried out in 2D on sliced specimens . Lately, high-resolution X-ray computed tomography (μ-CT) has been introduced to investigate polymerization shrinkage. In addition to surface measurements, this technique can also visualize internal deformations. To visualize the displacement field, Chiang et al . and Cho et al . added spherical particles to the composite and traced their movement before and after polymerization by means of rigid image registration . In a more recent study, Takemura et al . intentionally included air bubbles, which were used as tracers . However, the intentional inclusion of air bubbles by mixing seems impractical and can considerably change the properties of the composite . Virtually all restorations contain a certain amount of porosities without intentional mixing, but these porosities are not distributed evenly within the composite and thus may be less suitable as traceable markers.
In order to calculate the displacement field, image registration has been used. This is a well-known technique in the biomedical field, for instance to relate information in different images for diagnosis, treatment or basic science . Applications of image registration involve combining images of the same patient from different modalities , aligning temporal sequences of images to compensate for motion between scans, and image guidance during interventions. Unlike rigid image registration, non-rigid registration allows some localized scaling in addition to simple transformations such as rotation or translation, this in order to obtain maximal correspondence between images. Hence, distortion of a shape can also be traced.
Experimental measurement of the actual orientation of polymerization shrinkage within a composite restoration is indispensable to estimate the deformation that may occur in a realistic clinical setting. Therefore, the purpose of this study was to visualize the local displacements and to quantify and spatially resolve the accompanying volumetric strains that occur in a composite restoration upon its polymerization by means of non-rigid image registration. We tested the hypothesis that cavity size/depth does not influence volumetric displacement and strain within the composite upon polymerization.
2
Materials and methods
Ten composite cylinders with a diameter of 4.7 mm and a height of 6.0 mm were prepared from a microhybrid composite (Gradia Direct Anterior, GC, Tokyo, Japan) using a polypropylene mold. This composite was selected because of its radio-translucency, so to not interfere with the X-ray computed tomography (μ-CT) of the composite test material (see below). The specimens were divided into two groups and standardized cylindrical occlusal cavities with different dimensions were prepared. The small cavities had a diameter of 2.4 mm and 2.0 mm depth, while the large cavities had a diameter of 3.4 mm and 4.0 mm depth. The C-factors of the small and large cavities were 2.2 and 5.8, and the volumes were 9.0 mm 3 and 36.3 mm 3 , respectively.
The cavities were ultrasonically cleaned in distilled water to remove cutting debris. A 10-MDP-containing adhesive (Clearfil SE Bond, Kuraray Noritake, Tokyo, Japan) was applied, without the prior use of a primer and cured for 10 s with a LED curing device (Bluephase 20i, Ivoclar-Vivadent, Schaan, Liechtenstein). The curing device was always used in ‘high’ mode with an output of 1200 mW/cm 2 , which was verified prior to each use with the accompanying radiometer (Bluephase meter, Ivoclar-Vivadent).
Micro-CT scans were acquired using a nanofocus X-ray computed tomography system (Phoenix nanotom 180, GE Sensing & Inspection Technologies, Wunstorf, Germany), combined with Phoenix Datos|x CT acquisition software. Three scans were taken from each sample. First, the empty cavity was scanned, prior to composite application (‘empty’). Next, the cavity was filled with a flowable composite (G-ænial Flo, GC) and a second scan was taken prior to polymerization (‘uncured’). After polymerization for 40 s with the LED curing device (Bluephase 20i), the third and last scan was taken (‘cured’).
The sample was fixed on a rotating stage where the position between source and detector determines the geometrical magnification. In this way the obtained voxel sizes for the small and large cavities were 2.50 μm 3 and 3.13 μm 3 , respectively. The X-ray tube has a diamond-tungsten target which generates a broad energy spectrum with a peak voltage set at 70 kVp. The system has a fast scanning mode (frame averaging of 1 and image skip of 0), taking 1200 images with an exposure time of 500 ms leading to a total scan time of 10 min.
The projection images were reconstructed in tomographic slices using a modified Feldkamp cone-beam algorithm (NRecon 1.6.5.8, Bruker MicroCT, Kontich, Belgium), creating a 3D dataset. Thereafter, a rigid registration (Euler transformation) was performed to align the three subsequent scans. Although the sample was not removed from the scanner between scans, small movements might have occurred during the filling procedure, as the tip of the composite syringe needs to be in contact with the cavity walls to avoid the inclusion of air bubbles. After the alignment of the scans, the empty cavity was selected and used to accurately define the region of interest (ROI) of the subsequent ‘uncured’ and ‘cured’ scans, so that only the cavity content remained, meaning the flowable composite filling. Three-dimensional, non-rigid, intensity-based image registration was then performed between the ROIs in the ‘uncured’ and ‘cured’ scans. Specialized 2D/3D analysis software (CTAn, Bruker MicroCT) and a custom-made software package based on Elastix were used for the ROI determination and registration, respectively. The registration was computed using a B-spline transformation model, with a grid spacing of 250 μm, 4 resolution levels, 250 iterations and 2048 spatial samples. Advanced Mattes mutual information was used as similarity metric; for the optimization, an adaptive stochastic gradient descent algorithm was applied. After registration, the regional displacements and principal strains were derived analytically from the B-spline deformation field. For the interpretation, the displacement of the particles within the composite was visualized by means of a 3D vector field. The maximum principal strains were visualized by means of a color spectrum. Descriptive statistics were used to summarize the displacement and strain results.
In order to evaluate the integrity of the interface between the cavity and restoration in more detail, samples from both groups were sectioned through their greatest diameter and gold-sputtered for examination by means of scanning electron microscopy (SEM; JEOL JSM-6610/6610LV, Tokyo, Japan) in secondary electron (SE) and backscattered electron (BSE) mode at an accelerating voltage of 15 kV and a spot size of 30.
In order to estimate the influence of the cavity depth on light attenuation, two Teflon molds with a diameter of 4 mm and a depth of 2 mm and 4 mm, respectively, were placed on top of a 0.15 mm microscope cover glass (Marienfeld, Lauda-Königshofen, Germany) and filled with the flowable composite (G-ænial Flo) for spectrophotometric analysis of the transmission of the curing light through the composite. The irradiance and the concomitant spectra were measured at the bottom of the specimen with a calibrated, NiST-referenced spectrometer (USB4000, Ocean Optics, Florida, USA) attached to a sensor with a diameter of 3.9 mm; the resulting delivered energy at the bottom of the cavity was calculated. The specimen diameter of 4 mm was wider than that of both the small and large μ-CT cavities/specimens (2.4 and 3.4 mm, respectively) in order to fully cover the spectrometer sensor, while being able to measure light attenuation with depth, the latter being the same as that of the μ-CT cavities (2 and 4 mm, respectively).
Because the degree of conversion (DC) cannot be assumed identical at both cavity depths, it might have influenced regional shrinkage. In order to check for possible differences in DC in the small and large cavities, both a small (diameter: 2.4 mm, height: 2 mm) and large (diameter: 3.4 mm, height: 4 mm) sample were prepared and sectioned vertically through their greatest diameter (Isomet, Buehler, Lake Bluff, Illinois) and stored in the dark at room temperature for 24 h. Next, they were analyzed with micro-Raman spectroscopy (Senterra, Bruker Optik, Ettlingen, Germany) using the following parameters: 785 nm wavelength laser with 100 mW power, 50 × 1000 μm aperture, 9–15 cm −1 resolution, 50–3500 cm −1 spectral range, integration time of 10 s with 2 co-additions. The laser beam was focused through an ×100 objective lens (BX51, Olympus, London, United Kingdom). The spectrum of the uncured composite was taken as a reference. To calculate DC, the absorbance peak intensities of vinyl C C located at 1640 cm −1 and phenyl C C located at 1610 cm −1 were measured to compare spectra before and after polymerization. The double bond conversion was determined using the following equation:
DC ( % ) = 1 − R cured R uncured × 100
where R is the ratio of peak heights at 1640 cm −1 and 1610 cm −1 for the cured and uncured material.
2
Materials and methods
Ten composite cylinders with a diameter of 4.7 mm and a height of 6.0 mm were prepared from a microhybrid composite (Gradia Direct Anterior, GC, Tokyo, Japan) using a polypropylene mold. This composite was selected because of its radio-translucency, so to not interfere with the X-ray computed tomography (μ-CT) of the composite test material (see below). The specimens were divided into two groups and standardized cylindrical occlusal cavities with different dimensions were prepared. The small cavities had a diameter of 2.4 mm and 2.0 mm depth, while the large cavities had a diameter of 3.4 mm and 4.0 mm depth. The C-factors of the small and large cavities were 2.2 and 5.8, and the volumes were 9.0 mm 3 and 36.3 mm 3 , respectively.
The cavities were ultrasonically cleaned in distilled water to remove cutting debris. A 10-MDP-containing adhesive (Clearfil SE Bond, Kuraray Noritake, Tokyo, Japan) was applied, without the prior use of a primer and cured for 10 s with a LED curing device (Bluephase 20i, Ivoclar-Vivadent, Schaan, Liechtenstein). The curing device was always used in ‘high’ mode with an output of 1200 mW/cm 2 , which was verified prior to each use with the accompanying radiometer (Bluephase meter, Ivoclar-Vivadent).
Micro-CT scans were acquired using a nanofocus X-ray computed tomography system (Phoenix nanotom 180, GE Sensing & Inspection Technologies, Wunstorf, Germany), combined with Phoenix Datos|x CT acquisition software. Three scans were taken from each sample. First, the empty cavity was scanned, prior to composite application (‘empty’). Next, the cavity was filled with a flowable composite (G-ænial Flo, GC) and a second scan was taken prior to polymerization (‘uncured’). After polymerization for 40 s with the LED curing device (Bluephase 20i), the third and last scan was taken (‘cured’).
The sample was fixed on a rotating stage where the position between source and detector determines the geometrical magnification. In this way the obtained voxel sizes for the small and large cavities were 2.50 μm 3 and 3.13 μm 3 , respectively. The X-ray tube has a diamond-tungsten target which generates a broad energy spectrum with a peak voltage set at 70 kVp. The system has a fast scanning mode (frame averaging of 1 and image skip of 0), taking 1200 images with an exposure time of 500 ms leading to a total scan time of 10 min.
The projection images were reconstructed in tomographic slices using a modified Feldkamp cone-beam algorithm (NRecon 1.6.5.8, Bruker MicroCT, Kontich, Belgium), creating a 3D dataset. Thereafter, a rigid registration (Euler transformation) was performed to align the three subsequent scans. Although the sample was not removed from the scanner between scans, small movements might have occurred during the filling procedure, as the tip of the composite syringe needs to be in contact with the cavity walls to avoid the inclusion of air bubbles. After the alignment of the scans, the empty cavity was selected and used to accurately define the region of interest (ROI) of the subsequent ‘uncured’ and ‘cured’ scans, so that only the cavity content remained, meaning the flowable composite filling. Three-dimensional, non-rigid, intensity-based image registration was then performed between the ROIs in the ‘uncured’ and ‘cured’ scans. Specialized 2D/3D analysis software (CTAn, Bruker MicroCT) and a custom-made software package based on Elastix were used for the ROI determination and registration, respectively. The registration was computed using a B-spline transformation model, with a grid spacing of 250 μm, 4 resolution levels, 250 iterations and 2048 spatial samples. Advanced Mattes mutual information was used as similarity metric; for the optimization, an adaptive stochastic gradient descent algorithm was applied. After registration, the regional displacements and principal strains were derived analytically from the B-spline deformation field. For the interpretation, the displacement of the particles within the composite was visualized by means of a 3D vector field. The maximum principal strains were visualized by means of a color spectrum. Descriptive statistics were used to summarize the displacement and strain results.
In order to evaluate the integrity of the interface between the cavity and restoration in more detail, samples from both groups were sectioned through their greatest diameter and gold-sputtered for examination by means of scanning electron microscopy (SEM; JEOL JSM-6610/6610LV, Tokyo, Japan) in secondary electron (SE) and backscattered electron (BSE) mode at an accelerating voltage of 15 kV and a spot size of 30.
In order to estimate the influence of the cavity depth on light attenuation, two Teflon molds with a diameter of 4 mm and a depth of 2 mm and 4 mm, respectively, were placed on top of a 0.15 mm microscope cover glass (Marienfeld, Lauda-Königshofen, Germany) and filled with the flowable composite (G-ænial Flo) for spectrophotometric analysis of the transmission of the curing light through the composite. The irradiance and the concomitant spectra were measured at the bottom of the specimen with a calibrated, NiST-referenced spectrometer (USB4000, Ocean Optics, Florida, USA) attached to a sensor with a diameter of 3.9 mm; the resulting delivered energy at the bottom of the cavity was calculated. The specimen diameter of 4 mm was wider than that of both the small and large μ-CT cavities/specimens (2.4 and 3.4 mm, respectively) in order to fully cover the spectrometer sensor, while being able to measure light attenuation with depth, the latter being the same as that of the μ-CT cavities (2 and 4 mm, respectively).
Because the degree of conversion (DC) cannot be assumed identical at both cavity depths, it might have influenced regional shrinkage. In order to check for possible differences in DC in the small and large cavities, both a small (diameter: 2.4 mm, height: 2 mm) and large (diameter: 3.4 mm, height: 4 mm) sample were prepared and sectioned vertically through their greatest diameter (Isomet, Buehler, Lake Bluff, Illinois) and stored in the dark at room temperature for 24 h. Next, they were analyzed with micro-Raman spectroscopy (Senterra, Bruker Optik, Ettlingen, Germany) using the following parameters: 785 nm wavelength laser with 100 mW power, 50 × 1000 μm aperture, 9–15 cm −1 resolution, 50–3500 cm −1 spectral range, integration time of 10 s with 2 co-additions. The laser beam was focused through an ×100 objective lens (BX51, Olympus, London, United Kingdom). The spectrum of the uncured composite was taken as a reference. To calculate DC, the absorbance peak intensities of vinyl C C located at 1640 cm −1 and phenyl C C located at 1610 cm −1 were measured to compare spectra before and after polymerization. The double bond conversion was determined using the following equation:
DC ( % ) = 1 − R cured R uncured × 100
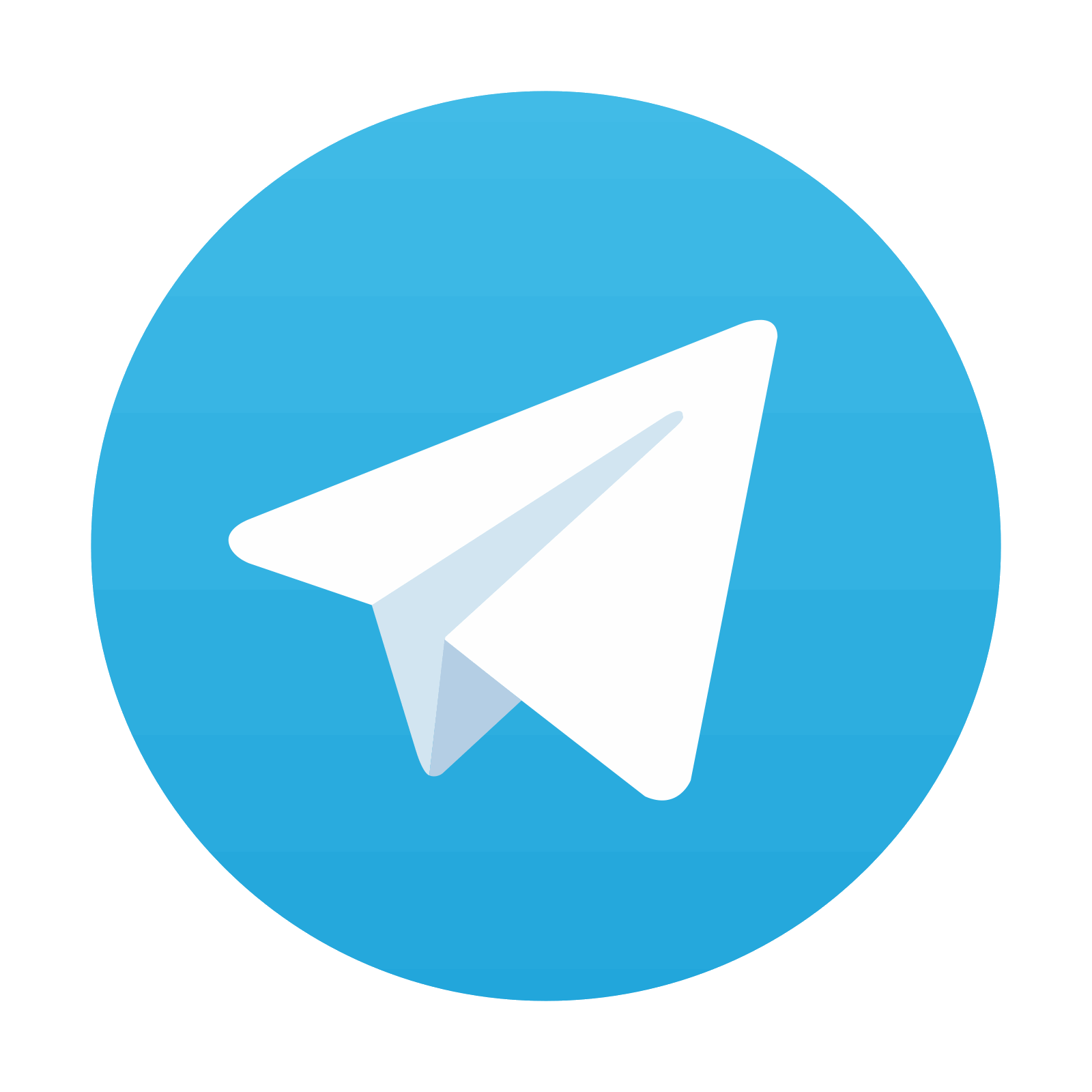
Stay updated, free dental videos. Join our Telegram channel

VIDEdental - Online dental courses
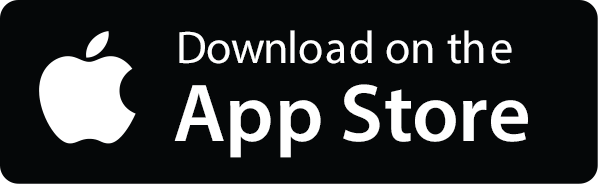
