Dental Casting Alloys and Metal Joining
Historical Perspective on Dental Casting Alloys
1907: the Lost Wax Process
Classification of Dental Casting Alloys
Alloy Classification by Noble Metal Content
In 1984, the American Dental Association (ADA) proposed a simple classification for dental casting alloys based on the content of noble metals. Three categories were described: high noble (HN), noble (N), and predominantly base metal (PB). This classification is presented in Table 16-1. Noble metals comprise a group of seven metals that are resistant to corrosion and tarnish in the mouth. In order of increasing melting temperature, they include gold, palladium, platinum, rhodium, ruthenium, iridium, and osmium. Only gold, palladium, and platinum, which have the lowest melting temperatures of the seven noble metals, are currently of major importance in dental casting alloys. The noble metals and silver are sometimes called precious metals, referring to their high economic values, but the term precious is not synonymous with noble. Silver is reactive in the oral cavity and is not considered a noble metal.
TABLE 16-1
Alloy Classification by Noble Metal Content—American Dental Association (1984)
Alloy Type | Total Noble Metal Content |
High noble (HN) | Must contain ≥40% Au and ≥60% by weight of noble metal elements* |
Noble (N) | Must contain ≥25% by weight of noble metal elements |
Predominantly base metal (PB) | Contains <25% by weight of noble metal elements |
*Noble metal elements include Au, Pd, Pt, Rh, Ru, Ir, and Os.
As described in Chapter 5, the IdentAlloy program was established by manufacturers to provide documentation of certified alloys. Under the program, each alloy has a certificate that lists its manufacturer, alloy name, composition, and ADA classification. Some insurance companies use it as well to determine the cost of crown and bridge treatment. This system lacks the potential to discriminate among alloys within a given category, which may have quite different mechanical properties.
Alloy Classification by Mechanical Properties
ADA Specification No. 5 formerly classified gold alloys as types 1 through 4, depending on the content of gold, palladium, and platinum. The content of noble metals by weight ranges from 83% (type 1) to 75% (type 4). Both the current ADA Specification No. 5 (1997) and ISO Standard 1562 (2004) have classified four types of casting alloys using similar minimal yield strength and percent elongation values for each type of alloy. The only difference is that the ISO standard is specific for casting gold alloys whereas ADA Specification No. 5 covers all alloys that pass the tests for toxicity and tarnish. Table 16-2 lists the classification and mechanical properties described in ISO 1562.
TABLE 16-2
Type | Descriptor | Yield Strength (MPa) | Elongation (%) | Examples of Applications |
1 | Low | 80 | 18 | Inlays |
2 | Medium | 180 | 10 | Inlays and onlays |
3 | Hard | 270 | 5 | Onlays, thin cast backings, pontics, full crowns, saddles |
4 | Extra hard | 360 | 3 | Saddles, bars, claps, crowns, bridges, and partial denture frameworks |
The more recent ISO 22674 standard classifies metallic materials for fixed and removable restorations and appliances into six types according to their mechanical properties without referring to the composition of the alloys (Table 16-3). Although the properties for heat-treated specimens are not given in the table, it is assumed that the specimens are bench-cooled.
TABLE 16-3
Classification of Metallic Material for Dental Applications—ISO 22674 (2006)*
Type | Yield Strength (MPa) | Elongation (%) | Examples of Applications |
0* | – | – | Single-tooth fixed restorations—e.g., small veneered one-surface inlays, veneered crowns |
1 | 80 | 18 | Single-tooth fixed restorations, veneered or nonveneered one-surface inlays, veneered crowns |
2 | 180 | 10 | For single-tooth fixed restorations—e.g., crowns or inlays without restriction on the number of surfaces |
3 | 270 | 5 | For multiple-unit fixed restorations—e.g., bridges |
4 | 360 | 2 | For appliances with thin cross sections that are subjected to very high forces—e.g., removable partial dentures, clasps, thin veneered crowns, wide-span bridges or bridges with small cross sections, bars, attachments, implant retained superstructures |
5 | 500 | 2 | For thin removable partial dentures, parts with tin cross sections, clasps |
*Metallic materials for metal-ceramic crowns produced by electroforming or sintering belong to type 0.
Alloy Classification by Principal Elements
Alloys may be classified based on the principal or most abundant element (e.g., a palladium-based alloy), or they may be named based on the two or three most important elements (e.g., Pd-Ag, Co-Cr, or Ni-Cr-Be alloys). When an alloy is identified according to the elements it contains, the components are listed in declining order of composition, with the largest constituent first followed by the second largest constituent. An exception to this rule is the identification of certain alloys by elements that significantly affect physical properties, which represent potential biocompatibility concerns, or both. For example, Ni-Cr-Mo-Be alloys are often designated as Ni-Cr-Be alloys because of the contributions of beryllium to the control of castability and surface oxidation at high temperatures and the relative toxicity potential of beryllium compared with other metals. Alloy groups shown in Table 16-4 are identified by principal elements.
TABLE 16-4
Classification of Casting Metals for Full-Metal and Metal-Ceramic Prostheses and Partial Dentures
Metal Type | All-Metal Prostheses | Metal-Ceramic Prostheses* | Partial Denture Frameworks |
High noble (HN) |
*Alloys for metal-ceramic prostheses can be used for all metal prostheses, but not vice versa.
Alloy Classification by Dental Applications
There are three categories of dental alloys designated by their applications, including all-metal fixed prostheses, metal-ceramic prostheses, or removable partial dentures. Alloys for all-metal prostheses are also used as substrates for resin-veneered metal prostheses. As shown in Table 16-4, each type of alloy by noble metal content (HN, N, and PB) is available in all three categories. High noble and noble alloys for metal-ceramic prostheses can be used for all-metal prostheses, whereas those for all-metal restorations are rarely used for metal-ceramic restorations. The reasons are as follows: (1) the alloys may not form thin, stable oxides required for porcelain bonding; (2) their melting range may be too low to resist deformation or melting at porcelain-firing temperatures; and (3) their thermal contraction coefficients may not be close enough to those of commercial porcelains. The introduction of ultralow-fusion high-expansion porcelains, which sinter below 850 °C, has led to the use of some yellow-colored, high gold alloys that can be veneered with porcelain. There is a group of high gold-containing alloys that are designated for both all-metal and metal-ceramic applications.
Desirable Properties of Dental Casting Alloys
Tarnish and Corrosion Resistance
As previously discussed in Chapter 3, corrosion is the physical dissolution of a material in the oral environment and tarnish is a thin film of a surface deposit that is adherent to the metal surface. Corrosion resistance is derived from the use of noble metals that do not react in the oral environment (e.g., gold and palladium) or by the ability of one or more of the metallic elements to form an adherent passivating surface film, which inhibits any subsurface reaction (e.g., chromium and titanium).
Thermal Properties
The melting range of the casting alloys must be low enough to form smooth surfaces with the mold wall of the casting investment (Chapter 10). To achieve an accurate fit of cast prostheses, oversized dies for waxing and controlled mold expansion are needed to compensate for casting shrinkage of the alloy and provide space for the luting cement. For metal-ceramic prostheses, the alloys must have closely matching thermal expansion coefficients to be compatible with given porcelains, and they must tolerate high processing temperatures without deforming via a creep process.
Functional Mechanical Properties of Casting Alloys
The strength of an alloy is an important factor in ensuring that the prosthesis for which it is used will serve its intended functions effectively, safely, and for a reasonable time (Chapter 4). In a general sense, mechanical properties are the measured responses of materials under an applied force or distribution of forces, such as elastic deformation, plastic deformation, or a combination of both. The level of strength needed depends on the intended categories of application and types of prostheses to be made. The following are important functional characteristics of casting alloys.
Yield Strength
The yield strength, proportional limit, and elastic limit all are essentially measures of the same property under tension (Chapter 4). It is important to note the difference between these three properties. Yield strength is defined as the amount of stress needed to cause 0.2% plastic deformation of the material, which is why it is also called 0.2% offset yield strength. Proportional limit is the elastic stress above which the linear relationship between stress and strain no longer exists on the stress-strain plot. The elastic limit is the greatest stress to which the alloy can be subjected, such that it will return to its original dimensions when the forces are removed. Both yield strength and proportional limit can easily be located on the stress-strain curve, but elastic limit cannot be identified precisely.
Alloys for All-Metal Prostheses
High Noble and Noble Alloys
For prosthetic dental applications, it is necessary to incorporate various elements in gold to produce alloys with suitable properties. Platinum increases the hardness and elasticity of gold and raises the melting temperature of the alloy. When palladium became expensive in the late 1990s, platinum was used in place of palladium. Copper in a sufficient quantity relative to the gold content renders the alloy heat-treatable (Chapter 5). Silver forms solid solutions with gold and palladium and is a common component in this group of alloys. In gold-copper (Au-Cu) alloys, silver is effective in neutralizing the reddish color of copper. In the case of palladium-based alloys, silver is needed to develop the white color of the alloys. Palladium has a good range of solubility with several metals, such as gold, silver, and copper, and an ability to impart good mechanical properties. It has excellent tarnish/corrosion resistance and is relatively biocompatible. It has also been incorporated in small quantities (about 1.5% by weight) in gold alloys to improve resistance to tarnish and corrosion without a significant loss of gold color. Zinc acts as an oxygen scavenger during melting and casting of noble and high noble alloys. Indium can be used in place of zinc and, when added in greater amounts (18% to 30% by weight), it can promote a gold-like color in Pd-Ag-based alloys. Iridium or ruthenium is added in small quantities as a grain refiner, since smaller grains improve yield strength.
The compositions of selected high noble and noble alloys are given in Table 16-5. Their physical and mechanical properties are shown in Table 16-6. Since some noble metals contain no gold and rely on palladium for corrosion resistance, these alloys are discussed in two categories: Au-based alloys and Ag-Pd alloys.
TABLE 16-5
Typical Compositions of High Noble and Noble Alloys for All-Metal Prostheses
ELEMENTAL COMPOSITION (PERCENT BY WEIGHT) | ||||||||
Alloy Type | Color | Au | Pd | Ag | Cu | Pt | In | Balance* |
1 | Yellow | 83 | 0.5 | 10 | 6 | – | – | Zn; Ir |
2 | Yellow | 82 | – | – | – | 18 | – | Ir |
Yellow | 77 | 1 | 13 | 8.5 | – | – | Zn; Ir | |
3 | Yellow | 74.5 | 3.5 | 11 | 10.5 | – | – | Zn; Ir |
Yellow | 50 | 4 | 35 | 10 | – | – | Zn; Ir | |
Yellow | 2 | 34.9 | 30 | – | – | 30 | Zn:3; Ir | |
White | – | 25 | 71.5 | – | – | 2.5 | Zn; Ru | |
4 | Yellow | 60 | 4 | 20.5 | 15 | – | – | Zn; Ir |
Yellow | 50 | 3 | 26 | 11.5 | – | 3 | Zn:1; Ir | |
Pale yellow | 20 | 20 | 36 | – | – | 18 | Zn:6; Ir | |
White | 4 | 30.3 | 45.7 | 18.5 | – | – | Zn:1.5; Ir |
TABLE 16-6
Alloy Type | ADA Classification | Density (g/cm3) | Yield Strength (soft/hard) (MPa) | Hardness (soft/hard) (VHN) | Elastic Modulus (GPa) | Percent Elongation (soft/hard) |
1 | High noble | 16.6 | 126 | 85 | 70 | 51 |
2 | High noble | 19.2 | 146 | 95 | 50 | 23 |
High noble | 15.4 | 221 | 120 | 109 | 54 | |
3 | High noble | 15.5 | 207/276 | 121/182 | 76 | 39/19 |
Noble | 13.2 | 309/648 | 138/225 | 104 | 28/15 | |
Noble | 10.5 | 297 | 180 | 51 | 5-6 | |
Noble | 10.5 | 248/310 | 145/155 | 55 | 10/8 | |
4 | High noble | 14.5 | 350/607 | 165/235 | 88 | 35/4 |
Noble | 13.2 | 428/683 | 180/255 | 86 | 28/16 | |
Noble | 11.3 | 420/530 | 165/220 | 103 | 10/2 | |
Noble | 10.6 | 460/700 | 195/265 | 116 | 10/3 |
Gold-Based Alloys
These alloys are generally yellow in color (see Table 16-5). Type 1 gold alloys are soft and designed for inlays supported by teeth and not subjected to significant mastication forces. Type 2 alloys are widely used for inlays because of their superior mechanical properties, but they have less ductility than type 1 alloys. Type 3 alloys are used for constructing crowns and onlays for high-stress areas. Increasing the Pt or Pd content raises the melting temperature, which is beneficial when components are to be joined by soldering (or brazing). Type 4 gold alloys are used in high-stress areas such as bridges and partial denture frameworks. The cast alloy must be rigid to resist flexure, possess high yield strength to prevent permanent distortion, and be ductile enough for adjustment if the clasp of a framework has been distorted or needs adjustment.
Heat Treatment of Gold-Copper Alloys
To soften the alloy, the casting is placed in a furnace for 10 minutes at 700 °C and then quenched in water. All intermediate phases in the alloy are changed to a disordered solid solution at 700 °C, and the rapid quenching prevents ordering from occurring during cooling. The tensile strength, proportional limit, and hardness are reduced by such a treatment, and the ductility is increased. To harden the alloy, the temperature of the furnace is set between 200 °C and 450 °C and the casting is heated for 15 to 30 minutes before it is quenched in water. Ideally, before the alloy is age-hardened, it should be subjected to a softening heat treatment to relieve all residual strain hardening (Chapter 17) before the alloy is hardened again by heat treatment to produce a disordered solid solution. Otherwise the amount of solid-state transformation will not be properly controlled. In metallurgical terminology, the softening heat treatment is referred to as a solution heat treatment and the hardening heat treatment is termed age hardening. Mechanical properties of both the softened and age-hardened states are shown in Table 16-6.
Silver-Palladium Alloys
By melting palladium and indium at the composition of 50% In and 50% Pd in atomic percent (52% In and 48% Pd by weight), the alloy is copper colored but increasing the palladium content causes the alloy to lose its reddish color and acquire a gold color. A minimum of 15% by weight of Pd-In intermetallic compound is needed to maintain the yellowish color. A much higher proportion of Pd-In intermetallic compound is used in commercial dental alloys (see Table 16-5). The tarnish resistance of the alloys is especially dependent upon the composition and the integrity of the casting. The colored phase of the Pd-In binary alloy system is hard and brittle and is not a strenghener. Silver, copper, and/or gold can be added to increase the ductility and improve the castability of the alloy for dental applications.
Predominantly Base Metals
Currently there are two main groups of base metal dental alloys: nickel-chromium (Ni-Cr) and cobalt-chromium (Co-Cr). The Ni-Cr alloys can be further divided into those with and without beryllium, which improves castability and promotes the formation of a stable metal oxide for porcelain bonding. The majority of Ni-Cr alloys are for small castings such as crowns and FDPs, and Co-Cr alloys are primarily used for casting removable partial dentures in which high elastic modulus and yield strength are needed. Some Ni-Cr alloys, which are used for partial denture frameworks, are formulated for their relative ease of finishing and polishing compared with Co-Cr alloys, which are used for crowns and FDPs in spite of their low ductility. Table 16-7 lists compositions and properties of selected base alloys for all metal and metal–ceramic applications. Molybdenum increases corrosion resistance and strength and decreases the thermal expansion coefficient of base metal alloys. The latter is beneficial for porcelain bonding and minimizes the risk of porcelain cracking or fracture. Base metal alloys for partial frameworks are discussed later.
TABLE 16-7
Typical Compositions of Base Metal Alloys for Crown, FDP, and Metal-Ceramic Applications
ELEMENTAL COMPOSITION (PERCENT BY WEIGHT) | MECHANICAL PROPERTIES | ||||||||
Alloy (supplier) | Ni | Co | Cr | Mo | Balance* | Yield Strength (MPa) | Hardness (VHN) | Elastic Modulus (GPa) | Elongation (%) |
IPS d.Sign 15 (Ivoclar) | 58.7 | 1 | 25 | 12.1 | Fe:1.9; Si:1.7; Ce | 340 | 230 | 200 | 13 |
Rexalloy (Pentron Alloys) | 67 | – | 14 | 8 | Ga:8; Al; Fe; Si; Mn; Zr; Cu | 300 | 177 | 191 | 27 |
Heraenium S (Heraeus Kulzer) | 62.9 | – | 23 | 10 | Si:2; Fe:15.5; Ce:0.5 | 310 | 220 | 120 | 29 |
NPX-III (CMP Industries) | 76.5 | x† | 14 | 4.5 | Al:2.5; Be:1.6; Ti | 784 | 350 | 200 | 9 |
Argeloy Bond (Argen) | 77 | – | 14 | 4.7 | Mn; Fe; Si; C | 630 | 370 | 207 | 10 |
Norex (Pentron) | – | 55 | 25 | – | W:10; Ru:5; Al, Nb, Y, Zr | 621 | 350 | 204 | 7 |
Heraenium P (Heraeus Kulzer) | – | 59 | 25 | 4 | W:10; Si:1; Mn:0.8; N | 650 | 330 | 200 | 8 |
Jelbond Supreme (Jelenko) | – | 61 | 27 | 6 | W:5; Mn; Si; Fe; C | 475 | 365 | 223 | 8 |
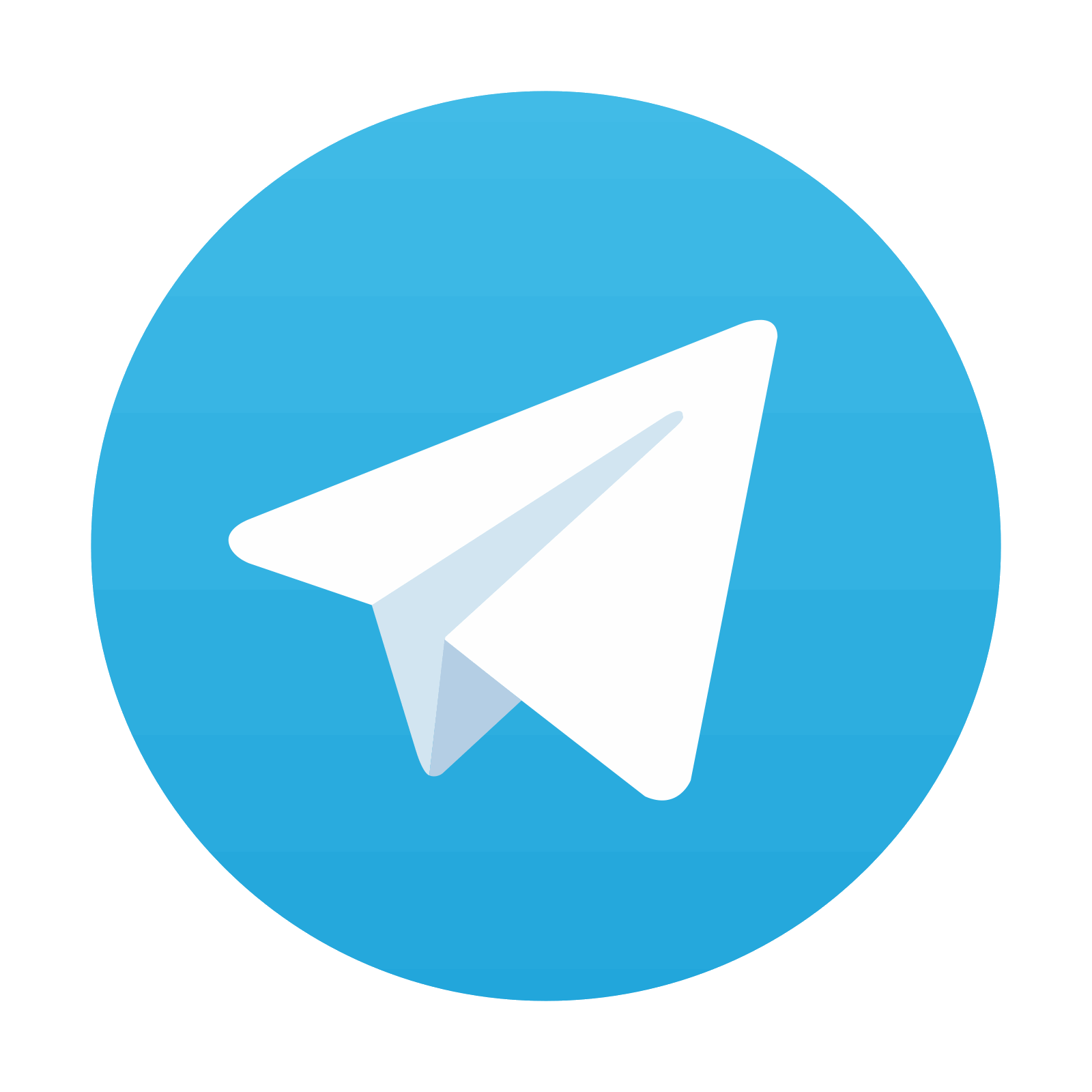
Stay updated, free dental videos. Join our Telegram channel

VIDEdental - Online dental courses
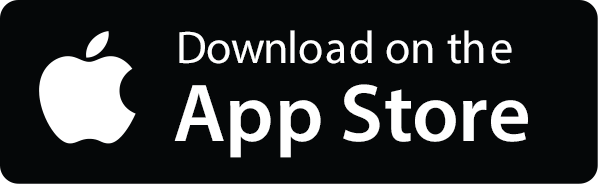
