Abstract
Objective
The aim of the present study was to investigate two- and three-body wear of microfilled, micro-hybrid and nano-hybrid composite resins using a ball-on-disc sliding device.
Methods
One microfilled (Durafill VS), one micro-hybrid (Filtek Z250), one hybrid (Clearfil AP-X), one nanofilled (Filtek Supreme XT), and two nano-hybrid (MI Flow, Venus Diamond) composite resins were examined. The composites were filled in a cylindrical cavity, and light polymerized. After storage in 37 °C distilled water for 7 days, all specimens were tested with a custom-made ball-on-disc sliding device with a zirconia ball as antagonist (50 N loads, 1.2 Hz, 10,000 cycles) immersed in water, poppy seed slurry and polymethyl methacrylate slurry, respectively. Maximum wear depth and volume loss of worn surfaces were quantified by a digital CCD microscope and analyzed with two-way analysis of variance.
Results
The interactions between composite resin and condition of their maximum wear depth and volume loss were significant ( p < 0.01). The abrasive wear produced at three-body loading with poppy seed slurry was very large for the microfilled composite, and small for all other composites tested. In contrast, two-body wear of the microfilled composite, and one nano-hybrid composite was very low.
Significance
The ball-on-disc sliding device used is considered suitable to simulate sliding of an antagonist cusp on an opposing occlusal composite restoration, either in the two- or the three-body wear mode. All tested materials except for the microfilled composite showed low surface wear when exposed to poppy seed as the third-body medium.
1
Introduction
Several long-term clinical studies on posterior composite resin restorations showed unanimously that the main reasons for restoration failures were secondary caries and fractures . New composite resins are designed on the basis of more than 30 years of in vivo and in vitro experience with previous composites. According to manufacturers and researchers the mechanical characteristics of recent composite restoratives are improved making them successfully applicable for restoration of all cavity classes . Among others, new monomers were introduced, such as siloranes and modified urethane (meth)acrylates. The main effect of filler refinement was not only to increase filler volume, but also to reduce particle size for enhanced polishing and wear resistance, while maintaining suitable handling characteristics. Recently, most newly introduced composite resins include nano-sized filler particles. Two different approaches to include nanoparticles as filler in composite resins are currently used: Nanofilled composites, including discrete nanofillers and nanofiller clusters, or nano-hybrid composites, including fine milled glass and discrete nanoparticles or composites with nanofiller containing prepolymers.
Wear of current composites is no longer considered a major concern when applied in small and medium sized cavities, whereas larger posterior restorations especially for patients with bruxing habits are still at risk for extensive wear . Randomized clinical trials comparing the wear of hybrid composites with the wear of nanofiller containing composites showed promising results; no significant differences in wear between the two material groups were found .
Quantitative wear data and wear morphology are under the influence of types of composite resins and presence of a third-body medium . In condition of two-body wear test, microfilled composite resin showed lower material loss with smoothly worn surface, whereas micro-hybrid showed greater material loss with cracks in the worn surface . When microfilled composite was worn in presence of abrading slurry the worn surface showed greater failure .
Although there is broad consensus that clinical evaluation of composite resin wear is the ultimate and reliable information, numerous articles are continuously found in dental literature, reporting in vitro wear data produced with different wear testing devices . Therefore, combination of at least two different wear settings is recommended to assess the wear resistance of materials . However, so far the results acquired with laboratory wear methods could not consistently be correlated with in vivo wear data, mainly due to lack of long-term studies done with identical materials . Moreover, laboratory methods to test conventional resins for wear are criticized less important, especially since most of them do not reflect the clinical wear . However, in vitro wear testing has been important for evaluating new materials before clinical usage.
With the increasing number of nanofiller containing composite resins introduced to the market, it is still important to analyze the mechanisms resulting from two-body wear at direct contact between opposing tooth surfaces (occlusal contact area = OCA: attrition), and from three-body wear (contact free area = CFA: abrasion), occurring when a food bolus is compressed between antagonist teeth and abrading particles of food slide over the restoration surface . Since in most cases occlusal restorations are affected by both mechanisms, it is reasonable that wear simulating devices should be designed to simulate both loading types. At this time, unanimously accepted in vitro wear testing methods are not approved. The ISO technical specification 14569-2:2001 “Wear by two- and/or three-body contact” does not give a clear recommendation either . The natural grains as poppy seed and the synthetic material PMMA have been suggested as abrasives in this standard. The nano hardnesses of PMMA and poppy seed were reported 0.279, and 0.226 GPa, respectively .
Studies quantifying wear should preferably include morphological analyses of the wear patterns in order to explore the basic wear mechanisms under the different wear conditions. Apart from the production of wear patterns on specimens simulating in vivo conditions, it is equally important to apply quantitative evaluation methods, rather than semi-quantitative or qualitative methods. Determination of volume loss using three-dimensional contact or non-contact scanners is apparently the most suitable method to obtain accurate and reproducible data. The provided unequivocal reference planes/points, not affected during the wear process, are defined .
Aim of this in vitro study was to investigate and compare two- and three-body wear of microfilled, micro-hybrid and nano-hybrid composite resins, using a custom-made ball-on-disc sliding device. The null hypotheses tested in this study were that there would be no significant differences in quantitative wear and no differences in micro-morphology of the worn surfaces among the composite resins investigated.
2
Materials and methods
Table 1 summarizes the materials investigated and their main compositions, as publicly made available on the respective manufacturers’ websites.
Material | Shade | Type | Code | Manufacturer | Batch | Composition | ||
---|---|---|---|---|---|---|---|---|
Monomer | Filler | |||||||
Composition | Vol% | |||||||
Durafill ® VS | A3 | Microfilled | DUR | Heraeus Kulzer, Hanau, Germany | 010210 | Bis-GMA, UDMA, TEGDMA | SiO 2 (20–70 nm), prepolymer <20 μm. SiO 2 in prepolymer: 32 wt% | 66 |
Filtek™ Z250 | A3 | Micro-hybrid | Z250 | 3 M ESPE, St. Paul, MN, USA | 9UR | Bis-GMA, Bis-EMA, UDMA | SiO 2 , ZrO 2 , particle size 0.01–3.5 μm, average 0.6 μm | 60 |
Clearfil AP-X | A2 | Hybrid | APX | Kuraray, Okayama, Japan | 1078 A | Bis-GMA, TEGDMA | Silanated barium glass, Silanated colloidal silica, silinated silica (0.1–15 μm) | 70 |
Filtek™ Supreme XT | A3B | Nanofilled | FIL | 3 M ESPE, St. Paul, MN, USA | 9WT | Bis-GMA, UDMA, Bis-EMA, TEGDMA | Aggregated SiO 2 /SrO 2 clusters (0.8–1.4 μm) an non-agglomerated SiO 2 (20 nm) | 59.5 |
MI Flow | A3 | Nano-hybrid | MFL | GC Corporation, Tokyo, Japan | 0904132 | UDMA, Bis-MEPP, DMA | Sr-glass, lanthanoid fluoride, SiO 2 (average = 700 nm) | 40 |
Venus ® Diamond | A3 | Nano-hybrid | VED | Heraeus Kulzer, Hanau, Germany | 100027 | TCD-DI-HEA, UDMA | Ba-Al-F-silicate glass < 20 μm SiO 2 (5 nm) |
64 |
2.1
Specimen preparation
Composite resin specimens were produced at ambient laboratory atmosphere in slightly undercut aluminum molds, 8 mm in diameter and 2 mm in depth. The lightly overfilled cavities were covered with a Mylar strip and pressed flush under a glass plate prior to 40 s light activation with the light exit window of the halogen curing unit (XL 3000, 3 M ESPE, MN, USA; output >500 mW cm −2 ) in contact with the Mylar foil. Immediately after curing, the specimens were stored for 7 days in 37 °C water before excess was removed by manually grinding on wet SiC paper, using consecutive grit numbers 600, 1500 and 4000. Two reference points were engraved at the peripheral area of the composite resin using a diamond round point (Diamond Point #40, Shofu, Kyoto, Japan; 1.0 mm in diameter). The specimen was ultrasonically cleaned for 5 min.
2.2
Wear testing device
In the custom made ball-sliding on disc wear testing machine, a zirconia ball (4 Φ mm, YTZ ball, Nikkato Corp, Osaka; 4.0 mm in diameter, 1330 in HV1) served as the antagonist “cusp” loading the composite specimen at 15° angulation for a 3.7 mm long slide path. At the end of each sliding motion the zirconia ball was lifted and returned into the zero position for the next sliding cycle (50 N load, 1.2 Hz, 10,000 cycles). The zirconia ball was checked at every 10,000 cycles under a traveling microscope (MM-60, Nikon Corp., Tokyo, Japan) and a new zirconia ball was mounted when any scratch was found. The specimens were mounted on the fixed table of the device in an aluminum container, filled with water for simulation of two-body wear, an aqueous slurry of 33 mass% lightly pre-ground poppy seeds (60 s in a coffee grinder) or an aqueous slurry of 30 mass% polymethyl methacrylate beads (PMMA: Palapress denture base material polymer beads; average particle size 40 μm) for simulation of three-body wear, respectively. The reference points were covered by the container and thus not exposed to grounding during the test. For each composite resin 6 specimens were tested under each of the three conditions, using freshly prepared abrasive slurries, at ambient atmosphere.
2.3
Determination of wear
Specimens were carefully rinsed with tap water and dried with compressed air. Each sample was scanned with a digital CCD microscope at 100-fold magnification (VHX-1000 with VH-Z 100R lens, KEYENCE Corp., Osaka, Japan) at 5 μm intervals along the z -axis. The specimens’ reference planes were horizontally adjusted using three points on the non-abraded site near the reference points. Small ridge-like elevations seen next to the wear trace, probably due to plastic deformation under the action of the sliding ball, were disregarded for the software-produced calculation of maximum depth and volume loss of the wear trace by manually aligning the reference plane. The accuracy of the CCD microscope was determined from a Rockwell indentation made on a polished CoCr-alloy and two composite resin (DUR, Z250) surfaces. First the indentation diameter was measured using the traveling microscope at 50-fold magnification, and then the same Rockwell indentation diameter was measured on the CCD microscope. The diameters (standard deviations) after five repetitive measurements of CoCr-alloy, DUR, and Z250 using the traveling microscope were 453.2 (1.5), 1062.2 (1.6), and 753.8 (0.8) μm, respectively; those using the CCD microscope were 452.4 (2.6), 1061.7 (1.5), and 752.5 (1.2) μm, respectively. The mean difference between the traveling and CCD microscope measurements of Co–Cr alloy, DUR, and Z250 were 0.8, 0.5, and 1.3 μm, respectively.
The sliding wear results were analyzed with two-way analysis of variance (ANOVA) followed by Tukey’s HSD test at a significance level of α = 0.05 (SPSS Statistics ver.17, SAS, Cary, USA).
2.4
Scanning electron microscope investigation of worn surfaces
Scanning electron microphotographs (SEMs) were made from representative specimens of each material after each of the wear test conditions. The specimens were sputter-coated with platinum to a thickness of approximately 5 nm. Specimens were examined by SEM (VE-8800, Keyence Corp.) at 10 kV acceleration voltage and 500× magnification.
2
Materials and methods
Table 1 summarizes the materials investigated and their main compositions, as publicly made available on the respective manufacturers’ websites.
Material | Shade | Type | Code | Manufacturer | Batch | Composition | ||
---|---|---|---|---|---|---|---|---|
Monomer | Filler | |||||||
Composition | Vol% | |||||||
Durafill ® VS | A3 | Microfilled | DUR | Heraeus Kulzer, Hanau, Germany | 010210 | Bis-GMA, UDMA, TEGDMA | SiO 2 (20–70 nm), prepolymer <20 μm. SiO 2 in prepolymer: 32 wt% | 66 |
Filtek™ Z250 | A3 | Micro-hybrid | Z250 | 3 M ESPE, St. Paul, MN, USA | 9UR | Bis-GMA, Bis-EMA, UDMA | SiO 2 , ZrO 2 , particle size 0.01–3.5 μm, average 0.6 μm | 60 |
Clearfil AP-X | A2 | Hybrid | APX | Kuraray, Okayama, Japan | 1078 A | Bis-GMA, TEGDMA | Silanated barium glass, Silanated colloidal silica, silinated silica (0.1–15 μm) | 70 |
Filtek™ Supreme XT | A3B | Nanofilled | FIL | 3 M ESPE, St. Paul, MN, USA | 9WT | Bis-GMA, UDMA, Bis-EMA, TEGDMA | Aggregated SiO 2 /SrO 2 clusters (0.8–1.4 μm) an non-agglomerated SiO 2 (20 nm) | 59.5 |
MI Flow | A3 | Nano-hybrid | MFL | GC Corporation, Tokyo, Japan | 0904132 | UDMA, Bis-MEPP, DMA | Sr-glass, lanthanoid fluoride, SiO 2 (average = 700 nm) | 40 |
Venus ® Diamond | A3 | Nano-hybrid | VED | Heraeus Kulzer, Hanau, Germany | 100027 | TCD-DI-HEA, UDMA | Ba-Al-F-silicate glass < 20 μm SiO 2 (5 nm) |
64 |
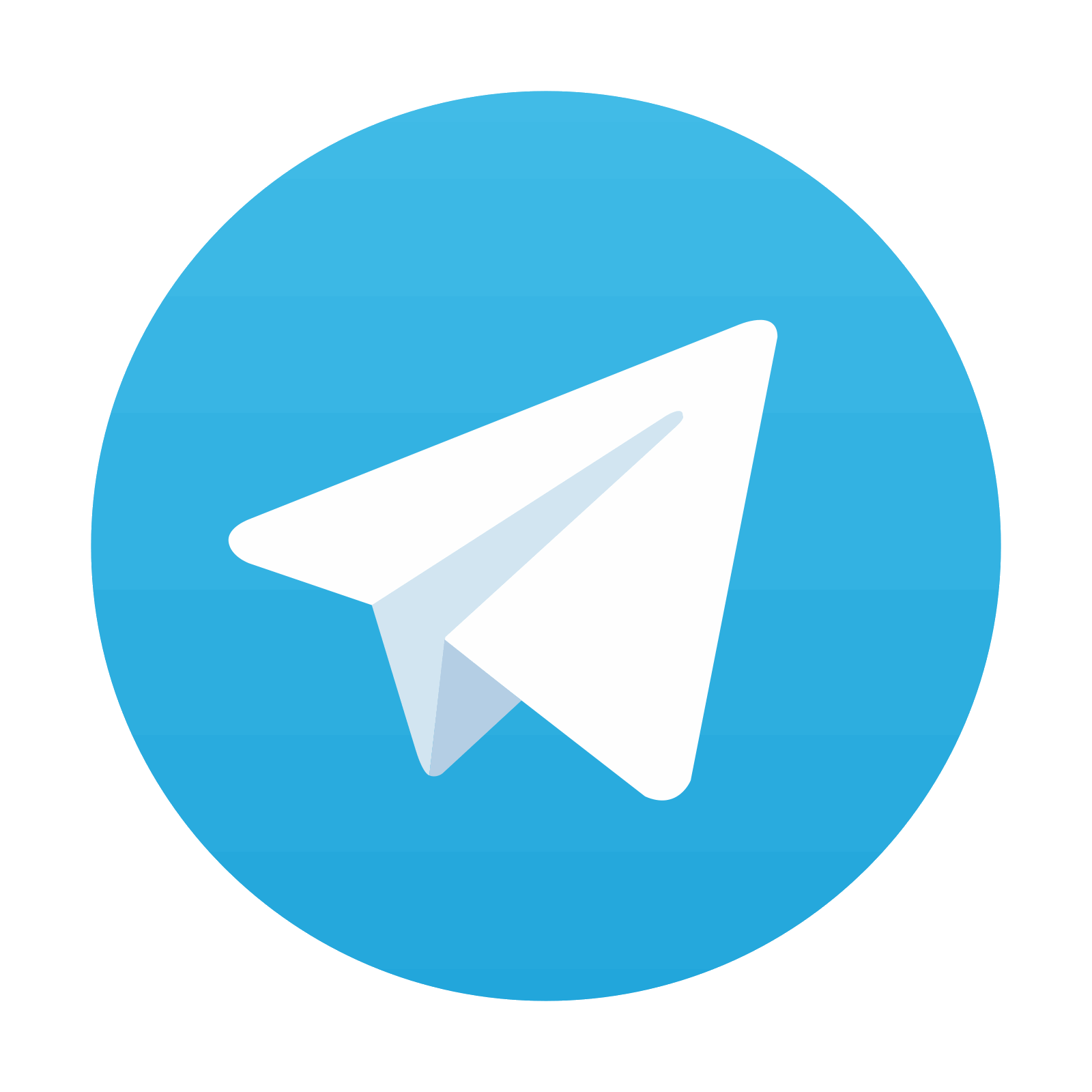
Stay updated, free dental videos. Join our Telegram channel

VIDEdental - Online dental courses
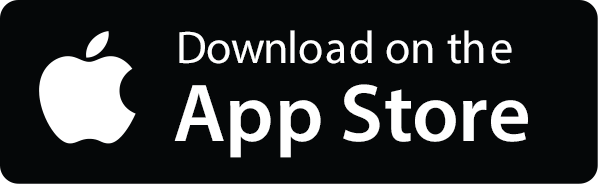

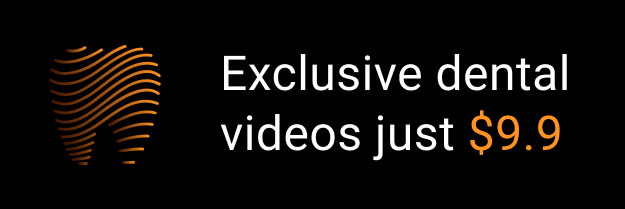