Introduction
The aim of this study was to analyze the time-dependent in-vitro behavior of the periodontal ligament (PDL) by determining the material parameters using specimens of porcine jawbone. Time-dependent material parameters to be determined were expected to complement the results from earlier biomechanical studies.
Methods
Five mandibular deciduous porcine premolars were analyzed in a combined experimental-numeric study. After selecting suitable specimens (excluding root resorption) and preparing the measurement system, the specimens were deflected by a distance of 0.2 mm at loading times of 0.2, 0.5, 1, 2, 5, 10, and 60 seconds. The deflection of the teeth was determined via a laser optical system, and the resulting forces and torques were measured. To create the finite element models, a microcomputed tomography scanner was used to create 3-dimensional x-ray images of the samples. The individual structures (tooth, PDL, bone) of the jaw segments were reconstructed using a self-developed reconstruction program. A comparison between experiment and simulation was conducted using the results from finite element simulations. Via iterative parameter adjustments, the material parameters (Young’s modulus and Poisson’s ratio) of the PDL were assessed at different loading velocities.
Results
The clinically observed effect of a distinct increase in force during very short periods of loading was confirmed. Thus, a force of 2.6 N (±1.5 N) was measured at the shortest stress duration of 0.2 seconds, and a force of 1.0 N (±0.5 N) was measured at the longest stress duration of 60 seconds. The numeric determination of the material parameters showed bilinear behavior with a median value of the first Young’s modulus between 0.06 MPa (2 seconds) and 0.04 MPa (60 seconds), and the second Young’s modulus between 0.30 MPa (10 seconds) and 0.20 MPa (60 seconds). The ultimate strain marking the transition from the first to the second Young’s modulus remained almost unchanged with a median value of 6.0% for all loading times.
Conclusion
A combined experimental-numeric analysis is suitable for determining the material properties of the PDL. Microcomputed tomography allows high-precision recordings with only minimum effort. This study confirms the assumption of time dependency and nonlinearity of previous studies.
Highlights
- •
Time-dependent behavior of the PDL was evaluated with an experimental numeric method.
- •
Combined analysis was suitable for determining material properties of the PDL.
- •
Time-dependency and nonlinearity and results from previous studies were confirmed.
The periodontal ligament (PDL), a complex, fibrous biologic connective tissue, is responsible for cushioning and transmitting all forces that affect the teeth and their surrounding bones. Consequently, it has an important influence on tooth movement. In the stomatognathic system, the PDL transfers the forces into the alveolar bone that act on the teeth. The resulting change in position of the tooth in the alveolus generates pressure as well as tensile areas. In the pressure areas, the periodontal fibers are compressed, resulting in bone resorption; in the tensile areas, the fibers are outstretched, finally resulting in bone apposition. Reitan and Reitan and Kvam divided tooth movement into 3 phases (initial phase, hyalinization, and resorption). According to them, tooth movement starts with an initial cushioning that deflects the tooth and compresses the PDL.
The initial cushioning that occurs with subliminal forces can be reduced to a variety of mechanisms: the elasticity of dental hard tissue, the elastic deformation of the alveolar bone, the initial extension of desmodontal fibers, and the hydrodynamic cushioning through desmodontal tissue fluid (with the desmodont as the connective part of the PDL between bone and tooth). During this phase, the desmodontal circulation stays intact, and the reactions of the periodontium are reversible.
Due to its complex multiphase structure, the PDL shows distinct time-dependency, nonlinearity, and anisotropy. The inconsistent results of previous studies concerning biomechanical behavior can be explained by a number of factors, including differing experimental setups with varying loading velocities, the complexity of involved tissues, and different assumptions about the mechanical properties of the PDL. This led to values for Young’s modulus ranging from 0.07 MPa to 1379 MPa.
In this study, a combined experimental and numeric approach was used to analyze the time-dependent behavior of the PDL using samples of porcine jawbone. Finite element (FE) models were generated to determine the material parameters (Young’s modulus, Poisson’s ratio) of the PDL by comparing experiment and simulation. The aim of this study was to complement or complete previous results on the biomechanical behavior of the PDL by increasing the range of loading velocities in previous studies and verifying the material parameters.
Material and methods
Specimens from domestic pigs were used to determine the time-dependent behavior of the PDL. Porcine jawbones were provided by a butcher’s shop immediately after slaughtering. The pigs were aged between 4 and 6 months; thus the roots of their milk teeth were fully developed. For the examination of deciduous premolars, 2-dimensional x-rays were taken to preselect samples by the resorption of their roots. Subsequently, 10 of 14 samples could be used, were embedded in resin (Technovit 4004; Heraeus Kulzer, Hanau, Germany), and subsequently prepared for measurement in the previously described mobility measurement system. This measurement system ( Fig 1 ) is an optomechanical setup, consisting of an optoelectronical part ( Fig 2 ) for the noninvasive measurement of tooth displacement and a mechanical part for the application of forces and torques. The laser cube of the optical registration system is fixed in the tooth’s crown by drilling a hole in the crown and inserting a thread rod. The specimen is rigidly fixed in the setup so that the laser beams are pointing at the center of the position sensitive devices ( Fig 2 ).


Once installed on the measurement system, the crown of the sample was deflected by 0.2 mm by applying a force from vestibular. Each sample was loaded repeatedly at time intervals of 0.2, 0.5, 1, 2, 5, 10, and 60 seconds with intermediate relaxation times of at least 5 minutes. The deflection of the teeth was assessed by the laser optical system, and the resulting forces and torques were measured.
After experimentation, the samples were x-rayed 3 dimensionally with a microcomputed tomography scanner (model 1174; Skyscan, Kontich, Belgium) to construct FE models. Using the microcomputed tomography scans, the possible prevalence of root resorption could be detected, and 2 additional samples had to be excluded from the numeric analyses. Using the self-developed reconstruction program Advanced Object Reconstruction in 3D, the structures of tooth, PDL, and bone were identified and reconstructed in subsequent layers of the 3-dimensional data sets and connected to compose 3-dimensional surface models. These models were then refined using the Remesh 2 software (Marco Attene, MATI-GE/CNR) and converted into FE volume models using the 2010 FE software (MSC Software, Newport Beach, Calif). Respective material parameters as presented in Table I were assigned to the structures of tooth, PDL, and bone. Various authors have shown that the subdivision of the tooth into enamel and dentin, as well as the subdivision of the bone into spongious and cortical, only have a negligible influence on numeric results. Consequently, bone and tooth were defined as isotropic, homogeneous, and linear elastic material. A sketch of the whole procedure of the study is presented in Figure 3 .
Material | Young’s modulus (MPa) | Poisson’s ratio (μ) |
---|---|---|
Tooth | 20.000 | 0.30 |
Bone | 2.000 | 0.30 |
PDL | Bilinear, adjusted | 0.30 |

Previous studies already have shown the bilinear behavior of the PDL. Taking this into account, we determined the Young’s moduli by an iterative parameter adjustment: the force/deflection diagrams of the numeric simulations were compared with the respective experimental curves and adjusted to them by variation of Young’s moduli and ultimate strain until a good accordance of numeric and experimental data was achieved. Figure 4 presents such an approximations for specimen 4 at 2, 10, and 60 seconds loading times. A good correlation of the fits is obvious. From the 8 samples that did not show root resorption, 2 more had to be excluded from the analysis because numeric instabilities in the models did not allow performing a proper fit of numeric and experimental curves. These numeric instabilities occur when, for example, the furcation seems to be quite narrow, and elements are generated that cause convergence problems of the nonlinear solver. A third specimen had to be excluded because it showed inconsistent experimental results, due to either drying or dental calculus in the periodontal space. These issues are discussed in detail below.

Results
Figure 5 shows mean values and standard deviations of the maximum measured forces of all 5 fully (experimentally and numerically) examined samples. Although the simulations did not reach the maximum deflection of 0.2 mm in all cases, the maximum forces from the numeric part could be assessed through extrapolation, since the calculated curves were placed inside the linear segment of the second Young’s modulus. The shortest stress duration of 0.2 seconds displayed maximum forces between 1.0 and 4.6 N with a mean value of 2.6 N (±1.5 N) and extrapolated forces between 1.0 and 4.6 N with a mean value of 2.6 N (±1.5 N). A loading time of 60 seconds (longest) showed maximum forces between 0.6 and 1.6 N with a mean value of 1.0 N (±0.5 N). The extrapolated forces ranged from 0.5 to 1.6 N with a mean value of 1.1 N (±0.5 N). This clearly points to a correlation between loading time (or velocity) and maximum force: the higher the loading velocity, the higher the measured force.

The calculated material parameters (E 1 , E 2 , and ε 12 ) of those samples that showed bilinear behavior of the PDL, as well as their median values and variances, are collected in Table II . A linear force/displacement relationship was measured in loading times shorter than 2 seconds due to restrictions of the setup. The reaction time of the position-sensitive detectors (an element of the optoelectronic part) and the following data collection are not fast enough for the short stress durations. The corresponding material parameters (E 1 ) are depicted in Table III . The results for samples 10 and 13 at a loading time of 2 seconds and for sample 10 at a loading time of 60 seconds could not be evaluated because of numeric instabilities.
Specimen | Loading time (s) | E 1 (MPa) | E 2 (MPa) | ε 12 (%) |
---|---|---|---|---|
1 | 2 | 0.04 | 0.20 | 6.0 |
5 | 0.03 | 0.20 | 6.0 | |
10 | 0.04 | 0.20 | 6.0 | |
60 | 0.04 | 0.20 | 6.0 | |
4 | 2 | 0.18 | 0.25 | 6.0 |
5 | 0.18 | 0.21 | 6.0 | |
10 | 0.11 | 0.20 | 8.0 | |
60 | 0.09 | 0.12 | 6.0 | |
5 | 2 | 0.06 | 0.40 | 6.0 |
5 | 0.06 | 0.28 | 4.0 | |
10 | 0.06 | 0.30 | 7.0 | |
60 | 0.03 | 0.20 | 8.0 | |
10 | 2 | – | – | – |
5 | 0.04 | 0.75 | 4.0 | |
10 | 0.03 | 0.65 | 4.0 | |
60 | – | – | – | |
13 | 2 | – | – | – |
5 | 0.04 | 0.45 | 6.0 | |
10 | 0.04 | 0.45 | 6.0 | |
60 | 0.05 | 0.20 | 5.0 | |
Median and variance | 2 | 0.06 (±0.02) | 0.25 (±0.01) | 6.0 (±0.0) |
5 | 0.05 (±0.02) | 0.28 (±0.05) | 6.0 (±1.2) | |
10 | 0.04 (±0.01) | 0.30 (±0.04) | 6.0 (±2.2) | |
60 | 0.04 (±0.01) | 0.20 (±0.01) | 6.0 (±1.6) |
Specimen | Loading time (s) | E 1 (MPa) |
---|---|---|
1 | 0.2 | 0.28 |
0.5 | 0.20 | |
1 | 0.20 | |
4 | 0.2 | 0.60 |
0.5 | 0.50 | |
1 | 0.46 | |
5 | 0.2 | 1.18 |
0.5 | 1.00 | |
1 | 0.85 | |
10 | 0.2 | 0.48 |
0.5 | 0.48 | |
1 | 0.42 | |
13 | 0.2 | 0.23 |
0.5 | 0.23 | |
1 | 0.21 | |
Median and variance | 0.2 | 0.50 (±0.12) |
0.5 | 0.48 (±0.10) | |
1 | 0.42 (±0.07) |
Figures 6-9 illustrate the median values and variances of the material parameters of the 5 fully examined samples. On the basis of the measured bilinear behavior at loading times above 2 seconds, 2 Young’s moduli (E 1 , E 2 ) and Poisson’s ratio (ε 12 ) were assessed. The diagram for E 1 ( Fig 6 ) shows a relationship between loading time and Young’s modulus. Here, the medians for E 1 were determined to be 0.06 MPa (±0.02 MPa) at 2 seconds and 0.04 MPa (±0.01 MPa) at 60 seconds loading times: The higher the loading velocity, the higher the corresponding Young’s modulus.




This correlation cannot be identified that clearly in the E 2 diagram ( Fig 7 , A ). The reason for this unclear relationship can be seen in Figure 7 , B . Obviously, specimen 10 displayed relatively high forces—ie, had high Young’s moduli. But at the same time, numeric instabilities did not allow determination of values for loading times of 2 and 60 seconds. As a result, median values for Young’s moduli at 5 and 10 seconds are enhanced, compared with 2 and 60 seconds. There was no obvious correlation between loading time and the ultimate strain ε 12 ( Fig 8 ). Figure 9 displays the notch boxes of the determined linear Young’s modulus E at loading times of 0.2, 0.5, and 1 seconds together with E 2 of the longer loading times. The time-dependant behavior with higher Young’s modulus at short loading times and decreasing values with increasing loading times is shown quite clearly.
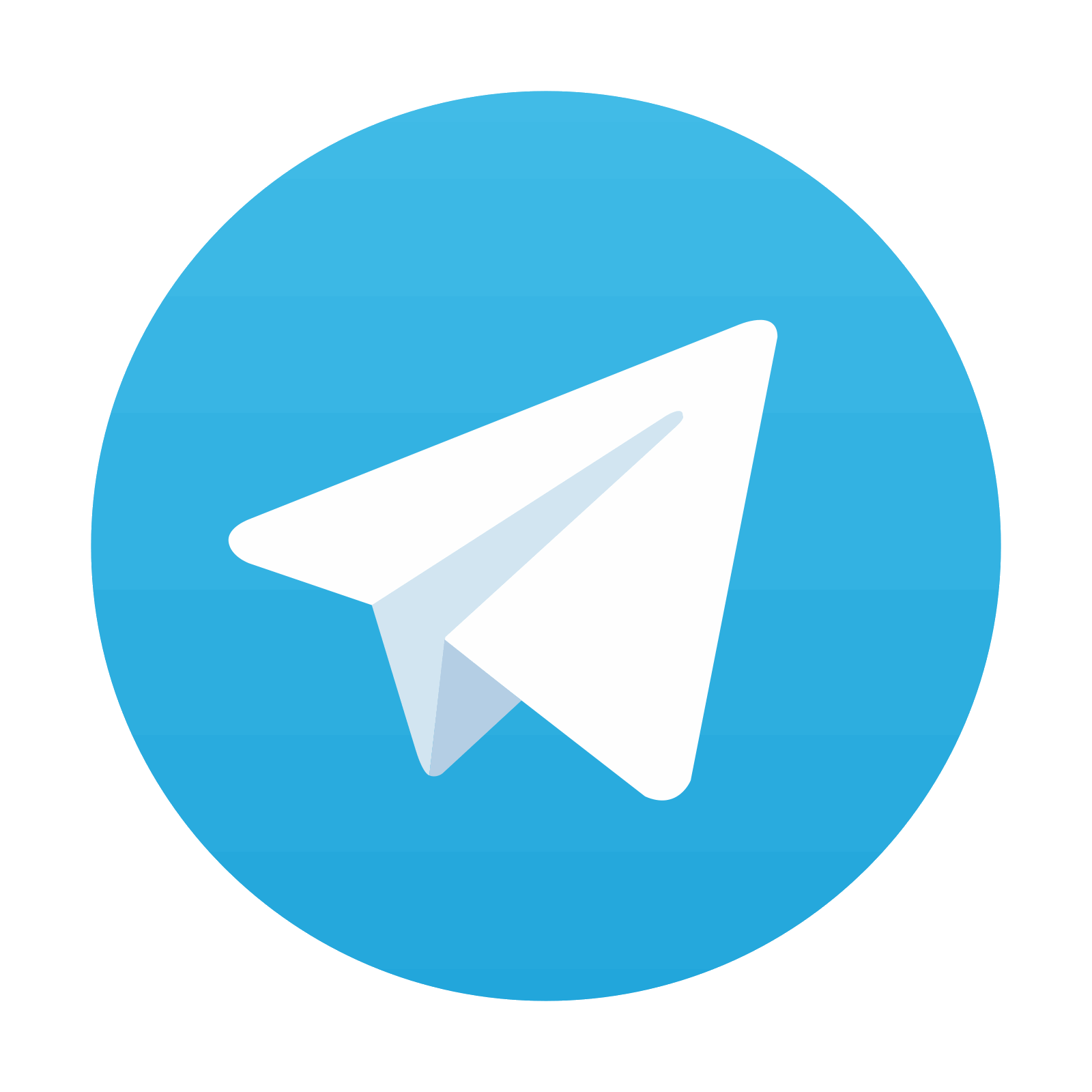
Stay updated, free dental videos. Join our Telegram channel

VIDEdental - Online dental courses
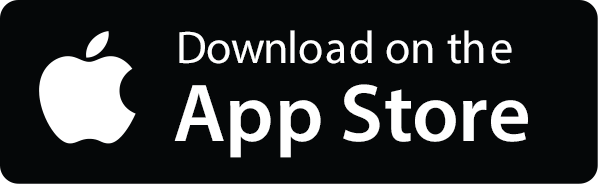
