In dentistry, several types of 3D resin printers are commonly used, each with its advantages and applications. 3D printing traces back to the 1980s. Each type of 3D resin printer has its strengths and limitations, and the choice of printer depends on factors such as desired resolution, printing speed, material compatibility, and budget. In dental practice, a combination of different types of resin printers may be used to meet the diverse needs of patients and clinicians. In summary, 3D-printing is likely to become a mainstay of every dental office with significant applications in prosthodontics, enhancing patient care pathways.
Key points
- •
Introduction to the History of 3-dimensional (3D) printing.
- •
An overview of hardware to faciliated 3D printing.
- •
Examples of scanning systems and how data accumulation works.
- •
Existing materials in 3D printing and evolution.
- •
An overview how accuracy is measured in 3D printing.
- •
Examples of software that can be used.
- •
Examples of open architecture workflows in restorative and surgical prosthodontics.
- •
An overview of artifical intelligence and future emerging technologies in 3D printing.
History of 3-dimensional printing
Three-dimensional (3D) printing, also known as additive manufacturing, traces back to the 1980s.
The Invention of Stereolithography (SLA): In 1983, Chuck Hull, a co-founder of 3D Systems Corporation, invented SLA, the first 3D printing technology. SLA involves curing layers of liquid resin with ultraviolet light to create 3D objects.
Development of Selective Laser Sintering (SLS): In the late 1980s, Carl Deckard and Joseph Beaman at the University of Texas at Austin developed selective laser sintering, another key 3D printing technology. SLS uses a laser to fuse powdered materials, layer by layer, to form objects.
Commercialization and Expansion: Throughout the 1990s, 3D printing technologies were further developed and commercialized. Companies like 3D Systems, Stratasys, and EOS began offering 3D printers for industrial and commercial use.
Patents Expire: By the late 2000s and early 2010s, many key patents related to 3D printing technologies began to expire, leading to an explosion of innovation and growth in the industry. This allowed for the emergence of new companies and the democratization of 3D printing technology.
Widespread Adoption: As the cost of 3D printers decreased and their capabilities expanded, 3D printing became increasingly accessible to individuals, hobbyists, and small businesses. This led to a surge in experimentation and innovation across various fields, including manufacturing, health care, aerospace, automotive, and more.
Hardware
Three-Dimensional Printing Systems in Dentistry
In dentistry, several types of 3D resin printers are commonly used, each with its advantages and applications.
Here are some of the most prominent types.
- 1.
Digital Light Processing (DLP) Printers: DLP printers utilize a digital light source, typically a projector, to selectively cure liquid resin layer by layer. These printers offer high resolution and fast printing speeds, making them well-suited for producing detailed dental models, prosthetics, surgical guides, and orthodontic appliances.
- 2.
SLA Printers: SLA printers operate similarly to DLP printers but use a laser to cure the resin instead of a digital light source. SLA printers also offer high resolution and accuracy, making them suitable for producing precise dental prosthetics, surgical guides, and orthodontic appliances.
- 3.
Liquid Crystal Display (LCD) Printers: LCD printers use an LCD screen to selectively cure liquid resin layer by layer. These printers offer fast printing speeds and can produce detailed dental models, prosthetics, surgical guides, and orthodontic appliances with high accuracy.
- 4.
Continuous Liquid Interface Production (CLIP) Printers: CLIP printers use a continuous liquid interface to cure liquid resin, allowing for rapid printing speeds and smooth surface finishes. These printers are capable of producing high-quality dental prosthetics, surgical guides, and orthodontic appliances with excellent accuracy.
- 5.
PolyJet Printers: PolyJet printers use inkjet printheads to selectively deposit photopolymer materials layer by layer. These printers offer high resolution and can produce multimaterial dental models, prosthetics, and surgical guides with varying levels of flexibility and color.
- 6.
MultiJet Printing (MJP) Printers: MJP printers use multiple printheads to selectively deposit photopolymer materials layer by layer. These printers offer high resolution and can produce detailed dental models, prosthetics, and surgical guides with excellent accuracy.
Each type of 3D resin printer has its strengths and limitations, and the choice of printer depends on factors such as desired resolution, printing speed, material compatibility, and budget. In dental practice, a combination of different types of resin printers may be used to meet the diverse needs of patients and clinicians ( Fig. 1 ).

The most popular printers in dental offices currently seem to be based on DLP technology. This is primarily because DLP allows for faster printing of multiple objects through the full projection of the outline of the object. Additionally, the cost, reliability, and value of these devices are well-suited for clinical dental practitioners.
LCD printers can also be used in the same setting, but they sometimes fall short compared with their DLP counterparts because of liability issues related to the LCD screen, even though LCD printers are generally more affordable.
SLA printers can create highly accurate prints, but they require more time because the curing laser has to trace the entire model layer by layer.
CLIP printers are reliable, fast, and very accurate. However, due to their higher cost, they are more commonly found in dental laboratories rather than in clinical settings.
Multijet and Polyjet printers offer advanced features such as multicolor or multimaterial printing, but they are not yet widely integrated into the broader dental market. As a result, these printers are not commonly seen in regular dental offices.
Scanning System and Data Accumulation
The 3D data that a 3D printer can accept for 3D printing depend on the software architecture of the printer and its own printing software. Intraoral scan data, cone beam computed tomography (CT) data, or desktop scan data can be in an open format or a closed format .
A closed system data structure is a self-contained environment where data can only be accessed, modified, and utilized by the specific software or application it resides in. Interfacing with external systems or applications is restricted or nonexistent. This is mainly due to the proprietary formats. (Restricted to specific applications.)
An open system data structure is designed for interoperability and accessibility, allowing data to be easily shared, accessed, and modified by various software applications and systems. This is mainly using standard formats at.stl, .ply, .obj, or in the case of the cone beam computer tomographie (CBCT) DICOM (Digital Imaging and Communications in Medicine) at standard formats. This allows collaboration and sharing over different platforms. (Accessible to various applications.)
We recommend working in an open architecture format (system), to be as flexible as possible in any situation and not to be dependent on changes in systems, vendors, and software that can disrupt entire reestablished workflows. That is why this article will essentially focus on the open architecture workflows.
File Formats
The scanner (intraoral or desktop) should be able to scan the object and export it in .stl, .ply, and .obj formats. A CBCT should be able to scan the hard tissue and export it in a DICOM format
STL—surface of an object that has no information about color or texture only geometry.
PLY—surface of an object that has information over the surface, color, and texture including geometry.
OBJ—surface of an object that has information over the surface, color, and texture including geometry. It is also a larger file but is considered a standard in 3D data.
DICOM—DICOM standardizes the format for medical images and the protocols for transmitting them across different devices and systems. It ensures compatibility and interoperability between imaging devices (like X rays, MRIs, and CT scanners) and software from different manufacturers.
Materials in 3-Dimensional Printing
There are many material options in 3D printing. For that reason, we will focus on the more commonly used materials in a (prosthodontics) private practice setting. We will not cover metals in this section, as these types of printers are rarely used in a private practice setting ( Fig. 2 ).
- 1.
Resins might be the largest group :
- •
Biocompatible Resins: Used for applications that require direct contact with the human body, such as dental implant crowns, surgical guides, temporary crowns, appliances, and removable prostheses.
- •
Castable Resins: Used for creating castable patterns for metal crowns and bridges.
- •
Nonbiocompatible Resins: Used for dental casts, study models, gingival masks, and custom impression tray materials.
- •
- 2.
Hybrid resins—a group that has ceramic particles in the resin matrix to enhance the properties and the esthetics
- •
Biocompatible Temporary Hybrid Resins: Used for reinforced temporary crowns, reinforced denture bases, and full fixed implant-supported temporary prototypes.
- •
- 3.
Hybrid Resin Ceramics—qualified by the American Dental Association (ADA) and Food and Drug Administration (FDA) to be cemented as a final crown if the ceramic content is over 50%. ,
- •
Currently, the maximum content of ceramic particles in these types of final restorations is around 70%. The limitation is due to the viscosity of the material and the error in the print consistency if the content is too high. New printing concepts seem to overcome this issue with different 3D printing formulas that will be covered later ( Figs. 3 and 4 ).
Fig. 3 Nano hybrid printing material.( With permission from SprintRay Inc.)Fig. 4 Final insertion and 3D print of ceramic hybrid materials.
- •
- 4.
Ceramics

Lithium Disilicate , : Known for its strength and esthetics, it is used in permanent restorations and is typically milled. This material has now been successfully 3D printed. However, due to the high cost of 3D printers, this type of printer is rarely seen in private practice environments ( Fig. 5 ).

Zirconia : Used for permanent crowns and bridges because of its high strength and biocompatibility. Zirconia 3D printing has been experimental for a long time without achieving the same quality as its already existing milled counterpart. The issue appears to be inconsistent printing layers, resulting in zirconia that is less durable and has low fracture resistance after sintering.
- 5.
Nylon , for filament-based 3D printing (fused deposition modeling [FDM]) is not as accurate as resin printing but can be used for dental appliances that do not need that high level of accuracy but can benefit from the flexibility of the material.
- •
Polyamide (Nylon): Used for flexible partial dentures due to its flexibility and strength.
- •
Applications
- •
Flexible partial dentures
- •
Surgical guides
Accuracy
In 3D printing, the X , Y , and Z axes are used to define the spatial dimensions and movement of the print head or build platform. Here is a breakdown of what each axis represents ( Fig. 6 ):
- 1.
X and Y Axes: These axes typically refer to the horizontal movement of the print head or the build platform along the width of the printer. The X axis runs left to right when facing the printer. The Y axis represents the horizontal movement perpendicular to the X axis. When facing the printer, the Y axis usually runs front to back.
- 2.
Both the X and Y axes define the pixel size in microns of the light that cures the resin. For example, if a printer has 50 micron accuracy, it refers to the square micron area created by the X and Y axes. Current contemporary dental resin printers operate in this range.
- 3.
Z Axis: The Z axis is the vertical axis, controlling the upward and downward movement of the print head or build platform. This axis determines the layer height or thickness of each layer being printed. The Z axis moves the print head or builds the platform up or down. The Z axis is responsible for the “slice” or “layer” aspect of the printed object. The layer height is typically set by the slicing software of the printer.

Accuracy in 3D printing is usually defined by trueness and precision . Trueness refers to how closely the dimensions of the printed object match those specified in the 3D model and precision refers to the consistency of achieving accurate results across multiple prints of the same object. A printer with good repeatability can consistently reproduce the same dimensions and details ( Fig. 7 ).

Factors that must be considered include the calibration of the printer, the tolerance allowed by the printer for deviations from the intended dimensions, which is further influenced by the material properties of the resin, and temperature fluctuations. Other studies have suggested that the support features of the printed object can influence accuracy; specifically, the more and thicker the support structure, the less accurate the print result may be. Further studies have examined the angulation of 3D printed objects in the nesting software of printers. However, the results did not conclusively determine that the angulation of the object is a decisive factor. Adding glycerin can improve the adhesion of certain materials to the printer-building platform. Glycerin can act as a binder or adhesive promoter, helping to enhance layer adhesion and overall print quality.
Achieving high accuracy in 3D printing involves selecting appropriate print settings, optimizing slicing parameters, ensuring printer calibration, correct ultra violet (UV) wavelength, and sometimes postprocessing techniques to refine the final output.
Software
In dentistry, computer-aided design (CAD) software is commonly used for designing dental restorations such as crowns, bridges, implants, and orthodontic appliances. Some popular CAD software used in dentistry includes:
- 1.
Exocad : Offers flexible CAD software solutions for designing dental prosthetics with a user-friendly interface.
- 2.
DentalCAD by 3Shape : Specifically designed for dental professionals, offering advanced tools for designing dental restorations.
- 3.
Dental Wings : Provides CAD software solutions for dental laboratories focusing on precision and efficiency in designing dental prosthetics.
- 4.
Planmeca Romexis : Includes a range of CAD/computer aided manufacturing (CAM) modules for various dental applications, including designing and manufacturing dental restorations.
- 5.
Exoplan: A comprehensive software solution designed for dental implant planning and surgical guide design. It is developed by Exocad.
- 6.
BlueSkyBio: Specializes in providing digital solutions for dental professionals, particularly in the fields of implantology, guided surgery, and digital dentistry.
- 7.
Nondental Software: If the files are in an open format, nondental 3D software as Blender, Zbrush, and Meshmixer is sometimes used due to their sandbox format.
Nesting Software plays a crucial role in optimizing the arrangement of dental models, prosthetics, or other objects within the build platform of the 3D printer. The goal is to maximize efficiency, minimize material usage, and ensure high-quality printing outcomes. Key points about nesting software include:
- 1.
Optimization of Space : Nesting software automatically arranges multiple dental models or prosthetics on the build platform in a way that maximizes the use of available space. This helps in reducing material waste and optimizing printing time.
- 2.
Support for Different Printers and Materials : Good nesting software supports a variety of 3D printers and materials. The software considers factors such as printer specifications, material properties, and print settings to optimize the nesting arrangement. Although, most 3D printing systems come with their nesting software.
- 3.
Accuracy and Precision : The software ensures that each model or prosthetic is positioned accurately on the build platform, taking into account factors like support structures.
- 4.
Integration with CAD/CAM Systems : Some nesting software solutions integrate seamlessly with CAD/CAM systems used in dental practices, allowing for direct import of digital designs and streamlined workflow from design to printing.
Nesting Software Examples
- •
Materialise Magics : Although widely used across various industries, it offers powerful nesting features suitable for dental applications ( Fig. 8 ).
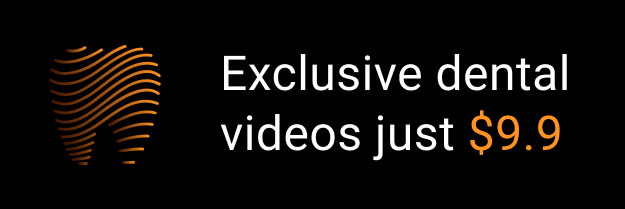