Objectives : To describe one method for the three-dimensional finite element modeling of dental implant by combining micro-CT technique and Mimics software.
Materials and methods : One dental titanium implant with abutment (Bone Level RC, Straumann, Switzerland) was scanned using X-ray micro-CT scanner (Skyscan1172, Skyscan, Belgium) with exposure time of 1180 ms and pixel size of 6.97 μm. 3749 slice images were generated and then processed by an interactive medical image control system (Mimics X64 13.0, Materialise, Belgium). The 3D objects of implant and abutment were generated from different masks which were automatically extracted using thresholding and region growing tools based on the grey values. The MedCAD tool was used to create the cylindrical fixture and hemispherical cap in order to simulate the fatigue testing according to ISO 14801. These different parts were incorporated into non-manifold assembly and remeshed simultaneously in the Mimics Remesher. The volume meshes were generated, and material properties were assigned using FEA/CFD tool. Finally the meshed models were imported and analyzed in the Finite Element Analysis (FEA) software (ABAQUS V6.8-4, Simulia, US).
Results : The 3D model showed good and detailed physical resemblance with the actual structure of the implant. Comparative measurements revealed that the dimensional error of this micro-CT based FEA modeling did not exceed 0.64%. FEA models with three different levels of mesh refinements (11991, 17209 and 50758 elements, respectively) were easily generated by controlling triangle edge length in Mimics Remesher and the use of non-manifold assembly ensured the matching surfaces and coinciding nodes between different parts. Maximum stress concentration occurred around the contact area of implant and fixture for all the models and showed good convergence.
Conclusions : Accurate and valid three-dimensional finite element models of dental implant can be generated rapidly by combining micro-CT techniques and Mimics software, which will be used in the further fatigue study of dental implant.
The study is supported by NIH-NIDCR grants DE017991 and DE013358.
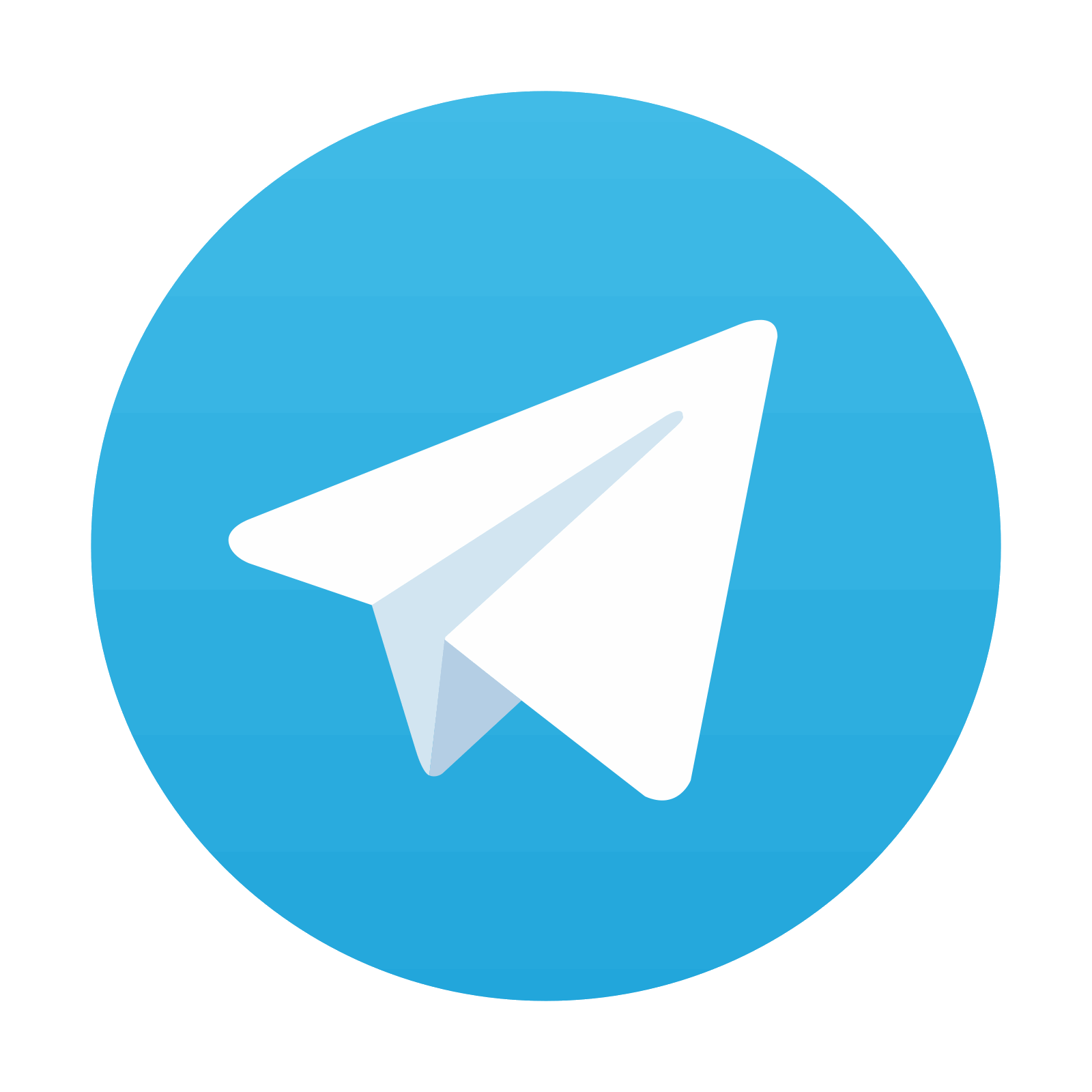
Stay updated, free dental videos. Join our Telegram channel

VIDEdental - Online dental courses
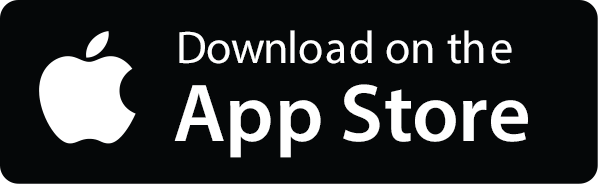
