Graphical abstract
Highlights
- •
Increase in degree of conversion and reduction in Rp max .
- •
Reduction in volumetric shrinkage and polymerization stress.
- •
Significant increase in toughness and fracture toughness.
- •
Increased flexural strength.
Abstract
Thio-urethanes were synthesized by combining 1,6-hexanediol-diissocyante (aliphatic) with pentaerythritol tetra-3-mercaptopropionate (PETMP) or 1,3-bis(1-isocyanato-1-methylethyl)benzene (aromatic) with trimethylol-tris-3-mercaptopropionate (TMP), at 1:2 isocyanate:thiol, leaving pendant thiols. Oligomers were added at 10–30 phr to BisGMA-UDMA-TEGDMA (5:3:2, BUT). 25 wt% silanated inorganic fillers were added. Commercial cement (Relyx Veneer, 3M-ESPE) was also evaluated with 10–20 phr of aromatic oligomer. Near-IR was used to follow methacrylate conversion (DC) and rate of polymerization (Rp max ). Mechanical properties were evaluated in three-point bending (ISO 4049) for flexural strength/modulus (FS/FM, and toughness), and notched specimens (ASTM Standard E399-90) for fracture toughness ( K IC ). Polymerization stress (PS) was measured on the Bioman. Volumetric shrinkage (VS, %) was measured with the bonded disk technique. Results were analyzed with ANOVA/Tukey’s test ( α = 5%).
In general terms, for BUT cements, conversion and mechanical properties in flexure increased for selected groups with the addition of thio-urethane oligomers. The aromatic versions resulted in greater FS/FM than aliphatic. Fracture toughness increased by two-fold in the experimental groups (from 1.17 ± 0.36 MPa m 1/2 to around 3.23 ± 0.22 MPa m 1/2 ). Rp max decreased with the addition of thio-urethanes, though the vitrification point was not statistically different from the control. VS and PS decreased with both oligomers. For the commercial cement, 20 phr of oligomer increased DC, vitrification, reduced Rp max and also significantly increased K IC , and reduced PS and FM.
Thio-urethane oligomers were shown to favorably modify conventional dimethacrylate networks. Significant reductions in polymerization stress were achieved at the same time conversion and fracture toughness increased.
1
Introduction
Bonded indirect restorations play a major role in contemporary dentistry . Resin cements have become popular clinically because of their ability to bond both to the tooth structure and to the restoration . Examples of their clinical applications include adhesion of ceramic fragments, crowns, bridges, and intra-canal posts. Due to the necessary (and sometimes excessive) taper on tooth preparations, and to constant incidence of tensile, compressive and oblique loads, resin cements must have high mechanical properties, as well as resistance to dissolution and strong bond to structures .
Conventional resin cements are based on methacrylate monomers which undergo vitrification at early stages of polymerization , increasing the strain/stress at the bonded interface and in the bulk of the material structure . This condition increases the risk of gap formation at the interface of cementation, which may lead to an increase of the material solubility, microleakage and staining, ultimately compromising the longevity of treatment . Based on the confined geometry in which the cement is applied, current operatory techniques available are not efficient in avoiding the development of strain/stress during the indirect restoration placement and, therefore, the solution to minimize stress generation needs to be based on improvements made directly to the material .
The use of thiol-enes has been proposed in dental composites, with successful results as stress reducing agents. The step growth nature of the thiol-ene and thiol-methacrylate polymerizations, given by chain-transfer reactions of the thiol to the ene/vinyl, leads to more homogeneous network formation and ultimately increased conversion in comparison to the pure methacrylate counterparts and for selected compositions, improvements in flexural strength, depth of cure and water solubility have also been reported . However, concerns over the somewhat compromised mechanical properties and the stability (shelf-life) of the fully formulated composite materials have delayed the commercial translation of thiol-ene-based materials . Another concern that applies to small molecule thiols is the foul odor associated with the material.
As an alternative to conventional thiol-enes or thiol-methacrylates, others have proposed the use of thio-urethane networks in applications where mechanical properties in general, but more specifically toughness and resistance to impact, are desirable . Some studies have demonstrated the more homogeneous nature of thio-urethane networks compared to the simple urethane counterparts, as well as the increased toughness values . In those studies, thiols are combined with isocyanates in situ , in a reaction catalyzed by a base. Currently, these are two-part systems (at least until compounds such as photo-base generators are readily accessible – , not suitable for dental composite applications. However, previous studies have demonstrated it to be possible to synthesize high molecular weight pre-polymerized thio-urethane oligomers to be later added to a secondary monomer matrix, polymerizable through a radical mechanism . When the oligomer is designed to have pendant thiols from the backbone, chain-transfer reactions to the surrounding methacrylate matrix result in delayed gelation and vitrification and, as consequence, reduction in polymerization stress . Due to the high molecular weight, reductions in the volumetric shrinkage are also expected, as well as the elimination of the odor concerns. Importantly, thiol-terminated thio-urethanes are capable of forming a more homogeneous network with the methacrylate, and also increase final conversion .
Therefore, the objectives of this study were to synthesize thiol-terminated thio-urethane oligomers with different backbone structures and to assess the properties of methacrylate-based resin cements modified with the oligomers. The hypotheses of this study were that the use of thio-urethanes would (I) increase the degree of conversion, (II) improve the material mechanical properties and (III) reduce the volumetric shrinkage/polymerization stress.
2
Materials and methods
2.1
Experimental materials composition
The experimental resin cement formulated for the study (BUT) was composed of Bis-phenol A diglycidyl dimethacrylate (Bis-GMA; Esstech, Essington, PA, USA), urethane dimethacrylate (UDMA; Esstech) and tri-ethylene glycol dimethacrylate (TEGDMA; Esstech) in a 50:30:20 mass ratio. Photoinitiators were added to the matrix as follows: 0.6 wt% of a tertiary amine (EDMAB – ethyl 4-dimethylaminobenzoate; Avocado, Heysham, England), 0.2 wt% of dl -camphoroquinone (Polysciences Inc., Warrington, PA, USA), and 0.5 wt% inhibitor (BHT – 2,6-di-tert-butyl-4-methylphenol; Sigma–Aldrich, St. Louis, MO, USA).
Oligomers were synthesized in solution (methylene chloride) by combining 1,6-hexanediol-diissocyante (HDDI) (aliphatic) with pentaerythritol tetra-3-mercaptopropionate (PETMP) or 1,3-bis(1-isocyanato-1-methylethyl)benzene (BDI) (aromatic) with trimethylol-tris-3-mercaptopropionate (TMP), at 1:2 isocyanate:thiol molar ratio, leaving pendant thiols. Triethylamine was used as a base in catalytic amounts. Oligomers were purified by precipitation in hexanes and rotaevaporation, and then characterized by 1 H-NMR and mid-IR spectroscopy . The disappearance of the isocyanate peak at 2270 cm −1 and the appearance of resonance signals at 3.70 ppm were used as evidence for completion of isocyanate reaction and thio-urethane bond formation, respectively . Thio-urethane oligomers were added to the methacrylate organic matrix in proportions of 0 (control), 10, 20 and 30 parts per hundred resin, phr (which corresponds to 9.1 wt%, 16.7 wt% and 27.7 wt%, respectively).
Filler was introduced at 25 wt% (15% OX-50 – 0.04 μm; 85% Barium glass 0.7 μm, density 3.0 g/ml, refractive index 1.553 – V117 4107, Esstech), with the aid of a mechanical mixer (DAC 150 Speed mixer, Flacktek, Landrum, SC, USA) for 5 min at 2400 rpm. All procedures were carried out under yellow lights.
One commercial light-cured cement (RelyX Veneer, 3M Espe, St. Paul, USA – lot N521803; Ref 7614A1, A1/light yellow shade) composed by BisGMA/TEGDMA and 66 wt% zirconia/silica filler was modified by addition of 10 phr and 20 phr of aromatic oligomer to the organic matrix (or 9.1 wt% and 16.7 wt%, respectively). The unmodified cement served as the commercial control.
2.2
Photopolymerization reaction kinetics and degree of conversion
The degree of conversion (DC) was obtained using near-infrared (NIR) spectroscopy in specimens of 10 mm in diameter and 0.8 mm thick laminated between two glass slides. The methacrylate CH 2 absorption at 6165 cm −1 was recorded before and after 60 s of irradiation at 700 mW/cm 2 (Bluephase, Ivoclar vivadent, Lichtenstein) with the light source in direct contact with the glass slide mold. Real-time monitoring of the polymerization kinetics was carried out in specimens of the same size at 2 scans per spectrum with 4 cm −1 resolution, which provides a greater than 2 Hz data acquisition rate. Kinetic data was collected continuously for 5 min. Samples ( n = 3) were irradiated for 60 s at an incident irradiance of 550 mW/cm 2 . The light attenuation in this case was due to a distance of 2 cm separating the tip of the light guide and the surface of the specimen.
2.3
Flexural strength, elastic modulus and toughness
Flexural strength of the samples was measured according to the 3-point bending method carried out with a universal test machine (Q-test, MTS, Eden Prairie, WI) at a cross-head speed of 0.5 mm/min. The bar specimens were prepared in dimensions of 2 mm × 2 mm × 25 mm according to ISO 4049 . The specimens ( n = 10) were fabricated between glass slides and photopolymerized with three overlapping 60 s exposures at 700 mW/cm 2 . Specimens were stored for one week in dark containers at room temperature. The flexural strength (FS) in MPa was then calculated as:
F S ( σ ) = 3 F l 2 b h 2
where F stands for load at fracture ( N ), l is the span length (20 mm), and b and h are the width and thickness of the specimens in mm, respectively.
The elastic modulus was determined from the slope of the initial linear part of stress–strain curve.
E = F l 3 4 b h 3 d
where F is the load at some point on the linear region of the stress–strain curve; d is the slack compensated deflection at load F ; l , b , and h are as defined above.
Toughness was calculated in MPa from the integration of the stress x strain curve using software (Origin 9.1, OriginLab Corporation, Northampton, MA, USA).
2.4
Volumetric shrinkage
The bonded disk method was used to evaluate volumetric shrinkage . Resin cements were placed into a brass ring of approximately 16 mm in diameter and 1.5 mm in height bonded to a glass slide. The cement ( n = 5) was placed so that it did not come in contact with the brass ring, and then the assembly was covered with a microscope cover slip (approximately 0.1 mm thick). A linear variable differential transducer (LVDT) probe was placed in contact with the center of the cover slip. The cement was photoactivated for 60 s at an incidence of 700 mW/cm 2 . As the cement cures and shrinks, it pulls the cover slip down and its deflection is monitored by the LVDT probe. Displacement data was obtained from the signal output of the transducer (in mV). The volumetric shrinkage (%VS) value was calculated as follows:
% VS = ( V f − V i ) × f h × 100
where V f is the final displacement value given after polymerization and, V i , is the initial value given by the LVDT probe, in mV, f is the multiplier from the calibration curve and h , is the cement specimen thickness after the polymerization, in μm.
Conversion-based predicted shrinkage was calculated according to the equation :
VS = [ C C ] × D C × κ
where [C C] 0 is the initial carbon–carbon double-bond concentration (in mol/mL); DC is the fractional degree of conversion and κ is the molar shrinkage coefficient for methacrylates (20.4 mL/mol) . Experimental and conversion-based predicted polymerization shrinkage results were compared to highlight the possible effect of phase-separation on dimensional change.
2.5
Polymerization stress
Polymerization stress development was followed in real-time using the Bioman, described previously . This system consists of a cantilever load cell whose extremity is fitted to a rigid integral clamp on its free end. The clamp holds a 10 mm diameter and 22 mm tall steel rod vertically and perpendicular to the load cell axis. A 5-mm diameter, 0.5-mm tall steel rod was fixed at the center of the lower face of the standard rod with a cyanoacrylate adhesive to produce a rod substrate with a reduced surface area to be consistent with a C-factor of 4. The surface of the rod was treated with a thin layer of Metal primer (Z-prime plus, Bisco, Schaumburg, IL). The opposite surface was a rigid fused silica glass plate of 3 mm thickness, treated with a thin layer of silane ceramic primer (3 M ESPE, St. Paul, MN, USA). The cement ( n = 5) was then inserted into the 0.5-mm gap between the upper rod and the lower glass slide and shaped into a cylinder. The specimens were photoactivated through the glass during 60 s at an incident irradiance of 700 mW/cm 2 (Bluephase) and the stress followed for 500 s. The load signal from the cantilever cell was amplified and acquired by a computer.
2.6
Fracture toughness
The fracture toughness of all materials was determined from the stress intensity factor ( K ) during crack propagation. To determine the fracture toughness (FT), single-edge notch beam (SENB) specimens ( n = 5) were fabricated according to ASTM Standard E399-90 in a 5 mm × 2 mm × 25 mm split steel mold with a razor blade providing a 2.5 mm notch in the center of the specimens. The cement was photoactivated for 60 s at an incidence of 700 mW/cm 2 . The bending fracture test was performed at a cross-head speed of 0.5 mm min −1 using a universal test machine ( Q -test) and the fracture toughness (critical stress intensity factor, K IC ) was calculated according the following equation:
K IC = 3 P L 2 B W 3 / 2 1.93 a W 1 / 2 − 3.07 a W 3 / 2 + 14.53 a W 5 / 2 = 25.11 a W 7 / 2 + 25.8 a W 9 / 2
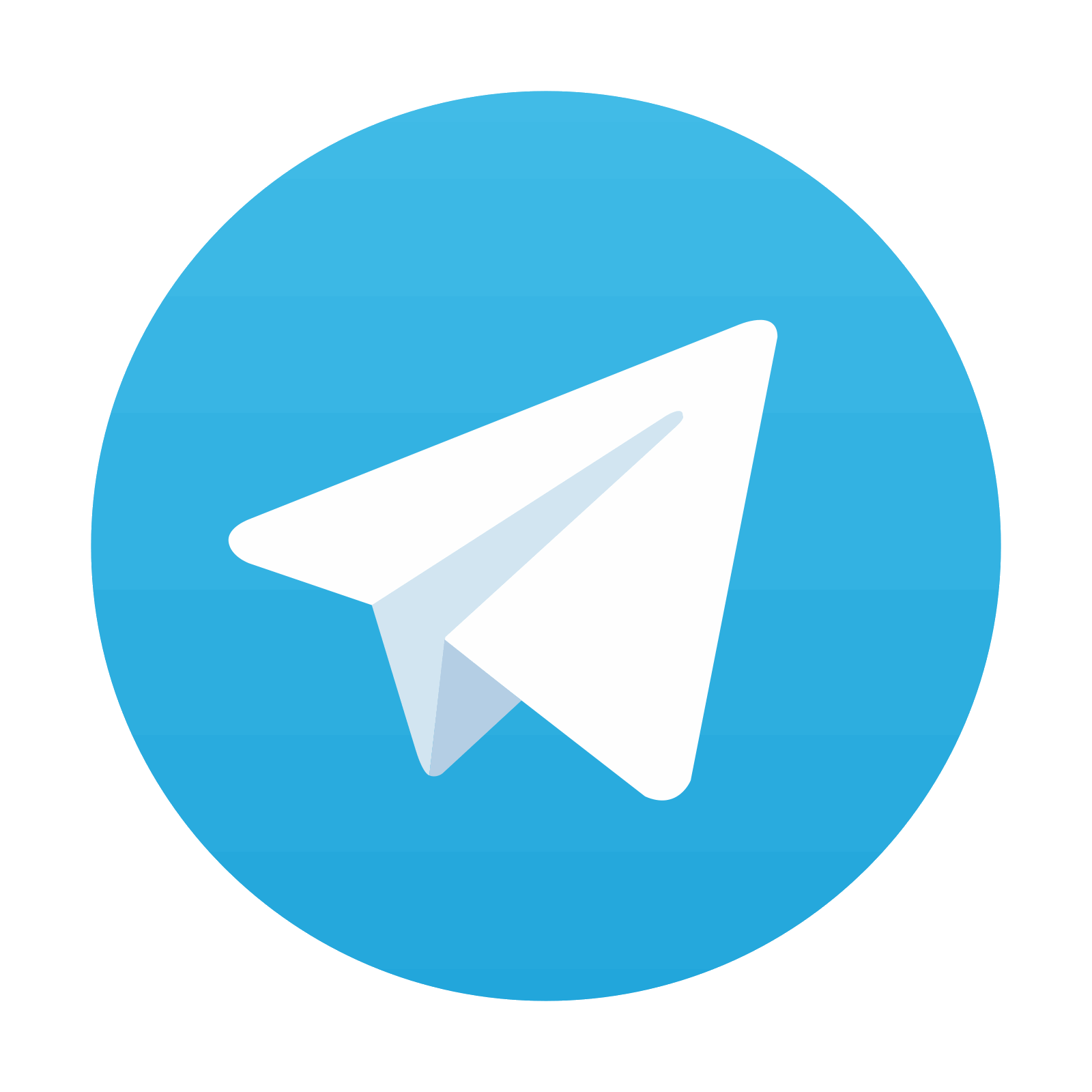
Stay updated, free dental videos. Join our Telegram channel

VIDEdental - Online dental courses
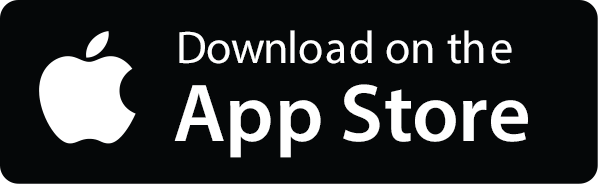
