Abstract
Objectives
To assess the repair potential of resin-modified glass-ionomer cements (RMGICs) with additional RMGIC and resin composite.
Methods
Specimens of two proprietary RMGICs (Ketac N100 (Ketac Nano), 3M/ESPE, St Paul, MN; Fuji II LC, GC Corporation, Tokyo) were prepared and stored in water at 37 °C for 4 days. The surface of the RMGIC was finished flat with 600-grit silicon carbide paper. After treatment of the original surface by either phosphoric acid or polyacrylic acid for 20 s, fresh RMGIC of the same brand was added in a plastics cylinder. Untreated specimens were used as a control. Further specimens were either left untreated (control) or etched with phosphoric acid for 20 s, and resin composite added. Specimens were stored in water at 37 °C for 24 h, and the shear bond strength measured. The fractured surfaces were examined for mode of failure. Additional RMGIC specimens were prepared for the examination of replicas of the finished and acid treated surfaces.
Results
The bond strength of new Ketac N100 to old Ketac N100 was in the order of 1.7 MPa, irrespective of the surface treatment, and many specimens failed before testing. The bond strength of new Fuji II LC to old Fuji II LC was in the order of 10 MPa, irrespective of the surface treatment. The bond strength of resin composite bonded to both RMGICs approximated 9–16 MPa. The mode of failure of the RMGIC to RMGIC bond varied depending on the products, and the mode of failure of the resin composite to RMGIC bond was predominantly cohesive in the RMGIC. SEM examination of the RMGIC surfaces showed little effect from acid treatment.
Significance
Based on this laboratory study, repair of RMGIC with additional RMGIC maybe clinically unpredictable, depending on the products used; repair with resin composite appears to be the preferred option.
1
Introduction
Glass-ionomer cements (GICs) became available in the late 1970s, essentially by reacting a polyalkenoic acid with a fluoroaluminosilicate glass . The resulting materials, so-called ‘conventional’ GICs, had some disadvantages in handling properties, aesthetics and strength, making them unsuitable in stress-bearing areas due to their potential for fracture. In addition, conventional GICs were susceptible to degradation in an acidic environment, for example in patients who are subject to corrosion (‘erosion’) from intrinsic and extrinsic acid. Continued development led to the introduction of the ‘resin-modified glass-ionomer cements’ (RMGICs) , which by the addition of a water-soluble resin, resulted in a material which was somewhat stronger and had better aesthetics.
Resin-modified GICs now have an established and important place in restorative dentistry, both as final restorative materials and as luting cements, lining cements and pit and fissure sealants. They are particularly useful where reliable, long-term adhesion is required, such as in non-carious cervical lesions , and there is some evidence that they maybe associated with a reduced incidence of secondary caries and also the remineralization of ‘affected’ (inner carious) dentin . Nevertheless, like all water-based cements, brittleness remains a fundamental property, which may occasionally lead to fracture or wear. There is thus the clinical need to be able to repair GIC by the addition of fresh material, and this may also be required if a cavity is under-filled due to a technique error or if there is unaesthetic marginal staining.
Repair of resin composite has been extensively studied, and is becoming a routine clinical procedure as it contributes to the philosophy of ‘minimum intervention’ operative dentistry . Repair of amalgam restorations is also a viable clinical procedure for the same reasons . However, there are few reports on the repair strength of RMGICs .
The aim of the present study was to measure the SBS of repairs of two RMGICs, using either the same RMGIC or a resin composite as the repair material, and assessing the effect of either phosphoric acid etching or polyacrylic acid conditioning as a pre-repair treatment.
2
Materials and methods
Epoxy resin was cast into polyvinylchloride (PVC) cylinders, 15 mm high × 22 mm external diameter × 18 mm internal diameter. After setting, an 8.5-mm dia recess, approximately 4 mm deep, was drilled centrally on one surface, and slightly undercut using an inverted cone bur in a slow-speed handpiece. Resin-modified glass-ionomer cement was mixed according to the manufacturer’s instructions, the recess overfilled with the material, covered with a plastics matrix strip and a glass microscope slide firmly pressed onto the matrix strip. The RMGIC was photocured for 20 s with a quartz halogen curing light (Elipar TriLight; ESPE, Germany) with a light intensity of >750 W/cm 2 , the microscope slide and matrix removed, the specimen checked for the presence of a uniform surface and if satisfactory the cylinder placed in water at 37 °C. Seventy-five specimens of each of Ketac N100 (also known as ‘Ketac Nano’; 3M ESPE, St Paul, MN) and Fuji II LC (GC Corporation, Tokyo, Japan) were prepared.
After 4 days, the surface of the RMGIC and embedding resin were lightly abraded with wet 600-grit silicon carbide paper until a uniform matt surface was visible, washed and blot dried. A piece of plastics adhesive tape, approximately 10 mm square with a 4.95-mm dia hole, was placed centrally over the RMGIC surface and firmly burnished down. An acrylic tube, 5.8 mm internal diameter × 4 mm high, was lubricated lightly internally with silicone oil and fixed centrally over the hole in the plastics tape using two small spots of sticky wax on its opposite sides.
The 75 specimens of each RMGIC were divided randomly into five groups if 15 specimens for ‘repair’ with either RMGIC or resin composite, as described in Table 1 (Ketac N100) and Table 2 (Fuji II LC). The respective RMGIC materials were syringed into the acrylic cylinders using either a ‘Centrix’ syringe (Ketac N100) or the manufacturer’s mixing capsule (Fuji II LC), and the resin composite packed into the ring using a plastic instrument. The ‘repair’ material was photocured for 20 s and the specimens stored in water at 37 °C.
Group 1 | Group 2 | Group 3 | Group 4 | Group 5 |
---|---|---|---|---|
Remove from water, blot dry, apply adhesive tape | ||||
Apply primer a , 15 s | Apply conditioner b , 20 s | Etch c , 20 s | Etch c , 20 s | Apply unfilled resin d , 15 s |
Air syringe dry, 10 s | Wash, 5 s | Wash, 5 s | Wash, 5 s | Air thin, 5 s |
Photocure, 10 s | Blot dry | Blot dry | Blot dry | Photocure, 20 s |
Apply primer a , 15 s | Apply primer a , 15 s | Apply unfilled resin d , 15 s | ||
Air syringe dry, 10 s | Air syringe dry, 10 s | Air thin, 5 s | ||
Photocure, 20 s | ||||
Apply plastics ring; mix and place Ketac N100; photocure 20 s; store in water at 37 °C | Apply plastics ring; place resin composite e ; photocure 40 s; store in water at 37 °C |
a Ketac Nano-ionomer Primer (3M ESPE, St Paul, MN; Lot No. 7AA).
b GC Dentin Conditioner (GC Corporation; Lot No. 070981).
c Scotchbond Etching Gel (3M ESPE; Lot No. 8NA).
Group 6 | Group 7 | Group 8 | Group 9 | Group 10 |
---|---|---|---|---|
Remove from water, blot dry, apply adhesive tape | ||||
Apply adhesive a , 10 s | Apply conditioner b , 20 s | Apply etch c , 20 s | Etch, 20 s | Blot dry |
Air stream dry, 10 s | Wash, 5 s | Wash, 5 s | Wash, 5 s | Apply adhesive a , 10 s |
Photocure, 10 s | Blot dry | Blot dry | Blot dry | Air thin, 5 s |
Apply adhesive a , 10 s | Apply adhesive a , 10 s | Apply adhesive a , 10 s | Photocure, 10 s | |
Air stream dry, 5 s | Dry, 10 s | Air thin, 5 s | ||
Photocure, 10 s | Photocure, 10 s | Photocure, 10 s | ||
Mix and place Fuji II LC; photocure 20 s; store in water at 37 °C | Apply plastics ring; place resin composite d ; photocure 40 s; store in water at 37 °C |
a G-Bond (GC Corporation; Batch No. 0805031).
b GC Dentin Conditioner (GC Corporation; Lot No. 070981).
After 1 day, the acrylic cylinder and the tape were removed, the specimen placed in a shear jig consisting of a steel plate with a blunt edge, 1.2 mm thick × 30 mm across ( Figs. 1 and 2 ), such that the ‘new’ material could be loaded in shear with the plate against the ‘old’ material. Then jig was placed in a universal testing machine (Model 8872; Instron Co Ltd., UK), the cylinder of ‘new’ material loaded at 0.75 ± 0.25 mm/min until failure and the shear bond strength (SBS) calculated from the known diameter of the bonded surface (4.95 mm) by the data acquisition software. Specimens which failed prior testing were assigned a notional SBS of 0 MPa. The data were analyzed using one-way analysis of variance (ANOVA) and t -tests.
The fractured surface of each specimen was examined using a light microscope at 2× magnification, and the mode of failure assessed as either ‘adhesive’, ‘cohesive in ‘old’ material’, ‘cohesive in new material’ or ‘mixed’ (partly cohesive in the ‘old’ material, partly cohesive in the new material and partly adhesive at the interface).
Further specimens of each RMGIC were prepared in epoxy cylinder moulds for examination with a scanning electron microscope (SEM) of the various surface preparations, as follows: a polyvinylsiloxane (PVS) impression (Provil, Heraeas Kulzer, Germany) was taken of the matrix-finish surface of the RMGIC, followed by impressions after preparing the 600-grit surface, after etching with phosphoric acid and after conditioning with polyacrylic acid/aluminum chloride. Prior to the latter three impressions, the surface of the RMGIC was washed and blotted dry. The PVS impressions were cast in epoxy resin, gold coated and examined with an SEM (JSM-5310LV; Jeol Co., Tokyo, Japan).
2
Materials and methods
Epoxy resin was cast into polyvinylchloride (PVC) cylinders, 15 mm high × 22 mm external diameter × 18 mm internal diameter. After setting, an 8.5-mm dia recess, approximately 4 mm deep, was drilled centrally on one surface, and slightly undercut using an inverted cone bur in a slow-speed handpiece. Resin-modified glass-ionomer cement was mixed according to the manufacturer’s instructions, the recess overfilled with the material, covered with a plastics matrix strip and a glass microscope slide firmly pressed onto the matrix strip. The RMGIC was photocured for 20 s with a quartz halogen curing light (Elipar TriLight; ESPE, Germany) with a light intensity of >750 W/cm 2 , the microscope slide and matrix removed, the specimen checked for the presence of a uniform surface and if satisfactory the cylinder placed in water at 37 °C. Seventy-five specimens of each of Ketac N100 (also known as ‘Ketac Nano’; 3M ESPE, St Paul, MN) and Fuji II LC (GC Corporation, Tokyo, Japan) were prepared.
After 4 days, the surface of the RMGIC and embedding resin were lightly abraded with wet 600-grit silicon carbide paper until a uniform matt surface was visible, washed and blot dried. A piece of plastics adhesive tape, approximately 10 mm square with a 4.95-mm dia hole, was placed centrally over the RMGIC surface and firmly burnished down. An acrylic tube, 5.8 mm internal diameter × 4 mm high, was lubricated lightly internally with silicone oil and fixed centrally over the hole in the plastics tape using two small spots of sticky wax on its opposite sides.
The 75 specimens of each RMGIC were divided randomly into five groups if 15 specimens for ‘repair’ with either RMGIC or resin composite, as described in Table 1 (Ketac N100) and Table 2 (Fuji II LC). The respective RMGIC materials were syringed into the acrylic cylinders using either a ‘Centrix’ syringe (Ketac N100) or the manufacturer’s mixing capsule (Fuji II LC), and the resin composite packed into the ring using a plastic instrument. The ‘repair’ material was photocured for 20 s and the specimens stored in water at 37 °C.
Group 1 | Group 2 | Group 3 | Group 4 | Group 5 |
---|---|---|---|---|
Remove from water, blot dry, apply adhesive tape | ||||
Apply primer a , 15 s | Apply conditioner b , 20 s | Etch c , 20 s | Etch c , 20 s | Apply unfilled resin d , 15 s |
Air syringe dry, 10 s | Wash, 5 s | Wash, 5 s | Wash, 5 s | Air thin, 5 s |
Photocure, 10 s | Blot dry | Blot dry | Blot dry | Photocure, 20 s |
Apply primer a , 15 s | Apply primer a , 15 s | Apply unfilled resin d , 15 s | ||
Air syringe dry, 10 s | Air syringe dry, 10 s | Air thin, 5 s | ||
Photocure, 20 s | ||||
Apply plastics ring; mix and place Ketac N100; photocure 20 s; store in water at 37 °C | Apply plastics ring; place resin composite e ; photocure 40 s; store in water at 37 °C |
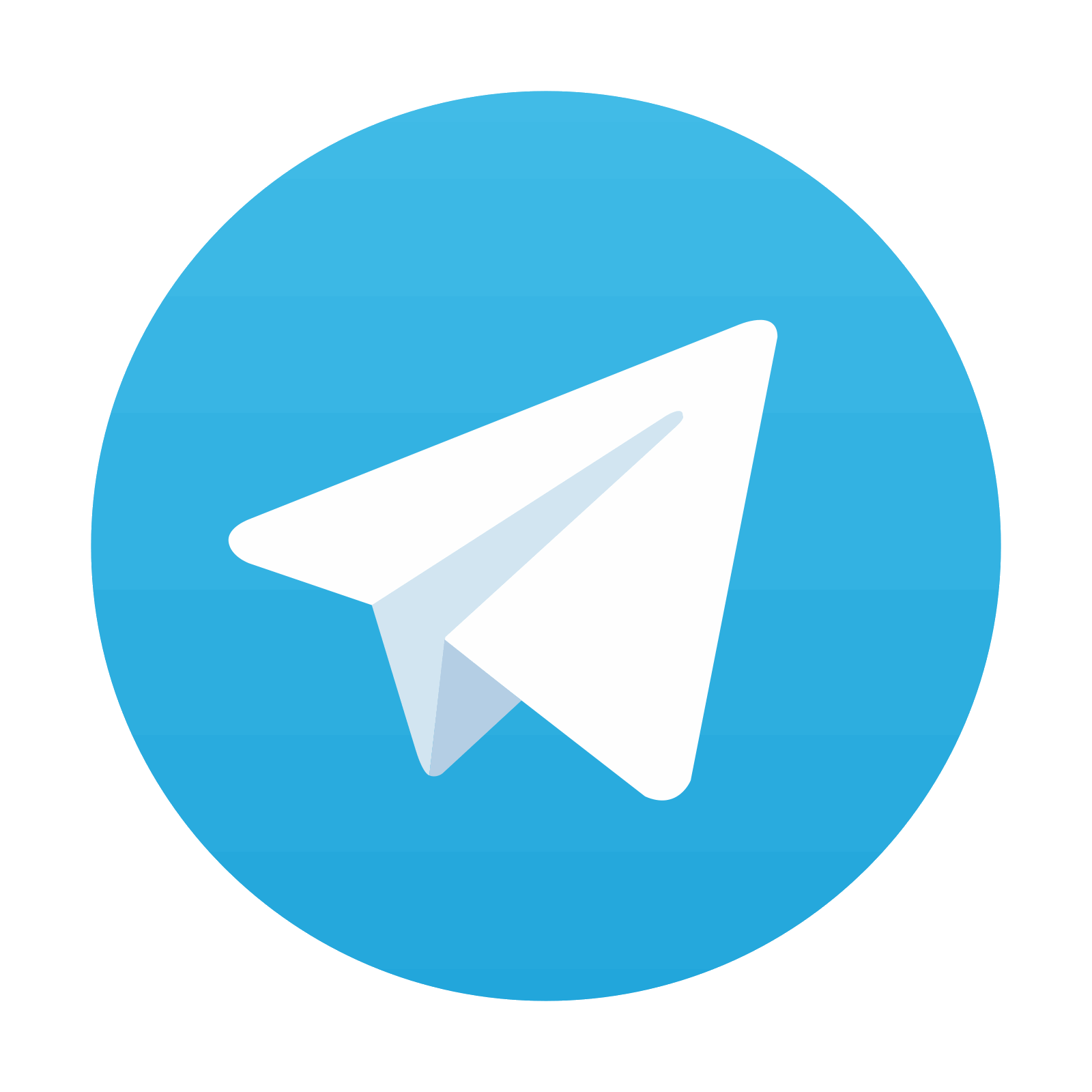
Stay updated, free dental videos. Join our Telegram channel

VIDEdental - Online dental courses
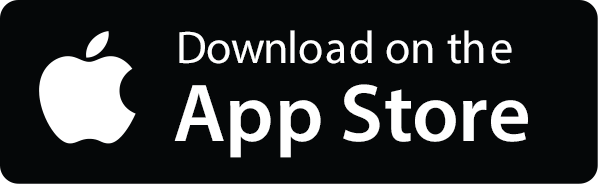

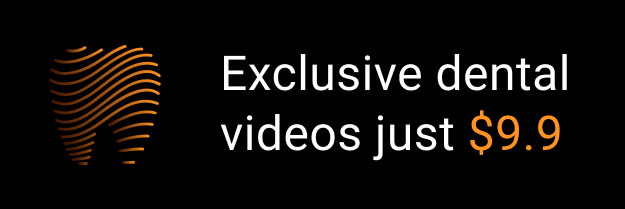