Abstract
Objectives
To describe the effect of fatigue on the strength of the bracket–adhesive–enamel complex and characterize the fatigue behavior of the materials tested.
Methods
Upper central incisor brackets (Discovery ® , Dentaurum) were bonded with a light-curing (Transbond XT™, 3M Unitek) and a chemically-curing adhesive (Concise™, 3M Unitek) on bovine teeth embedded in cylindrical resign bases and stored in water at 37(±2) °C for 24 (±2) h. The first 15 specimens were tested with a universal testing machine ZMART.PRO ® (Zwick GmbH & Co. KG, Ulm, Germany) for ultimate shear bond strength according to the DIN-13990-2-standard. The remaining three groups of 20 specimens underwent fatigue staircase testing of 100, 1000 and 3000 cycles at 1 Hz with a self-made testing machine. The survived specimens were subjected to shear strength testing.
Results
The fatigued specimens showed decreased shear strength with both adhesives at all cycle levels. The shear strength after fatigue for 100, 1000 and 3000 cycles was in the Concise™-groups 34.8%, 59.0%, 47.3% and in the Transbond™ XT-groups 33.6%, 23.1%, 27.3% relative to the ultimate shear strength. The fatigue life of the Concise™-groups decreased with increasing stress and Transbond™ XT showed lower fatigue ratio with no obvious trend. The specimens bonded with Transbond™ XT showed typically favorable fracture modes in contrary to Concise™.
Significance
Fatigue of the bracket–adhesive–enamel complex decreased its shear strength. The staircase method can provide a standardized experimental protocol for fatigue studies, however testing at various cycle numbers is recommended.
1
Introduction
Bonding attachments to teeth is a common procedure in contemporary orthodontics. A commonly encountered problem is the bond failure during treatment. The forces applied in the oral environment are usually of a cyclic nature, well below the ultimate shear strengths reported in in vitro studies . Initial powerful impacts are rare; failure is usually the result of cyclic low-force fatigue with or without sudden impact. Standard tests measure the strength at a sudden and powerful impact, although the system was not constructed to resist high loading . One approach in resolving the soundness of in vitro derived data is the fatigue of the bracket–adhesive–enamel system. This can be accomplished through exploring the total-life tolerance of the system to a low-magnitude, cyclic, mechanical stress. So far there are no standards for fatigue testing in orthodontics.
Two of the most common experimental methods in the total-life approach are the continuous and the staircase method. The staircase method assures that the fatigue testing is conducted at a load near the fatigue limit and – unlike other methods – gives a group of survived fatigued specimens, which can be used for further testing. The survived specimens are loaded with peak stress levels of sufficiently high value for fatigue crack initiation. As a result, a standardization of fatigue testing is possible .
International standardization norms for strength testing of orthodontic materials do not yet exist; however the German Institute for Standardization (DIN Deutsches Institut für Normung e.V.) published various standards to enforce the standardization of strength testing of the bracket–adhesive complex. The shear strength testing according to the DIN-13990-2-standard uses an applied load on the base of the bracket directly at the enamel surface.
Few studies have compared the bond strength of fatigued and nonfatigued specimens , only three including brackets , and the available data is not uniform. Most researchers utilizing fatigue testing compared the ultimate strength of the material with the fatigue limit and calculated the fatigue ratio . The fatigue limit may be a useful parameter to better understand fatigue behavior, but it does not give any information about the effect of fatigue on a later sudden incident.
Fatigue testing of dental materials reveals two types of behavior. In type one behavior – the classic fatigue behavior – there is a clear relationship between fatigue life and fatigue stress, i.e. the fatigue life decreases with increasing applied fatigue stress . The data can fit a power law – straight line, no apparent fatigue limit – or a hyperbolic law, implying differences between low and high cycle fatigue, as well as a fatigue limit . For type two behavior no relationship exists between fatigue life and fatigue stress. The failure occurs at a level of stress below the ultimate strength of the material, but the values of fatigue life appear to be distributed randomly when several specimens of the same material are tested. It is likely that, for these materials, resistance to fatigue is primarily dependent upon the presence or absence of flaws such as porosities. When a stress in the region of the fatigue limit is used, specimens with no flaws above a critical size are likely to survive indefinitely, while those with flaws above a critical size fail rapidly . Unlike type two behavior, for type one behavior testing should be carried out over a range of stresses and number of cycles in order to characterize the relationship between the two properties .
The aim of this study was to describe the effect of fatigue on the strength of the bracket–adhesive–enamel complex measured in accordance to the DIN-13990-2-standard and characterize the fatigue behavior of the materials tested by conducting fatigue testing at a various number of cycles. The study should also reveal, if the proposed method is suitable for future standardization of fatigue testing of orthodontic attachments bonded to enamel.
2
Materials and methods
Upper central incisor brackets with relatively flat and laser structured bases (Discovery ® , Dentaurum J.P. Winkelstroeter KG) were chosen. A light-curing adhesive (Transbond XT™, 3M Unitek) and a four-component chemically-curing adhesive (Concise™, 3M Unitek) were used to bond the brackets on bovine lower front teeth embedded in cylindrical resin bases using the bonding protocol of the manufacturers. For each material combination 75 specimens were prepared and divided randomly into one group of 15 and three groups of 20 specimens. Each specimen was stored in water at 37(±2) °C for 24 (±2) h after polymerization. The whole procedure of preparing the specimens was conform to the DIN-13990-2-standard .
The specimens were mounted into a universal testing machine ZMART.PRO ® (Zwick GmbH & Co. KG, Ulm, Germany). The first specimen group (15 specimens) of each material combination was used as a control to determine the ultimate shear bond strength without any fatigue-procedure. The movement of the head and the magnitude of the applied force was electronically controlled and monitored via the software testXpert ® II (Zwick GmbH & Co. KG, Ulm, Germany). The head was connected to a stainless spring steel plate with a square opening, which was adjusted around the bracket ( Fig. 1 ). It was held manually onto the adhesive layer between tooth and bracket in order to achieve a loading on the bracket base during shear strength testing at a speed of 1 mm/min. The whole procedure was conducted according to the DIN-13990-2-standard .
The remaining three groups (3 × 20 specimens) of each material combination underwent fatigue testing of 100, 1000 and 3000 cycles with a self-made mechanical testing machine. For the fatigue testing, a hardened stainless steel head was adjusted to apply the force as near as possible to the base of the bracket, in order to avoid a high rotational moment which would lead to a more tensile fracture mode. The head applied the fatigue load at the lateral side of each bracket; because of the design of the head and the brackets, a loading from occlusally to gingivally was not possible. The force/time curve had a saw tooth (triangular) shape with rounded corners: the stress started for all specimens at 2 N (due to limitations of the experimental design and the software, it was not possible to start at 0 N) and was increased until the maximum force value, decreased back to 2 N and so on. The tests were repeated and the maximum force value was changed according to the staircase method in each experiment. The maximum force value for the first fatigue test was near the expected fatigue limit, which was estimated at approximately 60% magnitude relative to the ultimate shear strength as determined from the first 15 specimens. The fatigue testing was carried out at a frequency of 1 Hz, which corresponds to the chewing frequency . The speed of the machine head was adjusted according to the force by the machine software. In the case of one specimen not failing within the prescribed number of stress cycles, the maximum stress for the next specimen was increased by a fixed increment of approx. 5% of the expected fatigue limit. When failure occurred, the maximum stress for the next specimen was decreased. The procedure of increasing the maximum stress following a test in which no failure occurred and decreasing the maximum stress by the same increment following a failure was continued for each succeeding specimen through all the 20 specimens of a group.
The survived fatigued specimens of each group were subjected to shear strength testing with the metal plate with the square opening adjusted to apply the force on the base of the bracket at a speed of 1 mm/min, according to the DIN-13990-2-standard , using the universal testing machine ZMART.PRO ® (Zwick GmbH & Co. KG, Ulm, Germany).
Comparisons between the strength values taken for fatigued and nonfatigued specimens were made to extrapolate the effect of fatigue on the shear bond strength. This was done in accordance to other fatigue studies and is based on the assumption that low stress cyclic fatigue will not only lead to failure during fatigue, but will also lead to a reduced strength against a later sudden incident or the debonding procedure.
The data were imported into the software Microsoft Excel 2007 (Microsoft Corporation). The mean shear fatigue limit and the standard deviation for each group was calculated according to Eqs. (1) and (2) .
X ¯ = X 0 + d A N ± 1 2
Eq. (1) . Calculation of the mean fatigue limit <SPAN role=presentation tabIndex=0 id=MathJax-Element-2-Frame class=MathJax style="POSITION: relative" data-mathml='X¯’>X¯¯¯X¯
X ¯
:
The analysis of the data is based on the least frequent event (failures or non-failures). The lowest level at which a failure or nonfailure occurs is denoted by i = 0, the next i = 1, etc. The number of events at the given level equals n i . The positive sign is used when the analysis is based on non-failures and the negative sign when failures are considered. X 0 is the lowest level on which the least frequent event occurs. d is the increment employed in the sequential tests. Further constants are defined by: <SPAN role=presentation tabIndex=0 id=MathJax-Element-3-Frame class=MathJax style="POSITION: relative" data-mathml='N=∑ni,A=∑ini,B=∑i2ni’>N=∑ni,A=∑ini,B=∑i2niN=∑ni,A=∑ini,B=∑i2ni
N = ∑ n i , A = ∑ i n i , B = ∑ i 2 n i
S = 1.62 d N B − A 2 N 2 + 0.029
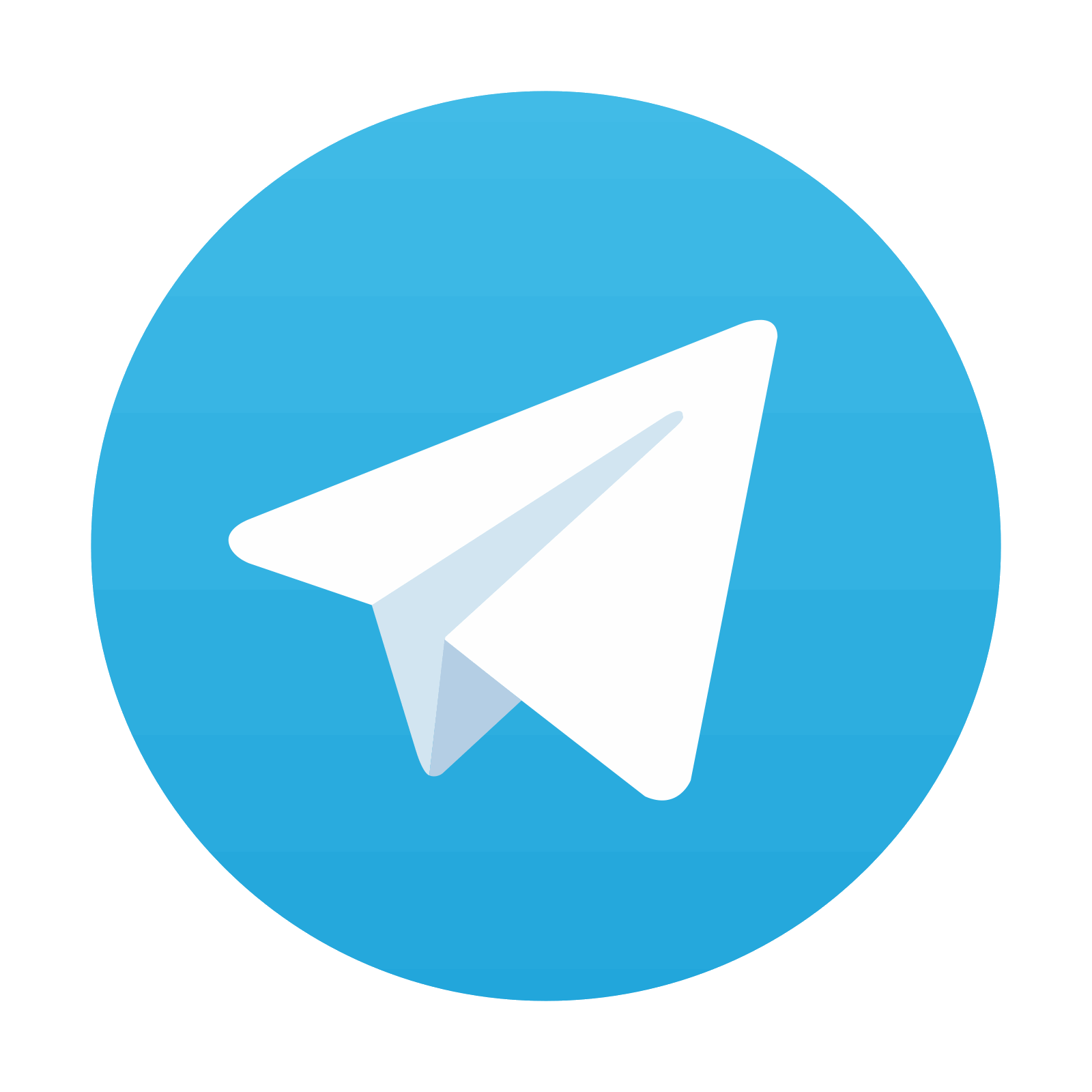
Stay updated, free dental videos. Join our Telegram channel

VIDEdental - Online dental courses
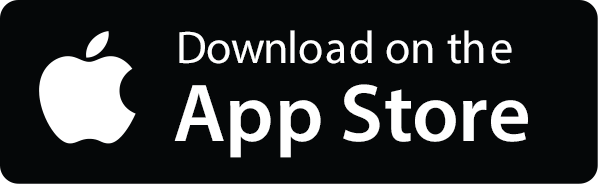
