Abstract
Objective
To use rapid scan FT-IR and Knoop microhardness to determine the effect of specimen temperature on the rate and extent of polymerization of a dental resin.
Methods
Two-millimeter thick specimens of shade A2 Tetric EvoCeram were light cured for 20 s at 22, 26, 30, and 35 °C. The IR spectrum was obtained at the bottom of the specimens at a rate of 3 measurements per second for the first 5 min, and then again 2 h later. The Knoop microhardness was measured at the bottom of the samples in the region where the IR spectrum was recorded at 5 min and 2 h after light curing. Data were statistically analyzed using mixed model ANOVA (with Fisher’s PLSD) to examine the effect of temperature, time and their interaction. The rate of conversion was determined using first differences and smoothed using a cubic spline procedure.
Results
The bottom surfaces of the samples light cured at 22, 26, 30 and 35 °C were all significantly different from each other ( p < 0.05). The higher temperature resulted in higher degree of conversion and Knoop microhardness values, and faster maximum rate of polymerization, which also occurred sooner. One second after the light was turned on, the rate of conversion was 106% faster at 35 °C than at 22 °C ( p = 0.003). Regression analysis showed a positive linear correlation between the degree of conversion and Knoop microhardness ( r 2 = 0.93).
Significance
A relatively small difference in temperature can have a large and significant effect on the rate and extent of polymerization of dental resin. Consequently laboratory studies comparing the performance of resins should be conducted at clinically relevant temperatures.
1
Introduction
Light-cured resin composites are widely used in dental restorations. These resins are polymerized by a light-curing unit (LCU) and the degree of conversion (DC) of dental resins can be determined using Fourier Transform-Infrared Spectroscopy (FT-IR) . In addition, Knoop microhardness has been shown to be a reliable method to determine how well a resin is cured and a good correlation has been reported between the Knoop microhardness and both the DC and the Young’s modulus .
The overall rate of polymerization of unfilled resins is determined by the rates of the initiation, propagation and termination phases of the reaction. The rate constant for initiation ( k i ) is independent of temperature, whereas the rate constants for both propagation ( k p ) and termination ( k t ) increase with temperature according to the Arrhenius dependence . Using typical activation energies for propagation and termination, it has been estimated that the overall polymerization rate for unfilled dimethacrylate based resins will increase by 1.90% for each 1 °C rise in temperature . However, the rate of polymerization of filled dental resins is further accelerated by the Trommsdorf effect, wherein the marked increase in the viscosity of the filled resin material during gelation decreases the mobility of large polymer radicals. This effectively reduces the termination rate constant k t at a given temperature and accelerates the reaction .
Kinetic studies of unfilled dimethacrylate resins using calorimetric techniques have shown that for a given resin composition and light intensity, increasing the temperature up to 50 or 60 °C results in greater extent of conversion as well as an increased maximum conversion rate. Daronch et al. and Trujillo et al. explored the effect of pre-heating commercial filled resin composites using infrared methods. In the 2006 study by Daronch et al. irradiation of Esthet X shade A2 with a QTH source emitting 630 mW/cm 2 showed a marked increase in extent of conversion at the top and bottom surfaces of 2-mm thick samples when temperatures of the resin were increased from 3 °C to 60 °C. Similarly Trujillo et al. observed an increase in immediate and final conversion values for three commercial resin composites using three different curing lights, when the temperatures of the resins were increased from 23 °C to 54.5 °C. Atai and Watts concluded in their study that shrinkage strain rate of a light curing resin composite increases at 45 °C compared to 23 °C . Similar conclusions were reported by Elhejazi when the temperature was raised up to 60 °C . Kitzmüller et al. also reported higher strain values at 37 °C compared to room temperature for dual-curing resin cements . These results confirmed that the basic temperature dependency observed in the earlier kinetic studies is relevant to commercial resin composites and resin cements.
The majority of dental research on resin polymerization, shrinkage and bond strengths has been conducted at room temperature, e.g., the ISO 4049 test for depth of cure stipulates that the temperature of the resin should be 23 ± 1 °C. Since resin polymerization in the mouth occurs neither at room temperature nor above 37 °C but at between 30 °C and 35 °C , it is expected that the rate and extent of resin polymerization in the tooth will be different from that occurring at room, or higher temperatures, e.g., above 37 °C. Consequently resin properties that are affected by the polymerization rate, such as bond strengths to the tooth , shrinkage, or internal stresses within the restoration , may be affected by relatively small changes in the resin temperature. This interaction may affect the conclusions of these studies because different resin based composites may react very differently when the temperature of the experiment is changed from room to typical intra-oral temperatures .
The aim of this study was to examine the photocuring of a common commercial resin (Tetric Evoceram shade A2) in the temperature range of 22–35 °C. Reflectance infrared spectroscopy (measuring DC) and Knoop microhardness were used to monitor polymerization. The temperature range was chosen to evaluate the rate and extent of resin polymerization carried out at room temperature and at representative intra-oral temperatures . A rapid infrared scan rate was used to monitor the DC at the bottom surface of the resin during the crucial initiation and gelation stages. The Knoop microhardness of the vitrified resins was correlated with the DC at 5 min and at 2 hours. Knoop microhardness was correlated with the DC of the vitrified resins at 5 min and 2 h.
The hypotheses tested were that:
- 1.
The degree of conversion, rate of polymerization and Knoop microhardness, will all be greater at representative intra-oral temperatures compared to room temperature.
- 2.
Within the range of conversion studied, there will be a positive linear correlation between the degree of conversion and Knoop microhardness measurements made at the same location.
2
Materials and methods
The same lot number of shade A2 Tetric Evoceram (Ivoclar-Vivadent Amherst, NY, USA) resin composite was used throughout the study. Samples of this resin composite were prepared in 2-mm thick aluminum rings that had a 6-mm diameter internal hole, directly on a temperature controlled Attenuated Total Reflectance (ATR) element (Golden Gate, Specac, New Brunswick, NJ, USA) attached to an infrared spectrometer (Tensor 27, Bruker, Billerica, MA, USA). The ring was filled with the resin composite and, using a flat microscope slide, a 50 μm thick Mylar Matrix Strip (Patterson Dental, St. Paul, MN, USA) was pressed down over the uncured resin to produce a flat surface. The slide was removed and resin composite and the ring were left on the heated ATR plate in the dark for 5 min to allow the temperature of the resin composite on the ATR plate to stabilize at 22, 26, 30, or 35 °C. The 5 min time interval was based on a pilot study where the temperature at the top and bottom of the resin composite was measured using a fast response tissue implantable T-type thermocouple (IT-23, Physitemp Instruments, Clifton, NJ, USA) and found to be the same as the heated ATR element after 5 min. The resin composite was then light cured at a distance of 0-mm from the end of the light guide for 20 s using a SmartLite IQ 2 curing light (Dentsply, York, PA, USA). The light output from this unit was recorded using a laboratory grade spectroradiometer (USB 4000, Ocean Optics, Dunedin, FL, USA) connected to an integrating sphere (FOIS-1, Ocean Optics) and analyzed using SpectraSuite software version 5.1 (Ocean Optics). This system was calibrated using a National Institute of Standards and Technology (NIST, Gaithersburg, MD, USA) referenced light source (Ocean Optics, LS-1-Cal-Int). The light output was checked three times throughout the experiment and the mean ± standard deviation (SD) irradiance values were 750 ± 8 mW/cm 2 . Thus all samples received 15 J/cm 2 .
Rapid scan Attenuated Total Reflectance Fourier Transform-Infrared Spectroscopy (ATR FT-IR) was used to determine the DC at the bottom of the resin composite as it polymerized. For three resin specimens made at each temperature (22, 26, 30, and 35 °C), the spectral window of 1200–1680 cm −1 was sampled at intervals of 0.33 s for 5 min. For each spectrum at a given time, the DC was calculated from the ratio of the integrated areas of the peaks at 1608 cm −1 (aromatic C C) and 1638 cm −1 (aliphatic C C) . Five minutes after light curing the resin, the specimens were removed from the ATR plate, the Mylar strip was removed from the top surface and immediately nine Knoop microhardness readings were made in close proximity to the location of DC recording ( Fig. 1 ). The 6 mm diameter hole in the metal ring allowed at least a 1-mm buffer of resin composite between any hardness measurement and the metal ring. This 1-mm buffer minimized any effect the mold may have had on resin polymerization . Three additional specimens were made at each temperature, and these specimens were left on the ATR plate for 2 h before making the DC and then the microhardness measurements. The microhardness measurements were made using a Knoop indenter that applied a 50-g load for 10 s (HM-123 Mitutoyo Canada Inc., Mississauga, ON, Canada). This hardness tester was pre-programmed to measure nine Knoop microhardness values across a 3 × 3-mm matrix pattern with a 1.5 mm pitch in the same area where the DC had been recorded ( Fig. 1 ). A total of 27 Knoop microhardness measurements were made at each temperature and at each time interval. The Knoop microhardness at the bottom of the resin specimens, as well as the polymerization rates and final DC recorded at the bottom of the specimens were compared at curing temperatures of at 22, 26, 30, and 35 °C. A total of 24 samples were made (4 temperatures × 3 repetitions × 2 time intervals) in a random order of temperatures. Analyses of variance (ANOVA) followed by Fisher’s PLSD post hoc multiple comparison analyses were carried out for DC and hardness to study the effect of temperature at a preset alpha of 0.05. A mixed model ANOVA was carried out to examine the effect of temperature, time and their interaction. The rate of conversion was determined using first differences and smoothed using a cubic spline procedure .
2
Materials and methods
The same lot number of shade A2 Tetric Evoceram (Ivoclar-Vivadent Amherst, NY, USA) resin composite was used throughout the study. Samples of this resin composite were prepared in 2-mm thick aluminum rings that had a 6-mm diameter internal hole, directly on a temperature controlled Attenuated Total Reflectance (ATR) element (Golden Gate, Specac, New Brunswick, NJ, USA) attached to an infrared spectrometer (Tensor 27, Bruker, Billerica, MA, USA). The ring was filled with the resin composite and, using a flat microscope slide, a 50 μm thick Mylar Matrix Strip (Patterson Dental, St. Paul, MN, USA) was pressed down over the uncured resin to produce a flat surface. The slide was removed and resin composite and the ring were left on the heated ATR plate in the dark for 5 min to allow the temperature of the resin composite on the ATR plate to stabilize at 22, 26, 30, or 35 °C. The 5 min time interval was based on a pilot study where the temperature at the top and bottom of the resin composite was measured using a fast response tissue implantable T-type thermocouple (IT-23, Physitemp Instruments, Clifton, NJ, USA) and found to be the same as the heated ATR element after 5 min. The resin composite was then light cured at a distance of 0-mm from the end of the light guide for 20 s using a SmartLite IQ 2 curing light (Dentsply, York, PA, USA). The light output from this unit was recorded using a laboratory grade spectroradiometer (USB 4000, Ocean Optics, Dunedin, FL, USA) connected to an integrating sphere (FOIS-1, Ocean Optics) and analyzed using SpectraSuite software version 5.1 (Ocean Optics). This system was calibrated using a National Institute of Standards and Technology (NIST, Gaithersburg, MD, USA) referenced light source (Ocean Optics, LS-1-Cal-Int). The light output was checked three times throughout the experiment and the mean ± standard deviation (SD) irradiance values were 750 ± 8 mW/cm 2 . Thus all samples received 15 J/cm 2 .
Rapid scan Attenuated Total Reflectance Fourier Transform-Infrared Spectroscopy (ATR FT-IR) was used to determine the DC at the bottom of the resin composite as it polymerized. For three resin specimens made at each temperature (22, 26, 30, and 35 °C), the spectral window of 1200–1680 cm −1 was sampled at intervals of 0.33 s for 5 min. For each spectrum at a given time, the DC was calculated from the ratio of the integrated areas of the peaks at 1608 cm −1 (aromatic C C) and 1638 cm −1 (aliphatic C C) . Five minutes after light curing the resin, the specimens were removed from the ATR plate, the Mylar strip was removed from the top surface and immediately nine Knoop microhardness readings were made in close proximity to the location of DC recording ( Fig. 1 ). The 6 mm diameter hole in the metal ring allowed at least a 1-mm buffer of resin composite between any hardness measurement and the metal ring. This 1-mm buffer minimized any effect the mold may have had on resin polymerization . Three additional specimens were made at each temperature, and these specimens were left on the ATR plate for 2 h before making the DC and then the microhardness measurements. The microhardness measurements were made using a Knoop indenter that applied a 50-g load for 10 s (HM-123 Mitutoyo Canada Inc., Mississauga, ON, Canada). This hardness tester was pre-programmed to measure nine Knoop microhardness values across a 3 × 3-mm matrix pattern with a 1.5 mm pitch in the same area where the DC had been recorded ( Fig. 1 ). A total of 27 Knoop microhardness measurements were made at each temperature and at each time interval. The Knoop microhardness at the bottom of the resin specimens, as well as the polymerization rates and final DC recorded at the bottom of the specimens were compared at curing temperatures of at 22, 26, 30, and 35 °C. A total of 24 samples were made (4 temperatures × 3 repetitions × 2 time intervals) in a random order of temperatures. Analyses of variance (ANOVA) followed by Fisher’s PLSD post hoc multiple comparison analyses were carried out for DC and hardness to study the effect of temperature at a preset alpha of 0.05. A mixed model ANOVA was carried out to examine the effect of temperature, time and their interaction. The rate of conversion was determined using first differences and smoothed using a cubic spline procedure .
3
Results
At 5 min and at 2 h, the bottom surfaces of the samples that had been light cured at 22, 26, 30 or 35 °C were all significantly different from each other ( p < 0.05). The higher temperature resulted in higher degree of conversion and Knoop microhardness values, and a faster maximum rate of polymerization, which also occurred sooner. Analysis of the results from the three repeats showed that a small round-to-round variability was present, but this was explicitly accounted for in the statistical models used. Table 1 reports the one-way ANOVA showing the highly significant effect of temperature on the DC at 5 min. Fig. 2 shows that after 2 h there was a meaningful and significant increase in DC at 35 °C; the mean ± SD for the resins light cured at 22 °C was 58.3 ± 1.0% and for the resins cured at 35 °C the DC was 64.5 ± 0.6%.
DC @ 5 min | DF | Sum of squares | Mean square | F -value | p -Value | λ | Power |
---|---|---|---|---|---|---|---|
Temperature | 3 | 183.311 | 61.104 | 95.148 | <.0001 | 285.445 | 1.000 |
Residual | 8 | 5.138 | 0.642 |
The Knoop microhardness at the bottom increased as the temperature of the resin increased from 22 °C to 35 °C. Table 2 shows that at 2 h after light curing, the Knoop microhardness values at the bottom of the specimens were significantly greater when the initial temperature of the resin was increased. Fig. 3 illustrates the effect of temperature on Knoop microhardness. Two hours after light curing there was a meaningful and significant increase in mean ± SD Knoop microhardness at the bottom from 30.9 ± 1.4 to 43.8 ± 0.4 KHN 50gf as the temperature of the resin was increased from 22 °C to 35 °C.
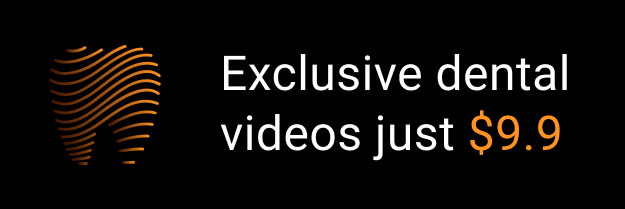