Abstract
Objectives
To verify the effects of alternating thermal changes in aqueous media and chemical composition on mechanical properties of apatite–mullite glass–ceramics and to investigate concentration of ions eluted from glass–ceramics in aqueous media.
Materials and methods
The glass compositions were from SiO 2 Al 2 O 3 P 2 O 5 CaO TiO 2 BaO ZrO 2 CaF 2 system. Glass–ceramics were prepared by heat-treating at 1100 °C for 3 h samples alternately immersed in water at 5 and 60 °C. The 3-point bending strength ( n = 10) were determined using 3 × 4 × 25 mm/bar and a universal testing machine, at a cross-head speed of 0.1 mm/min. Vickers micro hardness were evaluated by applying a total of 15–20 indentations under a 100 g load for 30 s. Concentrations of ions eluted from glass–ceramics immersed in 60 ± 5 °C double distilled water were determined by ion chromatography. The toxicity of glass–ceramics was assessed by seeding the osteosarcoma cells (MG63) on powder for different days and their cell proliferation assessment was investigated by MTT assay. The data were analyzed using one way analysis of variance and the means were compared by Tukey’s test (5% significance level).
Results
The highest flexural strength and hardness values after thermal changes belonged to TiO 2 and ZrO 2 containing glass–ceramics which contained lower amount of released ions. BaO containing glass–ceramic and sample with extra amount of silica showed the highest amount of reduction in their mechanical strength values. These additives enhanced the concentration of eluted ions in aqueous media. MTT results showed that glass–ceramics were almost equivalent concerning their in-vitro biological behavior.
Significance
Thermal changes and chemical compositions had significant effects on flexural strength and Vickers micro-hardness values.
1
Introduction
The growing trend for dental restorative materials has pushed on to the development of novel glass–ceramic systems . Glass–ceramics are composed of one or more crystalline phases which are surrounded by a glassy matrix. Heat-treatment process of the base glass which contains controlled crystallization and growth steps is one of the conventional methods in preparation and manufacturing of glass–ceramics . These materials have advantages over other bioceramics since their mechanical and biological properties are easily adjustable by using different amount of additives . The anti-bacterial effect of F − ions and the presence of needle-like fluorapatite crystals in natural bone and teeth make fluorapatite containing glass–ceramics promising candidates for medical and dental applications . Glass–ceramics based on interlocking microstructures of apatite and mullite crystals have previously been developed for dental restorations . These glass–ceramics contain dispersed fluorapatite (Ca 10 (PO 4 ) 6 F 2 ) and mullite crystals (3Al 2 O 3 ·2SiO 2 ) in a glassy matrix . Small crystals of fluorapatite, in these materials, result in biocompatibility and very special optical properties such as translucency and opalescence whilst mullite crystals induce adequate mechanical properties . Microstructure and chemical characteristic of glass–ceramic materials, chemical nature and temperature of the surrounding environment and duration of exposure to this environment are some factors which can manipulate the mechanical performance and chemical durability of dental glass–ceramics . Rapid and cyclic thermal changes in the oral cavity, which can exert considerable thermal stresses on the restorations solely or in the presence of the applied load of chewing process, are some of the other crucial issues which have unfavorable effects on mechanical properties of these materials . These thermal stresses can be simulated by thermo-cycling process which is based on alternating temperature changes in aqueous media . In a separate study, we focused on the performance of minor glass ingredients such as TiO 2 , ZrO 2 , BaO and additional amount of silica in points of crystallization behavior, microstructure and mechanical properties of an apatite–mullite based glass–ceramic system . Our results showed that small amounts of the above mentioned additives changed the microstructure and mechanical properties of the base glass–ceramic system in different ways . Despite the numerous studies about the effect of aqueous and acidic media on mechanical properties of silicate glasses, to our knowledge few studies have investigated the effect of alternative thermal changes on flexural strength and hardness variations in dental glass–ceramics . Such information is of practical importance to manufacture and application of apatite–mullite glass–ceramics in dentistry and other biomedical applications and can lead to better prediction of the future clinical behaviors of these materials . Therefore, the objective of this study is to verify the effect of thermo-cycling process duration on the strength and microhardness properties of the apatite–mullite glass–ceramics, concerning their different microstructures and chemical compositions.
2
Materials and methods
2.1
Specimen preparation
The raw materials used to produce the glass–ceramic samples are shown in Table 1 . 5 groups of glass–ceramics coded as G, GS, GZ, GB and GT with the batch formulations shown in Table 2 were prepared according to the procedure completely described in . Briefly, thoroughly mixed batches were melted at 1550 °C for 2 h. The resulted molten glasses were cast into a pre-heated steel mold and were cooled naturally to room temperature. Flexural strength and micro-hardness samples were prepared by cutting rectangular bars from as-mentioned glass blocks. All samples were annealed at 500 °C for 4 h. Based on the previously reported DTA and XRD results , obtained glass samples were first heat treated to 650 °C at a heating rate of 5 °C/min for 3 h, and then to 1100 °C at a heating rate of 10 °C/min for another 3 h and finally furnace cooled to room temperature. Microhardness samples were continually ground 5–10 min with abrasive grade SiC papers ranging from 60 grit to 1500 grit sizes and finally polished 5 min with 0.2 μm diamond paste until all scratches were removed. Specimens were washed in an ultrasonic bath after each step of grinding.
Sample code | G | GS | GZ | GB | GT |
---|---|---|---|---|---|
SiO 2 | 21.03 | 31.27 | 20.49 | 20.49 | 20.49 |
Al 2 O 3 | 35.06 | 30.51 | 34.15 | 34.15 | 34.15 |
CaO | 8.60 | 7.47 | 8.36 | 8.36 | 8.36 |
CaF 2 | 18.93 | 16.47 | 18.44 | 18.44 | 18.44 |
P 2 O 5 | 16.38 | 14.26 | 15.96 | 15.96 | 15.96 |
TiO 2 | – | – | – | – | 2.56 |
BaO | – | – | – | 2.56 | – |
ZrO 2 | – | – | 2.56 | – | – |
Raw material | SiO 2 | Al(OH) 3 | CaF 2 | Ca(CO) 3 | P 2 O 5 | TiO 2 | Ba(CO) 3 | ZrO 2 |
---|---|---|---|---|---|---|---|---|
Code | – | 239186 | 378801 | 481807 | 79609 | 14021 | 237108 | 204994 |
Company | Industrial SiO 2 (purified) | Sigma-Aldrich | Sigma-Aldrich | Sigma-Aldrich | Sigma-Aldrich | Sigma-Aldrich | Sigma-Aldrich | Sigma-Aldrich |
2.2
Thermocycling
Before testing, the prepared specimens for flexural strength and hardness analysis were alternately immersed in double distilled de-ionized water at 5 ± 5 °C for 20 s, ambient temperature for 20 s and finally double distilled de-ionized water at 60 ± 5 °C for 20 s. Flexural strength and microhardness values of each composition were assessed after specified number of cycles (dry state or 0 cycle, 3500, 7500, 18,000 and 24,000 cycles).
2.3
Flexural strength and micro-hardness assessments
The 3-point bending strength of specimens were determined using rectangular bars (3 × 4 × 25 mm) and a universal testing machine (SANTAM-20, Iran-Tehran), at a cross-head speed of 0.1 mm/min. Flexural strength values for glass–ceramics samples were calculated using the following relationship :
FS = 3 P L 2 W D 2
where FS is flexural strength (MPa); P is failure load (N); L is specimen length (mm); W is specimen width (mm) and D is specimen height (mm). In order to evaluate the Vickers surface microhardness of glass and glass–ceramic samples total of 15–20 indentations were made under a 100 g load applied for 30 s on the top surface of each specimen. The reported hardness values were an average of these readings.
2.4
Ion elution and MTT assey
In order to investigate the effect of 60 °C water exposure on leaching of some ions in glass–ceramic samples which may imply their chemical resistance, concentrations of PO 4 3− , Ca 2+ and F − ions eluted from glass–ceramic samples were determined by inductively coupled plasma optical emission spectroscopy (ICP-OES) (ES 700-VarianBV, Australia2007) after 1, 2 and 4 weeks of immersion in 60 ± 5 °C double distilled de-ionized water. Briefly, for this purpose, calibration was performed using titrisol (MERC) stock standard solutions. After immersion in 60 °C water (for 1, 2 and 4 weeks), glass–ceramic samples were pulverized and sieved to have a uniform particle size of about 200 μm in all samples. To measure the amounts of ions eluted from the glass–ceramic samples, 10 mg of each sample powder was dispersed in about 25 ml of the buffer solution and soaked for 1 week. The measurement was repeated about seven times for each ion, to ensure the reproducibility of the results.
The toxicity of glass–ceramic samples was assessed by seeding the osteosarcoma cells (MG63) on powder extracts for 7, 14 and 28 days. The proliferation and differentiation rates of the osteoblast-like cells were evaluated using extracted powders prepared according to ISO 1993-5 procedure . 0.1 g of powder samples with different compositions were incubated in 1 ml of culture medium. At the end of 7, 14 and 28 days, the mediums were collected for use in different cellular assays. Pure culture medium kept under similar conditions was used as a negative control sample. The proliferation rate of the osteoblast-like cells next to different powder extracts was determined by conducting the 3-[4,5-dimethylthiazol-2-yl]-2,5-diphenyltetrazolium bromide (MTT) assay. This test is based on the fact that active cells convert the yellowish MTT to an insoluble purple formazan crystal properties . The data (flexural values, microhardness, ions concentration and cell proliferation) were analyzed using one way analysis of variance (ANOVA) and the means were compared by Tukey’s test (5% significance level, p > 0.05 is for no significant difference and p < 0.05 is for significant difference).
2
Materials and methods
2.1
Specimen preparation
The raw materials used to produce the glass–ceramic samples are shown in Table 1 . 5 groups of glass–ceramics coded as G, GS, GZ, GB and GT with the batch formulations shown in Table 2 were prepared according to the procedure completely described in . Briefly, thoroughly mixed batches were melted at 1550 °C for 2 h. The resulted molten glasses were cast into a pre-heated steel mold and were cooled naturally to room temperature. Flexural strength and micro-hardness samples were prepared by cutting rectangular bars from as-mentioned glass blocks. All samples were annealed at 500 °C for 4 h. Based on the previously reported DTA and XRD results , obtained glass samples were first heat treated to 650 °C at a heating rate of 5 °C/min for 3 h, and then to 1100 °C at a heating rate of 10 °C/min for another 3 h and finally furnace cooled to room temperature. Microhardness samples were continually ground 5–10 min with abrasive grade SiC papers ranging from 60 grit to 1500 grit sizes and finally polished 5 min with 0.2 μm diamond paste until all scratches were removed. Specimens were washed in an ultrasonic bath after each step of grinding.
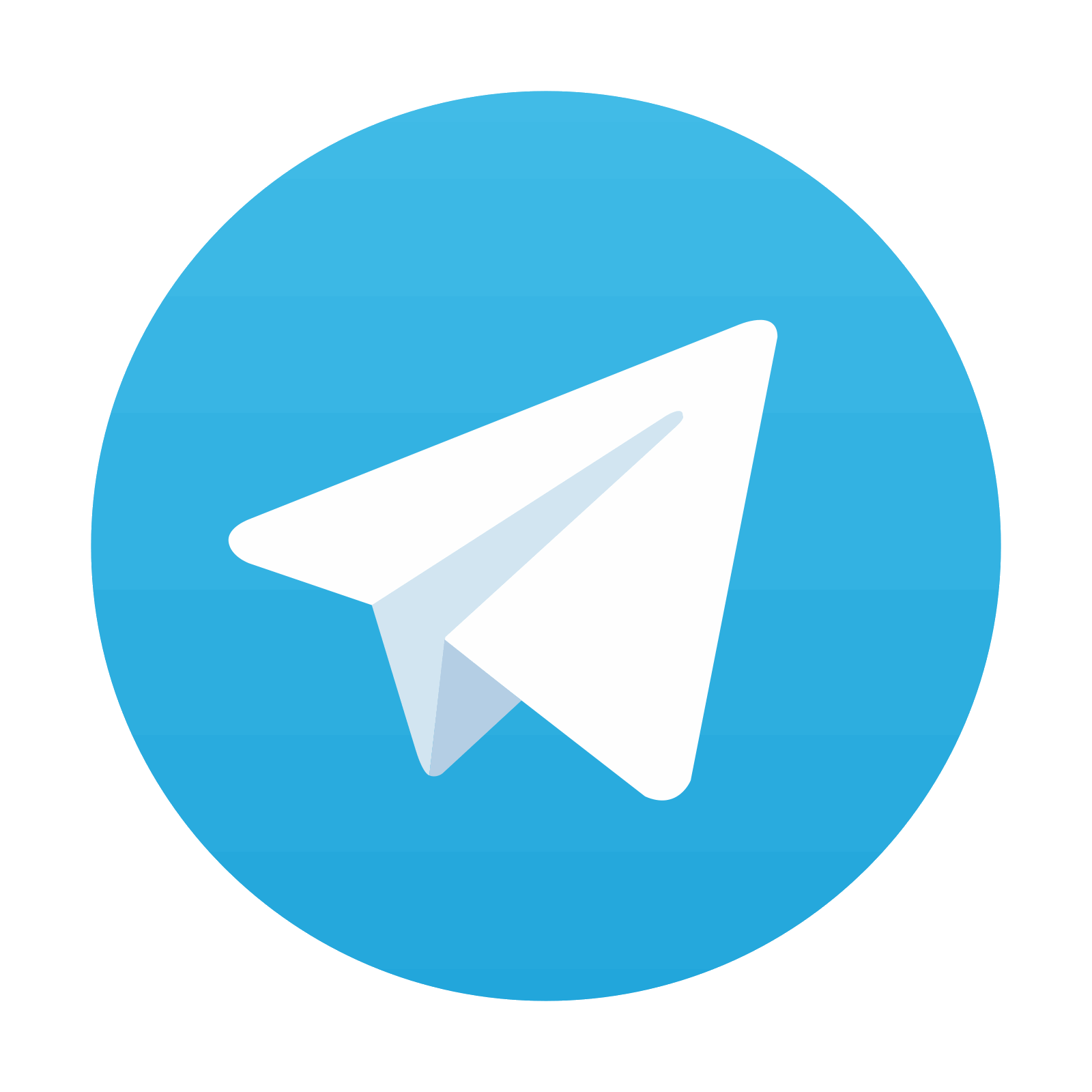
Stay updated, free dental videos. Join our Telegram channel

VIDEdental - Online dental courses
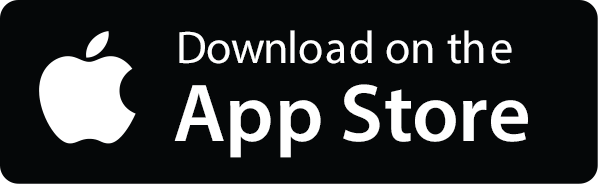

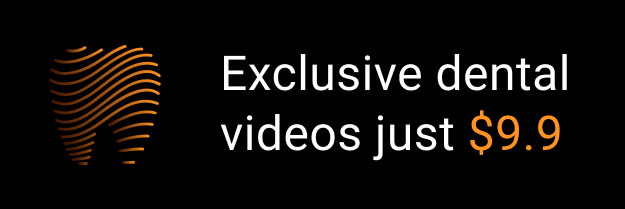