Abstract
Objectives
To assess the dimensional stability of 8 impression materials over 12 weeks relevant to in vitro tribology studies.
Methods
Ten impressions from eight impression materials were taken of a metal block (ADA block) conforming to the American Dental Association specification for impression materials and of another metal block (custom block) which allowed measurements over a larger surface area. The impressions and blocks were scanned on a non-contacting laser profilometer (Taicaan ® – Southampton, UK) and using surface metrology software Boddies ® (Taicaan ® – Southampton, UK) measurements were made at 24 h, 2, 4, 8 and 12 weeks. The impression materials tested were Aquasil ® , Aquasil ® DECA, Affinis ® , Express ® , Extrude ® , Impregum ® , President ® and Take 1 ® .
Results
Seven addition silicones and one polyether were tested. and were monophasic, the rest were putty-wash. The results from impressions of the ADA block showed that all materials contracted compared to measurements obtained directly from the block expanded over time (+31.5 μm) ( p < 0.05). The results from the custom block showed that all materials contracted compared to direct measurements of the block. and expanded over time (+62 μm and +63.8 μm respectively). contracted over time (−54.7 μm) ( p < 0.05).
Significance
No material showed linear changes >1.5% and were stable for 12 weeks. Nevertheless, the range of changes would affect tribology studies were cut-offs lesser than the reported changes are selected. All impressions should be processed after similar time delays to reduce the errors introduced by dimensional changes.
1
Introduction
Impression materials can be used to record topographical changes on teeth subjected to wear episodes in vivo and in vitro . The replicas can be scanned on profilometers and using surface metrology software, tooth wear can be measured as either step height of volumetric loss from unchanged reference areas. Reproducing the surfaces using impression materials rather than directly scanning them overcomes the problem of scanning materials of different colour and reflectivity which can introduce a source of error when scanning samples of different opacity . When used clinically, these impressions are normally cast within a few days; however, for many laboratory investigations there is less urgency to cast or digitise the impressions so there can be delays between impression taking and scanning. Also, in most in vitro studies measuring tooth wear, samples are subjected to several cycles of wear and the completion of these cycles may take from a few days to a few months, hence there may be a delay between impression taking and processing.
The dimensional stability of impression materials has been studied widely in the literature . Most studies follow protocols described by the American Dental Association (ADA) which replicates a clinical scenario . These guidelines advise using a cylindrical metal block allowing measurements over two horizontal coordinates in an area of less than five millimetres in length. Some researchers have recognized that this standard may not be sufficient to account for changes over the three coordinates or over larger surface areas.
Surprisingly little is known about the long term stability of impression materials and how this may affect in vitro tooth wear studies where measurements are reliant on accurate and stable reproductions of the tissues being studied. The aim of this study was to assess the dimensional stability of eight commonly used impression materials over a period of 12 weeks (84 days) using two blocks; the one specified on the ADA specification no. 19 for elastomeric impression materials and another custom block. The null hypothesis was that the materials showed linear dimensional changes <1.5% for the duration for the study.
2
Materials and methods
Seven addition cured silicone and one polyether impression materials ( Table 1 ) were assessed for dimensional changes over 12 weeks using two blocks. One block conformed to the ADA specification no. 19 for elastomeric impression materials (ADA block – Fig. 1 ) and the other (custom block – Fig. 2 ) allowed measurements to be taken in the ‘ X ’ and ‘ Y ’ axes. The ADA block was a 30 mm diameter metal cylinder with three parallel grooves of 20, 50 and 75 μm deep repectively; the maximum distance between the outermost grooves was five millimeters. The custom block was a 50 mm by 50 mm square with multiple features which allowed measurements to be obtained over more than one coordinate.
Trade name | Manufacturer | Type | Consistency | Lot/Expiry date |
---|---|---|---|---|
Affinis ® | Coltene/Whaledent | Poly-vinyl siloxane | Heavy Light |
0096188/July 2008 0090562/May 2008 |
Aquasil ® | Dentsply Caulk | Poly-vinyl siloxane | Putty Light |
0607000513/Dec 2008 060303/Mar 2009 |
Aquasil DECA ® | Dentsply Caulk | Poly-vinyl siloxane | Medium | 060406/Apr 2008 |
Express ® | 3M ESPE | Poly-vinyl siloxane | Putty Light |
6JM21/Oct 2008 5HLF2HR/Aug 2008 |
Extrude ® | Kerr Hawe | Poly-vinyl siloxane | Putty Light |
549546/May 2008 6-1137/May 2009 |
Impregum ® | 3M ESPE | Polyether | Medium | 262218/Feb 2009 |
President ® | Coltene/Whaledent | Poly-vinyl siloxane | Putty Light |
0109448/Jan 2009 0095975/Jul 2008 |
Take 1 ® | Kerr Hawe | Poly-vinyl siloxane | Heavy Light |
6-1230/Aug 2009 6-1094/Apr 2009 |
Ten impressions of each block were taken with each impression material following their manufacturer’s instructions. Impregum ® and Aquasil DECA ® were mixed on a Pentamix ® machine. The putty materials were weighed (5 g of base and catalyst each) on a set of laboratory scales (Mettler-Toledo AT250 – accuracy 1 mg, repeatability 3 mg) and were hand mixed until no streaks were visible to the naked eye. The rest of the materials were mixed using a gun-cartridge system and dispensed after thorough purging. Putty-wash impressions were taken with all materials except Impregum ® and Aquasil DECA ® , which were monophasic. To ensure an even thickness of the impressions a glass slab and a weight of one kilogram were positioned on top of either the block. All materials were used at least six months before their expiry date. The impressions were left to set undisturbed for 10 min and after removal checked under an optical microscope (EMZ TR, Meiji, Japan) for the accuracy of the impression. The impressions were carefully trimmed, labelled and their orientation axes marked.
The impressions were stored for 24 h and then scanned on a non-contacting laser profilometer (Xyris 2000TL, Taicaan ® Technologies, Southampton, UK). The scanner had an axis and sensor resolution of 0.1 μm and a 785 nm laser sensor with a spot size diameter of 30 μm. Accuracy was 0.1 μm and repeatability 0.3 μm. The impressions were scanned using a step-over distance of 50 μm. They were then re-scanned at two weeks, four weeks, eight weeks and 12 weeks using the same techniques. All testing and storage was performed in a dry environment (20 ± 1 °C). Data analysis was performed with Boddies v1.81 surface metrology software (Taicaan ® Technologies, Southampton, UK). For the ADA block, two measurements were obtained on the ‘ X ’ axis. For the custom block two measurements were obtained on the ‘ X ’ axis, two on the ‘ Y ’ and two cross sectional (from one corner of the block to the opposite corner).
Finally, the two blocks (ADA and custom) were scanned directly on the non-contacting laser profilometer using the same settings as described above; this allowed comparison of measurements obtained directly from the block to measurements obtained from the impressions. One-way analysis of variance (ANOVA) and post ANOVA Scheffe tests were used to assess differences in measurements obtained from different impression materials over time. Statistical significance was inferred where p < 0.05.
2
Materials and methods
Seven addition cured silicone and one polyether impression materials ( Table 1 ) were assessed for dimensional changes over 12 weeks using two blocks. One block conformed to the ADA specification no. 19 for elastomeric impression materials (ADA block – Fig. 1 ) and the other (custom block – Fig. 2 ) allowed measurements to be taken in the ‘ X ’ and ‘ Y ’ axes. The ADA block was a 30 mm diameter metal cylinder with three parallel grooves of 20, 50 and 75 μm deep repectively; the maximum distance between the outermost grooves was five millimeters. The custom block was a 50 mm by 50 mm square with multiple features which allowed measurements to be obtained over more than one coordinate.
Trade name | Manufacturer | Type | Consistency | Lot/Expiry date |
---|---|---|---|---|
Affinis ® | Coltene/Whaledent | Poly-vinyl siloxane | Heavy Light |
0096188/July 2008 0090562/May 2008 |
Aquasil ® | Dentsply Caulk | Poly-vinyl siloxane | Putty Light |
0607000513/Dec 2008 060303/Mar 2009 |
Aquasil DECA ® | Dentsply Caulk | Poly-vinyl siloxane | Medium | 060406/Apr 2008 |
Express ® | 3M ESPE | Poly-vinyl siloxane | Putty Light |
6JM21/Oct 2008 5HLF2HR/Aug 2008 |
Extrude ® | Kerr Hawe | Poly-vinyl siloxane | Putty Light |
549546/May 2008 6-1137/May 2009 |
Impregum ® | 3M ESPE | Polyether | Medium | 262218/Feb 2009 |
President ® | Coltene/Whaledent | Poly-vinyl siloxane | Putty Light |
0109448/Jan 2009 0095975/Jul 2008 |
Take 1 ® | Kerr Hawe | Poly-vinyl siloxane | Heavy Light |
6-1230/Aug 2009 6-1094/Apr 2009 |
Ten impressions of each block were taken with each impression material following their manufacturer’s instructions. Impregum ® and Aquasil DECA ® were mixed on a Pentamix ® machine. The putty materials were weighed (5 g of base and catalyst each) on a set of laboratory scales (Mettler-Toledo AT250 – accuracy 1 mg, repeatability 3 mg) and were hand mixed until no streaks were visible to the naked eye. The rest of the materials were mixed using a gun-cartridge system and dispensed after thorough purging. Putty-wash impressions were taken with all materials except Impregum ® and Aquasil DECA ® , which were monophasic. To ensure an even thickness of the impressions a glass slab and a weight of one kilogram were positioned on top of either the block. All materials were used at least six months before their expiry date. The impressions were left to set undisturbed for 10 min and after removal checked under an optical microscope (EMZ TR, Meiji, Japan) for the accuracy of the impression. The impressions were carefully trimmed, labelled and their orientation axes marked.
The impressions were stored for 24 h and then scanned on a non-contacting laser profilometer (Xyris 2000TL, Taicaan ® Technologies, Southampton, UK). The scanner had an axis and sensor resolution of 0.1 μm and a 785 nm laser sensor with a spot size diameter of 30 μm. Accuracy was 0.1 μm and repeatability 0.3 μm. The impressions were scanned using a step-over distance of 50 μm. They were then re-scanned at two weeks, four weeks, eight weeks and 12 weeks using the same techniques. All testing and storage was performed in a dry environment (20 ± 1 °C). Data analysis was performed with Boddies v1.81 surface metrology software (Taicaan ® Technologies, Southampton, UK). For the ADA block, two measurements were obtained on the ‘ X ’ axis. For the custom block two measurements were obtained on the ‘ X ’ axis, two on the ‘ Y ’ and two cross sectional (from one corner of the block to the opposite corner).
Finally, the two blocks (ADA and custom) were scanned directly on the non-contacting laser profilometer using the same settings as described above; this allowed comparison of measurements obtained directly from the block to measurements obtained from the impressions. One-way analysis of variance (ANOVA) and post ANOVA Scheffe tests were used to assess differences in measurements obtained from different impression materials over time. Statistical significance was inferred where p < 0.05.
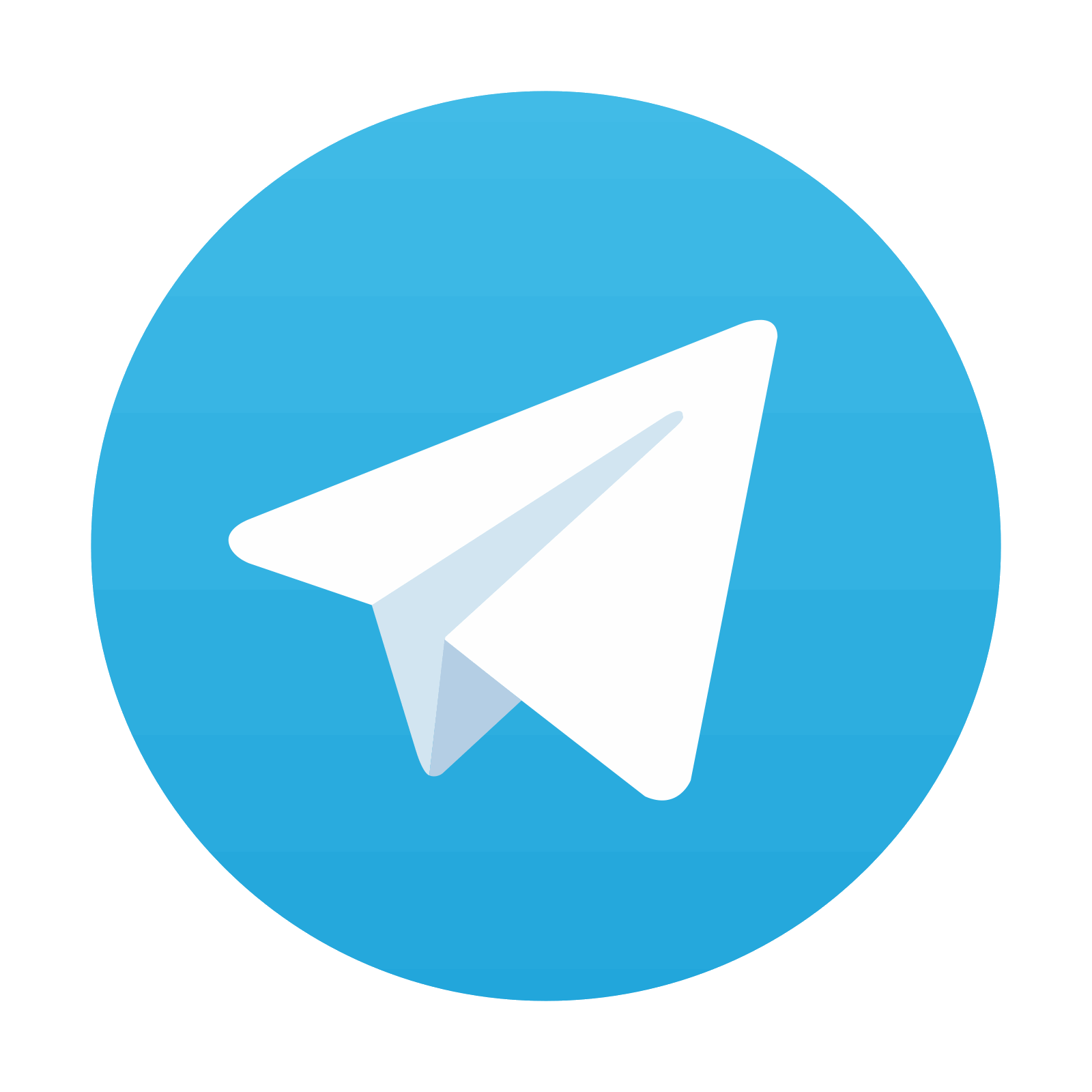
Stay updated, free dental videos. Join our Telegram channel

VIDEdental - Online dental courses
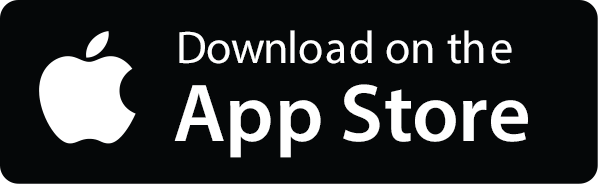
