Abstract
Objective
One of the challenges encountered with composite restorations is their inability to prevent secondary caries. Alternative fillers that initiate remineralization have been proposed but poor mechanical strength limits their use to lining and support materials. Mineral trioxide aggregate (MTA) is a material with many dental applications including root-end filling and pulp capping. MTA is capable of encouraging remineralization by leaching calcium in solution, and has the ability to form apatite in physiological solution. The aim of this study was to characterize and investigate the chemical properties of MTA-filled composite resins.
Methods
Composite resins composed of light-cured (Heliobond) and chemical-cured (Superbond) dental resins filled with MTA Plus (MTA-Light, MTA-Chem) respectively, and MTA Plus mixed with water (MTA-W), were investigated. Un-hydrated and set materials were characterized by scanning electron microscopy (SEM), energy dispersive X-ray (EDX) analysis, X-ray diffraction (XRD) analysis and Fourier transform infrared (FT-IR) spectroscopy after being stored dry or immersed in Hank’s balanced salt solution (HBSS). The chemical properties of the set materials were then investigated.
Results
XRD and FT-IR analyses revealed that MTA powder remains unhydrated within the composite, even after 28 days of immersion in HBSS. Furthermore neither resin appeared to chemically react with the MTA. EDX revealed minimal diffusion of bismuth oxide through the polymer network. Apatite formation on the material surfaces was demonstrated by SEM. Significantly less apatite deposition was exhibited on the composites compared to MTA-W. All materials leached calcium and produced an alkaline pH in physiological solution. The pH at 28 days was: MTA-W 12.7, MTA-Light 11.4, and MTA-Chem 10.8. Calcium ion concentration followed the same trend, with MTA-W > MTA-Light > MTA-Chem.
Significance
The novel composites exhibited calcium ion release, alkalinizing pH and formation of apatite, although in each case not as strongly as the control (MTA-W). MTA-Chem fared less favorably than MTA-Light in these aspects. Thus they are recommended for applications where bioactivity is desirable but not critical, and only they have a significant advantage over ordinary MTA in some other aspect.
1
Introduction
Composite resins have become a mainstay in restorative dentistry. A significant challenge that still remains with dental composite restorations is their inability to prevent formation of secondary caries . One of the modifications to improve the properties of these materials is the use of alternative fillers.
Composite resins incorporate fillers which are usually composed of silica-based glass. The incorporation of a filler is aimed at reduction in polymerization shrinkage, reduction in thermal expansion, improvement in mechanical properties, and also depending on the filler used the composite radiopacity and color and translucency can be controlled. Alternative fillers have been investigated. Calcium phosphate has been proposed as a suitable filler material as it was shown to initiate remineralization by the leaching of phosphates .
One way to incorporate a bioactive calcium-releasing filler in resin would be to use mineral trioxide aggregate (MTA) as a filler. MTA is bioactive; it leaches calcium ions in solution and is capable of forming a bone-like hydroxyapatite layer on its surface when immersed in physiological solution . This layer provides the benefits of increasing the sealing ability of MTA and promoting remineralization and regeneration of hard tissues. MTA already has numerous applications including pulp-capping, apexification, repair of root perforations, root-end filling and others . It has been reported in literature that combinations of MTA with light curing resin and chemical curing resin have shown promising results, promoting remineralization, releasing calcium ions and producing an alkaline pH in physiological solution. These materials thus warrant further investigation.
TheraCal, a light-curable pulp-capping material composed of Portland cement, resin, radiopacifier and hydrophilic thickening agent has been found to release more calcium than MTA at time periods up to the 28 days , produced an initially alkaline pH which became more neutral over time, had a cure depth of 1.7 mm and less solubility and higher water uptake than MTA. Preliminary evidence of apatite formation was also reported. This MTA/resin composite was deemed to have advantageous properties for pulp-capping .
The purpose of this study was to characterize and investigate the chemical properties of composite resins using MTA as filler material.
2
Methodology
MTA Plus (compounded by Prevest Denpro, Jammu, India for Avalon Biomed Inc., Bradenton, FL, USA) lot #2011022801 was used a filler material in a light cure and chemical cure resin systems. In this study the following composites were investigated:
- •
Light-curing resin (Heliobond, Ivoclar-Vivadent, Schaan, Liechtenstein) filled with MTA Plus – MTA-Light. The filler loading used was 1 g MTA per 0.030 g Heliobond.
- •
Chemical cure resin (Superbond C&B; Sun Medical, Shiga, Japan) filled with MTA Plus – MTA-Chem. The filler loading was used was one scoop MTA per scoop of clear L-type polymer (using the supplied scoop), to which was also added 4 drops monomer and 1 drop catalyst-V as per manufacturer’s instructions.
- •
Unfilled light curing resin (Light resin), chemical cure resin (Chem resin) and MTA Plus mixed with distilled water at a water to cement ratio of 0.35 (MTA-W) was used as a controls.
MTA-Light and Light resin were cured for 20 s using an LED curing wand (Kingfisher MD80; Mdtrad Ltd., West Yorkshire, UK). The materials were cured in 1 mm increments to allow the curing light to penetrate the deeper layers.
The testing was performed at 1 day and at 28 days unless otherwise indicated, and the materials were stored either dry or immersed in Hank’s balanced salt solution (HBSS; H6648, Sigma Aldrich, St. Louis, MO, USA).
2.1
X-ray diffraction analysis
Analysis of crystalline phases was carried out on the materials using X-ray diffraction (XRD). The diffractometer (Rigaku Ultima IV, Rigaku Corporation, Tokyo, Japan) used Cu Kα radiation at 40 mA and 45 kV. Samples were presented in powder form and the detector was rotated between 5° and 45°, with a sampling width of 0.05° and scan speed of 2°/min. Phase identification was accomplished by use of search-match software utilizing the ICDD database (International Centre for Diffraction Data, Newtown Square, PA, USA).
2.2
Fourier transform infra-red (FT-IR) spectroscopy
The materials were analyzed using a Fourier transform infrared spectrophotometer (Shimadzu IRAffinity-1; Shimadzu Corp., Kyoto, Japan) using and ATR window diameter of 7 mm, spectral resolution of 4 cm −1 and 45 scans per spectrum. Background noise was removed prior to analysis by means of background scans.
2.3
Scanning electron microscopy
Cube specimens with side 7 mm were prepared and stored for 28 days either dry or immersed in HBSS, in both cases at 37 ± 1 °C. At the end of the curing period the materials were desiccated and embedded in epoxy resin (Struers Epofix, Struers, Ballerup, Denmark). This was followed by grinding them with progressively finer grits of abrasive paper, polished with diamond paste, washed with isopropanol alcohol, dried and carbon coated (Agar auto carbon coater; Agar Scientific, Essex, England). They were then viewed under a scanning electron microscope (SEM; Zeiss MERLIN Field Emission SEM, Carl Zeiss NTS GmbH, Oberkochen, Germany) and cement microstructure was assessed in back scatter electron mode. Elemental constitution of each phase identified was carried out by energy dispersive X-ray (EDX) analysis. In addition, plots of calcium–silicon ratios of the cement particle center, the margin of the cement particle and the cement matrix were plotted. Bismuth plots of the same areas in relation to the bismuth oxide articles were also plotted.
Additionally, cement discs 15 mm in diameter and 1 mm thick were cured for 24 h as described, immersed in HBSS for 28 days, dried and finally carbon coated without polishing the surfaces. The unpolished surfaces were then observed under the scanning electron microscope.
2.4
pH and calcium ion release in physiological solution
Discs of diameter 15 ± 0.1 mm and height 2 ± 0.5 mm were cast and allowed to cure for 24 h in a dry incubator at a temperature of 37 ± 1 °C. They were then immersed in individual sealed polycarbonate containers containing 20 ± 0.01 ml of HBSS. Three replicate samples of each material were made.
Using a pH/mV/ISE meter (Hanna HI 3221, Hanna Instruments, Woonsocket, RI, USA) with a single-junction (Ag/AgCl) ceramic pH electrode (Hanna HI 1131, Hanna Instruments, Woonsocket, RI, USA) the pH of each solution was measured after 1, 7, 14, 21 and 28 days from the moment of immersion. Temperature compensation was accomplished by simultaneously immersing a temperature probe (HI 7662, Hanna Instruments, Woonsocket, RI, USA) in the measurement solution. The pH meter was calibrated using three standard calibrating solutions (pH 4.01, 7.01 and 10.00) prior to each set of measurements.
The calcium ion concentration of the solutions was measured at 1, 7, 14, 21 and 28 days using an ISE Calcium Electrode (consisting of Hanna HI 4000-50 Sensor handle and Hanna HI 4004-51 calcium module) with a separate reference electrode (Hanna HI 5315). Temperature compensation was accomplished in the same way as for the pH measurement. The meter was calibrated using two standard calibrating solutions (100 ppm and 1000 ppm) prior to each set of measurements.
2
Methodology
MTA Plus (compounded by Prevest Denpro, Jammu, India for Avalon Biomed Inc., Bradenton, FL, USA) lot #2011022801 was used a filler material in a light cure and chemical cure resin systems. In this study the following composites were investigated:
- •
Light-curing resin (Heliobond, Ivoclar-Vivadent, Schaan, Liechtenstein) filled with MTA Plus – MTA-Light. The filler loading used was 1 g MTA per 0.030 g Heliobond.
- •
Chemical cure resin (Superbond C&B; Sun Medical, Shiga, Japan) filled with MTA Plus – MTA-Chem. The filler loading was used was one scoop MTA per scoop of clear L-type polymer (using the supplied scoop), to which was also added 4 drops monomer and 1 drop catalyst-V as per manufacturer’s instructions.
- •
Unfilled light curing resin (Light resin), chemical cure resin (Chem resin) and MTA Plus mixed with distilled water at a water to cement ratio of 0.35 (MTA-W) was used as a controls.
MTA-Light and Light resin were cured for 20 s using an LED curing wand (Kingfisher MD80; Mdtrad Ltd., West Yorkshire, UK). The materials were cured in 1 mm increments to allow the curing light to penetrate the deeper layers.
The testing was performed at 1 day and at 28 days unless otherwise indicated, and the materials were stored either dry or immersed in Hank’s balanced salt solution (HBSS; H6648, Sigma Aldrich, St. Louis, MO, USA).
2.1
X-ray diffraction analysis
Analysis of crystalline phases was carried out on the materials using X-ray diffraction (XRD). The diffractometer (Rigaku Ultima IV, Rigaku Corporation, Tokyo, Japan) used Cu Kα radiation at 40 mA and 45 kV. Samples were presented in powder form and the detector was rotated between 5° and 45°, with a sampling width of 0.05° and scan speed of 2°/min. Phase identification was accomplished by use of search-match software utilizing the ICDD database (International Centre for Diffraction Data, Newtown Square, PA, USA).
2.2
Fourier transform infra-red (FT-IR) spectroscopy
The materials were analyzed using a Fourier transform infrared spectrophotometer (Shimadzu IRAffinity-1; Shimadzu Corp., Kyoto, Japan) using and ATR window diameter of 7 mm, spectral resolution of 4 cm −1 and 45 scans per spectrum. Background noise was removed prior to analysis by means of background scans.
2.3
Scanning electron microscopy
Cube specimens with side 7 mm were prepared and stored for 28 days either dry or immersed in HBSS, in both cases at 37 ± 1 °C. At the end of the curing period the materials were desiccated and embedded in epoxy resin (Struers Epofix, Struers, Ballerup, Denmark). This was followed by grinding them with progressively finer grits of abrasive paper, polished with diamond paste, washed with isopropanol alcohol, dried and carbon coated (Agar auto carbon coater; Agar Scientific, Essex, England). They were then viewed under a scanning electron microscope (SEM; Zeiss MERLIN Field Emission SEM, Carl Zeiss NTS GmbH, Oberkochen, Germany) and cement microstructure was assessed in back scatter electron mode. Elemental constitution of each phase identified was carried out by energy dispersive X-ray (EDX) analysis. In addition, plots of calcium–silicon ratios of the cement particle center, the margin of the cement particle and the cement matrix were plotted. Bismuth plots of the same areas in relation to the bismuth oxide articles were also plotted.
Additionally, cement discs 15 mm in diameter and 1 mm thick were cured for 24 h as described, immersed in HBSS for 28 days, dried and finally carbon coated without polishing the surfaces. The unpolished surfaces were then observed under the scanning electron microscope.
2.4
pH and calcium ion release in physiological solution
Discs of diameter 15 ± 0.1 mm and height 2 ± 0.5 mm were cast and allowed to cure for 24 h in a dry incubator at a temperature of 37 ± 1 °C. They were then immersed in individual sealed polycarbonate containers containing 20 ± 0.01 ml of HBSS. Three replicate samples of each material were made.
Using a pH/mV/ISE meter (Hanna HI 3221, Hanna Instruments, Woonsocket, RI, USA) with a single-junction (Ag/AgCl) ceramic pH electrode (Hanna HI 1131, Hanna Instruments, Woonsocket, RI, USA) the pH of each solution was measured after 1, 7, 14, 21 and 28 days from the moment of immersion. Temperature compensation was accomplished by simultaneously immersing a temperature probe (HI 7662, Hanna Instruments, Woonsocket, RI, USA) in the measurement solution. The pH meter was calibrated using three standard calibrating solutions (pH 4.01, 7.01 and 10.00) prior to each set of measurements.
The calcium ion concentration of the solutions was measured at 1, 7, 14, 21 and 28 days using an ISE Calcium Electrode (consisting of Hanna HI 4000-50 Sensor handle and Hanna HI 4004-51 calcium module) with a separate reference electrode (Hanna HI 5315). Temperature compensation was accomplished in the same way as for the pH measurement. The meter was calibrated using two standard calibrating solutions (100 ppm and 1000 ppm) prior to each set of measurements.
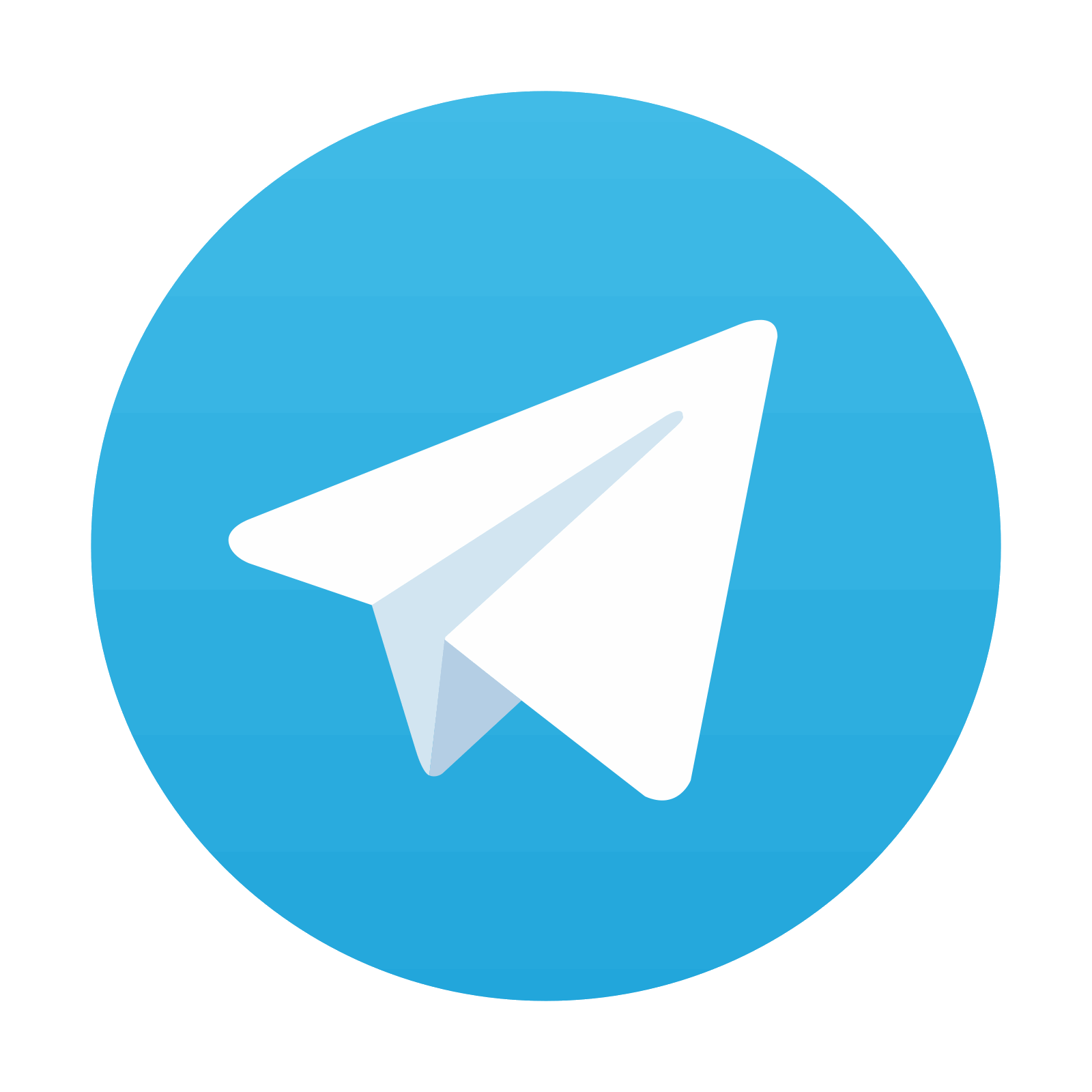
Stay updated, free dental videos. Join our Telegram channel

VIDEdental - Online dental courses
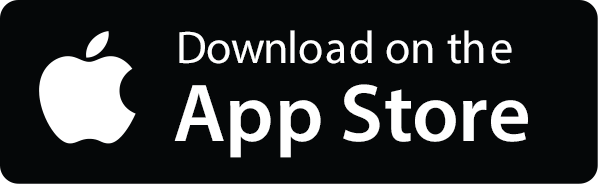
