Abstract
Objectives
To determine temperature dependence of shrinkage stress kinetics for a set of resin composites formulated with dimethacrylate monomer matrices.
Methods
Six representative resin composites with a range of resin matrices were selected. Two of them were considered as low shrinking resin composites: Kalore and Venus Diamond. The shrinkage stress kinetics at 23 °C and 37 °C were measured continuously using a Bioman instrument for 60 min. Stress levels between materials were compared at two intervals: 2 min and 60 min. Specimen temperatures were controlled by a newly designed heating device. Stress measurements were monitored for 1 h, after irradiation for 40 s at 550 mW/cm 2 (energy density = 22 J/cm 2 ). Three specimens ( n = 3) were used at each temperature per material.
Results
Shrinkage stress at 23 °C ranged from 2.93 MPa to 4.71 MPa and from 3.57 MPa to 5.42 MPa for 2 min and 60 min after photo-activation, respectively. The lowest stress-rates were recorded for Kalore and Venus Diamond (0.34 MPa s −1 ), whereas the highest was recorded for Filtek Supreme XTE (0.63 MPa s −1 ). At 37 °C, shrinkage stress ranged from 3.27 MPa to 5.35 MPa and from 3.36 MPa to 5.49 MPa for 2 min and 60 min after photo-activation, respectively. Kalore had the lowest stress-rate (0.44 MPa s −1 ), whereas Filtek Supreme XTE had the highest (0.85 MPa s −1 ). Materials exhibited a higher stress at 37 °C than 23 °C except for Kalore and Venus Diamond. Positive correlations were found between shrinkage stress and stress-rate at 23 °C and 37 °C ( r = 0.70 and 0.92, respectively).
Significance
Resin-composites polymerized at elevated temperature (37 °C) completed stress build up more rapidly than specimens held at 23 °C. Two composites exhibited atypical reduced stress magnitudes at the higher temperature.
1
Introduction
Since resin composites were developed and introduced commercially in the late 1950s to restore the appearance and function of biological tooth tissues they have been progressively re-formulated to improve their mechanical and physical properties . However, shrinkage and subsequent shrinkage stress that occur during polymerization are still disadvantages . This may lead to deleterious clinical complications, such as post-operative pain, marginal discoloration, recurrent caries, cusp deflection and enamel micro-cracks .
Shrinkage stress is the result of confining the shrinking material by bonding to cavity walls. During the early stage of the polymerization reaction, resin composites may flow and relax any developing stress. However, there is a very short period before the material becomes stiff and unable to deform readily. Then stress starts to increase . Thus, material properties, geometry, and boundary conditions are contributory factors that interact with each other to determine the resulting stress.
The degree of conversion, polymerization rate, shrinkage strain, elastic modulus, pre-gel flow, and post-gel shrinkage are among material factors that play a role in stress development . Previous studies have proposed different ways to reduce shrinkage and its accompanying stress, via incremental placement techniques, use of stress absorbing liners, soft-start light curing, and redesigning of materials . Several low shrinking resin composites have been introduced, including Kalore and Venus Diamond. Kalore is based on a novel monomer (DX-511), which is a modified UDMA and has a high molecular mass in comparison to Bis-GMA (895 g/mole vs. 512 g/mole) . Venus Diamond is based on TCD-DI-HEA monomer which is described as a low shrinkage monomer with low viscosity .
Previous studies showed the extent to which ambient temperature affects key properties of resin composites, including degree of conversion , rate of polymerization , shrinkage strain and its rate , and also the elastic and viscous moduli . Increasing temperature decreases resin composite viscosity, increases free volume and improves molecular mobility. Increasing degree of conversion is normally accompanied by increased shrinkage. Apart from effects of increasing crosslinking, higher temperature facilitates polymer chain segmental movement that is manifest in greater compliance and lower elastic modulus . Many studies have taken place that explores the polymerization stress phenomenon. However, the majority were conducted at ambient room temperature.
The objective of this study was to investigate the effect of increasing specimen temperature from room temperature (23 °C) to body temperature (37 °C) on shrinkage stress kinetics for a representative range of resin composites.
The null hypotheses were (1) temperature has no effect on shrinkage stress, (2) there is no difference in shrinkage stress at 2 min and 60 min, and (3) there is no relation between shrinkage stress and stress rate.
2
Materials and methods
Six commercial photo-activated resin-composites were selected on the basis of their matrix monomer compositions and filler loading ( Table 1 ).
Code | Resin composites | Filler loading | Resin matrix | Lot no. | Manufacturer | |
---|---|---|---|---|---|---|
wt.% a | vol.% | |||||
GRO | Grandio | 87 | 71.4 | Bis-GMA, TEGDMA | 581793 | Voco, Cuxhaven Germany |
GCK | G C Kalore | 82 | 69 | DX-511, UDMA and dimethacrylate co monomers | 0903171 | GC Europe |
VDD | Venus Diamond | 81.2 | 64 | TCD-DI-HEA UDMA | 010035 | Heraeus Kulzer, Germany |
FXE | Filtek Supreme XTE | 78.5 | 63.3 | BIS-GMA, BIS-EMA (6), TEGDMA, PEGDMA and UDMA | N147105 | 3 M ESPE Germany |
GDP | Gradia Direct Posterior | 77 | 65 | UDMA and dimethacrylate co-monomers | 0905201 | GC Europe |
GDA | Gradia Direct Anterior | 73 | 64 | UDMA and dimethacrylate co-monomers | 0901134 | GC Europe |
The Bioman instrument was used in this study to measure shrinkage stress kinetics ( Fig. 1 ) at 23 °C and 37 °C. This instrument incorporates a stiff cantilever load cell with a compliant end attached rigidly to a 2 cm thick stainless steel base-plate. The compliant end has an integral clamp holding a circular steel rod (10 mm in diameter, 22 mm long) in a vertical and perpendicular orientation to the load cell axis. Resin composite specimens were placed between two surfaces: the lower surface of the rod and a 3 mm thick glass plate surface. These two surfaces were lightly sandblasted to promote bonding of the composite specimens. The glass plate was held firmly in position by a metallic clamp and a hollow cylindrical bolt that allowed for passage of a straight light-curing optic to contact the lower surface of the glass plate. The specimen gap between the rod and glass plate was adjusted with the aid of a feeler gauge so that following placement of the specimen paste it would be 0.8 mm. Resin composite paste of standardized mass (0.12–0.15 g) was introduced into this space to form specimen disks of 10 mm diameter and 0.8 mm thickness (configuration factor = 6.25). After a period for temperature equilibration, the specimen was then photo-activated from below, by trans-illumination of the glass plate.
During polymerization, the stress created within the resin composite, between the opposing steel and glass surfaces, caused displacement of the compliant end of cantilever recording a signal via its strain-gauge load cell. This signal was amplified by a calibrated strain indicator (Model 3800, Vishay, Measurements Group, Raleigh, NC, USA) and was connected to a personal computer via data-logging hardware and software (Picotech, Cambridge, UK). The stress value in MPa was then obtained from the load, recorded a 1 s intervals, divided by the specimen disk area.
A newly designed heating device incorporating a heating element and connected to a power supply (Farnell E20-28, Farnell Ltd., Wetherby, UK) was used to provide a heat source for stress measurements at 37 °C ( Fig. 2 ). The power supply was set at 5.00 Volts to raise the heating element to 75 °C which was shown via thermocouple methods to set the resin composite specimen temperature to 37 °C. The resin composite specimen temperature reached 37 °C then stabilized for the next 60 min ( Fig. 3 ).
A light cure unit, with a modified straight curing tip and delivering a calibrated irradiance of 550 mW/cm 2 , (MARC RC, BlueLight Analytics, Inc., Halifax, Canada) was used to irradiate the specimen from beneath the glass plate for 40 s (energy density = 22 J/cm 2 ). Polymerization shrinkage stress was monitored for 60 min.
Statistical software (SPSS ver. 18, IBM Inc., USA) was used, and data were analysed by one-way analysis of variance (ANOVA). Prior to post hoc tests, data were analysed for equal variances using the homogeneity test ( p < 0.05). For data of shrinkage stress at 23 °C and 37 °C, equal variances can be assumed, thus Multiple pair-wise comparisons using a Tukey’s post hoc test were conducted to establish homogenous subsets at p = 0.05. Differences between groups for temperature and time effects were assessed using a paired t -test.
2
Materials and methods
Six commercial photo-activated resin-composites were selected on the basis of their matrix monomer compositions and filler loading ( Table 1 ).
Code | Resin composites | Filler loading | Resin matrix | Lot no. | Manufacturer | |
---|---|---|---|---|---|---|
wt.% a | vol.% | |||||
GRO | Grandio | 87 | 71.4 | Bis-GMA, TEGDMA | 581793 | Voco, Cuxhaven Germany |
GCK | G C Kalore | 82 | 69 | DX-511, UDMA and dimethacrylate co monomers | 0903171 | GC Europe |
VDD | Venus Diamond | 81.2 | 64 | TCD-DI-HEA UDMA | 010035 | Heraeus Kulzer, Germany |
FXE | Filtek Supreme XTE | 78.5 | 63.3 | BIS-GMA, BIS-EMA (6), TEGDMA, PEGDMA and UDMA | N147105 | 3 M ESPE Germany |
GDP | Gradia Direct Posterior | 77 | 65 | UDMA and dimethacrylate co-monomers | 0905201 | GC Europe |
GDA | Gradia Direct Anterior | 73 | 64 | UDMA and dimethacrylate co-monomers | 0901134 | GC Europe |
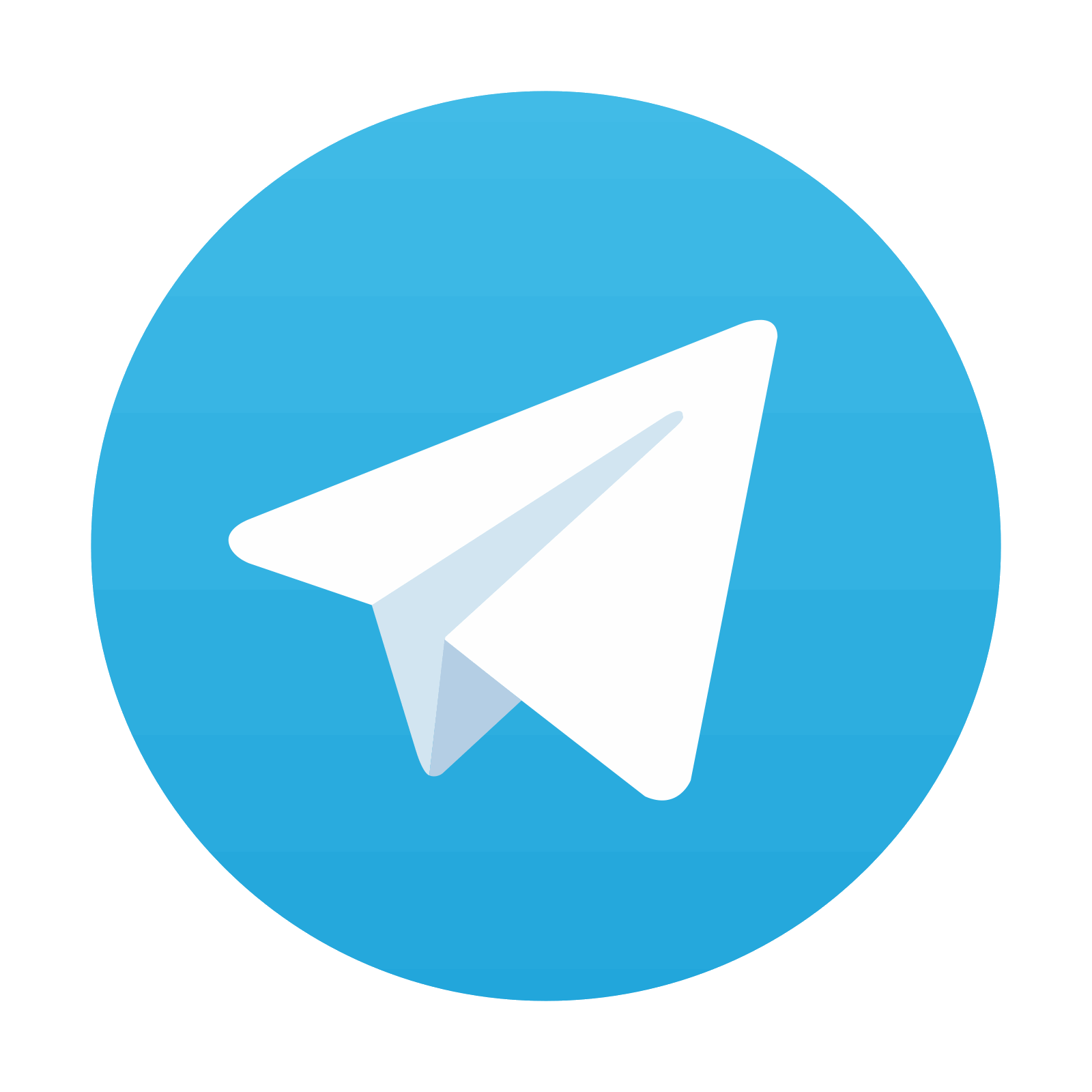
Stay updated, free dental videos. Join our Telegram channel

VIDEdental - Online dental courses
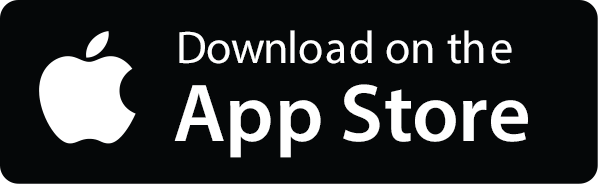

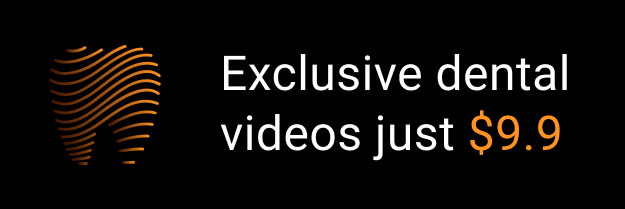