Graphical abstract
A different approach has been adopted to form highly branched polyacrylic acid (PAA) copolymers based on octavinyl polyhedral oligomeric silsesquioxane (octavinyl POSS). t -butyl acrylate star polymers with eight arms have been prepared from octavinyl-POSS using ATRP, and then the tertiary butyl acrylate has been hydrolysed to form PAA stars with a narrow distribution of molecular weights and a POSS core. The preparation of the polymer resins and their applications in the formation of glass ionomer cement (GICs) have been investigated.
Abstract
Objective
To investigate the application of a new type of multiarm polymer resins in the formulation of Glass Ionic Cements.
Methods
A series of star copolymers of t -butyl acrylate has been prepared by ATRP using a multiarm POSS-Br 8 initiator. The resulting POSS-co- t -butyl acrylate star copolymers with eight arms were subsequently hydrolysed by trifluoroacetic acid to produce the corresponding POSS-co-acrylic acid star copolymers. All of the copolymers have been characterized by 1 H and 13 C NMR and FTIR spectroscopies and TGA/DSC. The as-prepared star copolymers were mixed with the glass powder from Fuji IX GP to produce the GIC samples for compression testing.
Results
The new type of multiarm polymer resins have been shown to have narrow molecular weight distributions and thermal properties of the acrylic acid copolymers are similar to that of poly(acrylic acid), with a two stage degradation profile involving transitions at ≈140 °C and 250 °C, corresponding to anhydride formation and loss of carbon dioxide, respectively. In aqueous solution the POSS-co-acrylic acid copolymers form aggregates with ≈33 nm dimensions. When aqueous solutions of POSS-(PAA) 8 are mixed with a glass powder, a rigid glass ionomer cement, GIC, is formed with a maximum compressive stress significantly greater than that for a linear PAA GIC of a comparable polymer molecular weight.
Significance
Therefore, these POSS-(PAA) 8 copolymers demonstrate the potential for the application of well characterized star copolymers in the future development of new GICs as dental materials.
1
Introduction
Poly(acrylic acid), PAA, and its copolymers form an important class of polymeric materials with a broad range of applications in industry, biology and medicine. For example, amongst other applications, they are used as boiler scale removers in industry, in some bone cements used in medicine and as pH-sensitive controlled release devices in pharmaceuticals. In some applications the polymers are blended with other polymeric materials to form matrices with special properties, as in the case of glass ionomer cements, GICs, where PAA or its copolymers are mixed with water and a glass powder to form a rigid solid. The polyacid in the GIC forms strong ionic bonds with the polyvalent metal ions present in the glass powder to produce a hard amorphous matrix with a relatively low density .
PAA based GICs have found widely divergent applications, as exemplified by their use as the core materials of some golf balls and as restorative materials in dentistry . As dental materials, the GICs offer the advantages of being comprised of relatively cheap materials and they are simple to prepare. Their thermal expansion properties mimic the tooth structure, allowing them to achieve an hermetic seal when used as a bulk filling. However, although GICs are rigid materials, their material properties such as compressive strength and wear resistance are not as high as those of the acrylate-based restoratives. To improve the material properties of PAA based GICs, the acrylic acid, AA, is often copolymerized with other comonomers such as maleic acid, MA, or itaconic acid, IA . The role of these comonomers is to produce shorter sequences of AA in the copolymer chains, which lowers the viscosity of the liquid component of the GICs and also allows better interaction between the polycarboxylate anions and the polyvalent metal ions present in the glass of the GIC matrix .
Much work has been devoted to the improvement of the properties of GICs, most of which has been driven as a result of their applications in dentistry. Progress in this endeavor has been the subject of regular reviews .
The molecular weight of the PAA or its copolymers used in the preparation of the liquid component of a GIC is well known to influence the viscosity of the solution, and importantly the material properties of the final cured matrix . For a given PAA mass, the higher the molecular weight of a linear PAA, the higher the viscosity of the liquid component and the higher the compressibility and modulus of the GIC . In addition, the amount of water present in the liquid component has a strong effect on the GIC setting time, the aging profile of the GIC and its final overall material properties .
The glass powder is also a vital component in determining the GIC matrix properties, and is mainly responsible for determining properties such as the surface hardness of the GIC. The type of glass powder, the sizes of the glass particles and the polyvalent ions present in the glass all contribute to the properties of the ionically crosslinked matrix that is formed . Importantly, counter ions such as fluoride originally present in the glass powders can be released slowly from a GIC restorative, and this can have desirable effects on reducing tooth decay (formation of dental caries) and therefore improving the overall oral health of patients.
Another approach to improving the material properties of GICs has been to incorporate double bonds into the copolymer chain of the polyacid . These double bonds can then be photopolymerized during the curing process, thus crosslinking the polymer network so as to enhance properties such as the tensile and compressive strength. This type of GIC is commonly referred to as a resin modified glass ionomer cement (RMGIC). The simultaneous acid-base reaction and photopolymerization (dual setting system) of RMGICs enhances both the physical and mechanical properties of the GIC. This approach of forming both covalent polymer crosslinks and salt bridges has significantly expanded the use of GICs. However, the setting chemistry for RMGIC systems is complicated because the photochemical crosslinking reaction and the acid-base reaction can interfere with each other during cure. The acid-base medium affects the photochemical process and the presence of additional organic components can inhibit the acid-base neutralization process, along with the associated reduced diffusion coefficients of reactants and ions through a covalently cross-linked network .
Another disadvantage of RMGIC materials is their inherent tendency toward phase separation as the photochemical crosslinking reaction progresses. As a result of cross-linking the resin becomes water-insoluble, causing it to separate from the aqueous phase of the formulation. Thus neutralized, organic species can be induced to salt-out of the aqueous phase. This phase separating tendency means that the product is likely to contain domains of different composition .
Recently Zhao and coworkers have reported on the use of hyperbranched star-shaped PAA as a substitute polymer for linear PAA in the preparation of RMGICs . They have used ATRP to prepare hyperbranched star t -butyl acrylate with a narrow molecular weight distribution, which they subsequently hydrolysed to produce a hyperbranched poly(acrylic acid). The branches in the hyperbranched PAA all have double bonds at their termini which can be photopolymerized. These workers have found very significant improvements in the mechanical properties of RMGICs prepared from these hyperbranched polymers compared to an existing GIC Fuji II LC. In some cases improvements greater than ≈30–50% have been reported for polymers of comparable initial molecular weight. In addition to these material property improvements, solutions of hyperbranched polymers generally have lower viscosities than their linear equivalents, which is advantageous during mixing of the liquid component and the glass powder of the GICs.
In the current work, a different approach has been adopted to form highly branched PAA copolymers based on octavinyl polyhedral oligomeric silsesquioxane (octavinyl POSS). Here t -butyl acrylate star polymers with eight arms have been prepared from octavinyl-POSS using ATRP, and then the tertiary butyl acrylate has been hydrolysed to form PAA stars, POSS-(PLA) 8 , with a narrow distribution of molecular weights and a POSS core. Poly(acrylic acid) is an approved material for medical use and other polymers with the same central POSS core as POSS-(PAA) 8 have been shown to be non-cytotoxic and biocompatible . So the components of POSS-(PAA) 8 do not evoke any adverse biological responses.
The preparation of the polymer resins and their applications in the formation of GICs have been investigated.
2
Materials
Octavinyl polyhedral oligomeric silsesquioxane was obtained from Hybrid Plastics, (>97%, FW = 633.05), 2-mercaptoethanol (98%), 2-bromoisobutyryl bromide (BIBB) (98%), triethylamine (TEA) (>99.5%), N,N,N ′ ,N ″ ,N ″-pentamethyldiethylenetriamine (PMDETA) (98%), copper(II) bromide (99%) and trifluoroacetic acid (TFA) (99%) were obtained from Sigma-Aldrich and used in the synthesis without further purification. The t -butyl acrylate ( t -BA) (98%), obtained from Sigma-Aldrich, was extracted with NaOH (5%) and distilled under vacuum. Copper(I) bromide (Sigma-Aldrich, 97%) was purified by stirring with acetic acid overnight. Tetrahydrofuran (THF) was dispensed via a solvent purification system (MB SPS-800 Auto, MBRAUN, München) and chloroform (CHCl 3 ) was used as received (Sigma-Aldrich, 99.8%).
2.1
Synthesis of ATRP macroinitiator POSS-(Br) 8
2.1.1
Synthesis of POSS-(OH) 8

First, the fidelity of the octavinyl-POSS was confirmed by 1 H NMR, as shown in Fig. 1 A , where the peak assignments are given in the figure.

The procedure used for preparation of POSS-(OH) 8 was similar to that used previously to prepare POSS-(COOH) 8 . 6.33 g (0.01 mol) of pure octavinyl polyhedral oligomeric silsesquioxane, 7.0 mL (0.09 mol) of 2-mercaptoethanol and 500 mg (1.43 mmol) diphenyl (2,4,6-trimethylbenzoyl)-phosphine oxide were dissolved in 50 mL of THF and purged with a slow argon stream for 15 min. The coupling reaction was carried out by exposing the reaction flask to UV light (UVitron Sunray 600 UVA irradiator) at a constant power of 0.73 mW cm −2 for 10 min at room temperature. THF was then partially removed by rotary evaporation and the concentrated product was shaken with petroleum ether (3 × 30 mL). The mixture was then stirred with diethyl ether (50 mL). The POSS-(OH) 8 precipitated out of the solution and was collected and dried over night in a vacuum oven at 40 °C.
The chemical structure and purity of the product was confirmed by 1 H NMR as demonstrated in Fig. 1 B, where the peak assignments are indicated on the figure. 1 H NMR: (300 MHz, DMSO): δ (ppm) = 0.92 ( t ; 2H; SiCH 2 ), 2.56 (m; 4H; CH 3 S/SCH 2 ), 3.41 ( t ; 2H; CH 2 ), 4.72 (br. s; 1H; OH).
2.1.2
Synthesis of POSS-(Br) 8

The POSS-Br macroinitiator (MW 2429.8) was synthesized using a procedure developed by Kyeremateng et al. 1.35 g (1.11 mmol) of POSS-OH was dissolved in 15 mL THF and 1.3 mL TEA was added to the solution. The mixture was cooled to 0 °C in an ice-water bath before 2 mL (16.18 mmol) of 2-bromoisobutyryl bromide dissolved in 10 mL THF was added dropwise through a funnel. The solution was heated up to 40 °C and stirred for 36 h. During the reaction progress, precipitation of triethylamine hydrobromide was observed and the solid was collected by filtration. THF was then evaporated off the filtrate to leave behind a brownish crude product. The crude product was redissolved in DCM and shaken with 1 wt% aqueous NaHCO 3 solution (3 × 30 mL). DCM was then evaporated to give the POSS-Br macroinitiator as a brownish oily substance with a yield of 1.32 g (0.54 mmol; 48.6%).
The chemical structure and purity of the product was confirmed by 1 H NMR as demonstrated in Fig. 1 C, where the peak assignments are shown on the figure. 1 H NMR: (300 MHz, CDCl 3 ): δ (ppm) = 1.07 ( t ; 2H; SiCH 2 ), 1.95 (s; 6H; CH 3 ), 2.71 ( t ; 2H; CH 2 S), 2.82 ( t ; 2H; SCH 2 ), 4.33 ( t ; 2H; CH 2 O). ATR-FTIR: The important bands (cm −1 ) = 2814–3027 (C H), 1732 (C O), 1386 (CH 3 ), 1272 (C O C), 653 (C Br).
2.2
Synthesis of POSS-(P( t -BA)) 8
The method adopted for the polymerization of t -BA was based on that reported by Davis and Matyjaszewski et al. . The conditions for the POSS-(P( t -BA)) 8 synthesis were optimized and are described below. The t -butylacrylate (3.45 × 10 −2 mol) and the catalyst, consisting of CuBr/CuBr 2 (5.1 × 10 −4 /0.36 × 10 −4 mol), were added to a round bottom flask, sealed with a rubber septum and degassed with argon. PMDETA (4.8 × 10 −4 mol) was added via a syringe and the solution stirred and purged with argon until a greenish Cu/ligand complex had formed. The POSS-(Br) 8 macroinitiator (1.16 × 10 −4 mol) was dissolved in deoxygenated THF (3 mL) and injected to the reaction mixture via a syringe. The reaction was carried out at 60 °C for 5 h. The reaction was then quenched by exposure to air and diluted with ∼2 mL of THF. The crude product solution was then purified by precipitation from water and dried under vacuum to give POSS-(P( t -BA)) 8 as a white solid.
The structure and purity of the POSS-(P( t -BA)) 8 was determined by 1 H NMR and ATR-FTIR analyses see Figs. 2 and 3 , respectively. 1 H NMR: (300 MHz, CDCl 3 ): δ (ppm) = 1.15 (s; 6H; CH 3 ), 1.26 ( t ; 2H; SiCH 2 ), 1.45 (br. s; CH 3 ), 1.68 (br. s; CH 2 ), 2.24 (br. s; CH), 2.61 ( t ; 2H; CH 2 S), 2.74 ( t ; 2H; SCH 2 ), 4.17 ( t ; 2H; CH 2 O). 13 C NMR: (300 MHz, CDCl 3 ): δ (ppm) = 27.7 (m; SiCH 2 /CH 3 /CH 3 -backbone), 30.9 (s; CH 2 -backbone), 35.6 (s; 1C; CH 2 S), 37.3 (s; 1C; SCH 2 ), 42.0 (s; C/CH-backbone), 80.3 (s; CH 2 O/CO-backbone), 174.2 (s; CO 2 /CO 2 -backbone). ATR-FTIR: (neat, cm −1 ): 3050–2850 (C H str), 1720 (C O str), 1448 (CH 2 def), 1367 (CH 3 def), 1140 (Si C str), 1030 (Si O Si asym str).
2.3
Procedure for POSS-(P( t -BA)) 8 hydrolysis
For the conversion of POSS-(P( t -BA)) 8 into POSS-(PAA) 8 , typically 1 g of POSS-(P( t -BA)) 8 was dissolved in 12 mL CHCl 3 and 3 mL TFA was added. The reaction mixture was stirred for 20 h at room temperature. During the reaction progress, the hydrolysed product precipitated out of solution due to the radical change in polarity. The precipitate was filtered off and washed with pentane. For further purification, the product was dissolved in methanol and extracted with pentane (2 × 20 mL). Methanol was evaporated to leave POSS-(PAA) 8 as a slightly brownish solid.
The POSS-(PAA) 8 was characterized by 1 H and 13 C NMR as shown in Fig. 4 and by ATR-FTIR analysis ( Fig. 3 ).
2.4
Analytical methods
2.4.1
Nuclear magnetic resonance spectroscopy (NMR)
NMR spectra were recorded on a Bruker 300 instrument, using the Varian software VnmrJv2.2 Revision D. A 300 MHz field was used for 1 H NMR and 13 C NMR and the chemical shift values are referred to residual solvent resonances.
2.4.2
Fourier transform infrared spectroscopy (FT-IR)
Infrared spectra were collected on a Nicolet 5700 FT-IR spectrometer equipped with a Smart Diamond attenuated total reflectance (ATR) accessory which was operated via OMNIC software. The spectra were collected on dried samples over a wavelength range between 4000 and 400 cm −1 and for a total of 120 scans. The IR signals were normalized to the absorption band at 1448 cm −1 which was ascribed to the C H vibration of the CH 2 groups that were found to be the least varying throughout the ester hydrolysis reaction.
2.4.3
Gel permeation chromatography
A Waters 2414 GPC system was used for polymer chain separation based on the size exclusion principle. Two types of columns were used in series, a Styro-gel HT-6E and a Styro-gel HT-3 column. The columns were maintained at 40 °C with a flow rate of 1 mL/min during all analysis. The GPC device was fitted with a RI, a UV and a MALS detector and was operated with Empower software. The calibration was performed using polystyrene narrow standards and the molecular weights evaluated relative to the polystyrene standard. 2–3 mg polymer was used for analyses and were dissolved in 1 mL THF and filtered through a syringe filter of 0.45 μm pore size.
2.4.4
Differential scanning calorimetry (DSC)
A Mettler Toledo calorimeter operated by STAR e software was used for the DSC analysis. Dry samples (4–6 mg) were placed in 40 μL aluminum pan and sealed with an aluminum lid. The scans were run from 10 to 450 °C at 5 °C min −1 under N 2 atmosphere.
2.4.5
Thermogravimetric analysis (TGA)
A Mettler Toledo TGA operated by STAR e software was used for the thermal gravimetric analysis. Dried samples (4–6 mg) in 40 μL aluminum pans sealed with an aluminum lid were scanned from 30 to 450 °C at 5 °C min −1 under air atmosphere.
2.4.6
Transmission electron microscopy (TEM)
Transmission electron microscopy (TEM) images were obtained using a JEOL 1010 electron microscope with an acceleration voltage of 100 kV. A POSS-(PAA) 8 solution (1 mg mL −1 ) was prepared at room temperature in a 2 mL glass vial using ultrapure water. An aliquot of the solution was then cast onto a carbon-coated holey carbon grid and the sample was left to dry on the grid before TEM examination.
2.4.7
Preparation of GICs and compression tests
In this study it was decided to use the commercial product Fuji IX GP as the reference GIC and to use the same glass powder as that used in preparing Fuji IX GP GIC. To ensure consistency in the preparation of the GICs, the liquid component and the glass powder were mixed using a high speed mixer for encapsulated dental cements, which was supplied by Monitex Industrial Co. Ltd, Taiwan.
The GIC samples were prepared and cured according to the British Standard Specification for Dental Glass Ionomer Cements BS 6039, except that a smaller sample size (2 mm × 4 mm) was used because of instrumental requirements. The POSS-(PAA) 8 GIC samples were prepared using a standard Fuji IX GP capsule with the liquid component in the capsule replaced by an equal volume of an aqueous solution of POSS-(PAA) 8 . The powder component of the capsule consists of 95 wt% alumino-fluoro-silicate glass and 5 wt% PAA . The samples of Fuji IX GP were prepared at the same time from unmodified capsules.
After mixing, cylindrical samples of the GICs were prepared in Perspex molds of 2 mm diameter and 4 mm length. At least five cylindrical samples were prepared for each copolymer concentration. In preparing these samples, great care was taken to avoid any formation of voids by carefully packing the mixtures firmly into the molds. Following curing for one hour at 37 °C in a humid curing chamber, the samples were released from the molds and examined closely to ensure the absence of any undesirable defects. Any defective samples were discarded.
The compression tests were conducted on an Instron 5543 peel strength machine using the cylindrical samples. The Instron was operated with a crosshead speed of 1 mm min −1 via Bluehill 2 software. At least five replicate tests were carried out at each GIC composition and the mechanical properties reported as the average of the test results, with the associated experimental error being one standard error in the mean of the measurements. The toughness of the samples was determined from the area under the stress–strain curve.
2
Materials
Octavinyl polyhedral oligomeric silsesquioxane was obtained from Hybrid Plastics, (>97%, FW = 633.05), 2-mercaptoethanol (98%), 2-bromoisobutyryl bromide (BIBB) (98%), triethylamine (TEA) (>99.5%), N,N,N ′ ,N ″ ,N ″-pentamethyldiethylenetriamine (PMDETA) (98%), copper(II) bromide (99%) and trifluoroacetic acid (TFA) (99%) were obtained from Sigma-Aldrich and used in the synthesis without further purification. The t -butyl acrylate ( t -BA) (98%), obtained from Sigma-Aldrich, was extracted with NaOH (5%) and distilled under vacuum. Copper(I) bromide (Sigma-Aldrich, 97%) was purified by stirring with acetic acid overnight. Tetrahydrofuran (THF) was dispensed via a solvent purification system (MB SPS-800 Auto, MBRAUN, München) and chloroform (CHCl 3 ) was used as received (Sigma-Aldrich, 99.8%).
2.1
Synthesis of ATRP macroinitiator POSS-(Br) 8
2.1.1
Synthesis of POSS-(OH) 8
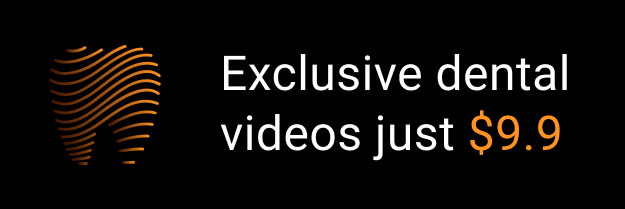