Abstract
Objectives
This study aimed to fabricate and characterise silanated and titanated nanobarium titanate (NBT) filled poly(methyl methacrylate) (PMMA) denture base composites and to evaluate the behaviour of a titanate coupling agent (TCA) as an alternative coupling agent to silane. The effect of filler surface modification on fracture toughness was also studied.
Methods
Silanated, titanated and pure NBT at 5% were incorporated in PMMA matrix. Neat PMMA matrix served as a control. NBT was sonicated in MMA prior to mixing with the PMMA. Curing was carried out using a water bath at 75 °C for 1.5 h and then at 100 °C for 30 min. NBT was characterised via Fourier transform-infrared spectroscopy (FTIR), Transmission Electron Microscopy (TEM) and Brunauer–Emmett–Teller (BET) analysis before and after surface modification. The porosity and fracture toughness of the PMMA nanocomposites ( n = 6, for each formulation and test) were also evaluated.
Results
NBT was successfully functionalised by the coupling agents. The TCA exhibited the lowest percentage of porosity (0.09%), whereas silane revealed 0.53% porosity. Statistically significant differences in fracture toughness were observed among the fracture toughness values of the tested samples ( p < 0.05). While the fracture toughness of untreated samples was reduced by 8%, an enhancement of 25% was achieved after titanation. In addition, the fracture toughness of the titanated samples was higher than the silanated ones by 10%.
Conclusion
Formation of a monolayer on the surface of TCA enhanced the NBT dispersion, however agglomeration of silanated NBT was observed due to insufficient coverage of NBT surface. Such behaviour led to reducing the porosity level and improving fracture toughness of titanated NBT/PMMA composites. Thus, TCA seemed to be more effective than silane.
Clinical significance
Minimising the porosity level could have the potential to reduce fungus growth on denture base resin to be hygienically accepTable Such enhancements obtained with Ti-NBT could lead to promotion of the composites’ longevity.
1
Introduction
A strong bond between the inorganic filler particles and the organic resin matrix during settling is crucial to obtain dental composites with an excellent clinical performance. This phenomenon is achieved through the use of coupling agents, such as silanes. These couplers are frequently used to improve the interfacial adhesion among dental composite phases. The filler–matrix interphase is the least abundant phase of composites, but this phase significantly affects the physico-mechanical properties of composites. Silane coupling agents are reportedly efficient in improving matrix-to-filler adhesion . However, some studies concluded that current silane coupling agents are not ideal because of their reduced mechanical properties . Using other metal primers may improve the performance of composites and thus increase the longevity and predictability of bonding procedures . Previous studies reported that applying an acetone primer to a glass prior to silane treatment improves silane bond; however, such as procedure does not solve the problem of silane degradation in oral fluids .
Titanate coupling agents (TCAs) could be favourable alternative coupling agents to silanes. Tham et al. investigated the effect of TCAs on the mechanical and morphological properties of poly(methyl methacrylate) (PMMA) denture base composites and indicated that TCAs can strengthen interphase bonding, improve mechanical properties, enhance filler homogenous dispersibility and modify the rheological behaviour of composites. Another work studied the effect of TCA treatment on various properties of fly ash-filled polypropylene (PP) composites. This study found that the presence of TCA increases the interfacial interaction between fly ash and PP, as well as improves the dispersion of fly ash in a PP matrix. Thus, the treatment improves the mechanical and thermal properties of fly ash-filled composites. Rojek et al. evaluated the mechanical properties of polyamide matrix composites filled with titanate-modified coal and concluded that mechanical properties of polyamides filled with titanated pit coal are higher than those of silanes. In our previous work , we mentioned that the chemical compatibility between the dispersed phase and the coupling agent should be considered. The accurate selection of a coupling agent is critical to obtain high-performance composites for dental applications.
PMMA in its bulk, polymerised form is widely used in denture fabrication because of its aesthetic value, easy operation, low cost and excellent biocompatibility. However, PMMA possesses insufficient mechanical strength and surface hardness when used alone; in particular, it easily breaks during an accident or when a patient applies a high mastication force to the denture base . Fracture toughness (K IC ) is an inherent characteristic of a material which describes its capability to resist crack propagation. Fracture occurs when the stress concentration inside the material reaches the critical level known as the ‘plane strain fracture toughness’, which is a measure of the crack resistance of a material. Characterisation of this material property can thus help prevent catastrophic failures . The mechanical properties of PMMA may be improved through nanoparticle addition. The introduction of nanomaterials offers a new promise for augmenting the mechanical properties of dental composites because the high surface area-to-volume ratio of these materials enhances their interfacial interaction with the resin matrix . The properties of polymer nanocomposites depend on the type of incorporated nanoparticles, their size, shape and distribution, as well as the concentration and interaction with the polymer matrix .
Nanocomposites composed of inorganic nanoparticles and organic polymers represent a new class of materials which exhibit improved performance when compared with microparticles . Nanomaterials with a small particle size and a high specific surface area show excellent performance and unique features different from conventional materials. When inorganic nanoparticles function as fillers in polymer materials, the superior characteristics of both polymer materials and nanomaterials integrate to enhance the rigidity, hardness, fracture toughness, optical property and other functional properties of composites . Nanofillers such as SiO 2 , ZrO 2 and Al 2 O 3 are usually used . Nanoparticles have been used in dental composites and interfacial silane reformulation . Nanobarium titanate (NBT), as a class of ceramic systems, displays interesting features for biological applications because of its favourable mechanical properties . In the current study, NBT is introduced as a new dental filler. The biocompatibility of TCAs and NBT has been reported ; however, the applications of such materials in dentistry are still limited. This topic, particularly in relation to denture base composites, has yet to be included in dental literature. Therefore, this study aimed to fabricate and characterise silanated and titanated NBT filled PMMA denture base composites and to evaluate the effect of TCA on the fracture toughness.
2
Materials and methods
2.1
Materials
The solid components consisted of PMMA (molecular weight: 996,000 GPC) and 0.5% benzoyl peroxide (BPO). The liquid component comprised methyl methacrylate (MMA) stabilised with 0.0025% hydroquinone plus the cross linking agent 10% ethylene glycol dimethacrylate (EGDMA). NBT supplied in powder form constituted the filler. These materials were purchased from Sigma–Aldrich (USA).
NBT was divided into three groups. The first group denoted as Un-NBT was incorporated as an untreated filler. The second group denoted as Si-NBT was treated with the silane coupling agent 3-(trimethoxysilyl) propyl methacrylate (γ-MPS) ( Fig. 1 a), which was also supplied by Sigma–Aldrich (USA). The last group denoted as Ti-NBT was treated with the TCA, KR 12 or isopropyl tri[di(octyl) phosphato] titanate ( Fig. 1 b). This coupler was provided by Kenrich Petrochemicals (USA).

2.2
Methods
2.2.1
Surface modification of NBT
γ-MPS was applied as reported by Alsharif et al. . A solution of acetone/water in a ratio of 70/30 was prepared in a glass beaker. NBT (5 g) was dispersed in the solution under stirring. Then, 10 wt.% γ-MPS relative to the filler was added dropwise with a sterile syringe under rapid stirring. The beaker was covered by Parafilm and left for stirring for approximately 15 min under magnetic stirring. The slurry was sonicated for 20 min to disrupt agglomeration. The mixture was further stirred at 80 °C until acetone was completely evaporated to allow the occurrence of the coupling reaction . Finally, the modified NBT was dried for 24 h in a vacuum oven at 120 °C.
For the TCA, 5 g of NBT was added to 100 mL of acetone followed by KR 12 under stirring for 15 min. The mixture was maintained under sonication for 20 min at room temperature for deagglomeration. The slurry was stirred for 30 min and then the temperature of the mixture was increased up to 80 °C to remove the solvent. Finally, the modified NBT was dried for 24 h in a vacuum oven at 120 °C.
2.2.2
Sample preparation
Table 1 shows the different formulations used to prepare the samples ( n = 6, for each group). The filler (5 wt.%) treated with the two coupling agents and the untreated filler were used. Control samples comprised pure PMMA. Modified and unmodified NBT were added to the liquid part (MMA monomer and 10% EGDMA) under stirring to obtain complete wetting of the filler surface and then ultrasonicated for 20 min. The mixture was transferred to the stirrer before adding the solid components (PMMA and 0.5% BPO) and mixing by hand. The powder/liquid solution in a 2.5:1 ratio by weight was mixed until the dough stage was reached. The mixture was kneaded and packed into the prepared moulds. Trial closure was performed at a low pressure, and excess materials were removed. The moulds were clamped and pressed under 14 MPa at room temperature for 25 min to allow proper penetration of the monomer into the polymer, even flow of the material and outward flow of the excess material. The moulds were immersed in a water bath at room temperature in a thermostatically controlled water bath. The temperature was slowly raised to 75 °C for 90 min and then elevated to the boiling point for 30 min. The moulds were allowed to bench cool before opening. The cured samples were carefully removed from the moulds, the excess flash was removed and the specimens were polished with fine sand paper.
Formulation | Control (wt%) | Un-NBT (wt%) | Si-NBT (wt%) | Ti-NBT (wt%) | |
---|---|---|---|---|---|
Powder | PMMA | 99.5 | 94.5 | 94.5 | 94.5 |
BPO | 0.5 | 0.5 | 0.5 | 0.5 | |
Liquid | MMA | 90 | 90 | 90 | 90 |
EGDMA | 10 | 10 | 10 | 10 | |
Filler | NBT | 0 | 5 | 5 | 5 |
Coupling agents | Silane | 0 | 0 | 10 | 0 |
Titanate | 0 | 0 | 0 | 2 |
2.2.3
Fourier transform infra-red spectroscopy (FTIR)
FTIR spectrophotometer (Perkin Elmer Spectrum 400) was used to characterise the NBT particles before and after treating. About 5 mg of each sample were mixed with about 95 mg of potassium bromide (KBr) prior to compacting into thin pellets with a hydraulic press, using 8 t of force and maintained for 3 min. The pellets were then inserted into a Nicolet Avatar 360 FTIR spectrophotometer and scanned with FTIR.
2.2.4
BET analysis
The BET surface area was measured using a conventional BET (ASAP 2020, Micromeritics Instruments). Before measurement, the samples were stored in a desiccator until testing. The samples were cooled with liquid nitrogen and analysed by measuring the volume of N 2 gas adsorbed at specific pressures. The samples were prepared by heating at 350 °C for 1 h while a flow of N 2 gas across the sample tube seeped the liberated contaminants. The specific surface area provides the average particle diameter (d) in nanometre in accordance with the formula below :
d = 6 × 10 3 S × ρ
where: S = specific surface area (m 2 /g) and ρ = density (g/cm 3 ).
2.2.5
Morphological characterisation
The morphology of the composites fracture surface was studied using field emission scanning electron microscopy (FESEM, Supra 55VP). All surfaces were gold coated to enhance image resolution and avoid electrostatic charging and to obtain better image resolution. energy-dispersive X-ray (EDX) test was applied to the treated filler in order to establish the chemical structure of filler after titanation. Transmission Electron Microscopy (TEM, TEMCM 12) was also applied to observe the NBT dispersion. Untreated, silanated and titanated NBT powder were prepared by dispersing in ethanol for 5 min and then one drop pipetted onto a carbon support film on a 3 mm copper grid. Image analysis on the NBT particles was carried out on various TEM images.
2.2.6
Porosity analysis
Specimens fractured in the fracture toughness test ( n = 6 for each formulation) were used to analyse the porosity level. A digital analytical balance was used to weigh each specimen in air and then in water. The absolute density of acrylic resin (1.198 ± 0.01 gm/cc) was used to calculate the percent mean porosity by using the following equations :
where: W a = specimen weight in air, W w = specimen weight in water, g = gravitational constant, d r = density of acrylic resin, d a = density of the air, d w = density of water, V sp = specimen volume, V ip = internal porosity volume.
In Eq. (2) , specimen volume minus volume of internal porosity was determined using the following known values: d r = 1.198 ±0.01 g/mL, d a = 1.23 kg/m 3 , d w = 1000 kg/m 3 and g = 9.8066 m/s 2 . The first equation for specimen volume minus internal porosity volume was solved, and the obtained value was used in Eq. (3) , along with W w measurement, to determine the volume of internal porosity. The specimen volume was calculated using known values for specimen volume minus internal porosity volume. The obtained specimen volume and internal porosity volume were used to calculate the total percent porosity with Eq. (4) .
2.2.7
Fracture toughness determination
The fracture toughness was performed on an Instron machine (model 5567 10KN) using single edge notch bending test (SEN-B) according to ISO 13586:2000. The test specimens (n = 6, per group) was carried out in moulded plate (thickness (t) = 4 mm, width (w) = 20 mm, span length (S) = 64 mm, overall length = 80 mm, notch length (a) = 4 mm) ( Fig. 2 ). The SEN-B specimens were tested at a crosshead speed of 1.00 mm/min. The values for K IC were calculated using the following Equation:

Geometrical correction factor (y) = 1.93–3.07 (a/w) + 14.53 (a/w) 2 –25.11 (a/w) 3 + 25.8 (a/w) 4 where: P = load at peak (N), S = span length (mm), a = notch length (mm), t = specimen thickness (mm), w = specimens width (mm).
Data of K IC were statistically analysed with analysis of variance (ANOVA) at the p < 0.05 significance level with SPSS (version 22, Statistical Package for Social Science, SPSS Inc., Chicago, IL, USA) to determine the differences between the groups.
2
Materials and methods
2.1
Materials
The solid components consisted of PMMA (molecular weight: 996,000 GPC) and 0.5% benzoyl peroxide (BPO). The liquid component comprised methyl methacrylate (MMA) stabilised with 0.0025% hydroquinone plus the cross linking agent 10% ethylene glycol dimethacrylate (EGDMA). NBT supplied in powder form constituted the filler. These materials were purchased from Sigma–Aldrich (USA).
NBT was divided into three groups. The first group denoted as Un-NBT was incorporated as an untreated filler. The second group denoted as Si-NBT was treated with the silane coupling agent 3-(trimethoxysilyl) propyl methacrylate (γ-MPS) ( Fig. 1 a), which was also supplied by Sigma–Aldrich (USA). The last group denoted as Ti-NBT was treated with the TCA, KR 12 or isopropyl tri[di(octyl) phosphato] titanate ( Fig. 1 b). This coupler was provided by Kenrich Petrochemicals (USA).
2.2
Methods
2.2.1
Surface modification of NBT
γ-MPS was applied as reported by Alsharif et al. . A solution of acetone/water in a ratio of 70/30 was prepared in a glass beaker. NBT (5 g) was dispersed in the solution under stirring. Then, 10 wt.% γ-MPS relative to the filler was added dropwise with a sterile syringe under rapid stirring. The beaker was covered by Parafilm and left for stirring for approximately 15 min under magnetic stirring. The slurry was sonicated for 20 min to disrupt agglomeration. The mixture was further stirred at 80 °C until acetone was completely evaporated to allow the occurrence of the coupling reaction . Finally, the modified NBT was dried for 24 h in a vacuum oven at 120 °C.
For the TCA, 5 g of NBT was added to 100 mL of acetone followed by KR 12 under stirring for 15 min. The mixture was maintained under sonication for 20 min at room temperature for deagglomeration. The slurry was stirred for 30 min and then the temperature of the mixture was increased up to 80 °C to remove the solvent. Finally, the modified NBT was dried for 24 h in a vacuum oven at 120 °C.
2.2.2
Sample preparation
Table 1 shows the different formulations used to prepare the samples ( n = 6, for each group). The filler (5 wt.%) treated with the two coupling agents and the untreated filler were used. Control samples comprised pure PMMA. Modified and unmodified NBT were added to the liquid part (MMA monomer and 10% EGDMA) under stirring to obtain complete wetting of the filler surface and then ultrasonicated for 20 min. The mixture was transferred to the stirrer before adding the solid components (PMMA and 0.5% BPO) and mixing by hand. The powder/liquid solution in a 2.5:1 ratio by weight was mixed until the dough stage was reached. The mixture was kneaded and packed into the prepared moulds. Trial closure was performed at a low pressure, and excess materials were removed. The moulds were clamped and pressed under 14 MPa at room temperature for 25 min to allow proper penetration of the monomer into the polymer, even flow of the material and outward flow of the excess material. The moulds were immersed in a water bath at room temperature in a thermostatically controlled water bath. The temperature was slowly raised to 75 °C for 90 min and then elevated to the boiling point for 30 min. The moulds were allowed to bench cool before opening. The cured samples were carefully removed from the moulds, the excess flash was removed and the specimens were polished with fine sand paper.
Formulation | Control (wt%) | Un-NBT (wt%) | Si-NBT (wt%) | Ti-NBT (wt%) | |
---|---|---|---|---|---|
Powder | PMMA | 99.5 | 94.5 | 94.5 | 94.5 |
BPO | 0.5 | 0.5 | 0.5 | 0.5 | |
Liquid | MMA | 90 | 90 | 90 | 90 |
EGDMA | 10 | 10 | 10 | 10 | |
Filler | NBT | 0 | 5 | 5 | 5 |
Coupling agents | Silane | 0 | 0 | 10 | 0 |
Titanate | 0 | 0 | 0 | 2 |
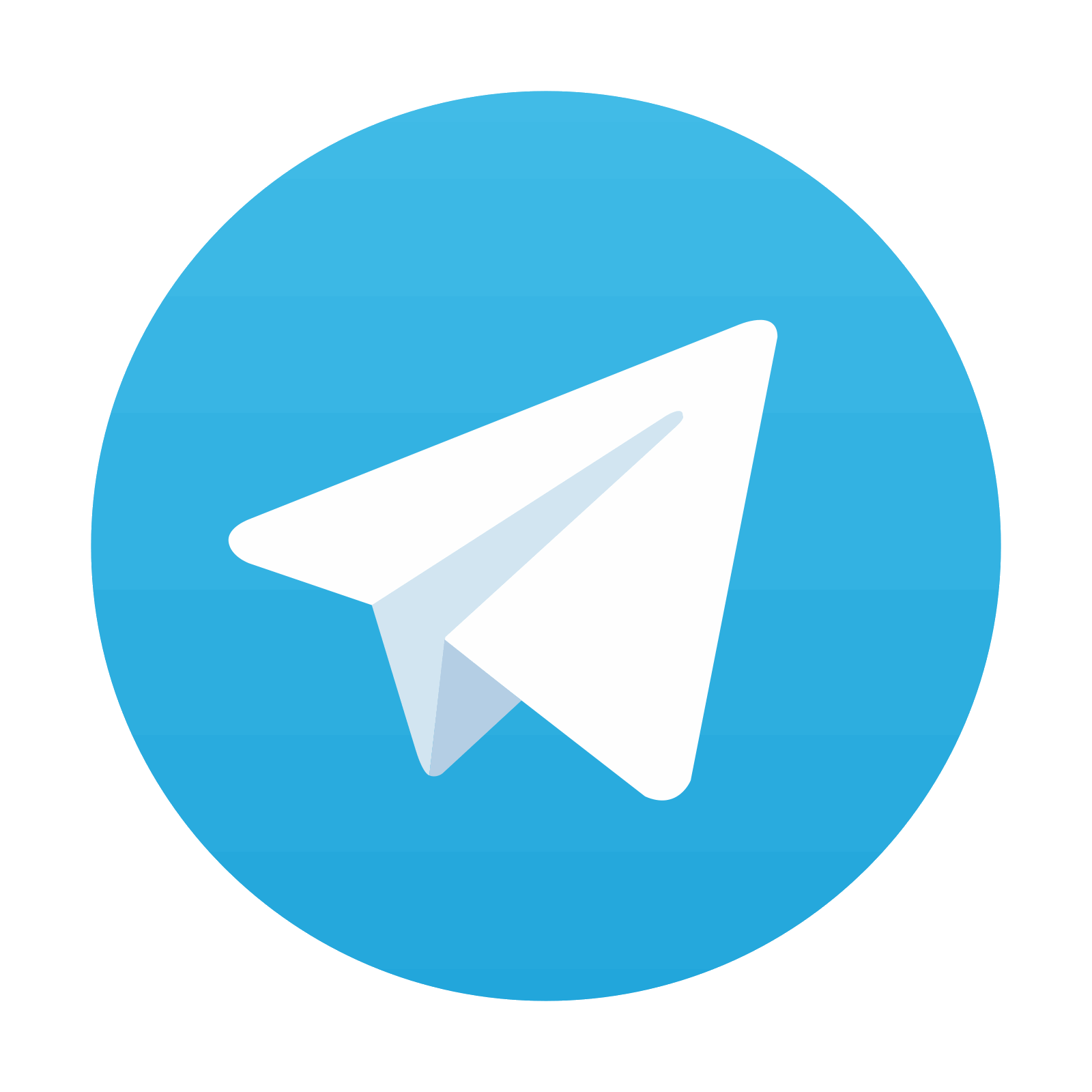
Stay updated, free dental videos. Join our Telegram channel

VIDEdental - Online dental courses
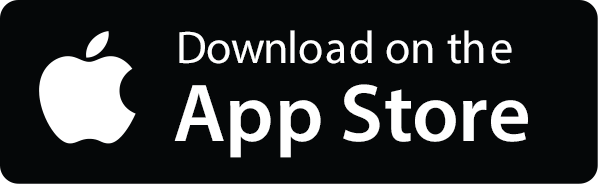

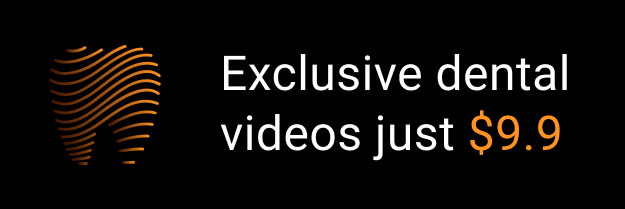