Abstract
Objective
To compare the fatigue life and damage modes of zirconia crowns fabricated with and without framework design modification when porcelain veneered using a fast or slow cooling protocol.
Methods
Composite resin replicas of a first molar full crown preparation were fabricated. Zirconia copings were milled as conventional (0.5 mm even thickness, Zr-C, n = 20,) or modified (lingual margin of 1.0 mm thickness, 2.0 mm height connected to two proximal struts of 3.5 mm height, Zr-M, n = 20). These groups were subdivided ( n = 10 each) according to the veneer cooling protocol employed: fast cooling (Zr-CFast and Zr-MFast) and slow cooling (Zr-CSlow and Zr-MSlow). Crowns were cemented and fatigued for 10 6 cycles in water. The number of cycles to failure was recorded and used to determine the interval databased 2-parameter probability Weibull distribution parameter Beta ( β ) and characteristic life value Eta ( η ).
Results
2-parameter Weibull calculation presented β = 5.53 and β = 4.38 for Zr-MFast and Zr-CFast, respectively. Slow cooled crowns did not fail by completion of 10 6 cycles, thereby Weibayes calculation was applied. Increased fatigue life was observed for slow cooled crowns compared to fast cooled ones. Groups Zr-MFast and Zr-MSlow presented no statistical difference. Porcelain cohesive fractures were mainly observed in fast cooled groups. Slow cooled crowns presented in some instances inner cone cracks not reaching the zirconia/veneer interface.
Significance
Improved fatigue life in tandem with the absence of porcelain fractures were observed in slow cooled crowns, regardless of framework design. Crowns fast cooled chiefly failed by porcelain cohesive fractures.
1
Introduction
Over the past ten years several in vitro and clinical studies have attempted to document and understand the nature of porcelain veneer cohesive fractures in all-ceramic restorations, specially yttria-tetragonal zirconia polycrystals (Y-TZP) . Besides issues related to manufacturing process (i.e., porosities and micro-structural defects) , chipping has been suggested to be strongly related with; residual thermal stress , coefficient of thermal expansion mismatches , poor framework design , and others .
Changes in the porcelain physical properties (during the transition from the visco-elastic to solid state) when it is cooled down from the sintering temperature to room temperature take place in every firing cycle . As a result, non-uniform residual thermal stresses may be produced throughout the porcelain veneer as a function of cooling rates . Such residual stress may be induced within the porcelain veneer either by thermal expansion mismatches or by the temperature gradients produced during cooling or both . Similarly to tempered glass, during a fast cooling process the outer crown surface becomes solid first and starts to contract inducing a compressive stress. However, while the inner surface is still in a visco-elastic state and at high temperature, leading to high tensile stress when the system reaches room temperature . This process is expected given that the porcelain veneer inner bulk remains in a temperature above its glass-transition temperature ( T g ), leading to the gradient temperature (difference between the inner and outer temperature) . As a consequence, residual thermal stresses are held within the porcelain veneer , also known as tempering. In addition, Y-TZP shows a low thermal diffusivity (thermal conductivity of 2 W m −1 K −1 whereas metals vary from 100 to 300 W m −1 K −1 ) , which may increase the thermal gradient intensity within veneer porcelain . Therefore, the multifaceted role of the above factors, has been speculated as potential sources related to high Y-TZP chipping rates reported in the literature .
Recently, efforts have been devoted to the reduction of residual thermal stresses in Y-TZP restorations by managing the rates of cooling . It has been reported that overall thermal gradients within the porcelain veneered to Y-TZP decreased when a slow cooling protocol was used . Also, thermodynamic analysis performed in molar crowns showed that different results may be achieved as a function of cooling protocols . It has been shown that slow cooling (the furnace door opened when the temperature was below the porcelain veneer T g ) produced a small temperature variation between the inner and outer surfaces of crowns and, more important, it decreased the residual thermal stresses within the veneer layer . However, to date few attempts regarding the influence of cooling rate on the fatigue life of Y-TZP crowns are available.
Most manufacturers of porcelain veneers for Y-TZP restorations have modified their firing guidelines, advocating that technicians adopt a slow cooling rate protocol. In 2009 for example, one manufacturer recommended that the furnace was opened soon after the end of the firing cycle , and a year later it was modified and crowns should be kept into the closed furnace up to temperature reaching 450 °C, slightly below the T g (490 °C) of the veneer porcelain .
Another topic that has frequently been revisited is framework design modifications in Y-TZP restorations . Clinical evaluations have suggested that porcelain chipping is frequently associated with areas without appropriate porcelain support (proximal areas) . This empirical concept relies on the fact that the porcelain veneer should have an even thickness, of no more than 2 mm, and be supported by the core . Although framework design modifications have shown to decrease chipping rates in clinical trials no control groups (i.e., even thickness framework) have been included, hindering a more comprehensive understanding between framework design modification and chipping .
In light of the aforementioned information, this study sought to evaluate the fatigue life and failure modes of Y-TZP molar crowns fabricated with two different porcelain veneer cooling protocols with and without framework design modification. The following null hypotheses were tested: (1) cooling protocols during glazing will not improve the fatigue life of Y-TZP systems and (2) framework design modification will not improve the fatigue life of Y-TZP crown systems, irrespective of cooling rate.
2
Materials and methods
2.1
Sample preparation
A plastic maxillary first molar positioned in a mannequin (Plastic mannequin tooth – MOM, Marilia, SP, Brazil) was prepared to receive a full crown by reducing the axial walls by 1.5 mm, the occlusal surface by 2.0 mm and shoulder margin (1.2 mm of thickness) with rounded internal angles. Afterwards, 40 composite resin replicas were obtained from a vinyl polysiloxane impression (Express – 3M ESPE, St. Paul, MN, USA) of the prepared tooth, which was incrementally (2.0 mm of thickness) packed with composite resin (Z100 – 3M ESPE, St. Paul, MN, USA) and light-cured (Ultralux, Dabi Atlante, Ribeirão Preto, SP, Brazil) according to manufacturer’s instructions. All resin tooth replicas were stored in distilled water for at least 30 days to minimize dimensional changes during testing . Each replica was vertically positioned in 25 mm diameter PVC tubes and potted with acrylic resin (Jet, Clássico Artigos Odontológicos, São Paulo, SP, Brazil). The preparation finish line was maintained 2 mm above the potting surface. Stone dies were acquired from polyether impressions (Impregum F – 3M-ESPE, St. Paul, MN, USA) of each resin-tooth replica and sent to a dental laboratory.
Stone dies were randomly divided in 2 groups ( n = 20, each) according to framework design, as: conventional (Zr-C) or modified design (Zr-M). Subsequently, each group was subdivided in two subgroups ( n = 10) according to thermal cooling protocol as: fast cooling protocol (Zr-CFast and Zr-MFast) and slow cooling protocol (Zr-CSlow and Zr-MSlow).
Frameworks were milled from pre-sintered Y-TZP blocks (e.max ZirCAD, shade MO 0, block size 15C – Ivoclar Vivadent, Schaan, Liechtenstein) and sintered in the furnace (Sintramat, Ivoclar Vivadent AG, Schaan, Liechtenstein) at 1500 °C for 8 h. Zr-C cores were manufactured with an even thickness of 0.5 mm. For Zr-M cores, a lingual margin (thickness of 1.0 mm with 2.0 mm height) connected to two proximal struts of 3.5 mm height were added to an even thickness of 0.5 mm, as described previously ( Fig. 1 ).
All Y-TZP cores were veneered with porcelain (IPS e.max Ceram, shade Transpa Clear – Ivoclar Vivadent AG, Schaan, Liechtenstein) and sintered in a ceramic furnace (Programat EP3000 – Ivoclar Vivadent, Schaan, Liechtenstein). The hand-layering process was performed in accordance with the manufacturer’s recommendation, starting with one liner firing (ZirLiner – Ivoclar Vivadent AG, Schaan, Liechtenstein) followed by firing two layers of porcelain. Finally, the crowns were manually finished and polished before the glaze firing. The firing schedule of liner and veneering porcelain are shown in Table 1 and Fig. 2 A . A silicone matrix (Zetalabor – Zhermack, Badia Polesine, Rovigo, Italy) of the unprepared plastic mannequin tooth was used to guide and standardize the porcelain veneer contour. The occlusal and axial surfaces showed approximately 1.5 and 1.0 mm of thickness, respectively. The glaze layer (Glaze Paste and Stain Liquid Long Life, IPS e.Max Ceram – Ivoclar Vivadent AG, Schaan, Liechtenstein) was applied onto the porcelain surface and treated according to one of the following cooling protocols ( Fig. 2 B and Table 2 ):
- •
Fast cooling: after the end of the glaze firing cycle, the furnace head was opened. Then, crowns were immediately taken out from the mesh-tray to the bench, leading to cool at room temperature. This thermal cycle followed manufacturer’s recommendation published in 2009 .
- •
Slow cooling protocol: the furnace had the cooling rate set to 10 °C/min and crowns were kept into the furnace until the temperature reached 50 °C, after which the furnace head was opened.
Program | ZirLiner | e.Max Ceram |
---|---|---|
Stand-by temperature | 403 °C | 403 °C |
Stand-by time | 4 min | 4 min |
Temperature increase | 40 °C/min | 40 °C/min |
Holding temperature | 960 °C | 750 °C |
Holding time | 1 min | 1 min |
Vacuum on | 450 °C | 450 °C |
Vacuum off | 959 °C | 749 °C |
Opening furnace | 960 °C | 750 °C |
Cooling rate | – | – |
Program | Fast cooling | Slow cooling |
---|---|---|
Stand-by temperature | 403 °C | 403 °C |
Stand-by time | 6 min | 6 min |
Temperature increase | 60 °C/min | 60 °C/min |
Holding temperature | 725 °C | 725 °C |
Holding time | 1 min | 1 min |
Vacuum on | 450 °C | 450 °C |
Vacuum off | 724 °C | 724 °C |
Opening furnace | 725 °C | 50 °C |
Cooling rate | – | 10 °C/min |
The glazed crowns were cemented to the aged resin-composite tooth replicas using a dual cure resin cement (Rely X ARC – 3M-ESPE, St. Paul, MN, USA) following the manufacturer’s instructions. No treatment was made in the Y-TZP cementation surface. Prior to mechanical testing, samples were incubated in distilled water at 37 °C for at least 24 h.
2.2
Fatigue test
Fatigue test was carried out in a fatigue machine (Model MSFM – Elquip – São Carlos, SP, Brazil) in r-ratio mode at a 30–300 N load range for 10 6 cycles or until failure under distilled water (37 °C) . As the indenter was in contact with the specimen, the initial contact load of 30 N was applied without abrasion, attrition or impact, steadily increasing to 300 N and decreasing back to 30 N. The load was applied through a spherical steel indenter (3.18 mm radius) on the center of the occlusal surface, at 2 Hz. Our attempt was to simulate the most typical molar relationship in natural dentition (Angle class I) where the mesiolingual cusp of the maxillary first molar is situated in the central fossa area of the mandibular first molar . After a predetermined number of cycles (125,000) the test was interrupted for crown surface damage accumulation inspection under stereomicroscopy (Leica Zeiss MZE, Mannheim, Germany). Specimens were then repositioned in the machine for an additional 125,000 cycles and inspections until completion of 10 6 cycles or failure.
2.3
Data analysis
The failure during fatigue was recorded as a function of the number of cycles. This information was used to determine the interval databased 2-parameter probability Weibull distribution for Zr-CFast and Zr-MFast (Weibull 7++; Reliasoft, Tucson, AZ, USA). Weibull shape parameter Beta ( β ) and characteristic value Eta ( η ) (here the number of stress cycles ( n ) at which 62.3% of the specimens would fail) were determined employing 90% confidence levels for upper and lower limits where applicable. If either one of groups displayed no failures, a Weibayes calculation was employed based on the β of the counter group’s distribution. Weibayes is a one-parameter Weibull analysis technique developed to “solve problems when traditional Weibull analysis has large uncertainties or cannot be used because there are no failures” . “A basic assumption governing the accuracy of Weibayes analysis and its associated test regimens is that the value of the Weibull shape parameter ( β ) is known or can be reasonably estimated”. “Knowledge of β can be derived from historical failure data, prior experience, or from engineering knowledge of the physics of the failure”. Given β , an equation may be derived using the method of maximum likelihood to determine the characteristic life, η , as follows :
η = ∑ i = 1 N T β i r 1 β
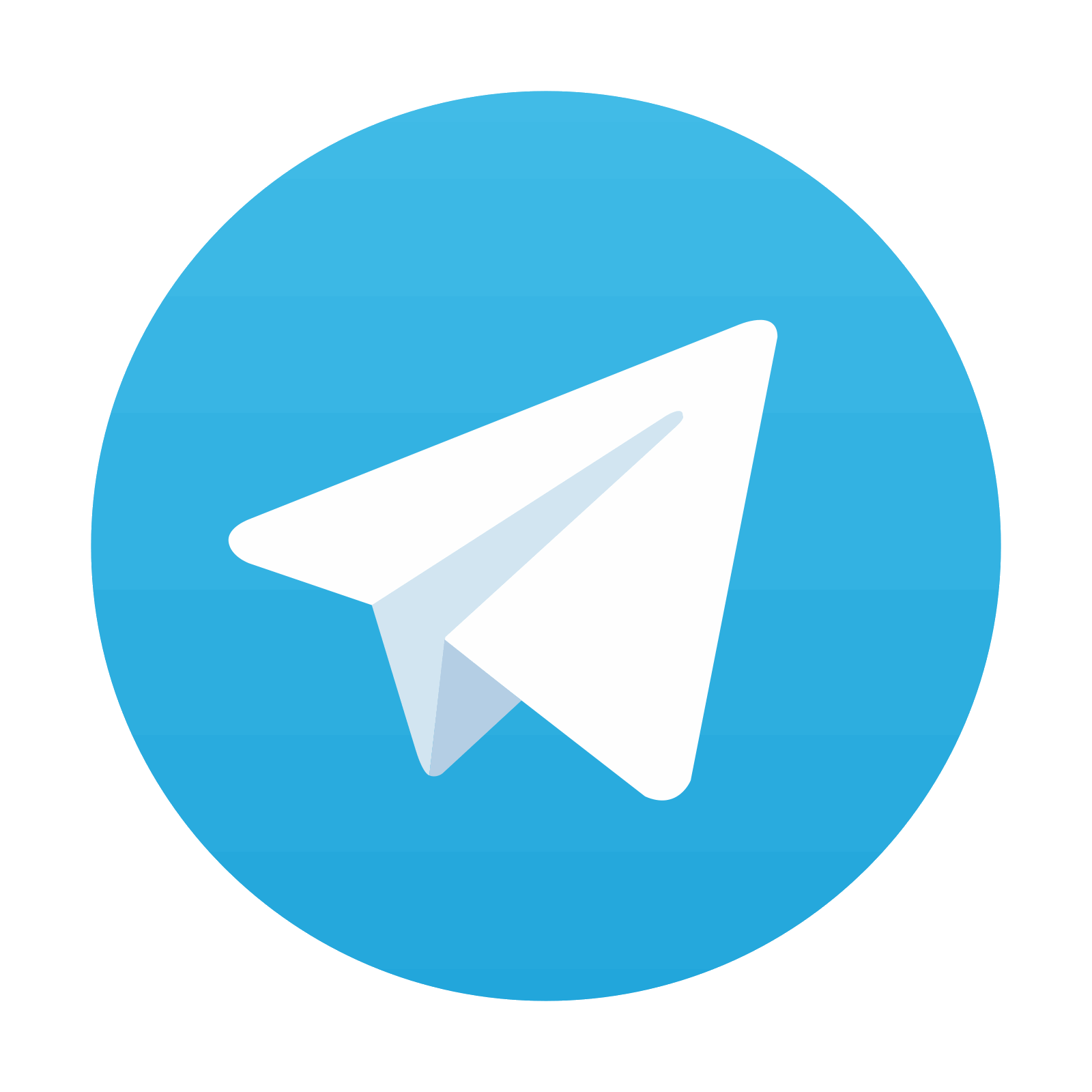
Stay updated, free dental videos. Join our Telegram channel

VIDEdental - Online dental courses
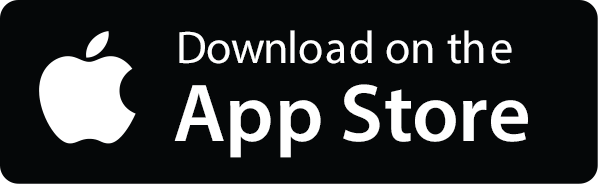
