Abstract
Objective
CAD–CAM blocks to fabricate semi-direct and indirect restorations are available in different sorts of ceramics as well as composite. In order to bond restorations prepared out of composite blocks into tooth cavities, it is recommended to gently sandblast the surface prior to the application of a primer/adhesive. Today, the effect of sandblasting composite block surfaces has not thoroughly been investigated. In this study, the ultra-structure of composite CAD–CAM blocks was investigated with special attention to the effect of sandblasting on the surface topography and of silanization on the bonding performance.
Methods
Five different composite CAD–CAM blocks were involved. We correlatively investigated their structural and chemical composition using X-ray diffraction (XRD), energy dispersion spectroscopy (EDS), scanning electron microscopy (SEM) and (scanning) transmission electron microscopy ((S)TEM). The effect of sandblasting was also imaged in cross-section and at the interface with composite cement. Finally, we measured the shear bond strength to the sandblasted block surface with and without silanization.
Results
All composite blocks revealed a different ultra-structure. Sandblasting increased surface roughness and resulted in an irregular surface with some filler exposure. Sandblasting also damaged the surface. When the sandblasted composite blocks were silanized, superior bonding receptiveness in terms of higher bond strength was achieved except for Shofu Block HC.
Significance
Sandblasting followed by silanization improved the bond strength to composite CAD–CAM blocks. However, sandblasting may also damage the composite CAD–CAM block surface. For the composite CAD–CAM block Shofu Block HC, the damage was so severe that silanization did not improve bond strength.
1
Introduction
In recent years, the fast progress in computer-assisted technology has dramatically changed today’s dental practice . Chairside CAD–CAM technology has already been available for more than 25 years in the form of the first-generation Cerec (Sirona, Bensheim, Germany) system. This technology has evolved to a well-established system, enabling either to construct semi-direct partial- or full-crown restorations or to apply it for digital impressioning, so the fixed partial denture (FPD) can be designed digitally and eventually milled in the dental technician lab . Today, other in-office CAD–CAM systems, like the E4D system (Planmeca, Helsinki, Finland), are available as well as there currently exists a plethora of intraoral scanners for digital impressioning; regarding the latter, one may expect that the use of conventional impressioning techniques using elastomeric impression materials will decrease in favor of digital impressioning.
Along with the fast innovation in digital dental devices, new CAD–CAM blocks in different sorts of ceramics have been developed, while most recently also CAD–CAM blocks in composite or in a ceramic–composite mixture, often being referred to as ‘polymer-infiltrated’ or ‘hybrid’ ceramic, have been produced . One of the first composite CAD–CAM blocks was Paradigm MZ100 (3M ESPE, St. Paul, MN, USA), but was only commercially available in certain markets . Since then, other composite CAD–CAM blocks were developed, using novel techniques to reach better degrees of conversion or more favorable filler loading and distributions . One of the major advantages of composite CAD–CAM blocks is the better milling accuracy; composite chips less at the restoration margin during milling than ceramic does . In addition, composite is more gentle in terms of abrasion for the opposing teeth . Some papers also documented that composite CAD–CAM blocks are superior in fatigue or fracture resistance than glass ceramics . Due to a recent installment of health insurance reimbursement in Japan regarding the use of composite CAD–CAM blocks for restoring premolars, many Japanese dental manufacturers have launched new composite CAD–CAM blocks to the Japanese market, of which some are also available outside Japan. Also noteworthy is the documented high de-bonding rate of Lava Ultimate (3M ESPE) composite blocks, having forced 3M ESPE to no longer support the indication to fabricate solitary crowns .
Since composite CAD–CAM blocks are relatively new materials, laboratory and clinical data are highly needed. Therefore, the structure of five composite CAD–CAM blocks was investigated, in particular to assess (1) the effect of sandblasting on their surface topography and (2) the effect of sandblasting and silanization on their bonding receptiveness. The null hypothesis investigated was that composite CAD–CAM blocks do not benefit from sandblasting and silanization with regard to their bonding receptiveness.
2
Materials and methods
Five composite CAD–CAM blocks were investigated in this study ( Table 1 ).
Product name | Company | Monomer composition | Filler composition | Filler mass (wt%) | Flexural strength (MPa) |
---|---|---|---|---|---|
Cerasmart | GC, Tokyo, Japan | Bis-MEPP, UDMA, DMA | SiO 2 (20 nm), barium glass (300 nm) | 71 | 240 |
Katana Avencia | Kuraray Noritake, Tokyo, Japan | UDMA, methacrylate monomer | SiO 2 (40 nm), Al 2 O 3 (20 nm) | 62 | 231 |
KZR-CAD HR | Yamakin, Osaka, Japan | UDMA, TEGDMA | SiO 2 –Al 2 O 3 –ZrO 2 (200–600 nm), SiO 2 (20 nm, 100 nm) | 73 | 235 |
Lava Ultimate | 3M ESPE, St. Paul, MN, USA | Bis-GMA, UDMA, bis-EMA, TEGDMA | SiO 2 (20 nm), ZrO 2 (4–11 nm), ZrO 2 /SiO 2 clusters | 80 | 204 |
Shofu Block HC | Shofu, Kyoto, Japan | UDMA, TEGDMA | SiO 2 , zirconium silicate | 61 | 191 |
a According to technical documentation from the respective manufacturers.
2.1
Scanning electron microscopy (SEM) of untreated composite CAD–CAM blocks
From block size 14, thin 1-mm thick slices were cut using a semi-automated high-speed diamond saw (Accutom, Struers, Ballerup, Denmark). For each brand, three CAD–CAM blocks were cross-sectioned by argon-ion milling (SM-090101 Cross-Section Polisher, JEOL, Tokyo, Japan). Subsequently, a thin layer of carbon was vaporized on the surface (JEE-420T Vacuum Evaporators, JEOL), after which the specimens were examined using Field-emission-gun SEM (Feg-SEM; JSM-6701F, JEOL), being operated at 5 kV and using an annular semi-conductor detector.
2.2
Scanning transmission electron microscopy (STEM) of untreated composite CAD–CAM blocks
Following SEM, the cross-sections were further processed for STEM using an argon-ion slicer (EM-09100IS Ion Slicer, JEOL). STEM (JEM-2100F, JEOL) was carried out employing an accelerating voltage of 200 kV and current density of 40 pA/cm 2 . Again, three different specimens for each composite CAD–CAM block were examined.
2.3
X-ray diffraction (XRD) of untreated composite CAD–CAM blocks
From block size 14, thin 1-mm thick slices were cut using the semi-automated high-speed diamond saw (Accutom, Struers). The surface was ground and polished using a 15-μm diamond lapping film in order to reach a mirror-polished surface. Three different specimens for each composite CAD–CAM block were prepared.
The crystal phases of the specimens were identified using an X-ray powder diffractometer (CuKα1 1.5406 Å, RINT 2500, Rigaku, Tokyo, Japan), operated at 40 kV acceleration and 200 mA current and a scanning rate of 0.02° s −1 for 2θ/θ scans.
2.4
SEM of sandblasted composite CAD–CAM blocks
Using the methods described above, additional 1-mm thick and mirror-polished specimens were prepared and sandblasted using a laboratory sandblaster (Hi-Blaster III, Shofu, Kyoto, Japan). With 50-μm aluminium oxide (HI ALUMINAS, Shofu, Kyoto, Japan) and at an air pressure of 0.2 MPa for 10 s, the device was held at a distance of 1 cm from the target surface. After coating the sandblasted surface with a thin layer of osmium (Neo Osmium Coater, Meiwafosis, Tokyo, Japan), Feg-SEM equipped with in-lens detectors (JSM-6701F, JEOL) was used to acquire high-resolution photomicrographs.
For SEM of the cross-sections, additional slice specimens were subjected to argon-ion milling (SM-090101 Cross-Section Polisher, JEOL) and osmium coating prior to Feg-SEM analysis. Three different specimens for each composite CAD–CAM block were examined.
2.5
Chemical elemental analysis of sandblasted composite CAD–CAM blocks
Element distributions of the sandblasted composite CAD–CAM blocks were determined using SEM (DC-720, Topcon, Tokyo, Japan) equipped with Energy dispersive X-ray spectroscopy (EDS; Noran Voyager III M3100, Noran Instruments, Middleton, Wisconsin, USA). Three different specimens for each composite CAD–CAM block were analyzed.
2.6
Shear bond strength (SBS) to sandblasted composite CAD–CAM blocks
Twenty 10 × 10 × 1-mm composite specimens were sandblasted as described above. Ten specimens were kept as such, while the second set of 10 specimens were treated with a silane-containing ceramic primer before cementation.
Zirconia cylinders were used to measure the bond strength of cement to the composite CAD–CAM blocks; Zirconia is strong enough and a composite cement can strongly be bonded to zirconia on the condition that it beforehand is sandblasted and chemically pre-treated with a combined MDP (10-methacryloyloxydecyl dihydrogen phosphate)/silane ceramic primer . Zirconia (Tosoh, Tokyo, Japan) cylinders of 2-mm height and 3.6-mm diameter were therefore sandblasted using a laboratory sandblaster (Hi-Blaster III, Shofu) with 50-μm aluminium oxide (Shofu) and at an air pressure of 4.0 MPa for 10 s. The device was held at a distance of 1 cm from the target zirconia surface. After having been treated with an MDP/silane-containing ceramic primer (Clearfil Ceramic Primer, Kuraray Noritake, Tokyo, Japan), the zirconia cylinders were luted to the composite CAD–CAM block specimens using a composite cement (Clearfil Esthetic Cement, Kuraray Noritake).
All bonded specimens were light-cured for 40 s from two opposite directions (totaling to a final curing time of 80 s) using G-Light Prima II Plus (light intensity of 2800 mW/cm 2 ; GC, Tokyo, Japan). After curing, the bonded specimens were stored in distilled water at 37 °C for 24 h. To measure the shear-bond strength, the bonded specimens were mounted in a universal testing machine (Model 5565, Instron, Canton, MA, USA) and exposed to shear stress at a cross-head speed of 0.5 mm/min. All fractured specimens were analyzed with a light microscope (4×) (SMZ-10, Nikon, Tokyo, Japan) to determine the fracture mode.
For statistical comparison, two-way ANOVA followed by Tukey’s multiple comparison test was used, whereby p < 0.05 was considered statistically significant.
2.7
Cross-section SEM and STEM of cement–composite CAD–CAM block interfaces
Each composite CAD–CAM block was sandblasted using a laboratory sandblaster (Hi-Blaster III, Shofu) with 50-μm aluminium oxide at 0.2-MPa air pressure. All sandblasted surfaces were treated with Clearfil Ceramic primer (Kuraray Noritake), upon which a luting composite (Clearfil Esthetic Cement, Kuraray Noritake) was applied and light-cured for 40 s (G-Light Prima II Plus). Cross-section specimens were prepared as described above and then observed using SEM and STEM.
2
Materials and methods
Five composite CAD–CAM blocks were investigated in this study ( Table 1 ).
Product name | Company | Monomer composition | Filler composition | Filler mass (wt%) | Flexural strength (MPa) |
---|---|---|---|---|---|
Cerasmart | GC, Tokyo, Japan | Bis-MEPP, UDMA, DMA | SiO 2 (20 nm), barium glass (300 nm) | 71 | 240 |
Katana Avencia | Kuraray Noritake, Tokyo, Japan | UDMA, methacrylate monomer | SiO 2 (40 nm), Al 2 O 3 (20 nm) | 62 | 231 |
KZR-CAD HR | Yamakin, Osaka, Japan | UDMA, TEGDMA | SiO 2 –Al 2 O 3 –ZrO 2 (200–600 nm), SiO 2 (20 nm, 100 nm) | 73 | 235 |
Lava Ultimate | 3M ESPE, St. Paul, MN, USA | Bis-GMA, UDMA, bis-EMA, TEGDMA | SiO 2 (20 nm), ZrO 2 (4–11 nm), ZrO 2 /SiO 2 clusters | 80 | 204 |
Shofu Block HC | Shofu, Kyoto, Japan | UDMA, TEGDMA | SiO 2 , zirconium silicate | 61 | 191 |
a According to technical documentation from the respective manufacturers.
2.1
Scanning electron microscopy (SEM) of untreated composite CAD–CAM blocks
From block size 14, thin 1-mm thick slices were cut using a semi-automated high-speed diamond saw (Accutom, Struers, Ballerup, Denmark). For each brand, three CAD–CAM blocks were cross-sectioned by argon-ion milling (SM-090101 Cross-Section Polisher, JEOL, Tokyo, Japan). Subsequently, a thin layer of carbon was vaporized on the surface (JEE-420T Vacuum Evaporators, JEOL), after which the specimens were examined using Field-emission-gun SEM (Feg-SEM; JSM-6701F, JEOL), being operated at 5 kV and using an annular semi-conductor detector.
2.2
Scanning transmission electron microscopy (STEM) of untreated composite CAD–CAM blocks
Following SEM, the cross-sections were further processed for STEM using an argon-ion slicer (EM-09100IS Ion Slicer, JEOL). STEM (JEM-2100F, JEOL) was carried out employing an accelerating voltage of 200 kV and current density of 40 pA/cm 2 . Again, three different specimens for each composite CAD–CAM block were examined.
2.3
X-ray diffraction (XRD) of untreated composite CAD–CAM blocks
From block size 14, thin 1-mm thick slices were cut using the semi-automated high-speed diamond saw (Accutom, Struers). The surface was ground and polished using a 15-μm diamond lapping film in order to reach a mirror-polished surface. Three different specimens for each composite CAD–CAM block were prepared.
The crystal phases of the specimens were identified using an X-ray powder diffractometer (CuKα1 1.5406 Å, RINT 2500, Rigaku, Tokyo, Japan), operated at 40 kV acceleration and 200 mA current and a scanning rate of 0.02° s −1 for 2θ/θ scans.
2.4
SEM of sandblasted composite CAD–CAM blocks
Using the methods described above, additional 1-mm thick and mirror-polished specimens were prepared and sandblasted using a laboratory sandblaster (Hi-Blaster III, Shofu, Kyoto, Japan). With 50-μm aluminium oxide (HI ALUMINAS, Shofu, Kyoto, Japan) and at an air pressure of 0.2 MPa for 10 s, the device was held at a distance of 1 cm from the target surface. After coating the sandblasted surface with a thin layer of osmium (Neo Osmium Coater, Meiwafosis, Tokyo, Japan), Feg-SEM equipped with in-lens detectors (JSM-6701F, JEOL) was used to acquire high-resolution photomicrographs.
For SEM of the cross-sections, additional slice specimens were subjected to argon-ion milling (SM-090101 Cross-Section Polisher, JEOL) and osmium coating prior to Feg-SEM analysis. Three different specimens for each composite CAD–CAM block were examined.
2.5
Chemical elemental analysis of sandblasted composite CAD–CAM blocks
Element distributions of the sandblasted composite CAD–CAM blocks were determined using SEM (DC-720, Topcon, Tokyo, Japan) equipped with Energy dispersive X-ray spectroscopy (EDS; Noran Voyager III M3100, Noran Instruments, Middleton, Wisconsin, USA). Three different specimens for each composite CAD–CAM block were analyzed.
2.6
Shear bond strength (SBS) to sandblasted composite CAD–CAM blocks
Twenty 10 × 10 × 1-mm composite specimens were sandblasted as described above. Ten specimens were kept as such, while the second set of 10 specimens were treated with a silane-containing ceramic primer before cementation.
Zirconia cylinders were used to measure the bond strength of cement to the composite CAD–CAM blocks; Zirconia is strong enough and a composite cement can strongly be bonded to zirconia on the condition that it beforehand is sandblasted and chemically pre-treated with a combined MDP (10-methacryloyloxydecyl dihydrogen phosphate)/silane ceramic primer . Zirconia (Tosoh, Tokyo, Japan) cylinders of 2-mm height and 3.6-mm diameter were therefore sandblasted using a laboratory sandblaster (Hi-Blaster III, Shofu) with 50-μm aluminium oxide (Shofu) and at an air pressure of 4.0 MPa for 10 s. The device was held at a distance of 1 cm from the target zirconia surface. After having been treated with an MDP/silane-containing ceramic primer (Clearfil Ceramic Primer, Kuraray Noritake, Tokyo, Japan), the zirconia cylinders were luted to the composite CAD–CAM block specimens using a composite cement (Clearfil Esthetic Cement, Kuraray Noritake).
All bonded specimens were light-cured for 40 s from two opposite directions (totaling to a final curing time of 80 s) using G-Light Prima II Plus (light intensity of 2800 mW/cm 2 ; GC, Tokyo, Japan). After curing, the bonded specimens were stored in distilled water at 37 °C for 24 h. To measure the shear-bond strength, the bonded specimens were mounted in a universal testing machine (Model 5565, Instron, Canton, MA, USA) and exposed to shear stress at a cross-head speed of 0.5 mm/min. All fractured specimens were analyzed with a light microscope (4×) (SMZ-10, Nikon, Tokyo, Japan) to determine the fracture mode.
For statistical comparison, two-way ANOVA followed by Tukey’s multiple comparison test was used, whereby p < 0.05 was considered statistically significant.
2.7
Cross-section SEM and STEM of cement–composite CAD–CAM block interfaces
Each composite CAD–CAM block was sandblasted using a laboratory sandblaster (Hi-Blaster III, Shofu) with 50-μm aluminium oxide at 0.2-MPa air pressure. All sandblasted surfaces were treated with Clearfil Ceramic primer (Kuraray Noritake), upon which a luting composite (Clearfil Esthetic Cement, Kuraray Noritake) was applied and light-cured for 40 s (G-Light Prima II Plus). Cross-section specimens were prepared as described above and then observed using SEM and STEM.
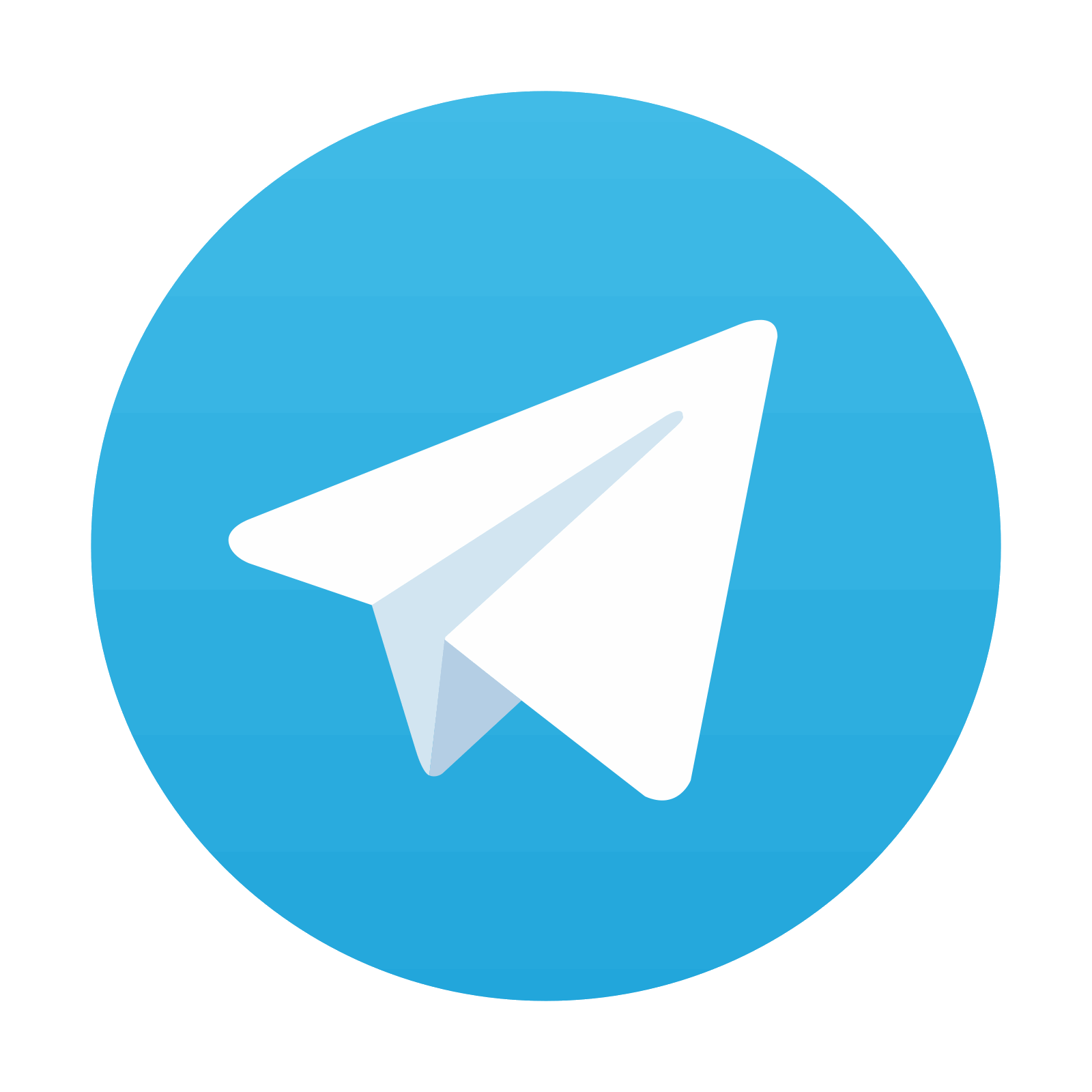
Stay updated, free dental videos. Join our Telegram channel

VIDEdental - Online dental courses
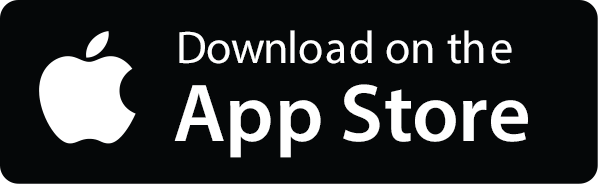
