Abstract
Objective
To test the hypothesis that the difference in the coefficient of thermal contraction of the veneering porcelain above ( α liquid ) and below ( α solid ) its T g plays an important role in stress development during a fast cooling protocol of Y-TZP crowns.
Methods
Three-dimensional finite element models of veneered Y-TZP crowns were developed. Heat transfer analyses were conducted with two cooling protocols: slow (group A) and fast (groups B–F). Calculated temperatures as a function of time were used to determine the thermal stresses. Porcelain α solid was kept constant while its α liquid was varied, creating different Δ α / α solid conditions: 0, 1, 1.5, 2 and 3 (groups B–F, respectively). Maximum ( σ 1 ) and minimum ( σ 3 ) residual principal stress distributions in the porcelain layer were compared.
Results
For the slowly cooled crown, positive σ 1 were observed in the porcelain, orientated perpendicular to the core–veneer interface (“radial” orientation). Simultaneously, negative σ 3 were observed within the porcelain, mostly in a hoop orientation (“hoop–arch”). For rapidly cooled crowns, stress patterns varied depending on Δ α / α solid ratios. For groups B and C, the patterns were similar to those found in group A for σ 1 (“radial”) and σ 3 (“hoop–arch”). For groups D–F, stress distribution changed significantly, with σ 1 forming a “hoop-arch” pattern while σ 3 developed a “radial” pattern.
Significance
Hoop tensile stresses generated in the veneering layer during fast cooling protocols due to porcelain high Δ α / α solid ratio will facilitate flaw propagation from the surface toward the core, which negatively affects the potential clinical longevity of a crown.
1
Introduction
Clinical trials have shown that the long-term success of veneered Yttria Tetragonal Zirconia Polycrystal (Y-TZP) crowns or fixed partial dentures is often compromised by chipping of the porcelain . The incidence of chipping failure is higher in Y-TZP restorations, in which framework fractures are generally uncommon . Depending on the size of the porcelain fragment, the chipped crown often needs to be replaced. Even when a simple polishing or a minor restoration can solve the problem, this clinical incident is very frustrating.
The strength of industrial glasses and ceramics can be increased by rapidly cooling the material from a temperature above the glass transition temperature ( T g ), the so-called thermal tempering . Between softening ( T s ) and glass transition temperatures, atomic rearrangements occur, resulting in significant changes in the material properties. At temperatures above T s , a material is in a liquid state. As the temperature drops below T s , the liquid densifies and atomic mobility becomes restricted. Below the glass transition region, these motions are even more difficult . As a consequence of these changes during cooling, the coefficient of thermal contraction of porcelains above their T s ( α liquid ) is much higher than the coefficient below T g ( α solid ). Meanwhile, the elastic modulus of a material above its T s is much lower than below T g .
During a well-known glass tempering procedure, achieved by rapidly cooling glass objects, the temperature decreases faster at the surface than in the interior . As a consequence, the outer surface solidifies ( T < T g ) and contracts first, while the interior remains in a liquid-like state, because it is still above T g . Therefore, thermal gradient induced stresses can be initially relaxed because of the viscoelastic behavior of the glass and no notable stresses are generated. When the inner part solidifies and tries to contract, the solid, elastic and colder outer surface, with a lower α , will not contract at the same rate, nor to the same extent . The contraction of the inner part creates a favorable residual stress field, with compressive stresses in the external region and tensile stresses in the interior. These superficial compressive stresses are known to strengthen the material, as any applied stress must initially overcome these compressive stresses before generating tensile stresses at the surface . Since the inner part of the glass generally does not contain flaws and generally does not contribute significantly to internal stresses during flexure, the resultant tempered body offers better fracture resistance .
Glass tempering principles have been adopted in Dentistry in order to strengthen veneering porcelain . Although rapid cooling protocols have been successfully used with metaloceramic systems, they have been associated with chipping failures in veneered zirconia-based systems . As a consequence, some researchers and manufacturers are recommending slow cooling for Y-TZP-core porcelain-veneered restorations .
In bilayered crowns, which behave differently from the above described tempering process in monolithic glass objects, the porcelain is supported by a stiff framework material, that will oppose the contraction of the porcelain. In such cases, the mismatch between the core and porcelain coefficient of thermal contraction ( α core − α veneer ) plays an important role in the residual stress distributions . It is well known that a small positive mismatch ( α core > α veneer ) is recommended for veneered dental crowns . However, during the cooling process the porcelain α changes abruptly as it passes through its T g . The α liquid ( T > T g ) of commercial porcelains recommended for Y-TZP frameworks can vary between 196% and 420% of the α solid value , depending on the material composition and microstructure. Meanwhile, the framework material α is not expected to change significantly, as its T g is not reached during porcelain firing. Therefore, the α mismatch between core and veneer can be highly negative ( α core ≪ α veneer ) above T g .
Hence, the hypothesis of this study is that, depending on the porcelain Δ α value ( α liquid ≪ α solid ), fast cooling the crown from temperatures above porcelain T g could generate high residual tensile stresses at the surface of the veneering ceramic instead of the compressive stresses that would be expected by the analogy with the tempering process of glass.
The objective of this work was to determine the influence of porcelain Δ α on the residual stress in Y-TZP crowns. Finite element analysis (FEA) was used to study the residual stresses within the complex geometries and temperature dependent material properties. Although experimental methodologies can be used to study residual stress profiles of veneered crowns, FEA offers the advantage of considering the complex nature of stress , which can be represented by a scalar value (when an equivalent stress is adopted) or by a second rank tensor (where the normal and shear stresses are individualized). Observing the local stress components is very useful to understand the effects of the cooling protocol and material properties on residual thermal stresses in veneered Y-TZP crowns , and, consequently, is crucial for designing strategies to minimize chipping failures.
2
Materials and methods
The three-dimensional (3D) FEA model was based on an experimental study in which the thermal gradient of symmetric veneered zirconia crowns, corresponding with the geometry of a premolar tooth, was measured . The use of rotationally symmetric crowns instead of anatomically precise ones was selected by Tholey et al. in order to ensure the production of identical samples and to simplify the thermocouple placement and cross-sectioning. Due to the geometric symmetry and boundary conditions, just 1/4 of the model needed to be modeled ( Fig. 1 ). The mesh consisted of 9851 four-node tetrahedral elements. A convergence test showed that no further refinement was necessary. The Y-TZP framework was considered homogeneous, isotropic and linear-elastic ( Table 1 ), while the porcelain thermoelastic properties were considered non-linear ( Figs. 2 and 3 ). The numerical analyses were performed with MSC.Marc (MSC Software, Santa Ana, CA, USA) and consisted of two steps: heat transfer analysis to establish temperature profiles and then thermal stress analysis.
Conductivity (W/mm °C) | Specific heat (J/kg °C) | Density (kg/mm 3 ) | Elastic modulus (GPa) | Poisson’s ratio | α solid (ppm °C −1 ) | References | |
---|---|---|---|---|---|---|---|
Y-TZP | 2.0 × 10 −3 | 450 | 6.0 × 10 −6 | 205 | 0.30 | 10.2 | |
Veneering porcelain | 1.5 × 10 −3 | 840 | 2.4 × 10 −6 | Fig. 2 | 0.21 | 9.2 |
2.1
Heat transfer analysis
Heat transfer analyses were conducted in accordance with a previous experimental study in which two cooling protocols were compared. In the first protocol a crown was slowly cooled in the furnace until the glass transition temperature (600 °C), after which it was removed from the furnace. In the second protocol the crown was removed from the furnace before reaching the glass transition temperature.
These two different cooling protocols were simulated by FEA. Due to their difference in cooling rates above T g , the two protocols were labeled as slow and fast, respectively. For slow cooling, it was assumed that all stresses generated above T g were relieved due to the viscoelastic behavior of the porcelain. Therefore, an initial temperature of 600 °C (porcelain T g ) was applied. For fast cooling, it was assumed that there was no time for stress relaxation below porcelain T s . Therefore, an initial temperature of 700 °C (porcelain T s ) was applied throughout the FEA model. For both models, the final equilibrium temperature was set at 25 °C.
The thermal properties of both materials are presented in Table 1 . Convective cooling was simulated using constant heat transfer coefficients (42 W/m 2 °C for the slow model and 250 W/m 2 °C for fast models) at the surface of veneering porcelain. The interior of the crown was assumed to be insulated. Although the cooling rate below T g does not influence the residual stress (it influences only transient stresses), different heat transfer coefficients were used in order to be consistent. The resultant cooling rates were 10 °C s −1 and 100 °C s −1 for slow and fast simulations, respectively.
The temperature distributions calculated in this thermal analysis are not presented in the results section, as they are not the primary scope of this study. Typically the maximum temperature difference between the external and internal surfaces of the crowns were 21 °C and 113 °C for the slow and fast cooling conditions, respectively. The temperature distribution as a function of time was used as the input data for the thermal stress analysis, allowing the simulation of changes in porcelain elastic modulus and α as a function of temperature ( Figs. 2 and 3 ).
2.2
Thermal stress analysis
In order to avoid rigid body motions, the axial displacement ( x -direction) of the cervical nodes was restricted ( Fig. 1 A). Symmetry ensured the boundary conditions in y – and z -directions ( Fig. 1 B and C). For slow cooling (group A), constant values of elastic modulus, Poisson’s ratio and α were applied ( Table 1 ).
For fast cooling models, the large increase in porcelain modulus close to the T g was taken into account ( Fig. 2 ). In addition, the porcelain α liquid was varied in order to create five Δ α / α solid conditions: 0, 1, 1.5, 2 and 3 (groups B–F, respectively. See Fig. 3 ). The first condition, Δ α / α solid = 0 was chosen to isolate the effects of elastic modulus variation between T s and T g and the difference in delta temperature between slow and fast protocols. The other four conditions were selected based on experimental Δ α / α solid measurements of commercial veneering porcelain, where values were varied from 0.95 to 3.20 . Therefore, the Δ α / α solid conditions tested in this study are comparable with the real scenario.
The residual maximum ( σ 1 ) and minimum ( σ 3 ) principal stress distributions and their orientation in the porcelain layer were compared. Positive values of σ 1 correspond to the highest tensile stress at each region, while negative values of σ 3 correspond to the highest compressive stress . High positive σ 1 tends to facilitate crack propagation, while high negative σ 3 tends to close critical flaws, protecting the veneer .
2
Materials and methods
The three-dimensional (3D) FEA model was based on an experimental study in which the thermal gradient of symmetric veneered zirconia crowns, corresponding with the geometry of a premolar tooth, was measured . The use of rotationally symmetric crowns instead of anatomically precise ones was selected by Tholey et al. in order to ensure the production of identical samples and to simplify the thermocouple placement and cross-sectioning. Due to the geometric symmetry and boundary conditions, just 1/4 of the model needed to be modeled ( Fig. 1 ). The mesh consisted of 9851 four-node tetrahedral elements. A convergence test showed that no further refinement was necessary. The Y-TZP framework was considered homogeneous, isotropic and linear-elastic ( Table 1 ), while the porcelain thermoelastic properties were considered non-linear ( Figs. 2 and 3 ). The numerical analyses were performed with MSC.Marc (MSC Software, Santa Ana, CA, USA) and consisted of two steps: heat transfer analysis to establish temperature profiles and then thermal stress analysis.
Conductivity (W/mm °C) | Specific heat (J/kg °C) | Density (kg/mm 3 ) | Elastic modulus (GPa) | Poisson’s ratio | α solid (ppm °C −1 ) | References | |
---|---|---|---|---|---|---|---|
Y-TZP | 2.0 × 10 −3 | 450 | 6.0 × 10 −6 | 205 | 0.30 | 10.2 | |
Veneering porcelain | 1.5 × 10 −3 | 840 | 2.4 × 10 −6 | Fig. 2 | 0.21 | 9.2 |
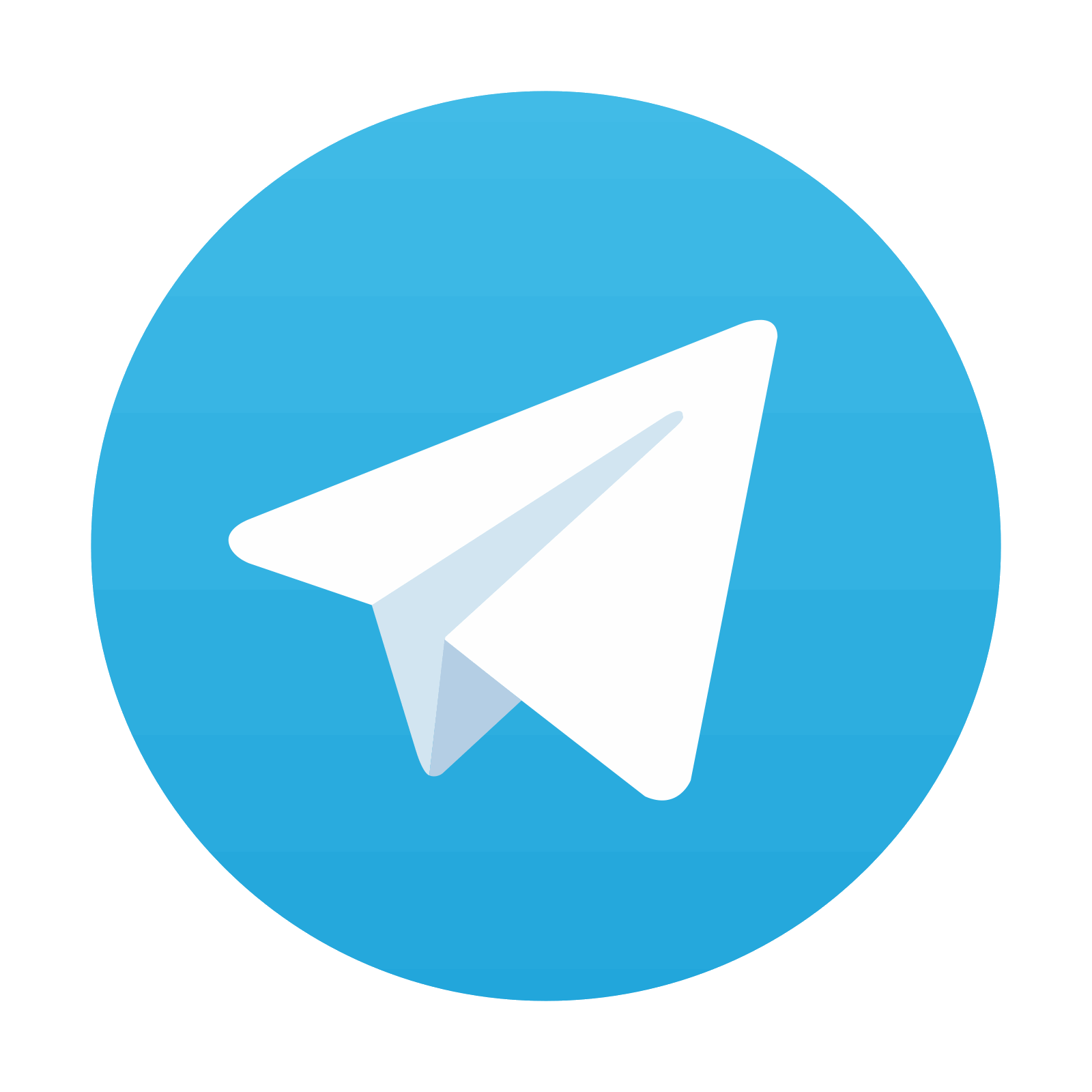
Stay updated, free dental videos. Join our Telegram channel

VIDEdental - Online dental courses
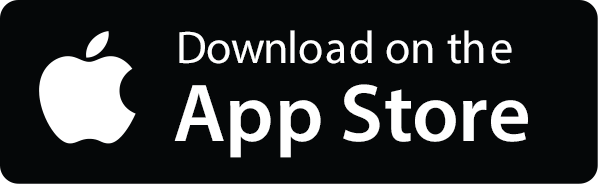

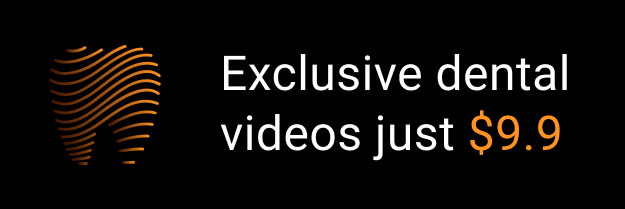