Abstract
Objectives
The residual stress profile developed within the veneering ceramic during the manufacturing process is an important predicting factor in chipping failures, which constitute a well-known problem with yttria-tetragonal-zirconia polycrystal (Y-TZP) based restorations. The objectives of this study are to measure and to compare the residual stress profile in the veneering ceramic layered on three different polycrystalline ceramic framework materials: Y-TZP, alumina polycrystal (AL) and zirconia toughened alumina (ZTA).
Methods
The stress profile was measured with the hole-drilling method in bilayered disk samples of 19 mm diameter with a 0.7 mm thick Y-TZP, AL or ZTA framework and a 1.5 mm thick layer of the corresponding veneering ceramic.
Results
The AL samples exhibited increasing compressive stresses with depth, while compressive stresses switching into interior tensile stresses were measured in Y-TZP samples. ZTA samples exhibited compressive stress at the ceramic surface, decreasing with depth up to 0.6 mm from the surface, and then becoming compressive again near the framework.
Significance
Y-TZP samples exhibited a less favorable stress profile than those of AL and ZTA samples. Results support the hypothesis of the occurrence of structural changes within the Y-TZP surface in contact with the veneering ceramic to explain the presence of tensile stresses. Even if the presence of Y-TZP in the alumina matrix seems to negatively affect the residual stress profiles in ZTA samples in comparison with AL samples, the registered profiles remain positive in terms of veneer fracture resistance.
1
Introduction
Polycrystalline ceramic frameworks appeared on the market in the nineties due to the development of CAD–CAM processing methods. The first commercialized material was alumina polycrystal (AL), while yttria-tetragonal-zirconia polycrystal (Y-TZP) was introduced for dental applications ten years ago.
AL exhibits high biocompatibility, esthetics, wear and corrosion resistance properties, but has a low fracture toughness and a limited flexural strength in comparison with Y-TZP . Despite these drawbacks, clinical studies about alumina anterior and posterior single crowns report high survival rate and few fractures of the veneering ceramic (chipping) .
Y-TZP has been proposed as an alternative to metal for dental crowns and fixed partial dentures (FPDs) frameworks because of its good biocompatibility, optical, strength and toughness properties. Nevertheless, clinical trials using zirconia-based restorations highlight unacceptable rates of veneer fracture . The chipping rate is reported to be significantly higher than for PFM systems and constitutes the first cause of failure of Y-TZP based restorations . Another disadvantage of Y-TZP is its metastable behavior, which can lead to low temperature degradation (LTD) due to the combined effect of time and water diffusion. The LTD process induces surface changes, leading to the formation of microcracks, and decrease of mechanical properties . The consequences of this phenomenon on the long-term performance of dental crowns and bridges are still unpredictable.
Alumina-zirconia composites were suggested for orthopedic implants in the early 2000s to overcome the LTD problem encountered with Y-TZP . Zirconia toughened alumina (ZTA) polycrystalline ceramics contain zirconia particles dispersed as a second phase in an alumina matrix. ZTA exhibits higher fracture toughness and stress intensity factor threshold in comparison with AL and could constitute a promising material for use as dental prosthesis framework. However, the mechanical behavior of the veneering ceramic to be layered on it is still unknown.
Knowledge about the residual stress distribution in the veneering ceramic as a function of depth, i.e. stress profile, is an important factor to understand and predict chipping. Residual stresses are “locked-in” stresses that are generated within the veneer and the framework during the cooling/solidification period of the veneer firing process. These stresses remain within the structure and will add to functional stresses generated during the chewing process. Compressive residual stresses reinforce the ceramic while tensile residual stresses facilitate the initiation and the propagation of cracks. The residual stress profile in the veneering ceramic is generated by the chronological effects of the thermal gradients occurring during the cooling/solidification period of the veneer liquid phase sintering process, and the mismatch in thermal expansion properties between core and veneering ceramics. Thermal gradients are influenced by cooling rate, material thickness and thermal conductivity. They induce a non-uniform solidification with time, since the temperature decreases faster at the surface than in the interior of the ceramic body, thereby causing a significant contraction mismatch within the material. Due to this tempering effect, residual stresses are compressive within the surface of the veneering ceramic, and their magnitude decreases with depth. In the case of PFM frameworks, the thermal expansion coefficient (CTE) of the veneering ceramic is usually slightly lower than that of the framework so that during cooling from T g to room temperature, interior compressive stresses are developed within the ceramic near the framework .
Recently, residual stress profiles were measured in metal- and Y-TZP-based disks samples. As expected, PFM structures showed only compressive stresses while surprisingly, in spite of the CTE mismatch and the cooling rates employed, the veneering ceramic layered on Y-TZP exhibited tensile stresses close to the interface with the framework. The presence of tensile stresses was found to depend on the veneer-framework thickness ratio and cooling rate and is a potential explanation for fractures encountered in clinical practice. The differences in residual stress profiles between metal and Y-TZP based structures were explained by Y-TZP’s metastable behavior and the hypothesis that structural changes occur in the Y-TZP surface in contact with the veneering ceramic during the manufacturing process. Those changes were supposed to be characterized by Y-TZP volume increase, which promotes tensile stress development in the veneer. Recently, Y-TZP surface alterations were highlighted with focused ion beam nanotomography at the veneer–zirconia interface in a sample exhibiting tensile stress, but their origin and their nature are still unknown .
To date, residual stress profiles have never been measured in veneering ceramics layered on alumina or ZTA frameworks. Some authors studied residual stress in veneering ceramics layered on alumina frameworks using 2D-computation or 3D-finite element analysis . Results vary from one study to the other depending on the different parameters settings. Moreover these technics encounter difficulties reproducing such a complex process as the ceramic firing procedure, especially in terms of temperature distribution within the specimen and variations of thermal and physical properties with temperature.
The first objective of the present study was to measure and compare the residual stress profile in the veneering ceramic layered on Y-TZP and alumina frameworks. Since Y-TZP is reported to be submitted to specific surface structural changes promoting tensile stress development, the null hypothesis was that in an opposite way AL does not undergo those changes and then promotes only compressive stresses, as metal. The second objective was to investigate the residual stress profile in the veneering ceramic layered on experimental ZTA, which is a mix of AL and Y-TZP, and is envisaged as a future framework material for dental prosthesis.
2
Materials and methods
2.1
Y-TZP, ZTA and AL pre-sintered blocks and cylinders manufacturing
Three experimental core materials were selected for the study: yttria-tetragonal-zirconia polycrystal (Y-TZP), alumina (AL) and zirconia-toughened alumina (ZTA). Y-Y-TZP and AL pre-sintered blocks were produced from a Y-TZP powder with an average particle size of 0.3 μm (TZ-3YSB, Tosoh, Japan) and a fine AL powder with an average particle size of 0.6 μm (CT-3000SDP, Almatis, Germany) respectively. The ZTA powder was produced as follows:
- (a)
16-h mixing, by ball milling (Pulverisette 5 Fritsch, Idar-Oberstein, Germany), of alumina (CT-3000SDP, Almatis, Germany) (85 vol.%) and Y-TZP (15 vol.%) powders in distilled water.
- (b)
Drying of the resulting suspension at 95 °C in an electric oven.
- (c)
Manual granulation of the powder with a 100 mesh screen.
The Y-TZP and ZTA powders were dry-pressed using uni-axial loading under 65 MPa and 100 MPa respectively, in a tungsten carbide mold (15.75 mm × 42.10 mm × 60 mm), and pre-sintered at 1050 °C (Y-TZP) or 1100 °C (ZTA) for 1 h, with an intermediate holding time of 1 h at 500 °C, for binder removal. The pre-sintered blocks final dimensions were 41.5 mm × 15.0 mm × 30 mm. Alumina cylinders (25 mm diameter) were slip cast in a cylindrical mold and presintered at 1180 °C during 2 h.
2.2
Specimen preparation
One mm-thick Y-TZP disks (25 mm diameter, n = 4), ZTA disks (23 mm diameter, n = 4) and AL disks (23 mm diameter, n = 4) were cut out the pre-sintered blocks or cylinders. The disks were ground with 500-grit silicon carbide disks (Struers LabPol polishing machine, Copenhagen, Denmark) to a 0.9 mm ± 0.02 mm for Y-TZP and 0.83 mm ± 0.02 mm thickness for both AL and ZTA. The different dimensions were designed to compensate the sintering shrinkage of each material respectively. Y-TZP disks were densely sintered at 1530 °C for 120 min with heating rate of 10 °C/min (Zircomat furnace, Vita Zahnfabrik, Bad Säckingen, Germany). AL and ZTA disks were densely sintered at 1600 °C for 120 min with a heating rate of 10 °C/min (Zircomat furnace, Vita Zahnfabrik, Bad Säckingen, Germany). All sintered disks exhibited 19 mm in diameter and 0.7 mm in thickness. Vita VM9 feldspar veneering ceramic (shade 3M2) (Vita Zahnfabrik, Bad Säckingen, Germany) was progressively layered on Y-TZP disks following standard dental laboratory procedures. Vita VM7 feldspar veneering ceramic (shade 3M2) (Vita Zahnfabrik, Bad Säckingen, Germany) was used for AL and ZTA disks. Three layers of dentin ceramic were successively fired, starting with a wash layer. The firing procedures were performed in a Vita Vacumat 4000 Premium furnace (Vita Zahnfabrik, Bad Säckingen, Germany) according to the manufacturer’s guidelines, as summarized in Table 1 . Then, samples were sequentially ground with 180-grit and 500-grit silicon carbide disks to obtain a1.50 ± 0.02 mm thick veneer layer.
Starting T (°C) | Pre-drying time (min) | Heating rate (°C/min) | Heating (min) | Firing temperature (°C) | Holding time (min) | Vacuum holding time (min) | |
---|---|---|---|---|---|---|---|
Vita VM9 Wash firing (first layer) | 500 | 2 | 55 | 8.11 | 950 | 6 | 8.11 |
Vita VM7 Wash firing (first layer) | 500 | 2 | 60 | 7.30 | 950 | 6 | 7.30 |
Vita VM7 and VM9 Dentin firing | 500 | 6 | 55 | 7.27 | 910 | 6 | 7.27 |
After final polishing, all specimens were exposed one by one to a last firing cycle. This last firing cycle restores the residual stress profile through the veneering ceramic thickness. All samples were placed in the same position, on the center of the mesh-tray and of the furnace. They were tempered from 910 °C to room temperature by opening the furnace door, as typically performed in dental laboratories, and removed from the mesh-tray at 200 °C. In compliance with the manufacturer’s recommendations, the firing temperature was maintained 6 min in place of 1 min in order to reach 910 °C within the framework.
2
Materials and methods
2.1
Y-TZP, ZTA and AL pre-sintered blocks and cylinders manufacturing
Three experimental core materials were selected for the study: yttria-tetragonal-zirconia polycrystal (Y-TZP), alumina (AL) and zirconia-toughened alumina (ZTA). Y-Y-TZP and AL pre-sintered blocks were produced from a Y-TZP powder with an average particle size of 0.3 μm (TZ-3YSB, Tosoh, Japan) and a fine AL powder with an average particle size of 0.6 μm (CT-3000SDP, Almatis, Germany) respectively. The ZTA powder was produced as follows:
- (a)
16-h mixing, by ball milling (Pulverisette 5 Fritsch, Idar-Oberstein, Germany), of alumina (CT-3000SDP, Almatis, Germany) (85 vol.%) and Y-TZP (15 vol.%) powders in distilled water.
- (b)
Drying of the resulting suspension at 95 °C in an electric oven.
- (c)
Manual granulation of the powder with a 100 mesh screen.
The Y-TZP and ZTA powders were dry-pressed using uni-axial loading under 65 MPa and 100 MPa respectively, in a tungsten carbide mold (15.75 mm × 42.10 mm × 60 mm), and pre-sintered at 1050 °C (Y-TZP) or 1100 °C (ZTA) for 1 h, with an intermediate holding time of 1 h at 500 °C, for binder removal. The pre-sintered blocks final dimensions were 41.5 mm × 15.0 mm × 30 mm. Alumina cylinders (25 mm diameter) were slip cast in a cylindrical mold and presintered at 1180 °C during 2 h.
2.2
Specimen preparation
One mm-thick Y-TZP disks (25 mm diameter, n = 4), ZTA disks (23 mm diameter, n = 4) and AL disks (23 mm diameter, n = 4) were cut out the pre-sintered blocks or cylinders. The disks were ground with 500-grit silicon carbide disks (Struers LabPol polishing machine, Copenhagen, Denmark) to a 0.9 mm ± 0.02 mm for Y-TZP and 0.83 mm ± 0.02 mm thickness for both AL and ZTA. The different dimensions were designed to compensate the sintering shrinkage of each material respectively. Y-TZP disks were densely sintered at 1530 °C for 120 min with heating rate of 10 °C/min (Zircomat furnace, Vita Zahnfabrik, Bad Säckingen, Germany). AL and ZTA disks were densely sintered at 1600 °C for 120 min with a heating rate of 10 °C/min (Zircomat furnace, Vita Zahnfabrik, Bad Säckingen, Germany). All sintered disks exhibited 19 mm in diameter and 0.7 mm in thickness. Vita VM9 feldspar veneering ceramic (shade 3M2) (Vita Zahnfabrik, Bad Säckingen, Germany) was progressively layered on Y-TZP disks following standard dental laboratory procedures. Vita VM7 feldspar veneering ceramic (shade 3M2) (Vita Zahnfabrik, Bad Säckingen, Germany) was used for AL and ZTA disks. Three layers of dentin ceramic were successively fired, starting with a wash layer. The firing procedures were performed in a Vita Vacumat 4000 Premium furnace (Vita Zahnfabrik, Bad Säckingen, Germany) according to the manufacturer’s guidelines, as summarized in Table 1 . Then, samples were sequentially ground with 180-grit and 500-grit silicon carbide disks to obtain a1.50 ± 0.02 mm thick veneer layer.
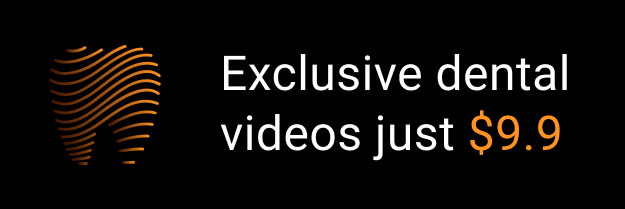