Graphical abstract
Micron-scale focused ion beam (FIB) ring-core methods allow for high-resolution residual stress profiling of dental prostheses materials.
Highlights
- •
Micron scale ring-core FIB–DIC method is used to map residual stress in dental prostheses.
- •
Results show complex residual stress profiles on veneering ceramic layers.
- •
A correlation is found between the distribution of compressive stress and indentation fracture toughness.
- •
Significant residual stress re-arrangement is measured in correspondence of interfacial micro-voids.
- •
Residual stress vs. toughness established correlations will help the design process of such materials.
Abstract
Objectives
The production of fixed partial dentures (FPDs) induces complex residual stress profiles, due to both the thermal expansion coefficient mismatch between the veneering ceramic and the framework and to the thermal gradients occurring during the final cooling. Detailed knowledge of residual stress distributions in the veneering ceramics is important to understand the interface phenomena with the framework and the consequences of the different firing systems. The first objective of this study was to analyse the residual stress distribution in heat-pressed ceramic on zirconia core with micrometer spatial resolution, with also a focus on the stress at the interface versus porcelain-fused-to-metal samples. The second purpose was to correlate the residual stress with the fracture toughness.
Methods
The micron-scale focused ion beam (FIB) ring-core method was used to map the residual stress over the cross-sections of the veneering ceramics. The methodology is based on FIB micro-milling of annular trenches, combined with high-resolution in situ scanning electron microscope (SEM) imaging, a full field strain analysis by digital image correlation (DIC) and numerical models for residual stress calculation. Fracture toughness was evaluated by using high load Vickers indentation and hardness/modulus were measured by nanoindentation testing also across the interfaces.
Results
Both prosthetic systems showed a compressive stress at the ceramic surface on a micron-scale. The stress profile for porcelain fused to metal (PFM) showed a transition to tensile stress at the half of the layer, whilst the stress in proximity of the interface was more compressive in both the cases. Residual stress on a micron scale are higher in magnitude than the corresponding macro-scale values reported in the literature, due to the stress relaxation given, at larger scales, by micro-voids and cracks. The stress field was directly correlated with the indentation fracture toughness, which was higher in those areas where the compressive stress is greater. Stress analysis in correspondence of interfacial porosity for the zirconia sample also showed that micro-defects could induce local modifications of the residual stress field, which may even locally generate a tensile stress state.
Significance
The interfacial stress in dental systems was analysed on a micron scale and can give further insights into the process/property/performance correlation for this class of materials. In particular, interfacial and/or local modifications of the residual stress are expected to have a significant influence on crack nucleation mechanism in correspondence of micro-defects. A direct correlation between residual stress distribution and fracture toughness was proposed. It is noteworthy that the method can be used to study real crowns and bridges. In fact, complex geometries can be easily analysed by this procedure.
1
Introduction
The in-service strength of metal–ceramic (porcelain-fused-to-metal, PFM) and zirconia–ceramic systems reported some clinical failures, so significant efforts were focused on studying the relationship between the different materials properties and their changes during the manufacturing of crowns and bridges in the dental lab (machining of partially or fully sintered blocks) . In case of the metal–ceramic systems, a strong interface is usually reported as the result of a chemical adhesion and a macro- (and micro-) mechanical interaction between the two components. The good interfacial adhesion is also correlated to compressive stress in the veneering ceramic, which are usually reported for such systems . Concerning the ZrO 2 –porcelain systems, both machining and sintering processes could generate complex residual stress profiles that may lead to in-service failures due to insufficient adhesion, poor load bearing capacity, fatigue resistance and reliability. The residual stress profiles in veneering ceramics arise from thermal gradients during the solidification of the liquid phase and the difference of thermal expansion coefficients during the final cooling .
Different techniques like optical interferometry and temperature thermocouple direct measurements were performed on rotationally symmetric experimental crowns to measure the residual stress as a consequence of the firing process as far as of different cooling modes. Also a finite element analysis (FEA) from temperature thermocouple direct measurements was used on experimental crowns to measure the influence of different cooling rates as a function of the ceramic thickness with or without alumina defect.
Recently, Mainjot et al. have performed an accurate assessment of the surface macro-scale residual stress fields in veneering ceramics, as reported in a series of papers . The Authors evaluated the effects of cooling rate and thickness of the veneering ceramic on the residual stress depth profile by the macro-scale hole drilling method. They observed a compressive stress at the free surface of the ceramic layer (−96 MPa), then decreasing with depth and becoming tensile at 0.5–1.0 mm from the surface; finally, it become slightly compressive again. Mechanisms on the stress formation and evaluation mechanisms are then proposed to explain the observed hole-drilling profiles .
The hole drilling method involves removal of a significant volume of material (usually a few mm 3 ), and could lead to local micro-cracks or artifacts in strain measurement due to local heating during the drilling process ; in addition, it cannot be applied directly to real crowns or bridges but only on flat samples . For such reasons, the hole drilling method cannot measure completely the interfacial stress field, as the maximum penetration depth is usually of the order of 1.2 mm .
Therefore, a lack of knowledge is still present in the current literature for the local assessment of residual stress distributions in dental prosthetic systems, and in particular the analysis of the residual stress fields in correspondence of the porcelain-framework interface.
In fact, no papers are currently available where the interfacial residual stress is locally measured with high spatial resolution and a correlation with toughness and failure modes still has to be found.
The aim of the present study was the characterization of the in vitro residual stress gradient across the interfaces of dental metal–ceramic (feldspatic) and zirconia–ceramic (heat-pressed) systems measured with sub-micrometer resolution, using a focused ion beam (FIB, Fig. 1 ) ring-core milling combined with digital image correlation strain analysis.

This method shares most of the features with the macro-scale hole-drilling procedure, but allows for the evaluation of local residual stress measurement with sub-micrometer spatial resolution with negligible damage induced by the FIB operations, as presented in previous studies . The mechanical properties of the materials are then measured by nano- and micro-indentation methods and finally a correlation to residual stress is proposed . To this purpose, high load Vickers micro-indentations are performed to characterize the fracture toughness at different positions of the veneering ceramic layer.
2
Experimental details
2.1
Sample preparation
Samples under investigation consisted of a ceramic–metal system, coded “ CM ” in the following (VE-Alloy, 8853 S.p.a., Italy and Ceramic Avanté ® , Pentron Ceramics Inc., Somerset, NJ, USA) and a ceramic–zirconia system, coded “ CZ ” (IPS e.max ® ZirCAD and Ceramic IPS e.max ® ZirPress, Ivoclar-Vivadent AG, Schaan, Liechtenstein).
Ten bars of the different systems were produced in the dental lab following the manufacturer’s instructions, where metal–ceramic specimens were the result of a ceramic veneering on the lost-wax alloy layer (porcelain-fused-to-metal) and the zirconia–ceramic samples were produced by the dedicated CAD-CAM procedures of the zirconia core (with final sintering) and the following veneered heat pressed ceramic. Thickness of both the frameworks was 1 mm and 2.1 mm for the porcelain in the metal-free samples. Veneering ceramic was 2.0 mm in metal framework samples. After glazing and polishing, square plates (4 mm × 4 mm) were manufactured by low speed diamond saw under pure ethanol (Bueheler ® IsoMet ® 1000), and then carefully mirror polished by a sequence of diamond lapping films. In case of ceramic materials, it is possible to assume that the polishing process does not significantly modify the residual stress state.
A complete characterization of the morphology and microstructure of coupling between veneering ceramic and ZrO 2 or metal alloy framework is reported in our previous work .
2.2
Residual stress field evaluation
The focused ion beam (FIB) micron scale incremental ring-core method was used to analyse the local residual stress state of the veneering ceramics. Some tests were made on different spots of carefully polished sections, from the surface of the ceramic layer to the interface to get the residual stress distribution. Each single measurement consists of a sequence of steps of FIB milling of micron-size annular trenches, as showed in Fig. 2 .

High-resolution in situ scanning electron microscope (SEM) imaging before and after the tests with a full field digital image correlation (DIC) was used for relaxation strain mapping. More details on the FIB milling procedures and the use of DIC algorithms for relaxation strain mapping are reported in our previous studies . A circular platinum wall (thickness 100 nm, diameter 3 μm), was deposited to protect the surface from re-deposition during FIB milling and to provide the ideally sharp edges of the produced pillar. Then, a grid of small platinum dots (diameter and depth of about 60 nm) was obtained in situ by electron beam assisted deposition, with no surface damage induced on the sample materials, as described in Fig. 2 a.
Annular trenches (6 μm outer and 3 μm inner diameters) were then FIB incrementally milled (48 pA at 30 kV) around the Pt-coated area with a step size of 100 nm. A series of ten SEM micrographs of the patterned area were acquired before first milling and after each milling step. The sequence of high-resolution SEM averaged images were then used as the input to a DIC routine to calculate the relaxation strain profiles at each incremental milling step as a function of milling depth. The average strain at a relative milling depth of h / d = 0.2, is finally obtained by polynomial fitting of the strain versus depth profile. Given the interpolated average relaxation strain for each single measurement, the local average residual stress field was then calculated according to the procedure described in our previous studies .
Previous results obtained by finite element simulation (FEM) have shown that a complete surface relaxation of the stress is achieved for h / d = 0.2 in case of the ring-core geometry. Therefore, we used the interpolated relaxation strain at h / d = 0.2 to calculate the average stress in the sample volume, by using the same calculation procedures reported in previous study , which are also similar to the one used for hole-drilling techniques .
2.3
Mechanical characterization
Hardness and elastic modulus were measured using Berkovich nanoindentation in accordance with the UNI EN 14577/1-2-3 standards. Tests were performed using a novel iNano nanoindentation system produced by Nanomechanics Inc. and operating in DSM mode (Dynamic Stiffness Measurement); thereby it was possible to evaluate the mechanical properties (hardness and modulus) along the profile of the lapped surface and mediated in depth ( Figs. 3 and 4 ). Constant strain rate 0.2 s −1 , DSM 80 Hz oscillation frequency, oscillation amplitude of 1 nm, a maximum indentation depth of 500 nm, Poisson’s ratio of the sample 0.25 for ceramics, 0.3 for the metal alloy. For each material, an array of 5 × 5 indentations was made in the core of the layer’s thickness to evaluate the mean value and the standard deviation. Then, profiles were realized across interfaces.

Fracture toughness of the porcelain layers was evaluated by using Vickers indentation testing following preliminary authors preliminary report , and according to the wide literature available in this field . All cracks were classified to be of radial–median geometry for the porcelain materials ( c / d > 2.5, being 2 c the total crack length and d the indentation size) , thus allowing one to use Anstis–Marshall model, described by the following equation:
K C = α ⋅ E H 1 / 2 ⋅ P c 3 / 2
where E is the elastic modulus, H is the hardness and α a constant that characterizes the shape of the Vickers indenter ( δ = 0.016 ± 0.004). In case of measurements in the zirconia layers, cracks were classified in the Palmqvist regime, and the specific model by Laugier was used for toughness calculation. The measurements were carried out with an applied load P of 5 N (0.5 kgf) for the porcelain, while a load of 2 kgf was used for zirconia (because it was the minimum load to induce any cracks in ZrO 2 ); then the crack length and geometry were measured by optical and SEM images. Failure mechanisms at the interface were observed by SEM and optical microscopy as well.
2
Experimental details
2.1
Sample preparation
Samples under investigation consisted of a ceramic–metal system, coded “ CM ” in the following (VE-Alloy, 8853 S.p.a., Italy and Ceramic Avanté ® , Pentron Ceramics Inc., Somerset, NJ, USA) and a ceramic–zirconia system, coded “ CZ ” (IPS e.max ® ZirCAD and Ceramic IPS e.max ® ZirPress, Ivoclar-Vivadent AG, Schaan, Liechtenstein).
Ten bars of the different systems were produced in the dental lab following the manufacturer’s instructions, where metal–ceramic specimens were the result of a ceramic veneering on the lost-wax alloy layer (porcelain-fused-to-metal) and the zirconia–ceramic samples were produced by the dedicated CAD-CAM procedures of the zirconia core (with final sintering) and the following veneered heat pressed ceramic. Thickness of both the frameworks was 1 mm and 2.1 mm for the porcelain in the metal-free samples. Veneering ceramic was 2.0 mm in metal framework samples. After glazing and polishing, square plates (4 mm × 4 mm) were manufactured by low speed diamond saw under pure ethanol (Bueheler ® IsoMet ® 1000), and then carefully mirror polished by a sequence of diamond lapping films. In case of ceramic materials, it is possible to assume that the polishing process does not significantly modify the residual stress state.
A complete characterization of the morphology and microstructure of coupling between veneering ceramic and ZrO 2 or metal alloy framework is reported in our previous work .
2.2
Residual stress field evaluation
The focused ion beam (FIB) micron scale incremental ring-core method was used to analyse the local residual stress state of the veneering ceramics. Some tests were made on different spots of carefully polished sections, from the surface of the ceramic layer to the interface to get the residual stress distribution. Each single measurement consists of a sequence of steps of FIB milling of micron-size annular trenches, as showed in Fig. 2 .
High-resolution in situ scanning electron microscope (SEM) imaging before and after the tests with a full field digital image correlation (DIC) was used for relaxation strain mapping. More details on the FIB milling procedures and the use of DIC algorithms for relaxation strain mapping are reported in our previous studies . A circular platinum wall (thickness 100 nm, diameter 3 μm), was deposited to protect the surface from re-deposition during FIB milling and to provide the ideally sharp edges of the produced pillar. Then, a grid of small platinum dots (diameter and depth of about 60 nm) was obtained in situ by electron beam assisted deposition, with no surface damage induced on the sample materials, as described in Fig. 2 a.
Annular trenches (6 μm outer and 3 μm inner diameters) were then FIB incrementally milled (48 pA at 30 kV) around the Pt-coated area with a step size of 100 nm. A series of ten SEM micrographs of the patterned area were acquired before first milling and after each milling step. The sequence of high-resolution SEM averaged images were then used as the input to a DIC routine to calculate the relaxation strain profiles at each incremental milling step as a function of milling depth. The average strain at a relative milling depth of h / d = 0.2, is finally obtained by polynomial fitting of the strain versus depth profile. Given the interpolated average relaxation strain for each single measurement, the local average residual stress field was then calculated according to the procedure described in our previous studies .
Previous results obtained by finite element simulation (FEM) have shown that a complete surface relaxation of the stress is achieved for h / d = 0.2 in case of the ring-core geometry. Therefore, we used the interpolated relaxation strain at h / d = 0.2 to calculate the average stress in the sample volume, by using the same calculation procedures reported in previous study , which are also similar to the one used for hole-drilling techniques .
2.3
Mechanical characterization
Hardness and elastic modulus were measured using Berkovich nanoindentation in accordance with the UNI EN 14577/1-2-3 standards. Tests were performed using a novel iNano nanoindentation system produced by Nanomechanics Inc. and operating in DSM mode (Dynamic Stiffness Measurement); thereby it was possible to evaluate the mechanical properties (hardness and modulus) along the profile of the lapped surface and mediated in depth ( Figs. 3 and 4 ). Constant strain rate 0.2 s −1 , DSM 80 Hz oscillation frequency, oscillation amplitude of 1 nm, a maximum indentation depth of 500 nm, Poisson’s ratio of the sample 0.25 for ceramics, 0.3 for the metal alloy. For each material, an array of 5 × 5 indentations was made in the core of the layer’s thickness to evaluate the mean value and the standard deviation. Then, profiles were realized across interfaces.
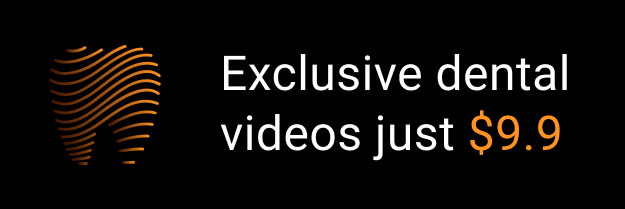