Abstract
Objectives
The aim of this study was to use high-pressure high-temperature (HP/HT) polymerization to produce urethane dimethacrylate (UDMA)–triethylene glycol dimethacrylate (TEGDMA) based resin composite blocks (RCB) suitable for dental computer-aided design/manufacture (CAD/CAM) applications and to compare their physical/mechanical properties to those of a commercial dental RCB. The null hypotheses tested were: (1) there are no differences in the physical/mechanical properties between HP/HT polymerized UDMA-TEGDMA RCB and a commercial RCB; (2) volume fraction filler ( V f ) does not affect the physical/mechanical properties of HP/HT polymerized RCB.
Methods
Four UDMA-based experimental RCB were manufactured under HP/HT conditions. A RCB manufactured under the same HP/HT conditions from a commercial resin composite (Z100) and its commercial counterpart CAD/CAM RCB (Paradigm MZ100) were used as controls. Flexural strength ( σ f ), fracture toughness ( K IC ), and hardness were determined. The results were analyzed using one-way ANOVA, Scheffé multiple means comparisons ( α = 0.05), and Weibull statistics (for σ f ). Scanning electron microscopy was used to characterize fractured surfaces.
Results
All HP/HT polymerized RCB had superior σ f , K IC , and Weibull modulus compared to the commercial dental RCB. The experimental RCB had similar or superior properties compared to HP/HT polymerized Z100 RCB. Fewer and smaller porosities (not quantified) were apparent in HP/HT polymerized RCB. The experimental RCB that contained 65% V f showed higher porosity, suggesting practical difficulties in filler incorporation beyond a certain V f .
Conclusions
The results of this study suggested that RCB suitable for dental CAD/CAM applications could be obtained by HP/HT polymerization of resin composites based on pure UDMA.
1
Introduction
Advances in materials science, digital imaging, and computer assisted design and manufacturing (CAD/CAM) have led to dramatic changes in the production of indirect dental restorations . Developments in manufacturing have been accompanied with corresponding advances in new materials amenable for CAD/CAM. While ceramic blocks, due to their superior esthetics and mechanical properties, remain the material of choice for CAD/CAM applications, resin composite blocks (RCB) seem to gain wider acceptance due to their ease of milling, lower cost, easier through-access in case of need (endodontics), and likelihood of easier repair . The first RCB suitable for CAD/CAM applications was introduced by 3M ESPE (Paradigm MZ100; 3M ESPE, St. Paul, MN, USA), based on their Z100 restorative direct resin composite. High-pressure high-temperature (HP/HT) polymerization of commercially available resin composites was proposed as a novel methodology to produce RCB suitable for CAD/CAM applications, with superior mechanical properties to those of the commercially available CAD/CAM RCB . Current concerns (even if not justified ) related to any material obtained from bisphenol A (4,4′-isopropylidinediphenol), encourage the avoidance of Bis-GMA [2-propenoic acid, 2-methyl-, (1-methylethylidene)bis(4,1-phenyleneoxy(2-hydroxy-3,1-propanediyl))ester] in dental resin composite formulations . Consequently, copolymers of urethane dimethacrylate [UDMA; 1,6-bis(methacryloxy-2-ethoxycarbonylamino)-2,4,4-trimethylhexane], a less viscous monomer with relatively high molecular weight (MW = 470) , and triethylene glycol dimethacrylate (TEGDMA) have been commonly used in commercial dental resin composites . The aim of this study was to use HP/HT polymerization to produce UDMA-TEGDMA-based RCB suitable for CAD/CAM applications and to compare their physical/mechanical properties to those of a commercially available dental CAD/CAM RCB. The null hypotheses tested were: (1) there are no differences in the physical/mechanical properties between UDMA-TEGDMA-based RCB obtained via HP/HT polymerization and a commercially available dental CAD/CAM RCB; (2) volume fraction filler ( V f ) does not affect the physical/mechanical properties of UDMA-TEGDMA-based RCB obtained via HP/HT polymerization.
2
Materials and methods
Four UDMA-based experimental RCB were manufactured in the laboratory under HP/HT conditions. As controls, a RCB manufactured under the same HP/HT conditions from a commercially available dental resin composite, Z100 (3M ESPE, St. Paul, MN, USA), and its commercially available counterpart CAD/CAM block, Paradigm MZ100 (3M ESPE, St. Paul, MN, USA), were selected for this study. Table 1 summarizes the details regarding the materials used and the group codes, while sample preparation and characterization procedures are described in the following sections.
Composite and manufacturer | Matrix b | Filler | V f | Group | Polymerization parameters |
---|---|---|---|---|---|
Experimental | 100% UDMA | BaO SiO 2 B 2 O 3 Al 2 O 3 0.7 μm and 3 μm |
60% | E60U | HP/HT |
Experimental | 2/3 UDMA 1/3 TEGDMA |
BaO SiO 2 B 2 O 3 Al 2 O 3 0.7 μm and 3 μm |
55% | E55 | HP/HT |
Experimental | 2/3 UDMA 1/3 TEGDMA |
BaO SiO 2 B 2 O 3 Al 2 O 3 0.7 μm and 3 μm |
60% | E60 | HP/HT |
Experimental | 2/3 UDMA 1/3 TEGDMA |
BaO SiO 2 B 2 O 3 Al 2 O 3 0.7 μm and 3 μm |
65% | E65 | HP/HT |
Z100 3M ESPE |
Bis-GMA TEGDMA |
ZrO 2 SiO 2 0.6 μm |
64.2% | Z100 | HP/HT |
Paradigm MZ100 3M ESPE | Bis-GMA TEGDMA |
ZrO 2 SiO 2 0.6 μm |
64.2% | P | As received CAD/CAM blocks |
a The composition of the organic matrix and filler content of P and Z was obtained from manufacturer’s data.
b Bis-GMA is bisphenol A glycol-dimethacrylate; TEGDMA is triethyleneglycol dimethacrylate; UDMA is urethanedimethacrylate.
A silanated barium alumino borosilicate glass (Dental Flass 101-S EEG1; Esschem Europe Ltd., Seaham, Germany) mixture, containing 25% (wt) particles of granulometry average size of 0.7 μm and 75% (wt) particles of granulometry average size of 3 μm, was used as filler for the experimental resin composites. As matrix, either UDMA alone (Esschem Europe Ltd., Seaham, Germany) or a mixture of 2/3 UDMA (wt) with 1/3 TEGDMA (wt) (Sigma–Aldrich, Saint-Louis, USA) was used. The incorporation of the fillers into the matrix was accomplished by using a planetary mixer (Thinky ARE-250, Thinky Corporation, Tokyo, Japan). With UDMA alone, the maximum V f achieved was 60%. Three V f (55%, 60%, and 65%) were incorporated into 2/3 UDMA–1/3 TEGDMA matrix. Neither stabilizers nor initiators were used.
Approximately 100 g of composite (experimental or Z100) was placed inside a flexible silicone tube (25 mm internal diameter). The filled tube was introduced into an autoclave (custom-built for this study) with pressure and temperature control (LabVIEW version 8.2, National Instruments, USA). A thermocouple was placed in the proximity of the sample to enable accurate monitoring and, via feed-back, control of the temperature. In the first stage, the pressure within the autoclave was increased to 300 MPa at a rate of 0.1 MPa/s, at ambient temperature. In the second stage, the temperature was increased to 200 °C at a rate of 2 °C/min. The sample was maintained at 300 MPa and 200 °C for 60 min before being cooled off and the pressure released.
One part of each HT/HP polymerized RCB and Paradigm MZ100 RCB were cut, with an Isomet saw (Buehler) under water irrigation, to produce 30 (4 mm × 2 mm × 20 mm) rectangular bars for three point bending (3 pb) flexural test. Each specimen was polished on 4000 grit SiC paper on a water-irrigated grinding wheel and its dimensions were measured with a digital caliper (Mitutoyo Co., Kawasaki, Japan) before being tested. Flexural strength ( σ f ) was determined by loading the samples in a 3 pb device (with a 16 mm span between the supports) at a cross-head speed of 1 mm/min, using a computer controlled (NexyGen ® , Lloyd, UK) Lloyd LRX (Lloyd, UK) universal testing machine. Flexural strength was calculated using the formula:
σ f = 3 F L 2 h c 2
where F is the load at fracture, L is the specimen span, h is the specimen width, and c is the specimen height.
One part of each HT/HP polymerized RCB and Paradigm MZ100 RCB were cut, with an Isomet saw under water irrigation, into eight (8 mm × 8 mm × 15 mm) rectangular bars, which were then wet ground on 800 grit SiC to obtain (6 mm × 6 mm × 6 mm × 12 mm) equilateral triangular prisms. Fracture toughness ( K IC ) was determined using the notchless triangular prism (NTP) specimen K IC test . For testing, the NTP specimen was secured into one half of the specimen holder and a sharp scalpel was used create a small (<0.1 mm-deep) defect along the loading edge before securing the second half of the specimen holder. The assembly was loaded in tension, using a computer controlled (Bluehill, Instron, USA) universal testing machine (Instron model 4301, Instron Canada Inc.), at a crosshead speed of 0.01 mm/min until crack arrest or fracture. The maximum load recorded before crack arrest or complete failure ( P max ) was used to calculate K IC in MPa m 1/2 using the following equation, proposed by Barker and adopted by ASTM standard E1304:
K I C = Y min P max D W 1 / 2
where <SPAN role=presentation tabIndex=0 id=MathJax-Element-3-Frame class=MathJax style="POSITION: relative" data-mathml='Ymin’>YminYmin
Y min
is the minimum dimensionless stress intensity coefficient (estimated at 28 for NTP samples ), D is the specimen holder diameter (12 mm), and W is the specimen holder length (10.4 mm).
Half-bars from the 3 pb tests were surface coated with a thin (∼10 nm) gold layer, in a sputter-coater (SC500, Bio Rad, UK), in order to improve reading. Surface microhardness was measured by means of a Vickers indenter (MH3, Metkon, Bursa, Turkey), under 10 N load and 20 s dwell time. Thirty determinations on five samples were made for each material.
Representative fractured NTP specimens (with K IC close to the average for the group) were sputter-coated (SC500, Bio-Rad, UK) with gold. The surface morphology was then characterized under a scanning electron microscope (SEM) (JSM-6400, JEOL Ltd., Tokyo, Japan) at low and high magnification.
The results were analyzed by one-way ANOVA test followed, if warranted, by Scheffé multiple mean comparisons ( α = 0.05), using PASW Statistics 18 (SPSS, USA). Weibull statistics parameters were calculated for σ f using the Weibull statistics option in Excel ® (Microsoft, USA). The description of the Weibull distribution is given by:
P f = 1 − e − ( σ / σ 0 ) m
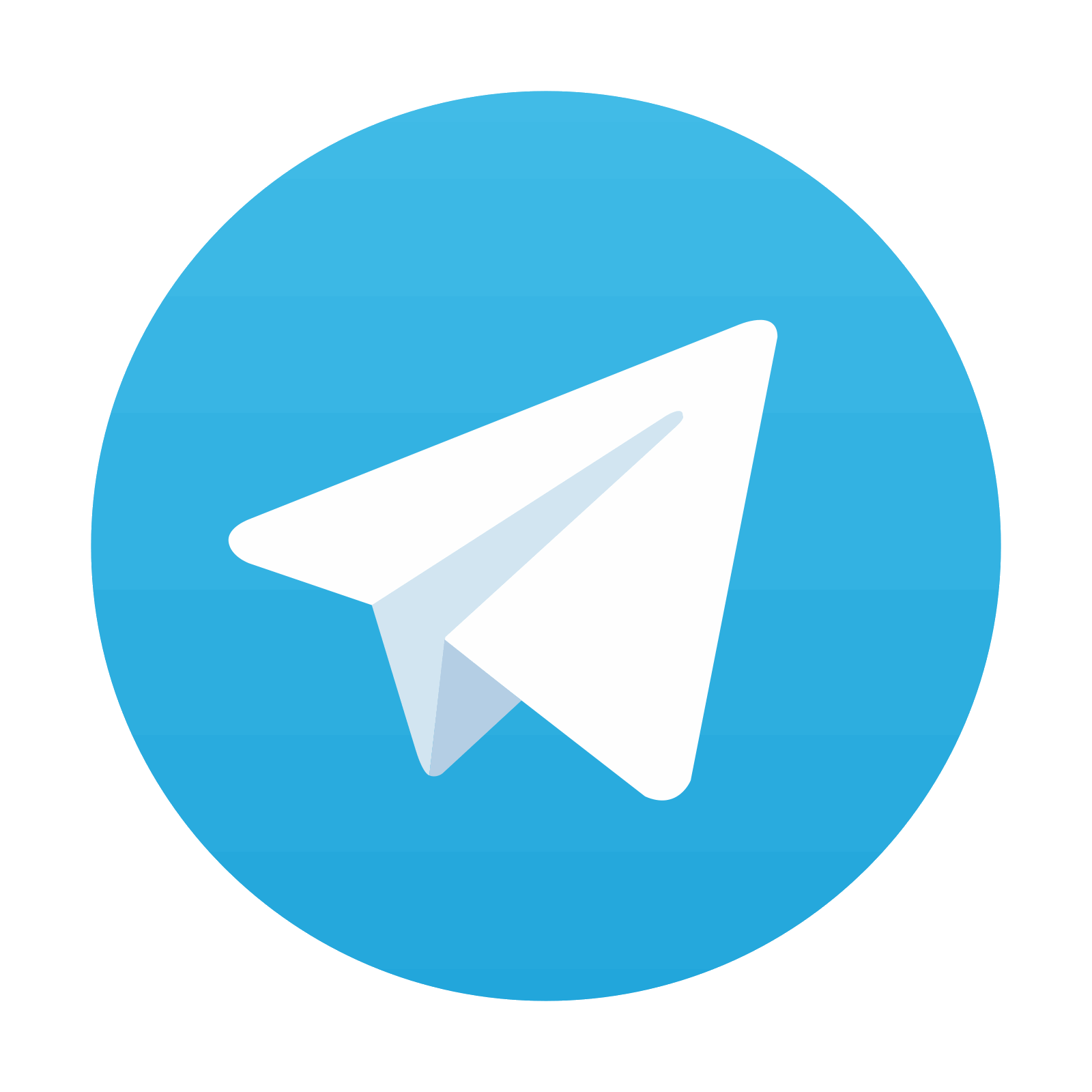
Stay updated, free dental videos. Join our Telegram channel

VIDEdental - Online dental courses
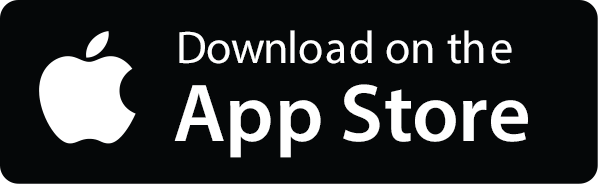
