Precious alloys are an important material group in dentistry because of their ease of use, excellent compatibility, favorable mechanical and physical properties, and application in ceramometal bonding. Although new precious alloys have been introduced in the past decades, frequently because of economic pressure, gold-based alloys remain a popular choice. Researchers have suggested that alloys should be chosen based on an understanding of the alloy system, selection of proven alloys from quality manufacturers, and consideration of the requirements of a given clinical situation.
Metals may be classified in two basic groups: ferrous and nonferrous. Ferrous metals contain iron and include metals such as steel. Nonferrous metals refer to noble metals, base metals, and light metals. Noble metals include gold and the platinum group, which contains platinum, palladium, ruthenium, rhodium, iridium, and osmium. They are characterized by good chemical stability to oxidation and resistance to corrosion and tarnish. Noble metals are often referred to as precious metals because of their relative high cost. Although silver is also considered to be a precious metal, poor resistance to corrosion and tarnish preclude it from being noble. Light metals, such as titanium, are characterized by their low density, whereas base metals include nickel, cobalt, and other heavy metals.
Most metals used in dentistry are in the form of alloys, or mixtures of one or more metal. Alloys are advantageous compared with pure metals in physical and mechanical properties because of engineering the optimum influence from each constituent. For example, pure gold is ductile, malleable, and soft, which is not desirable for prosthetic applications such as crowns. Introduction of additional metals into the gold increases the usefulness by altering the properties of the alloy through creation of solid solutions, precipitates, and multiple phases or by controlling grain size . The addition of only 10% copper to gold results in a fourfold increase in tensile strength and similar increase in hardness . The amount of gold in an alloy may be expressed by the number of carats or fineness of gold ( Table 1 ). Pure gold is defined as 24 carat or 1000 fine. For dental alloys, the American Dental Association has classified the types of metal alloys based on noble metal content. In 2003, the Council for Scientific Affairs revised the classification to include titanium in a separate category because of its extensive usage and similar properties with noble metals ( Table 2 ) .
Weight % gold | Carat | Fineness |
---|---|---|
100 | 24 | 1000 |
75 | 18 | 750 |
58 | 14 | 583 |
42 | 10 | 420 |
Class | Required noble content (%) | Required gold content (%) | Required titanium content (%) |
---|---|---|---|
High noble alloys | ≥60 | ≥40 | |
Titanium and titanium alloys | ≥85 | ||
Noble alloys | ≥25 | ||
Predominantly base metals | ≥25 |
Precious alloys in dentistry are most commonly used in the form of castings. In 1907, Taggart developed a process to cast metals using the lost-wax technique. The development of investment materials in the 1930s that matched the thermal expansion of the investment to that of the metal during the casting process significantly improved accuracy . Gold alloys dominated the precious metal use in dentistry before the deregulation of gold prices on the open market in the late 1960s. During the next three decades, numerous alloys were introduced as lower cost substitutes for gold alloys. Current precious alloys most commonly use gold with various alloying elements, however, including palladium, platinum, silver, and copper, with combinations resulting in differing properties. Wataha noted that the development of dental alloys have been influenced not only by economic factors but also by the need for improved physical and mechanical properties and concerns regarding corrosion and biocompatibility.
Casting alloys have been classified further by their yield strength and percent elongation in the American National Standards Institute/American Dental Association Specification No. 5 ( Table 3 ) . Casting alloys are designated as Type 1, 2, 3, or 4, with each alloy type recommended for specific usage. Type 3 castings are most commonly used in current dental practice. Types 1 and 2 offer limited resistance to oral forces, such as localized wear, but allow burnishability to mechanically improve the fit of a casting at the margin. Leinfelder noted that type 3 castings also provide burnishability by heat softening after soaking for 10 to 15 minutes at 700°C followed by immediate quenching. The soft alloy can be burnished. After the burnishing procedure, the alloy is hardened by heating to 450°C for 30 minutes, cooling to 250 °C, and quenching to improve the its hardness and wear resistance.
Type | Designation | Minimum 0.2% yield strength | Minimum elongation (annealed) (%) | Recommended usage for castings |
---|---|---|---|---|
1 | Low strength | 80 MPa | 18 | Light stress (eg, inlays) |
2 | Medium strength | 180 MPa | 12 | Moderate stress (eg, inlays and onlays) |
3 | High strength | 240 MPa | 12 | High stress (eg, onlays, pontics, full crowns, short-span fixed partial dentures) |
4 | Extra high strength | 300 MPa | 10 | High stress and thin cross-sections (eg, bars, thin veneer crowns, long-span fixed partial dentures, removable partial dentures) |
Metallic elements in dental alloys
Metals commonly found in current dental casting alloys are shown in Table 4 . Most precious dental alloys have two or three major elemental constituents with the addition of minor elements to influence specific properties, such as the melting range, grain formation, or resistance to corrosion. Gold is a major constituent of most precious dental alloys. Pure gold is the most ductile and malleable of all metals. It is resistant to corrosion and surface tarnish, which results in its noble status. These properties led to the use of gold as a direct filling material known as gold foil. Gold is yellow in color and is relatively insoluble in acids, with the exception of aqua regia, which is a combination of hydrochloric and nitric acids. Gold is dense and provides excellent castability, and it has a relatively low melting point. It is highly conductive and has an elastic modulus and hardness similar to enamel, which results in a desirable wear coupled with teeth.
Element | Atomic mass | Melting point (°C) | Density (g/cm 2 ) | Comment |
---|---|---|---|---|
Gold (Au) | 196.97 | 1064 | 19.32 | Noble, precious |
Palladium (Pd) | 106.42 | 1554 | 12.02 | Noble, precious |
Platinum (Pt) | 195.08 | 1772 | 21.45 | Noble, precious |
Iridum (Ir) | 192.22 | 2410 | 22.65 | Noble, precious |
Ruthenium (Ru) | 101.07 | 2310 | 12.48 | Noble, precious |
Rhodium (Rh) | 102.91 | 1966 | 12.41 | Noble, precious |
Silver (Ag) | 107.87 | 962 | 10.49 | Base, precious |
Copper (Cu) | 63.55 | 1083 | 8.92 | Base |
Titanium (Ti) | 47.87 | 1668 | 4.51 | Light |
Palladium is a common constituent in many precious dental alloys. This metal was popularized as a low-cost substitute to gold; however, market fluctuations have dramatically increased the cost. Palladium is white in color and has a density approximately 60% that of gold. Palladium has a higher melting temperature than gold but may absorb hydrogen gas when heated, resulting in undesirable properties. Palladium has the unusual property of absorbing nearly 900 times its volume of hydrogen gas and is used in industry as a means of purifying hydrogen.
Platinum is a bright white metal characterized by high hardness and density. Platinum has a high melting point and resists oxidation at high temperatures. In foil form, it is used as a substrate for porcelain densification because it has a coefficient of thermal expansion similar to porcelain and a melting temperature higher than the porcelain sintering temperature. When alloyed with metals that have a lower melting temperature, such as gold, the resultant alloy may be compatible with ceramometal bonding. The high hardness imparts excellent resistance to wear and is a common constituent in precision prosthetic attachments. Although noble alloys generally have desirable biocompatibility , some reports have implicated platinum, along with palladium, in undesired biologic responses, such as hypersensitivity . The evidence strongly supports the continued use of both metals in dentistry, however.
The remaining noble elements are less common metals in precious dental alloys but impart important properties to enhance the alloy’s usefulness. Because of high melting temperatures, small amounts of iridium and ruthenium act as centers for nucleation and growth to reduce grain size when cooling after a casting procedure. Small grains are beneficial in improving mechanical properties of the alloy. These noble metals also are sometimes added to improve corrosion resistance to base metal dental alloys . Rhodium and osmium have limited use in dentistry.
Silver is a common constituent in numerous dental alloys. Although some classify silver as precious or semi-precious because of financial value, it is not considered noble. Silver has a low melting temperature and readily uptakes oxygen, which makes it difficult to cast without porosity. Silver is reactive with sulfides, halides, and phosphates, which results in a surface tarnish. Silver forms solid solutions with gold and palladium, which improves the shortcomings of the pure metal for corrosion resistance and castability. Silver has been considered a whitening element for the color of dental alloys. Some silver alloys used for ceramometal bonding, especially with palladium, are considered to “green” porcelains, however, which results in a more yellowish appearance. At high temperature, silver diffuses into the porcelain, where it is reduced to form a colloidal metallic silver that results in a color change.
Numerous nonnoble elements are also common in precious dental alloys. Copper is present in many casting alloys, in which it forms solid solutions with gold and palladium to strengthen the alloy. Tin, indium, iron, zinc, and gallium are also common in small concentrations. Tin hardens platinum and palladium but may make the resultant alloy too brittle if used in too great a quantity. Zinc helps bind oxygen in the molten alloy but has minimal concentration in the final casting because of its low density and leaves most of the zinc in the casting “button.” Because of its low melting point and high chemical activity, zinc is also a common element in many dental solders. Indium has been used as an oxygen scavenger and to “yellow” the alloy. Indium, tin, and gallium are used to enhance surface oxide formation necessary for ceramometal bonding.
Precious alloys for dental applications
Evaluation of precious alloys available to the dental market suggests a multitude of elemental combinations available for selection . Examples of high noble and noble alloy compositions and properties are shown in Tables 5 and 6 , respectively. If the alloy is intended for ceramometal bonding, the melting range must be higher than the porcelain firing temperatures to prevent distortion of the casting. The melting range describes the temperatures for the liquidus and solidus for a given composition. Constituents such as platinum and palladium are commonly used to counter the relatively low melting temperature of gold. Small amounts of high-temperature constituents, such as iridium, do not significantly influence the melting range of the alloy but affect the grain formation and resultant properties. The casting temperature is typically 50° to 100°C higher than the liquidus temperature and varies according to manufacturer recommendations. The investment materials must be compatible with the casting temperature used and the thermal expansion of the alloy.
%Au | %Pd | %Pt | %Ag | %Cu | %Other | |
---|---|---|---|---|---|---|
High noble | ||||||
Au-Pt-Pd-Ag | 78.00 | 12.00 | 6.00 | 1.20 | 1 Fe; <1 In, Sn, Ir | |
Au-Cu-Ag-Pd I | 77.00 | 1.00 | 13.54 | 7.95 | <1 Zn, Ir | |
Au-Cu-Ag-Pd II | 60.00 | 3.75 | 26.70 | 8.80 | <1 Zn, In, Ir | |
Au-Pt-Pd | 86.00 | 1.95 | 10.00 | 2 In; <1 Ir | ||
Au-Pd-Ag-In | 40.00 | 37.40 | 15.00 | 6 In; 1.5 Ga; < 1 Ir | ||
Noble | ||||||
Au-Cu-Ag-Pd III | 46.00 | 6.00 | 39.50 | 7.49 | 1 Zn; <1 Ir | |
Pd-Cu-Ga | 75.90 | 10.00 | 6.5 Ga; 7 In; <1 Ru | |||
Ag-Pd | 53.42 | 38.90 | 7 Sn; <1 Ga, Ru, Rh | |||
Pd-Ga-Au | 2.00 | 85.00 | 10 Ga; 1.1 In; <1 Ag, Ru | |||
Pd-Ag-Au | 6.00 | 75.00 | 6.50 | 6 In; 6 Ga; <1 Ru |
Melting range (°C) | Density (g/cc) | Heat treatment | Vicker’s hardness (VHN) | Ultimate tensile strength (MPa) | Modulus of elasticity (GPa) | Percent elongation | Coefficient of thermal expansion (α x 10 −6 /°C) | |
---|---|---|---|---|---|---|---|---|
High Noble | ||||||||
Au-Pd-Pt-Ag | 1170–1300 | 17.2 | C | 255 | 689 | 103.4 | 4% | 14.3 @ 500 °C |
Au-Cu-Ag-Pd I | 920–980 | 15.8 | A | 145 | 434 | 82.7 | 44% | |
Au-Cu-Ag-Pd II | 900–990 | 14.2 | B | 165/245 | 455/689 | −/96.5 | 45%/20% | |
Au-Pt-Pd | 1060–1230 | 18.7 | C | 190 | 586 | 82.7 | 6% | 14.5 @ 500 °C |
Au-Ag-Pd-In | 1175–1280 | 13.0 | C | 265 | 586 | 124 | 17% | 14.2 @ 500 °C |
Noble | ||||||||
Au-Cu-Ag-Pd III | 900–1000 | 13.1 | B | 170/250 | 448/689 | −/103.4 | 40%/20% | |
Pd-Cu-Ga | 1120–1270 | 10.5 | C | 365 | 1068 | 131 | 7% | 13.8 @ 500 °C |
Ag-Pd | 1190–1300 | 10.9 | C | 220 | 689 | 115.8 | 25% | 15.1 @ 500 °C |
Pd-Ga-Au | 1105–1330 | 10.9 | C | 285 | 717 | 131 | 25% | 13.9 @ 500 °C |
Pd-Ag-Au | 1130–1340 | 11.0 | C | 250 | 827 | 131 | 35% | 14.0 @ 500 °C |
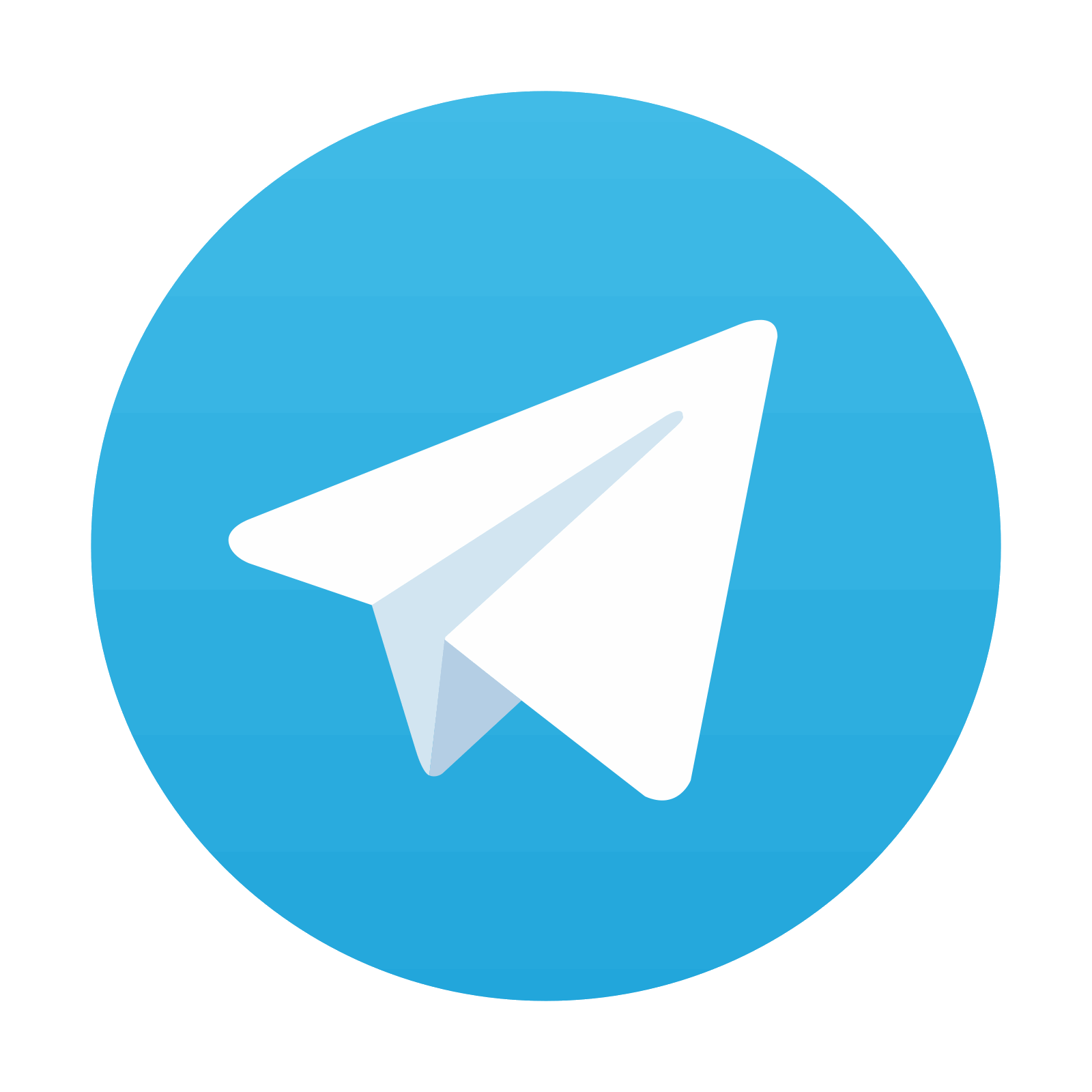
Stay updated, free dental videos. Join our Telegram channel

VIDEdental - Online dental courses
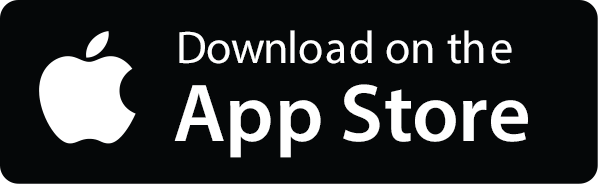

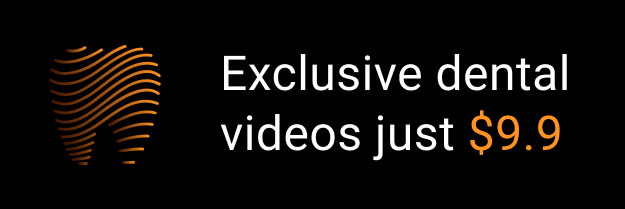