Abstract
Objective
The objective of the present study was to determine the hardness and adhesion strength at the porcelain to alloy interface.
Methods
15 bi-layer porcelain veneered Co–Cr specimens of each alloy group [cast, powder metallurgy (PM), CAD/CAM(CC)] were manufactured. 12 bi-layered specimens were tested using four-point bend strain energy release rate adhesion test. One before and after porcelain firing specimen of each alloy group were nano-indented at the bulk and metal-porcelain interface to determine the mechanical properties. Electron backscatter diffraction was used to determine the microstructure and phase of the indented areas.
Results
The results obtained from the four-point bend strain energy release rate test indicated highest adhesion energy of 92.15 J/m 2 observed in the CC produced Co–Cr alloy. This was followed by the PM alloy with an adhesion energy of 62.24 J/m 2 and cast alloy with an adhesion energy of 42.83 J/m 2 . All comparisons of adhesion energy between the three alloys were found to be statistically significant (p < .05). Nano-indentation test indicated higher hardness values of 4.6–6.1 GPa at the metal-porcelain interface compared to the bulk, which had hardness values of 3.1–3.9 GPa.
Significance
The adhesion of the alloy to porcelain was found to be inversely related to the hardness of the interfacial layer at the alloy surface. Lower interfacial hardness was found to be accompanied with higher adhesion energy due to the additional plastic energy consumed during crack propagation along the more ductile interface region of the alloy.
1
Introduction
Traditional methods of manufacturing cobalt–chromium (Co–Cr) dental alloy restorations were based on the lost-wax casting technique of metal sculpturing. This technique became immensely popular for manufacturing both full metal and porcelain-fused-to-metal restorations due to the ability to create highly precise substructures: a key factor dictating the success of dental restorations. Unfortunately as cast alloys generally have large grain structures, due to their relatively unrestricted grain growth , therefore, exhibit little benefit from Hall–Petch grain boundary strengthening . These alloys are also known to consist of a mixture of face-centered cubic (fcc) and hexagonal close-packed (hcp) crystal structures, the resulting fraction of each is dependent on the thermodynamic equilibrium associated with composition and the cooling conditions . The significance of the two crystal structures has an important role in dictating the properties of the material. The crystal structure fcc is general known to exhibit ductile properties due to the greater availability of slip systems, while in contrast, the hcp structure exhibits more brittle like properties due to the limited availability of slip systems.
For the purposes of dental restorations, preservation of the ductile properties is preferable in terms of both laboratory and clinical manipulation of the alloy and the resistance to catastrophic failures in vivo. Under normal cooling conditions during casting, the relatively sluggish nature of the fcc-hcp transformation in Co–Cr alloys results in the fcc structure being predominantly retained despite the fact that hcp is the equilibrium stable phase at room temperature . However, this equilibrium has been shown to be shifted in favor of the hcp phase by subsequent conventional porcelain firing temperatures of ∼900 °C as established in the previous study by Li et al. . These porcelain firings not only alter the bulk phase composition but also develop a fine grained hcp layer near the surface of the alloy. Consequently, the properties at the alloy surface can be substantially modified, which can also be detrimental to the adhesion between the alloy and porcelain. Traditionally, adhesion strength is known to be dependent on the mechanical and chemical bonding as well as the thermal compatibility between the alloy and porcelain. The mechanical bond is enhanced by roughening the surface of the alloy to allow porcelain to flow into the surface crevices and interlock during sintering. Chemical bonding is established through the production of a metal oxide layer on the alloy surface that is subsequently partially dissolved within the porcelain layer during sintering. Thermal compatibility is the close matching of the coefficient of thermal expansion (CTE) between the porcelain and alloy so that the residual stresses, which occur on cooling, are not excessively high that it would result in spontaneous fracture or chipping. This maximum allowable difference in CTE between the alloy and porcelain to minimise failure is generally agreed by the scientific community to be within the range of ±1 × 10 −6 K −1 . More recently developed techniques such as computer aided design/manufacturing (CC) and powder metallurgy (PM) produced Co–Cr alloys allow the manufacturer to refine the microstructure of the alloy without it being lost in the melting and casting process: thus enabling further enhancement of various properties. An investigation by Li et al. on the microstructure and phases of these modern Co–Cr alloys observed that the fcc phase stability after porcelain firing heat treatment was much higher in fine grained Co–Cr alloys. This in turn, significantly reduced the depth and fcc-hcp phase transformation of the interfacial layer after porcelain firing cycles as shown in Fig. 1 . Although the theoretical significance of the hcp and fcc phase as well as the microstructural refinement has been thoroughly discussed, mechanical and adhesion testing investigation is still required to validate the above phenomenon and implications.

Previous literature studies, which have evaluated the localized properties of dental Co–Cr alloys, have relied on Vickers indentation methodologies . Although this technique is valid and extremely useful in many circumstances, the limitations of the pyramidal design restricts the accuracy required for certain applications . This is especially important in the case of interfacial analysis as the thickness of the layer as well as the bulk average grain sizes are typically only micrometers. Therefore, the use of instrumented nano-indentation with a Berkovich indenter is much more appropriate for mapping such changes since the sharper tip and non-reliance on optical measurements permits greater accuracy to be achieved.
The objectives of the present study were to: (1) identify and compare the hardness properties of the bulk and metal-porcelain interface of selected Co–Cr dental alloys, and (2) determine the effect of the interfacial layer on the adhesion between the alloy and porcelain using four-point bend strain energy release rate test.
The hypothesis of this research is that fcc to hcp transformation near the surface will result in the hardness at the metal-porcelain interface to be higher than the bulk of the Co–Cr alloy and that the harder interfacial layer developed will have a detrimental effect on the adhesion between the alloy and porcelain.
2
Materials and methods
Bi-layered specimens were manufactured from cast (LOT: 20111115, DentaNEM, Wieland Pforzheim, Germany), PM (LOT: 1301001, Sintron, Amanngirrbach, Germany) and CC (LOT: 408699, Remanium Star MD I, Dentaurum, Germany) Co–Cr alloys as directed by the manufacturers’ instructions. The adhesion of porcelain to these specimens along with their mechanical, chemical and phase relationships were evaluated using four-point bend strain energy release rate and nano-indentation tests, as well as SEM and EBSD analysis. A leucite-containing porcelain (Vita VMK Master, Vita, Germany) was used for the veneering layer.
2.1
Preparation of the substrate material
Rectangular plates (n = 18) 30 × 8.0 × 1.5 mm of each Co–Cr alloy were fabricated using different techniques. The cast alloy was manufactured by first embedding pre-cut thermoforming discs (Erkodent, Germany) with a phosphate-bonded investment. The investment was subsequently pre-heated to 950 °C for 1 h and cast using an induction heating machine (Fornax, BEGO, USA) at temperatures above the melting point of this alloy of ∼1490 °C. The investment and cast alloy was then left to air cool to room temperature before subsequent removal. The PM produced alloy was dry sectioned to the required dimensions using a low-speed precision cutting machine (DTQ-5, Weiyi, China) in its pre-sintered state. The CC alloy was cut to the required dimensions using an electrical discharge machine. All specimens were ground with 320 grit size SiC (SiC paper, Struers, Denmark) paper to achieving exact dimensions, flat surface finish and in the case of the CC alloy, removal of any surface contamination from the electrical discharge cutting process. Finally, the surfaces were impacted with airborne particle abrasion using 110 μm Al 2 O 3 particles at 2 bar pressure.
2.2
Preparation of the veneering porcelain
The layering of the veneering porcelain was in accordance to the manufacturers’ recommendations with the exception that an extended drying time of 12 min was used for dentin 1 and dentin 2 firing to compensate for the large volume of porcelain . Specimens were treated to a total of 5 porcelain firings cycles. A detailed summary of the firing and specimen group specifications is listed in Table 1 . The veneering porcelain was layered to a thickness of 1.5 mm with the assistance of prefabricated templates.
Firing programs | Sintering temperature (°C) | Heating rate (°C/min) | Hold time (min) | Cast, PM, CC Co–Cr alloy | |
---|---|---|---|---|---|
Control | OD5 | ||||
Wash opaque | 960 | 80 | 1 | – | 1 |
Opaque 2 | 950 | 80 | 1 | – | 1 |
Dentin 1 | 930 | 55 | 1 | – | 1 |
Dentin 2 | 920 | 55 | 1 | – | 2 |
Total firings | – | – | – | 0 | 5 |
2.3
Interfacial strain energy release rate test
The approach used to evaluate the adhesion energy between the porcelain and Co–Cr substructure was proposed by Charalambides et al. and later adapted by Suansuwan and Swain for testing dental materials . This approach measured the strain energy release rate of a stable crack extension along the bi-layer interface. Following Suansuwan and Swain , the bi-layered specimens (n = 12) were manufactured to a total dimension of 30 × 8 × 3 mm. with the porcelain layer of the specimen notched close to the bi-layer interface using a water-cooled diamond impregnated saw blade. A small pre-crack (<2 mm) was then initiated from the base of the notch to the bi-layer interface using a special rubber-backed jig observed under an optical microscope. The bi-layered specimens were stored in kerosene prior to testing in order to minimize the influence of water on subcritical crack growth .
Testing of the bi-layer specimens were performed on a Universal Testing Machine (Instron 3369) using a 4-point bending jig ( Fig 2 ) at a crosshead speed of 0.05 mm/min and the data recorded using the BlueHill 3 software. An increasing load was applied onto the specimen until it reached a critical value, which initiates stable crack propagation along the interface as indicated by a plateau on a force-displacement curve. The mean value of the plateau load was used to calculate the strain energy release rate (G) using the formula:
G = η [ P 2 I 2 ( 1 − v m 2 ) ] E m b 2 h 3
where G is the strain energy release rate, l is the distance between the inner and outer roller on the same side, p is the load necessary to stably propagate the crack at the plateau region, E m and E p is the elastic modulus of the Co–Cr and porcelain respectively, v m and v p is the Poisson’s ratio of the Co–Cr and porcelain respectively, b is the width of the specimen (E p, v m and v p values obtained from the paper by Swain whereas E m was obtained from the nano-indentation data), h m and h p is the thickness of the Co–Cr and porcelain respectively and h is the total thickness of the specimen. The non-dimensional parameter η includes all geometric parameters and is calculated using the following formula:
η = ( 3 2 ) [ 1 ( h m h ) 3 − λ { ( h p h ) 3 + λ ( h m h ) 3 + 3 λ ( h p h m h 2 ) [ h p h + λ h m h ] − 1 } ]
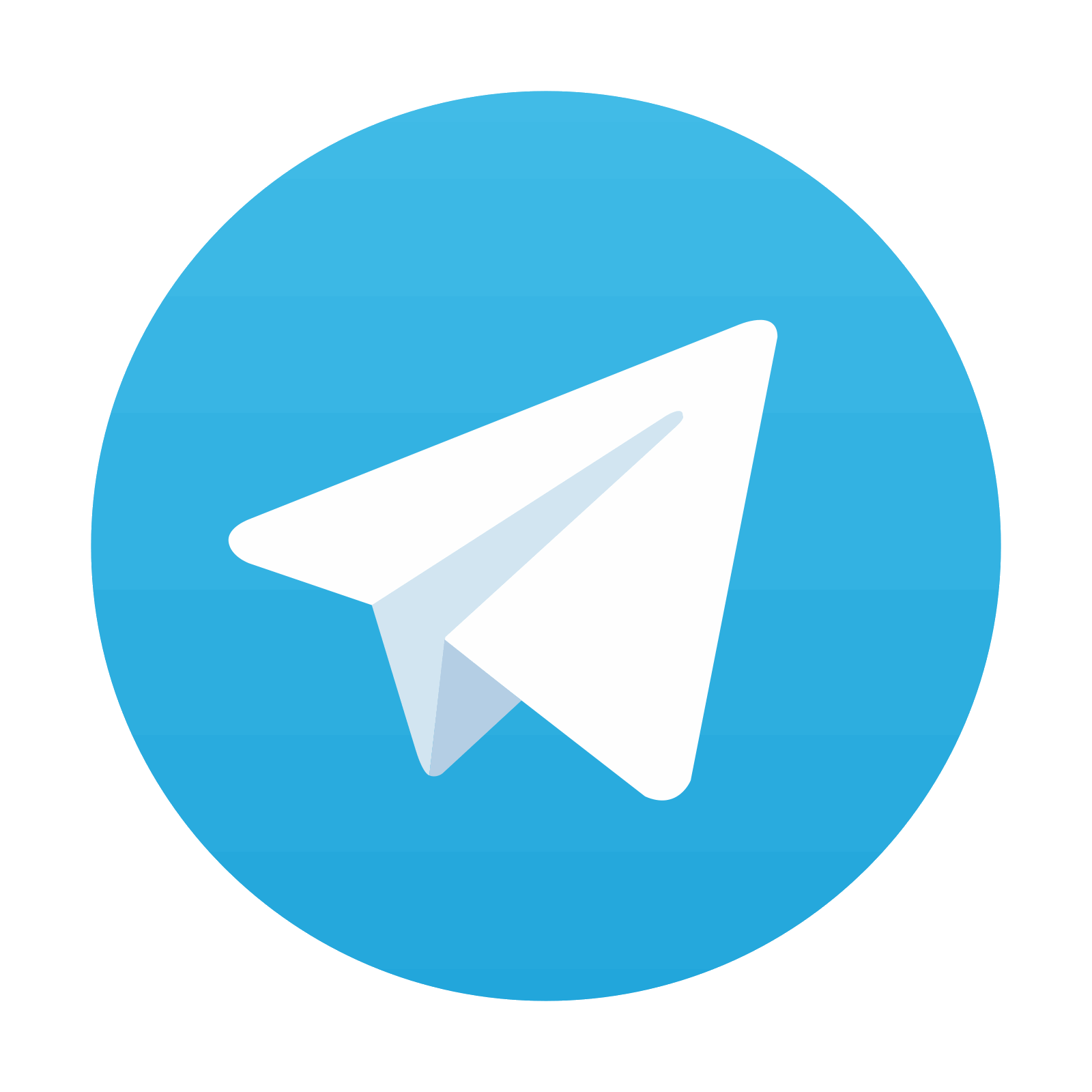
Stay updated, free dental videos. Join our Telegram channel

VIDEdental - Online dental courses
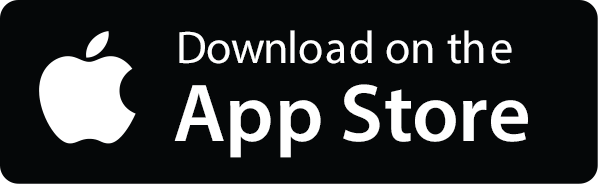
