Introduction
There is continuing interest in an esthetic, effective labial archwire. In this study, we evaluated the potential of new, high-strength polyphenylene polymers to fill this need.
Methods
Polyphenylene (Primospire, Solvay Advanced Polymers, Alpharetta, Ga) polymer was extruded into wires with clinically relevant round and rectangular cross sections. Tensile, flexure, spring-back, stress-relaxation, and formability characteristics were assessed. Arch forms and secondary shapes were formed.
Results
Smooth wires with consistent cross-sectional dimensions, high spring-back, and good ductility were produced. Forces delivered were generally similar to typical beta-titanium and nickel-titanium wires of somewhat smaller cross sections. The polyphenylene wire did experience stress relaxation for up to 75 hours. The force magnitudes place polyphenylene wires in the category of an alignment or leveling wire. High formability allowed shape bending similar to that associated with stainless steel wires.
Conclusions
Polyphenylene polymers could serve as esthetic orthodontic archwires; further study is warranted.
There have been a number of approaches for esthetic orthodontic treatment, including aligners, lingual orthodontics, and esthetic labial orthodontics. Much progress has been made in the development of esthetic clear and translucent brackets for labial orthodontics ; however, the most effective wires continue to be fabricated from efficient, albeit unesthetic, metal alloys.
A number of alternatives have been explored to create an esthetic archwire that would allow efficient orthodontic treatment from the labial aspect. Metal wires, particularly nickel-titanium (NiTi) alloys, have been coated with either tooth-colored polymers or inorganic materials. Although these wires might be considered more esthetic, a number of problems have been identified. They lack the translucency and ideally the transparency of an esthetic arch. Furthermore, the outer coating can wear or peel, and bending of the wire is limited. The small cross sections needed for an orthodontic wire limit the extent of any coating. Since the outer positions are the farthest from the neutral axis, they are biomechanically the most important and therefore should have optimal properties.
It would seem that a solid polymeric wire would offer excellent esthetics, since it could be either transparent or translucent. Until recently, the available polymers simply lacked the properties necessary for an orthodontic wire. They lacked sufficient rigidity and strength; in engineering terms, the modulus of elasticity and yield strength were too low. In addition, stress relaxation and low hardness limited their efficiency, leading to exaggerated permanent deformation and possible frictional resistance.
Are there methods to enhance the properties of a polymeric wire so that it could be suitable as an active wire? One possibility is fiber reinforcement. With long fibers, such as glass, it is possible to increase rigidity and strength adequately. Unfortunately, a fiber-reinforced composite (FRC) wire in typical configurations is brittle and lacks ductility, and would be susceptible to breakage in the mouth, particularly in small flexible cross sections. Because the reinforcing fibers are parallel to the long axis, FRC wires are anisotropic, possessing lower rigidity and strength in the direction of torsion or torque. Bending of FRC wires also could be complicated because of the need to maintain proper, uniform orientation of the fibers.
The approach presented here is the use of a new advanced polyphenylene polymer that has enhanced rigidity, strength, and hardness. It obtains these higher properties by a mechanism of molecular-level reinforcement. Polyphenylenes also have increased hardness and resistance to stress relaxation. Along with good formability, torque control, and translucency, this thermoplastic polymer might be an efficient and esthetic labial orthodontic wire.
Typical thermoplastic polymers are amorphous, high molecular weight, long chain macromolecules. Bulk mechanical properties, such as modulus of elasticity and yield strength, are largely determined by the molecular-level rigidity of the polymer chains. When the polymer chains can easily rotate, bend, or slide past each other, bulk stiffness and strength are lower, but ductility is increased. Reducing polymer chain mobility and increasing chain rigidity results in higher bulk stiffness and strength, but lower ductility and often processing and forming into complex or narrow shapes are more difficult.
Within the past 15 years, it was discovered that inserting flexible segments into an otherwise rigid all-phenylene backbone can produce a high-strength, yet processable, polymer. Various strategies are possible, such as the structure shown in Figure 1 . The pendant R groups and the nonrigid segments [-A-]m (both representing a wide range of possible organic groups) disrupt the excessive alignment and rigidity of the covalently linked phenylene groups, leading to a high-strength, yet processable, polymer. Generically, these polymers are called polyphenylenes. Because the blocks of phenylene groups in the backbone chain are rigid, these polymers are also called self-reinforced polymers (SRP).
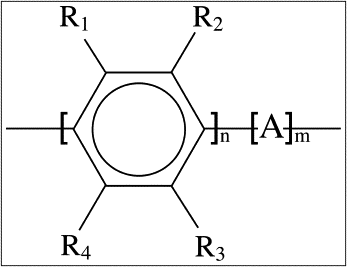
The manufacturer’s (Solvay Advanced Polymers, Alpharetta, Ga) range of values for modulus and strength for polyphenylenes are 5.5 to 8.3 GPa and 152 to 207 MPa, respectively. This is more than double the properties of polycarbonate and even one third greater than high-performance polymers such as poly(ether ether ketone). Although the properties of polyphenylenes are still considerably below those of the beta-titanium or NiTi alloys, our premise is that polyphenylene’s properties are sufficient for use as orthodontic archwires. However, polyphenylenes have not been fabricated into wires nor have such wires been evaluated for clinically relevant properties. Furthermore, the manufacturer’s values are based on large, standardized size test specimens, which are not necessarily predictive of the clinical performance of small-diameter, short-span orthodontic designs. We demonstrate that polyphenylenes can be extruded into wires with clinically relevant cross sections and report clinically important mechanical properties of polyphenylene orthodontic wires.
Material and methods
A self-reinforced polyphenylene thermoplastic (Primospire PR-250, Solvay Advanced Polymers) was obtained in pellet form. Primospire is an amorphous polymer that is translucent with a slight yellow tint. The pellets were melt extruded by using specially designed profile dies to achieve wires with clinically relevant cross sections of either 0.021 × 0.030-in rectangular or 0.020-in round (Zeus Industrial Products, Orangeburg, SC). A total of approximately 200 feet of wire were extruded. The wire was visually examined, and cross-sectional dimensions were inspected continuously along the length. At several locations, samples were cut and examined with optical and scanning electron microscopy to evaluate the outer surface and cross-sectional shape.
Samples of the extruded wire were cut into lengths of approximately 6 inches for tensile testing. The cross-sectional dimensions at 3 locations along the length of each tensile specimen were measured with a digital micrometer (Starrett, Athol, Mass), and the means for each sample were used in calculating the mechanical properties. At least 5 samples each of the round and rectangular wires were independently placed into smooth-faced platens in a universal testing instrument (Mini Bionix II, MTS, Eden Prairie, Minn) equipped with a 5-kN force sensor. Through preliminary trials, the tightness of the grips was determined that produced full stress-strain curves with neither slippage nor premature failure. A 1-in gauge length strain extensometer was carefully attached, and the grips were separated at a rate of 1 mm per minute until sample failure. Elastic modulus, yield strength, ultimate strength, elongation at yield, and elongation at break were calculated (TestWorks 4 software, MTS) for each sample.
The flexure properties of the 0.021 × 0.030-in and 0.020-in poyphenylene and 0.016-in beta-titanium (TMA, Ormco, Glendora, Calif) wires were evaluated with a free-end cantilever procedure described earlier. The beta-titanium wire was included for comparison because it has low wire stiffness for a metal wire and no superelastic or temperature-related behavior. Wire samples approximately 30 mm long were secured in a vise grip and deflected against a fixed post positioned to provide a clinically relevant span length of 5 mm. The moment was recorded as the angular deflection was increased in 0.5° increments until the yield region was reached, and then increased in 1.0° increments to a maximum deflection of 15°. The sample was returned to zero moment. Five samples of each wire were tested. The mean moment-angular deflection curves were smoothed and plotted (Prism 5.0a, GraphPad Software, La Jolla, Calif).
An unusual characteristic of a polymeric orthodontic wire would be its potential to experience time-dependent stress relaxation and creep. Stress relaxation would result in lower forces over time even at a constant deflection. As an initial assessment of this property, tensile samples of the 0.021 × 0.030-in rectangular wires were positioned in the testing instrument with the 1-in gauge length extensometer as described above. The samples were placed under tensile loads equal to 20%, 40%, 60%, and 80% of the yield stress. The extension (strain) was held constant, and the decreasing stress was continuously monitored until it reached an approximately constant value, which occurred in 24 to 75 hours.
Because of its time-dependent characteristics, the spring-back of a polymeric wire depends on the test method. As an initial screening of spring-back properties, the following method was developed. Three sets of bracket pairs were bonded to acrylic sheets with an interbracket distance of 7 mm and vertical displacements of 1, 2, and 3 mm. Samples of the polyphenylene wire, approximately 38 mm long, were secured in the left-most bracket of each bracket pair by using an orthodontic O-ring. The top edge of the sample was aligned with a fixed background reference grid. Each wire was loaded into the right-most bracket of the pair and left in place for 10 seconds. The wire was then released from the right-most bracket, and the deformation was recorded with the reference grid to the nearest 0.25 mm. Nine samples were measured at each initial deflection. The means and standard deviations were calculated.
The formability of both round and rectangular polyphenylene wires was evaluated at room temperature and after heating. At room temperature, wires were formed by using the rounded face of a bird-beak pliers to create various bends and loop shapes. In the heat-formed method, the wire was held in a stream of warm air (model 6966C, Ungar/Apex, Sparks, Md) until it just began to sag; then it was immediately removed from the heat and formed by hand into representative orthodontic configurations. Additionally, typical arch shapes were made by pulling the heated wire under tension around a mandrel (Zeus Industrial Products).
Results
Wires with the target rectangular and round cross sections were successfully extruded. The lengths were straight with no apparent curvature or twist. Scanning electron microscopy ( Fig 2 ) showed well-defined cross-sectional shapes with no distortion. The small radii in the corners of the rectangular wire were designed into the extrusion die. Surfaces were smooth with no visible defects ( Fig 2 , C ). The cross-sectional dimensions varied by less than 5% for both rectangular and round geometries.
Tensile properties of the round and rectangular extruded wires are reported in Table I . The manufacturer’s values for the same grade of polyphenylene, but obtained with the injection molded, larger size standard ASTM D638 test specimens, are also shown. The measured mean and standard deviation (SD) moduli of 5.57 (0.43) and 5.03 (0.40) GPa for the round and rectangular wires, respectively, were consistent with the manufacturer’s value of 5.90 GPa. The ultimate tensile strengths of 142.9 to 170.6 MPa were close to the expected value of 159 MPa. The relatively high values for elongation at yield, 3.1% (0.4%) and 3.5% (0.7%), and elongation at break, 4.5% (1.5%) and 7.0% (4.5%), are consistent with the expected ductile, high toughness characteristics of the polymer.
Nominal wire profile | Modulus (GPa) |
Yield strength (MPa) |
Ultimate strength (MPa) |
Elongation@ yield (%) | Elongation @ break (%) |
---|---|---|---|---|---|
0.020-in round | 5.57 | 160.1 | 170.6 | 3.1 | 4.5 |
(0.43) | (10.6) | (18.0) | (0.4) | (1.5) | |
0.021× 0.030-in rectangular | 5.03 | 138.4 | 142.9 | 3.5 | 7.0 |
(0.40) | (15.5) | (10.9) | (0.7) | (4.5) | |
Manufacturer’s data (ASTM D638) | 5.90 | N/A | 159 | 4.8 | 6.0-10.0 |
The mean moment vs angular deflection curves for the 0.021 × 0.030-in rectangular and the 0.020-in round polyphenylene wires are shown in Figure 3 . The polyphenylene wires exhibited typical flexure characteristics with linear, yield, and plateau regions. The 0.021 × 0.030-in wires had a mean (SD) stiffness of 191.7 (2.2) cN-mm per degree and generated a maximum moment of 1713 (95) cN-mm. After being deflected approximately 15°, the wire experienced about 2.5° of permanent deformation. The 0.020-in round wire had a similarly shaped flexure curve and generated a maximum moment of 767 (238) cN-mm with a stiffness of 77.7 (5.3) cN-mm per degree. After being deflected approximately 15°, the wire experienced about 0.0° of permanent deformation.
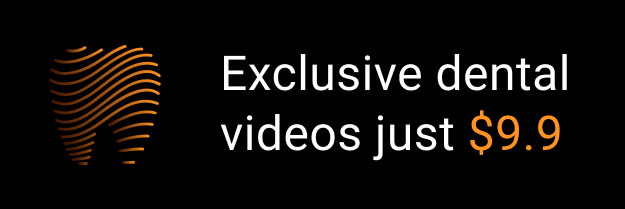