Abstract
Objectives
To investigate a set of resin-composites and the effect of their composition on polymerization shrinkage strain and strain kinetics, shrinkage stress and the apparent elastic modulus.
Methods
Eighteen commercially available resin-composites were investigated. Three specimens ( n = 3) were made per material and light-cured with an LED unit (1200 mW/cm 2 ) for 20 s. The bonded-disk method was used to measure the shrinkage strain and Bioman shrinkage stress instrument was used to measure shrinkage stress. The shrinkage strain kinetics at 23 °C was monitored for 60 min. Maximum strain and stress was evaluated at 60 min. The shrinkage strain rate was calculated using numerical differentiation.
Results
The shrinkage strain values ranged from 1.83 (0.09) % for Tetric Evoceram (TEC) to 4.68 (0.04) % for Beautifil flow plus (BFP). The shrinkage strain rate ranged from 0.11 (0.01%s −1 ) for Gaenial posterior (GA-P) to 0.59 (0.07) %s −1 for BFP. Shrinkage stress values ranged from 3.94 (0.40) MPa for TET to 10.45 (0.41) MPa for BFP. The apparent elastic modulus ranged from 153.56 (18.7) MPa for Ever X posterior (EVX) to 277.34 (25.5) MPa for Grandio SO heavy flow (GSO).
Significance
The nature of the monomer system determines the amount of the bulk contraction that occurs during polymerization and the resultant stress. Higher values of shrinkage strain and stress were demonstrated by the investigated flowable materials. The bulk-fill materials showed comparable result when compared to the traditional resin-composites.
1
Introduction
Polymerization shrinkage of resin-composite occurs due to the conversion of the monomer molecules in to polymer structure which is accomplished by replacing the van der waals spaces by covalent bonds and consequently reducing the free volume . Despite the numerous advances in improving the bonding mechanism between the tooth structure and the resin-composite material, the failure of the bonding interface remains . The defects that develop in the interfacial bonding are due to the polymerization stresses generated during the restorative placement procedure and later due to the functional thermal and mechanical stresses . With the introduction of the bulk-fill group of materials the effect of polymerization shrinkage is highlighted as these materials are recommended to be placed in 4 mm increments.
Several studies demonstrated the direct relationship between the stress generated during polymerization and the integrity of the restoration-tooth margins . The polymerization process is accompanied by volumetric shrinkage of the material and its magnitude depends on the composition of the material . The amount of the polymerization stress generated is the product of many controlling factors including the C-factor, the compliance of the dental substrate and the material properties .
The viscoelastic behavior of the material has an important role in the capacity of the material to flow during early stages of polymerization and on the elastic modulus development. Viscoelastic behavior of the material is another important factor that affects the polymerization stress development . The viscoelasticity of the material and the volumetric shrinkage are both controlled by similar factors that make it difficult to isolate their effect on the polymerization shrinkage stress development . In addition, the stress development is affected by the reaction kinetics as a higher polymerization rate is accompanied by high polymerization stress . The material plastic deformation is time dependent phenomenon in which the material needs time to flow to accommodate the contraction stresses before the development of the modulus of elasticity .
Different methods have been proposed to reduce polymerization shrinkage and its resultant stress. These methods include incremental placement of the restoration, soft start curing technique, the use of stress absorbing cavity liners and modification in the material composition . Polymerization shrinkage for monomers such as Bis-GMA and TEGDMA had been found to be substantially higher than the typically filled composites . There is a direct relation between the increase in filler loading and the reduction in polymerization shrinkage . The incorporation of pre-polymerized resin fillers (organic fillers) decreases the volume fraction of the polymerizable resin and increases the filler volume fraction resulting in reduction of the polymerization shrinkage. Flowable (low-viscosity) resin-composites have been reported with higher polymerization shrinkage as a result of reduced filler loading . Nano-composites are a class of composite that was introduced for its improved mechanical properties, esthetic outcomes and reduced polymerization shrinkage .
Several modifications have been made to the monomer systems of resin-composite materials to reduce the polymerization shrinkage. Many low shrinkage resin-composites have been commercially introduced to the market. Among these is the introduction of a high molecular based monomer with initially low double bond concentration (Dimer acid based monomer) an example of these materials is N’Durance from Septodont, France. It demonstrated lower polymerization shrinkage and higher degree of conversion when compared with conventional monomers as Bis-GMA and UDMA .
SDR ® bulk-fill material has been introduced with modified UDMA by introducing photo-active groups to the monomer. It has been shown that this material resulted in lower shrinkage stress compared to other flowable and conventional composites . TCD-DI-HEA was also introduced as a low shrinking monomer and it was incorporated in Venus diamond material from Haeraus Kulzer GmbH, Germany. This low viscosity monomer has a rigid back bone that results in low shrinking behavior . In addition, ethoxylated bisphenol A dimethacrylate (Bis-EMA) which is a Bis-GMA analog with lower viscosity due to the absence of hydroxyl groups from its structure was introduced for a similar purpose. It has been found to provide lower polymerization shrinkage when combined with other conventional monomers such as UDMA and Bis-GMA .
In this study eighteen commercially available materials from different classes were investigated for their shrinkage strain, shrinkage stain kinetics, stress and modulus of elasticity. The null hypothesis was that there are no significant differences in the results between the bulk-fill materials and the other investigated materials.
2
Materials and methods
Eighteen commercially available resin-composites with different viscosities were investigated. The materials represented a wide range of dental applications. Materials’ details and manufacturers’ specifications are shown in Table 1 .
Material | Filler loading (vol.%) | Resin matrix | Manufacturer | Type |
---|---|---|---|---|
Gradia direct posterior (GDP) | 65 | UDMA, DM | GC Corporation, Tokyo, Japan | Micro-hybrid conventional |
G-aenial posterior (GA-P) | 65 | UDMA, dimethacrylate | GC Corporation, Tokyo, Japan | Micro-hybrid conventional |
G-aenial anterior (GA-A) | 63 | UDMA, dimethacrylate | GC Corporation, Tokyo, Japan | Micro-hybrid conventional |
G-aenial universal flow (GA-F) | 50 | UDMA Bis-MePP, TEGMA |
GC Corporation, Tokyo, Japan | Nano-hybrid flowable |
Ever X posterior (EVX) | 57 | Bis-GMA, TEGDMA, PMMA | GC Corporation, Tokyo, Japan | Fiber reinforced Packable BF |
Venus diamond (VD) | 64 | TCD-DI-HEA, UDMA | Heraeus Kulzer GmbH, Germany | Nano-hybrid conventional |
Venus bulk fill (V-BF) | 38 | UDMA, BIS-EMA | Heraeus Kulzer GmbH, Germany | Nano-hybrid flowable BF |
Tetric Evoceram (TEC) | 53–55 | Bis-GMA, UDMA, BIS-EMA | Ivoclar Vivadent, Schaan, Liechtenstein | Nano-hybrid conventional |
Tetric Evoceram bulk fill (TEC-BF) | 60–61 | Bis-GMA, UDMA, BIS-EMA | Ivoclar Vivadent, Schaan, Liechtenstein | Nano-hybrid Packable BF |
Smart dentin replacement (SDR ® ) | 44 | Modified UDMA, BIS-EMA, TEGDMA | Dentsply Caulk, Milford, Delaware, USA | Fluoride-containing flowable BF |
Spectrum TPH (STPH) | 57 | BisGMA, Bis-EMA & TEGDMA | Dentsply Caulk, Milford, Delaware, USA | Micro-hybrid conventional |
Filtek supreme XTE (FSE) | 55.6 | BisGMA, Bis-EMA, UDMA, TEGDMA, PEGDMA | 3M ESPE, USA | Nano-hybrid flowable |
Estelite flow quick (EFQ) | 53 | Bis-MPEPP, TEGDM, UDMA | Tokuyama Dental Corporation, Tokyo, Japan | Micro-hybrid flowable |
Beautifil flow plus (BFP) | 47 | Bis-GMA, TEGDM | Shofu INC, Japan | Nano-hybrid Fluoride-containing Flowable |
Grandio SO heavy flow (GSO) | 68 | Bis-GMA, Bis-EMA, TEGDMA | Voco, Cuxhaven, Germany | Nano-hybrid flowable |
X-tra base (XB) | 58 | MMA, Bis-EMA | Voco, Cuxhaven, Germany | Hybrid flowable BF |
N’Durance (ND) | 65 | Bis-GMA, UDMA, DDCDMA | Septodont, France | Nano-hybrid packable |
Premise (PR) | 69 | BIS-EMA, TEGDMA | Kerr Corporation, Orange, USA | Nano-hybrid conventional |
2.1
Shrinkage strain measurement
The ‘bonded-disk’ method described by Watts and Marouf in 2000 was used to determine shrinkage-strain . Resin-composite paste specimens of circular disk geometry were prepared within 15 mm diameter brass rings of square cross section fixed on a 3.0 mm thick glass slab. The upper surface of the glass slab was lightly grit-blasted with alumina powder to promote bonding of the composite to the glass surface. The specimen was 1.0 mm in height and 8 mm in width. The disks were positioned centrally within the brass rings, leaving a free space around the disk. A flexible 22 mm × 22 mm size and 0.1 mm thick glass cover slip (VWR International Ltd., borosilicate glass, thickness No.0) was placed in close contact above the specimen, supported laterally by the brass ring. A glass plate was used during the preparation of the specimens, in conjunction with the cover slips, to compress the composite pastes into circular disks. Resin-composite specimens of circular disk geometry were of 0.12 g to obtain the required diameter of 8 mm. This value was obtained through pilot testing of different resin-composite weights and direct measurement of the resultant disk.
The bonded-disk arrangement is placed upon a custom jig. The jig was made of an aluminum stand with a horizontal ‘stage’ for specimen placement with two stainless steel clips to hold the glass slab. Mounted into the stage was a brass ring. The brass ring had a hollow center of 10 mm diameter through which the tip of a light curing unit was fixed in place. A clamp arrangement was attached to the stage to hold the uni-axial LVDT (linear variable displacement transducer) measuring system and allowed for vertical adjustment of its position. The LVDT measuring system, of 8 g active mass, was positioned centrally onto the cover slip. Specimens were light-cured by 20 s direct irradiation from beneath the glass slab at 1200 mW/cm 2 using an Elipar S10 LED curing light from 3M ESPE, and at an initial room temperature of 23 ± 1 °C. The light output was measured using a laboratory grade NIST-referenced USB-4000 spectrometer (MARC Resin Calibrator v.3, Blue-light analytics Inc, Halifax, NS, Canada). The measurements were made continuously every second for 60 min from irradiation time.
Three specimens were made for each material. The signal from the LVDT was transmitted to a computer by a signal conditioning unit (E 309, RDP Electronics Ltd., Wolverhampton, UK) and a high resolution analog to digital converter and data logger (PICO ADC-20 Data logger, Pico Technology Ltd, Cambs., UK). Following mechanical equilibration, data were captured for 60 min from 20 s prior to commencement of irradiation with sampling every second.
The data were then processed using SigmaPlot (SigmaPlot 2008 ver. 11, SPSS Inc., IL, USA). Using the following equation (Eq. (1) ) the strain values were calculated. For each composite the maximum recorded shrinkage strain of each of the three runs was recorded and the mean and standard deviation were calculated. In which ɛ is the strain, Δ L is the change in length and L 0 is the original length.
2.2
Shrinkage stress measurement
Shrinkage-stress was measured using The Bioman shrinkage-stress instrument that was designed and constructed at the University of Manchester . Components were bolted to a 2 cm thick stainless steel base-plate. Support frame was used to vertically mount the components of the instrument. A cantilever load-cell of 500 kg capacity was fitted with a rigid integral clamp at the compliant end (the free end) of the cantilever to securely hold a circular steel rod with 10 mm diameter and 22 mm long vertically and perpendicular to the load-cell axis. The bottom of the rod was sand-blasted to aid in composite retention and formed the top surface of the specimen chamber. The lower surface of the specimen chamber is made by a 3 mm thick glass plate that was also sand blasted for the same purpose. The glass plate was held rigidly with special clamp during the measurements. The specimen chamber gap was set with the aid of a feeler gauge to 0.8 mm giving a configuration-factor of 6.25 according to the following equation where d and h are the diameter and thickness of the disk specimen (Eq. (2) )
C = d 2 h
The specimen was irradiated from the bottom surface through the glass plate for 20 s at 1200 mW/cm 2 using an Elipar S10 LED curing light from 3M ESPE, and at an initial room temperature of 23 ± 1 °C. During polymerization, the stresses produced within the specimen caused a slight displacement of the free end of the load-cell. The load-signal from the cantilever cell was amplified by a wide-range strain indicator (Model 3800, Vishay, Measurements Group, Rayleigh, NC, USA). The signals produced by the displacement were continually sent to a computer via a signal conditioning unit and a high resolution analog to digital converter and data logger (ADC-20 multi-channel data acquisition unit and PicoLog software; Picotech, Cambridge, UK).
Three specimens were made from each material. The material required to make 0.8 mm thickness specimen of 10 mm diameter was 0.14 g that was determined by pilot mass testing and direct measurement of the disks. The unset material was placed on the glass plate which was then positioned and stabilized by the adjustment screw. The material then was pressed between the glass slab and the steel rod and left for one minute to allow relaxation of any internal stresses produced during manipulation. Data were recorded for 60 min from 20 s prior to commencement of irradiation, with sampling each second.
The data were then processed using SigmaPlot (SigmaPlot 2008 ver. 11, SPSS Inc., IL, USA). The stress value in MPa is then obtained from the recorded load divided by the specimen disk area. For each material the maximum recorded shrinkage stress of each of the three runs was recorded and the mean and standard deviation were calculated.
σ = Force Area
The shrinkage strain rate was calculated by numerical differentiation of the shrinkage strain data with respect to time. This was made for the first 200 s of the data from the three runs, using MATLAB (ver. 7.6, MathWorks Inc., MI, USA).
The modulus of elasticity was calculated from the measured polymerization shrinkage strain ( ɛ ) and stress ( σ ) following Eq. (4) .
2.3
Statistical analysis
A statistical package (SPSS ver. 16.0, SPSS Inc., IL, USA) was used to analyze the data. The shrinkage strain, shrinkage strain rate, shrinkage stress and modulus of elasticity results were analyzed using one-way ANOVA. Data were tested for equal variances using the homogeneity test ( p < 0.05). Equal variances were assumed, thus multiple comparisons using a Tukey post hoc test were conducted to establish homogenous subsets. Linear regression analyzes were made to correlate the measured properties.
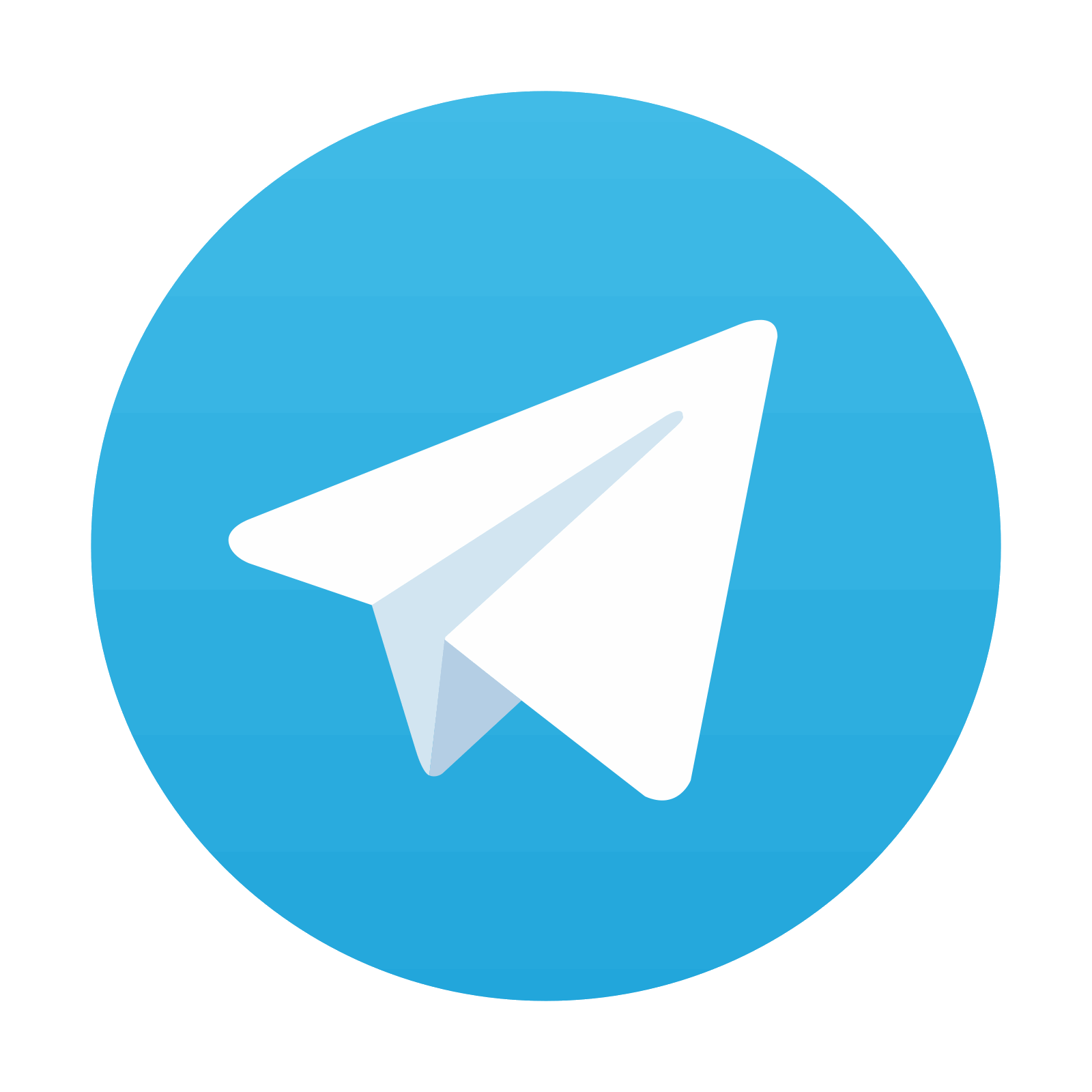
Stay updated, free dental videos. Join our Telegram channel

VIDEdental - Online dental courses
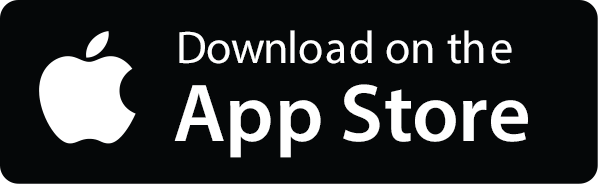
