Abstract
Objectives
To evaluate “low-shrink” composites in terms of polymerization kinetics, stress development and mechanical properties.
Methods
“Low-shrink” materials (Kalore/KAL, N’Durance/NDUR, and Filtek P90/P90) and one control (Esthet X HD/EHD) were tested. Polymerization stress (PS) was measured using the Instron 5565 tensometer. Volumetric shrinkage (VS) was determined by the ACTA linometer. Elastic modulus (E) and flexural strength (FS) were obtained by a three-point bending test. Degree of conversion (DC) and polymerization rate (Rp) were determined by NIR spectroscopy (6165 cm −1 for dimethacrylates; 4156 and 4071 cm −1 for P90). Photopolymerization was performed at 740 mW/cm 2 × 27 s. Glass transition temperature ( T g ), degree of heterogeneity and crosslink density were obtained in a DMA for the fully cured specimens. Analysis of extracts was done by 1 H NMR. Data were analyzed with one-way ANOVA/Tukey’s test ( α = 0.05).
Results
The control presented the highest shrinkage and T g . P90 showed the highest modulus, and NDUR demonstrated the highest conversion. The polymerization rates were comparable for all materials. NDUR and KAL had the highest and the lowest network homogeneity, respectively. The multifunctional P90 had the highest crosslink density, with no difference between other composites. The control had the greatest stress development, similar to NDUR. Crosslinking density and polymer network homogeneity were influenced by degree of conversion and monomer structure.
Significance
Not all “low-shrink” composites reduced polymerization stress. P90 and NDUR had no leachable monomers, which was also a function of high crosslinking (P90) and high conversion (NDUR).
1
Introduction
The choice of materials for direct restorations in posterior teeth has changed significantly over the past thirty years and currently there is a growing demand for esthetic composite restorations . However, there is still a major limitation regarding the longevity and clinical performance of these restorations compared to amalgam. Polymeric materials potentially undergo hydrolytic/esterase degradation and are subjected to stresses induced by the polymerization process. These two limitations have been related to loss of interfacial seal , microleakage , postoperative sensitivity, secondary caries and wear . The latter is considered to be one of the main reasons for the replacement of composite restorations .
One factor that has received considerable attention in recent years is the volumetric shrinkage, which is about 2–4% for the dimethacrylate-based materials . Composite shrinkage is restricted by the adhesion of the material to the cavity walls, thus generating stresses which generates stress at the interface . Shrinkage is related directly to the polymeric degree of conversion , and consequently, to the stresses distributed throughout the adhesive interface . High values of conversion also contribute to increased elastic modulus and crosslinking density which are also directly related to stress . Importantly, the filler also influences the magnitude of shrinkage and the elastic modulus and thus contributes to the stress development . Considering the complex interaction between all of these factors, it is not surprising that studies to date have been unable to determine the most important factor in stress development . Additional complications arise when comparisons are made among commercial materials, since their compositions are proprietary, and therefore cannot be controlled by the operator .
Some clinical strategies are used in an attempt to minimize polymerization stress, such as filling the tooth cavity in increments and/or using methods for curing with low initial irradiance. This latter measure, however, proved to be inefficient to delay the development of stiffness (elastic modulus) in polymeric materials to control stress development . In turn, changes in composite formulation, both in the inorganic portion as well as in the organic matrix, were the most promising in reducing polymerization stress . For instance, dimethacrylate materials have been developed based on high molecular weight monomers . Also, materials have been introduced in the market which develop heterogeneity during the polymerization, in a controlled manner, driven by incompatibility of monomer components. This heterogeneity translates into the formation of different phases, which minimizes residual stresses in polymeric network through relaxation at the phase interface . This strategy is commonly used in the coatings and molded parts industry to reduce the effects of polymerization stress .
Examples of monomers that rely on polymerization-induced phase separation (PIPS) for heterogeneity formation as a means to reduce polymerization shrinkage are the dimethacrylate-derivatives of dimer acid , used in the commercial composite N’Durance. These monomers present high molecular weight ( Fig. 1 ) and according to manufacturer’s information, induce heterogeneity in the commercial composite. In a previously published characterization study, this material showed the highest degree of conversion and good mechanical properties . Its high degree of conversion, together with hydrophobic characteristic can reduce sorption, solubility and the potential of leachability of the non-reacted monomers .

One high molecular weight monomer called DX-511 ( Fig. 1 ), based on urethane dimethacrylate and present in the commercial composite Kalore, leads to shrinkage reduction due to the low reactive group concentration available for reaction . The commercial composite that contains this monomer has shown lower polymerization stress and shrinkage values compared with conventional composites .
One composite with a new monomer system, based on silorane, which is a combination of siloxane and oxirane monomers, has been proposed as another solution ( Fig. 1 ). Cationic ring-opening polymerization of this epoxy material has inherently lower volumetric shrinkage when compared to materials with vinyl monomers . Previous studies have shown a reduced stress for this material . Another advantage is promoted by the oxirane groups that are present in its molecular structure, which were stable in biological fluids tested probably due to their lack of solubility or miscibility . These groups also decrease composite sorption and solubility showing lower values than that presented by the dimethacrylate-based composite Despite the growing number of laboratory studies for silorane based material, there are still difficulties in determining its conversion .
Given the recent introduction of composites aiming at reducing polymerization stress, this study proposes to characterize the composites regarding aspects as polymerization stress and its determinants, polymer network quality and mechanical properties, compared with a conventional dimethacrylate composite as a control.
2
Materials and methods
Three composites marketed as “low-shrink” were chosen: Kalore (KAL) and N’Durance (NDUR), which are based on dimethacrylates and Filtek P90 (P90), which is based on silorane. Esthet X HD (EHD) was used as a control ( Table 1 ).
Monomer | Material (shade) | Composition | Manufacturer | Batch number | |
---|---|---|---|---|---|
Resin matrix | Filler content (vol.%) | ||||
Dimethacrylate | Esthet X HD (A2) | Bis-GMA, Bis-EMA, TEGDMA | 60 | Dentsply/Caulk, Milford, DE, USA | 329100C |
Kalore (A2) | UDMA, UDMA (DX-511), Dimethacrylate co-monomers | 69 | GC America Inc., Alsip, IL, USA | 903232 | |
N’Durance (A2) | Bis-EMA, UDMA, dimethacrylate derivatives of the dimer acids | 65 | Septodont, Louisville, CO, USA | K0611-3 | |
Silorane | Filtek P90 (A2) | Silorane, Bis-3,4-epoxycyclohexylethyl-phenyl-methylsilane | 58 | 3M ESPE, St. Paul, MN, USA | N110333 |
2.1
Polymerization stress
Polymerization stress was measured using a universal testing machine (Instron 5565, Canton, MA, USA) with poly(methyl methacrylate) rods (diameter, 5 mm; 13 or 28 mm in length) as the bonding substrate for the composite. For adhesion, the sandblasted flat surfaces rods received a layer of methyl methacrylate (JET Acrílico Auto Polimerizante, Artigos Odontológicos Clássico, São Paulo, Brazil) followed by a thin layer of unfilled resin (Silorane System Adhesive Self-etch for P90 or Scotchbond Multi-purpose Plus for the other composites, both from 3M ESPE). The rods were attached to the opposing clamps of the testing machine, with the long axis perpendicular to the load cell and the treated surfaces facing each other. The longer rod (28 mm) was attached to the upper clamp. The shorter rod (13 mm) was clamped to a custom holder attached to the lower member of the testing machine. The light activation was carried out through the lower rod, so the surface opposite to the bonding surface was mirror-polished to allow for the highest possible light transmission during photoactivation . Composite ( n = 5) was inserted into 1 mm gap between the rods. An extensometer (0.1 μm resolution) was attached to them to provide feedback to the testing machine in order to keep the height constant. As the composite polymerized, shrinkage force was recorded for 10 min from the beginning of photoactivation (740 mW/cm 2 × 27 s – Bluephase G2, Ivoclar Vivadent, Schaan, Liechtenstein). Nominal stress was calculated by dividing the maximum force value by the cross-section of the rod.
2.2
Volumetric shrinkage
Cylindrical specimens ( n = 3, Ø = 6 mm, h = 1.5 mm) were placed on an aluminum disk sitting on top of the linear variable displacement transducer of a linometer (ACTA, Netherlands) and a glass slide was placed over the specimen through which light exposure took place. Volumetric shrinkage ( n = 3) was followed for 10 min from the beginning of photoactivation (740 mW/cm 2 × 27 s – Bluephase G2).
2.3
Elastic modulus and flexural strength
Bar-shaped specimens (n = 10, 10 mm × 2 mm × 1 mm) were photoactivated with one irradiation (740 mW/cm 2 × 27 s) on the top side using a 11 mm diameter light guide, without the need for overlapping exposures. After that, the specimens were stored dry in the dark for 24 h. Then, they were subjected to three-point bending in a universal testing machine (Instron 5565) at a crosshead speed of 0.5 mm/min with an 8 mm span between the supports. Data from the initial linear portion of the load vs. displacement curve were used to calculate the flexural modulus according to the formula :
E = C L 3 4 w h 3 d × 10 − 1
where C is the load at fracture (N), corresponding to the displacement d , L is the distance between the supports, w is the width and h is the height of the specimen (mm). The maximum value before rupture was used to calculate the flexural strength using the formula :
F S = 3 C L 2 w h 2
where C is the load at fracture (N), L is the distance between supports, w is the width and h is the height of the specimen (mm).
2.4
Degree of conversion and polymerization kinetics
Conversion and polymerization kinetics were monitored by near-infrared in a spectrometer (Nicolet 6700 FTIR, Thermo Scientific, Pittsburgh, PA, USA) equipped with an extended KBr beam splitter and an InGaAs detector. Specimens were placed in silicone rubber molds ( n = 3; Ø = 6.5 mm; h = 0.8 mm) sandwiched between glass slides and then photoactivated with 740 mW/cm 2 × 27 s (Bluephase G2). FTIR spectra (2 scans per spectrum, 4 cm −1 resolution, with collection speed of two spectra/s) were collected during 5 min. For methacrylate-based materials, the peak area corresponding to vinyl stretching (6165 cm −1 ) was used . For P90, peaks near the epoxy region were selected: 4156 cm −1 , which had been previously reported and 4071 cm −1 . The latter was identified in a separate study, whose results will be reported in a different paper. In brief, different commercially available epoxy monomers were characterized by mid- and near-IR. These monomers included species that are part of the P90 composition in addition to the silorane, according to the manufacturer’s Material Safety Data Sheet. The two peaks were selected since not all epoxy monomers included in the composition show absorption on the same region of the IR spectrum. According to previous studies , the near IR technique used here does not require the use of reference peaks, since the monomer and subsequent polymer spectra are collected on the same specimen, with the same cross-sectional area. Therefore, conversion (DC) was calculated from the ratio of peak area in monomeric and polymeric states , according to the following formula:
DC = 1 − area monomer area polymer × 100
The polymerization rate was calculated as the first derivative of the conversion vs. time curve . Kinetic parameters as maximum rate of polymerization Rp max (in %/s), degree of conversion at Rp max (DC at Rp max in %) and rate of polymerization at 2–5% conversion (Rp at DC 2–5% in %/s) were determined.
2.5
Dynamic mechanical analysis
A dynamic mechanical analyzer (DMA, 8000, Perkin Elmer, Massachusetts, USA) with the temperature scan performed over the range of −50 °C to 200 °C with a ramping rate of 3 °C per min in tension mode (sinusoidal stress at 1 Hz) was used. Samples ( n = 3, 15 mm × 3 mm × 1 mm) were irradiated with 1200 mW/cm 2 × 30 s (Bluephase G2), stored for 7 days and kept at 170 °C for 15 h (Isotemp oven Model Vacuum 282a, Fisher Scientific, Pittsburgh, PA, USA). This protocol was performed to ensure the maximum achievable degree of conversion and prevent any further polymerization from occurring during the heating cycle required for the dynamic mechanical testing. The glass transition temperature ( T g ) was measured as the peak value of tan delta curve . The loss and storage modulus, as well as the loss tangent (tan δ , ratio of loss to storage modulus), were recorded as a function of temperature . The width at half height of the tan delta curve (WHH) reflects the heterogeneity of the polymer network . Crosslink density was estimated through storage modulus in the rubbery plateau applying the equation:
v = E ′ 3 d R T
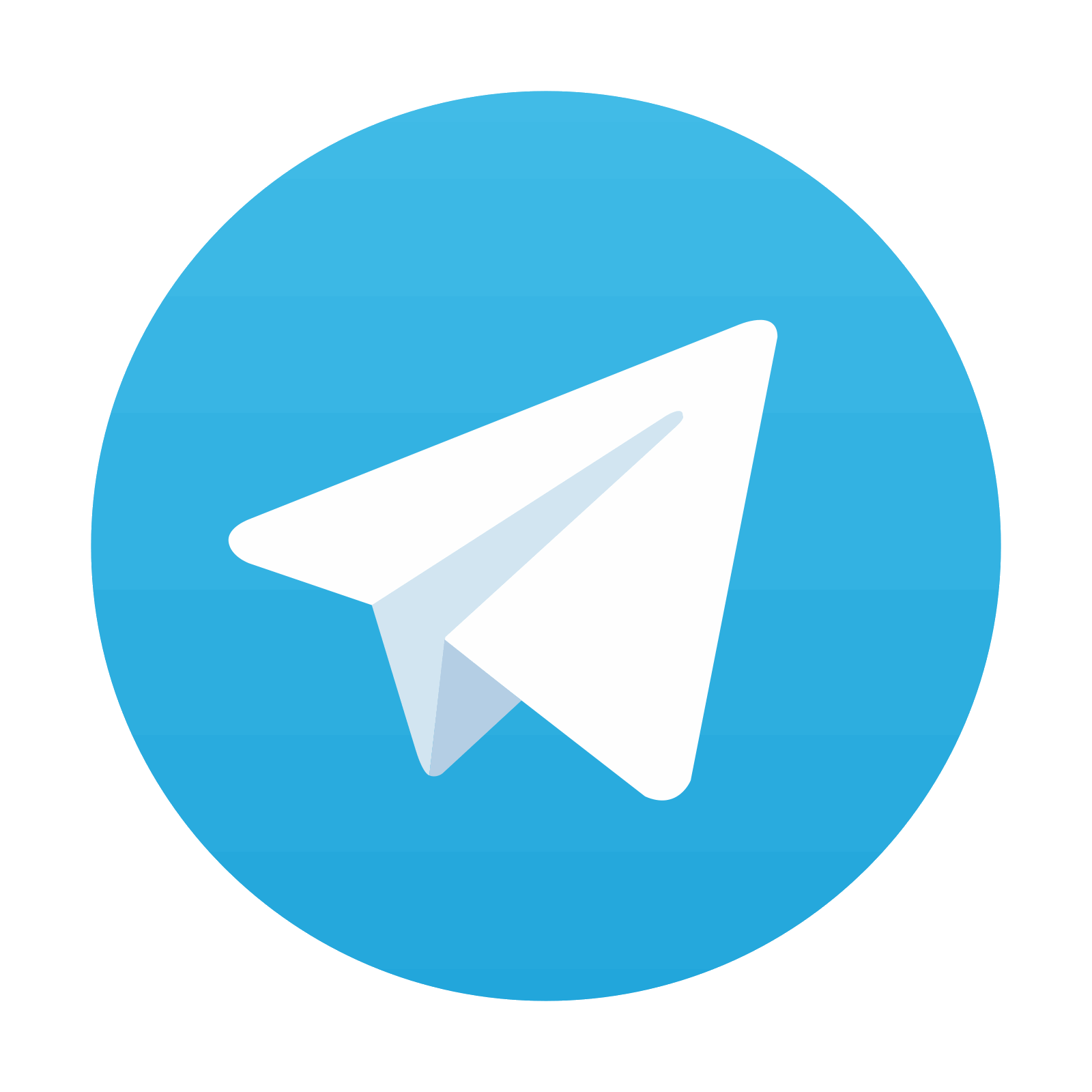
Stay updated, free dental videos. Join our Telegram channel

VIDEdental - Online dental courses
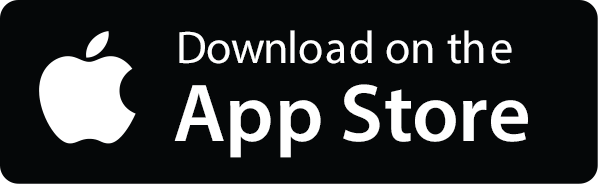
