Highlights
- •
The energetic approach methodology is used to estimate the K C of bovine enamel.
- •
Alternative energetic methodology has been developed to estimate K C of the enamel.
- •
The method is based on the contact stiffness evolution during the cracking process.
- •
The K C values are compared with those obtained using others methodologies.
Abstract
Objectives
There are many works that have attempted to estimate the fracture toughness of enamel by indentation techniques using equations whose success in determining the actual value of fracture toughness, rely on a particular three-dimensional pattern consisting of cracks growing from the edges of the indentation. Recently, an alternative methodology based on an energetic approach has been developed to estimate the fracture toughness of coatings by depth sensing indentation that is not less affected by the cracks pattern generated. In this work, the energetic approach to indentation fracture toughness of bovine enamel is presented and compared with those toughness values obtained using the traditional expressions reported in the literature.
Methods
Indentation tests were carried out using a diamond Berkovich indenter onto the enamel surface of eight incisors from bovines of two years old. A continuous stiffness measurement methodology was used with a frequency of 45 Hz and displacement amplitude of 2 nm up to a maximum penetration depth of 2000 nm.
Results
The results showed that some modifications in the energetic methodology should be performed in order to apply it successfully.
Significance
The fracture toughness values obtained using the traditional equation and applying the energetic methodology, were significantly different, although the values were within the range obtained by other authors.
1
Introduction
Enamel is the hardest and stiffest tissue of mammals. Its microstructure consists of rods encapsulated by thin protein rich sheaths that are arranged parallel in a direction perpendicular to the dentino-enamel junction (DEJ) from dentin to the outer enamel surface.
The enamel microstructure of all mammals appears to be very similar on a histochemical and anatomic basis .
Numerous methods have been employed to experimentally measure the fracture toughness ( K C ) of the enamel. The determination of K C by indentation techniques is based on measuring the size of cracks induced in a material during indentation . Several expressions are available to determine K C by this technique, depending on the indenter geometry and crack morphology .
In 1987, Laugier determined that:
K C = x V a l 1 / 2 E H 2 / 3 P c 3 / 2
where a is the half-diagonal of the indentation impression, l is the crack length measured from the indentation imprint edge, and c is the crack length measured from the center of the indentation imprint. Additionally, Laugier showed that the radial and half-penny models make similar predictions when x v = 0.015.
The Eq. (1) was developed for ceramic materials and for the symmetrical Vickers indentations. Some efforts have been made to obtain similar equation but properly modified for Berkovich indentations. Ouchterlony investigated the nature of the radial cracking and determined a modification factor for stress intensity factor to account the number of radial cracks, n , formed.
k 1 = n / 2 1 + ( n / 2 π ) sin ( 2 π / n )
The ratio of k 1 values for n = 4 (Vickers indenter) and n = 3 (Berkovich indenter) is 1.073. Introducing this ratio in Eq. (1) , a modified Laugier model adapted to Berkovich indentations can be obtained, according to Eq. (3) .
K C = 1.073 ⋅ x V a l 1 / 2 E H 2 / 3 P c 3 / 2
However, these equations provide an actual value of the fracture toughness by indentation only if a particular pattern of cracks running from the indentation imprint vertices is obtained.
This work has been developed to answer the question about what happens if cracks generated by indentation do not show that characteristic pattern. Concerning this point, there could be an alternative methodology based on the energy released during cracking process, as a measurement of the fracture toughness . This energetic method calculates the fracture toughness comparing the area limiting by the load-displacement curve with crack generation and the hypothetical one if cracking does not occur .
For a thin film, Li et al. determined the critical stress-intensity factor assuming Mode I:
K I C = E ( 1 − v 2 ) 2 π C R ⋅ Δ U t 1 / 2
where E is the elastic modulus and ν is the Poisson’s ratio, K IC is the indentation fracture toughness of the material, Δ U is a measure of the fracture energy, t is the film thickness and 2 πC R is the crack length. The product of 2 πC R and t gives the cracked area, A crack , therefore, Eq. (4) can be written as:
K I C = E ( 1 − ν 2 ) ⋅ Δ U A c r a c k 1 / 2
Eq. (5) allows obtaining fracture toughness values from indentation tests. Under this testing method, the strain energy, Δ U , can be obtained from the area between the hypothetical loading curve if no cracking exists and the experimental one. This equation can be used even when a particular cracks pattern is not obtained, although the critical point of Eq. (5) is to determine again the cracked area.
Hereafter, Eq. (3) is referred in this paper as the traditional equation to distinguish the equation using the energetic methodology, Eq. (5) .
There is some scatter in the literature about the actual fracture toughness of enamel . Hassan et al. have reported values of human tooth enamel, using a Vickers indenter, in the range of 0.7–1.37 MPa m 1/2 . Xu et al. reported fracture toughness values of 0.84 MPa m 1/2 for labial human enamel also using a Vickers indenter in the same range of those determined by Padmanabhan et al. . Bajaj and Arola reported fracture toughness values for human enamel that ranged from 1.79 MPa m 1/2 to 2.37 MPa m 1/2 obtained from R -curve analysis, and Baldassarri et al. obtained values of 0.5 MPa m 1/2 and 1.3 MPa m 1/2 for transversal and midsagital enamel orientation, respectively, using a Vickers indenter on rat tooth. There are various reasons that may cause the large variation in reported fracture toughness values. The biological nature of the enamel suggests that the compositional variations among specimens could impact to the toughness values . Additionally, the microstructure orientation of enamel could also contribute to this variability .
Therefore, the aim of this study was to compare the fracture toughness values obtained from the energetic methodology using depth sensing indentation technique with those obtained applying the traditional equation based in a specific pattern of cracks.
2
Materials and methods
2.1
Preparation of specimens
Eight incisors were extracted from bovines of two years old. Teeth were cleaned and stored in artificial saliva ( Table 1 ) prior to the tests. The labial surfaces of the specimens were polished in two steps, using a mechanical grinder (Labopol-5, Struers, Copenhagen, Denmark) with polishing cloths of alumina suspension slurry of 3 μm and 0.020 μm, respectively. This polish sequence provided an average roughness lower than 20 nm. This value was checked by atomic force microscopy measurements.
Composition | g/100 g of solution |
---|---|
Sodium carboxymethyl cellulose | 1.000 |
Sorbitol | 3.000 |
Sodium chloride | 0.084 |
Potassium phosphate | 0.120 |
Calcium chloride, dihydrate | 0.015 |
Magnesium chloride, hexahydrate | 0.005 |
Dibasic sodium diphosphate | 0.034 |
Purified water | bal |
Afterwards, the specimens were kept fully hydrated in artificial saliva at room temperature before the indentation tests. The composition of saliva is detailed in Table 1 .
2.2
Indentation tests
A preliminary study of Vickers indentations on the bovine enamel was carried out, following the ASTM standard requirements. Two different maximum loads were applied: 5 N, 20 N. The time to load and the dwell time was 15 s.
Additionally, hardness and elastic modulus of bovine enamel surfaces were studied by depth sensing indentation (Nanoindenter XP-MTS System Corporation) using a Berkovich diamond indenter with a tip radius of 50 nm. A Continuous Stiffness Measurement module (CSM) was chosen. A maximum penetration depth of 300 nm was fixed for all indentation tests. Three rows of 20 indentations were performed on each sample. Each indentation was separated by 100 μm from each other. During the loading branch, continuous loading–unloading cycles with amplitude of 2 nm and a frequency of 45 Hz were superimposed. The Oliver–Pharr methodology was applied on each of these partial unloading cycles, providing values of elastic modulus ( E ), and hardness ( H ), as a continuous function of load or penetration depth. Before each batch tests, the Berkovich indenter was calibrated on a standard fused silica.
2.3
Fracture toughness analysis
Additionally, 5 indentations were done on each sample using the CSM module up to a maximum penetration depth of 2000 nm. This penetration depth was sufficient to generate a characteristic pattern of cracks, allowing us to apply Eqs. (3) and (5) . After the indentation tests, the residual imprints were observed by scanning electron microscopy (SEM) (Hitachi S-3400N) under low vacuum condition.
The fracture toughness of the enamel was determined using the traditional methodology and the energetic one. The application of each methodology has difficulties. To estimate the fracture toughness by the traditional methodology implies to obtain a characteristic pattern of cracks. This problem was overcome choosing adequate indentation test conditions. To determine the fracture toughness by the energetic methodology, it is necessary to calculate the energy released during the cracking process, Δ U . The cracking area, A crack , has to be estimated for both methodologies.
2.3.1
Determination of Δ U
The proposed procedure to calculate the energy released during the cracking process, is based on the contact stiffness variation due to cracking. Besides the cracking process, other phenomena may affect the contact stiffness during indentation, as quasi-plastic deformation phenomena associated with the movement of the water and protein phase. However, given the conditions under which the indentation tests were made, with very high strain rates, the contribution of these phenomena to the variation of the contact stiffness, measured from the elastic unloading branch of each cycle, can be considered negligible. Additionally, it is well known that using a pyramidal indenter, the ratio of the contact area to the depth of the indentation, remains constant for an increasing indenter load, i.e. the Berkovich indentation exhibits geometrical similarity. Consequently, the strain within the material is constant, independent of the penetration depth, except for very small values, where the apex radius effect is dominant. Therefore, the plasticity effects should be equally important at low or high penetrations. If at low penetration depths, a linear tendency of the contact stiffness versus square root of the contact area is obtained, any different trend observed at high depths should not be a consequence of the plastic deformation of the enamel during the indentation process. Therefore, when the contact stiffness versus square root of the projected contact area does not show a linear tendency, it is, most probably, a consequence of a cracking process developed during the indentation process.
It is well known that the area under the load-displacement curve during the unloading process is the corresponding elastic work. However, if cracking occurs, part of the elastic energy stored during the indentation test will be released to create new crack surfaces. This will be reflected as a change in the contact stiffness and, consequently, the relationship between contact stiffness, S , and the squared root of the contact area, A , will not be linear, as the contact theory predicts . Therefore, the linear tendency of contact stiffness versus squared root of the contact area will only remain before cracking occurs. Then, it is possible to identify in the S – A 1/2 curve, a critical point associated with the onset of cracking ( S * , A 1/2* ). According to the Oliver–Pharr methodology , it is possible to calculate the load and penetration depth values corresponding to the critical point associated with the cracking initiation, P * and h * . For values ( P , h ) lower than the critical point, the indentation process will take place without cracking. For higher values, the indentation process will be characterized by the nucleation and propagation of cracks. The load-penetration depth curve for values lower than the critical one can be extrapolated according to the Kick’s law , <SPAN role=presentation tabIndex=0 id=MathJax-Element-6-Frame class=MathJax style="POSITION: relative" data-mathml='P=E⋅h2′>P=E⋅h2P=E⋅h2
P = E ⋅ h 2
, to the maximum penetration depth or indentation load, obtaining a hypothetical curve characteristic of a non cracking process.
2.3.2
Determination of A crack
Following the assumption of Laugier to develop the indentation fracture toughness model for Berkovich indentation , the radial crack geometry inside the enamel was postulated in this work (see Fig. 1 a ). Under this assumption, the authors propose two possible ways to estimate the cracked area: using the crack lengths directly; and through the contact stiffness variation.

The cracked area estimation through the crack length was determined assuming that the crack from the edge of the indentation imprint, run through the protein interlayer ( Fig. 1 b). This phenomenon was previously observed by other authors . Under this assumption, the crack path around each prism was approached as a half of a circumference ( Fig. 1 b). Additionally, this sinuous crack propagation, was considered effective from the end of the indentation imprint, a , to the end of the crack, c ( Fig. 1 b). Therefore, the length of each crack, L c , could be written as:
L c = π 2 ( c − a ) + a
In order to obtain the cracked area, an elliptical geometry of the crack shape in the depth direction was expected ( Fig. 1 a). The major axis was equal to the crack length, L c , and the minor one was assumed equal to c /2 ( Fig. 1 a). Similar postulation was previously pointed out by Hayashi-Sakai et al. . Therefore, the area of each crack, A c , was written as:
A c = π L c 2 c 2
If N cracks were generated during the indentation process, the total cracked area, A crack could be written as:
A crack = N ⋅ A c
Substituting Eqs. (6) and (7) into Eq. (8) , the total cracked area result:
A crack = N ⋅ π 2 8 c 2 + π ( 2 − π ) 8 a ⋅ c
where N corresponding to the number of cracks, a and c are cracks lengths defined in Fig. 1 .
Considering that the experimental conditions of the indentations were carefully selected to obtain a characteristic pattern composed of three cracks, each one running from each indenter Berkovich corner, N = 3.
The cracking area estimation from the contact stiffness can be expressed as a function of the elastic modulus of the enamel according to the Oliver and Pharr methodology . Therefore, the variation of the contact stiffness observed from the critical point ( P * , h * ), is associated with a progressive decrease in the corresponding elastic modulus.
The decrease of this property can be used to estimate the cracked area, mainly following the results of Budiansky and O’Connell , Case and Kim , Fan et al. , and others authors . According to these studies, the elastic modulus, E , of the microcracked body can be expressed by:
E = E S ( 1 − f ε )
where E s refers to the non-microcraked elastic modulus. The function f depends on the spatial orientation of the microcracks . The crack damage parameter ɛ can be expressed as:
ε = 2 π 〈 A 2 〉 〈 P 〉 ⋅ N V
where N v is the volume number density of microcracks, 〈 A 2 〉 is the mean of the square of the cracked area and 〈 P 〉 is the mean crack perimeter. The volume number of density is defined by the relation between the number of cracks, N , and a representative volume, V :
N V = N V
In this study and based on the cylindrical cavity model for cracked brittle solids subjected to indentation tests , a cylindrical representative volume of radius equal to the mean crack length, c , and total depth of c /2 was considered ( Fig. 1 ). Therefore, the volume of material affected by the indentation process could be estimated by Eq. (13) :
V = π ⋅ c 2 ⋅ c 2
According to Fig. 1 :
A = 1 2 π c 2 2
P = π c 2
Substituting Eqs. (14) and (15) into Eq. (11) :
ε = c 3 16 ⋅ N V
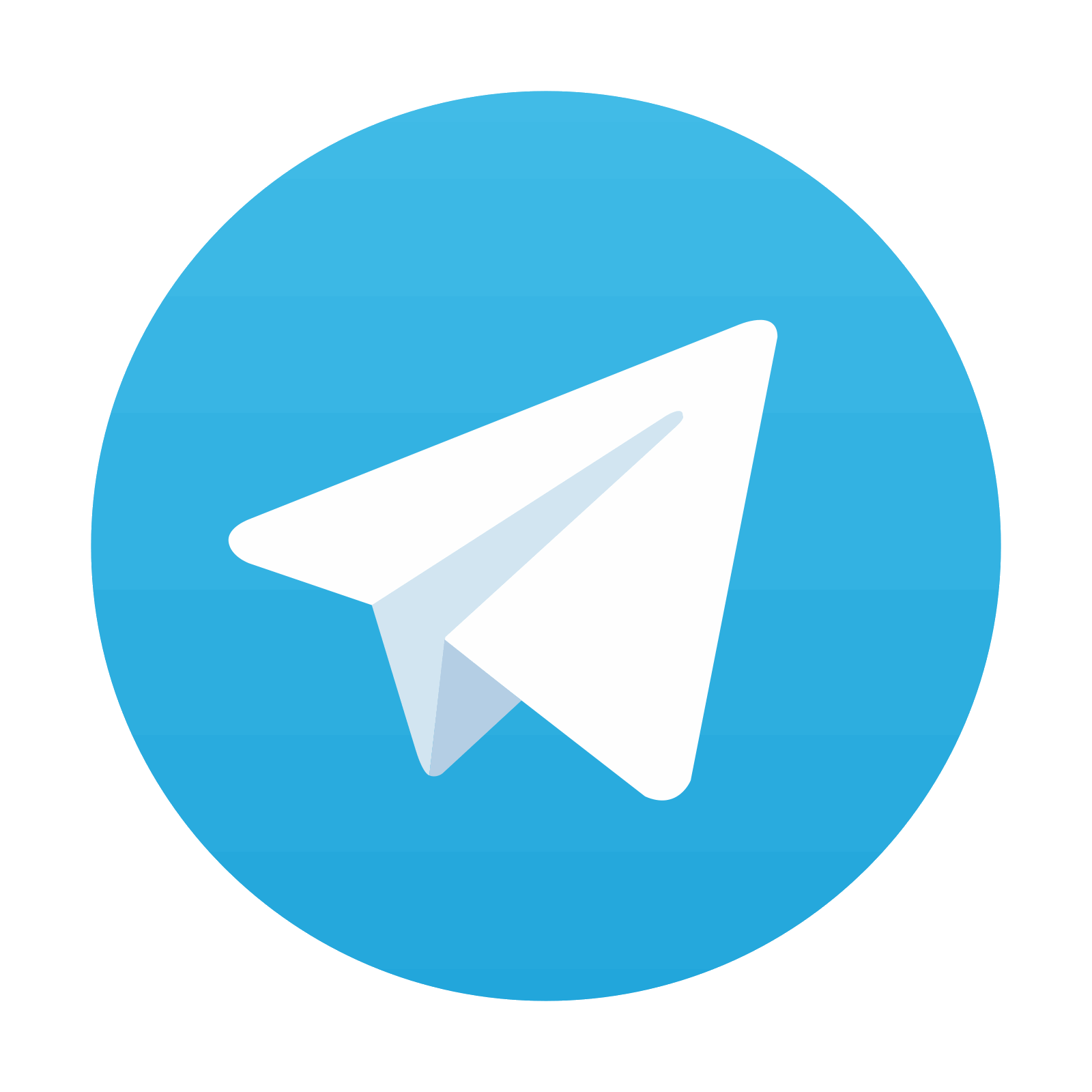
Stay updated, free dental videos. Join our Telegram channel

VIDEdental - Online dental courses
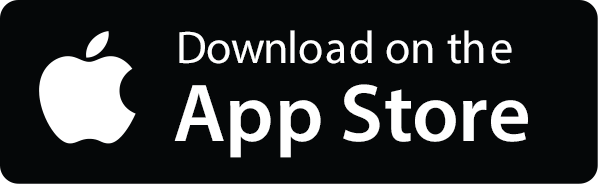
