Highlights
- •
Edge chipping tests with simple rectangular test blocks evaluate a materials resistance to chipping.
- •
Materials may be ranked for their chipping resistance.
- •
Force versus distance trends may be linear or nonlinear depending upon the sharpness of the indenter.
- •
A new model of edge chipping resistance is presented.
- •
Round robins (interlaboratory comparative studies) are a valuable tool to improve mechanical testing procedures and should be used more often by the dental materials community.
Abstract
Objective
The edge chipping test is used to measure the fracture resistance of dental restoration ceramics and resin composites. This paper focuses on the progress of evaluating chipping resistance of these materials and also on the progress of standardization of this test method. This paper also makes observations about the state of the art of mechanical testing of ceramic and composite restorative materials in general. Interlaboratory comparative studies (“round robins”) are recommended.
Methods
An edge chipping machine was used to evaluate dozens of materials including porcelains, glass ceramics, aluminas, zirconias, filled resin-composites, new hybrid ceramic-resin composites, laminated composite ceramics, and even polymethyl methacrylate based denture materials. Force versus distance data was collected over a broad range with different indenters. Several chipping resistance parameters were quantified.
Results
Older restorative materials such as feldspathic porcelains and veneering materials had limited chipping resistance, but more modern ceramics and filled composites show significant improvements. A yttria-partially stabilized zirconia had the greatest resistance to chipping. Much of the early work on edge chipping resistance of brittle materials emphasized linear force versus distance trends obtained with relatively blunt Rockwell C indenters. More recently, trends for dental restorative materials with alternative sharper indenters have been nonlinear. A new phenomenological model with a simple quadratic function fits all data exceptionally well. It is loosely based on an energy balance between indenter work and fracture and deformation energies in the chipped material.
Significance
Although a direct comparison of our laboratory scale tests on idealized simple geometries to clinical outcomes has not yet been done, anecdotal evidence suggests the procedure does produce clinically relevant rankings and outcomes. Despite the variations in the trends and indenters, comparisons between materials can easily be made by chipping convenient block-shaped specimens with sharp conical 120°, Vickers, or Rockwell C indenters at a defined edge distance of 0.5 mm. Broad distance ranges are recommended for trend evaluation. This work has provided important information for standardization.
1
Introduction
The edge chipping test was originally developed in the late 1980s to study hard metal cutting tools at the National Physical Laboratory in London . Chips are formed by advancing an indenter into a material near an edge as shown in the insert of Fig. 1 . The force required for chip formation, F , increases with distance from the edge, d . The shape of the chip usually is independent of the material tested . J. Quinn pioneered the application of this method to dental restorative materials in the mid-1990s to the time of her untimely death in 2008 . This work continued over the ensuing years including three papers in this Journal in 2014. Other groups have used it for the evaluation of human teeth , dental restorative materials , and structural ceramics in general . Clinical longevity studies have shown that chipping is a leading cause of restoration failure . In some cases it is possible to repair restorations, but in others a complete replacement is needed. Scherrer showed eight clinical failures studies of which six were chipping of the veneer. Chipping in veneers has been specifically identified as a problem in modern zirconia restorations . In other cases chipping can occur at a crown margin during manufacture and can weaken the restoration dramatically. Major cracks emanate from the margin starter chips and split a crown in half due to hoop stresses. Unfortunately, the extent of the chipping and the type of chipping is often unreported in clinical studies. Ref. is an interesting exception where six chipping modes were reported for 22 class IV restorations in a clinical study of 455 composite resin anterior restorations. Chipping in natural teeth was cited as a common problem associated with tongue piercing jewelry .

Although the in vitro edge chip tests use specific indenters on test blocks with carefully prepared edges, the chips physically resemble some types of in vivo failures . Our in vitro work has focused on testing block-shaped specimens for the most part, but there is no reason that human or artificial teeth cannot be tested as shown in Fig. 2 .

A short review paper on the edge chipping test method as applied to dental materials was prepared in 2012 , but there has been substantial progress in the last 2 years . Test procedures have been refined. The influence of indenter type has been clarified and it appears that material rankings do not change very much between indenter types. The actual force–distance trends do vary with indenter. Indenter sharpness was identified as a key factor in large part due to sideways wedging forces created during the chipping process . It was shown that the Vickers indenter with face angles of 136° 30′ and edge angles of 148° was equivalent to a 140° sharp conical indenter. Unlike the early assumption that most materials follow linear trends, we now know that nonlinear behavior is common especially for dental restorative materials chipped with sharp indenters. Although a full characterization is best achieved by collecting data over a broad force and distance range, a simple comparison of materials can be made by measuring the “edge strength,” which is the force to make a chip at the arbitrary distance of 0.5 mm as done by Watts et al. . Simple block shaped specimens that are at least 5 mm thick are adequate for most purposes. Comparative data taken on brittle denture materials showed that the data taken from flattened teeth matched the rectangular wear block data .
A new phenomenological model based on energy concepts was introduced in 2014 . Indenter energy is converted into fracture and deformation energies in the chipped material. A simple quadratic equation that relates indenter force to edge chipping distance is an excellent match to the nonlinear outcomes measured on all materials tested.
This paper steps back from the details presented in the earlier papers and presents a broader view of the results and includes some fresh data. Nevertheless, the details (e.g., how well the specimen must be mounted, problems with “overchipping” and the post fracture determination of the distance) are important as this method is developed into a standard. There are two draft test method standards on the edge chipping resistance of brittle materials: one in the European committee for Standards and one in ASTM International . One goal of this study has been to recommend improvements or adaptations to the drafts so that the standards will be useful to the dental community.
2
Materials and methods
The 32 materials have been described previously. 1
1 Commercial products and equipment are identified only to specify adequately the experimental procedures and does not imply endorsement by the authors, institutions or organizations supporting this work, nor does it imply that they are necessarily the best for the purpose.
They include feldspathic porcelains , leucite porcelains , porcelain veneers , glass ceramics , dental and structural aluminas , dental and structural zirconias , filled resin-composites , a new resin nano-filled composite, laminated composite alumina-zirconia ceramics , and even polymethyl methacrylate based denture materials . Test specimens for the various materials varied in size and shape from 3 mm by 4 mm cross section sized bend bar fragments to larger square blocks of 10–20 mm length per side and 5–6 mm thick. The most convenient shape was a wear test type rectangular block. Care is needed to grind the surfaces to make well-defined, reproducible edges. Additional details are in the original references. Several newer materials and data sets not included in the earlier publications are included. These include Ivoclar-Vivadent e.max press and e.max CAD lithium disilicate glass ceramics, and Ivoclar-Vivadent filled resin-composite Tetric EvoCAD. Also included are two batches of Vita Enamic, a “hybrid ceramic” made up of interconnected ceramic and polymer phases, that were obtained in March 2012 and in May 2013. New data on a high-purity structural alumina obtained with the Rockwell C indenter are included here for comparison to earlier sharp conical 120° indenter data .
A commercial edge chipping machine (Engineering Systems Model CK 10, Nottingham, UK) The 1000 N load cell readout resolution was 0.1 N. A reference mass with a certificate traceable to NIST standards was used to verify the accuracy of the load cell. The apparatus had a moveable head with the diamond indenter, a locating microscope, and an X – Y stage to position the test piece. The edge distance, d , was carefully set to a prescribed value prior to each chip test. All distances were from the specimen edge to the center of the point of load application. Most researchers use this convention especially since analytical fracture mechanics models that are relevant to the edge chipping problem usually are based on the axis of load application. The minimum edge distance was 0.10 mm. Usually twenty to thirty five-chips were made per material-indenter combination at distances from 0.10 mm to 0.60 mm. Force, F , was gradually applied in displacement control at 1 mm/min or 3 mm/min until fracture. For most of the materials, the chips popped off suddenly with an audible snap. All testing was done in laboratory ambient conditions. When a chip popped off, a sudden force drop off was detected by the break-load detection circuitry of the machine and the indenter extracted automatically and the peak load recorded. One problem detected in some of our early work, was “overchipping.” Since indenter extraction was not instantaneous, additional damage and a larger indentation were made in the test piece compared to the condition at the instant before the chip popped off. Overchipping severely affects measurements of the edge distances by posttest examination.
Although we favored the sharp tip (radius less than 5 μm) conical 120° indenter, we also experimented with 120° conical Rockwell C, Vickers, Knoop, and sharp conical indenters with 90°–140° angles. The Rockwell C indenter may seem sharp, but it actually has a blunt rounded tip with a 200 μm radius and, at small forces, only the rounded tip contacts the test piece.
It is preferable to collected data over a broad range of distances and forces in order to ascertain the full trend. One goal has been to evaluate whether the force distance data was linear (as assumed in most of the early work), or if nonlinear, whether a power law or a new quadratic function was best. If the trend is linear, then:
F = T e d
where F is the chipping force and d is the distance from the edge. The slope of the fitted line (usually in terms of force in Newtons per millimeter distance) has been defined as the edge toughness , M or T e , (N/mm). T e is numerically equivalent to the force necessary to create a chip at a distance of 1 mm. A power law is sometimes is used:
F = A d n
Although this function fits much of the data, the significance of the constants A and n are problematic. The units of A (N/mm n ) are hard to rationalize. The physical significance of a non-integer exponent n is also hard to justify and our previous results have shown that exponents can vary from 1 to 2 . An indentation mechanics model has been proposed , but only for the case of n = 1.5.
A better newer quadratic relationship based on a simple phenomenological model was derived in 2014 :
F = a 1 d + a 2 d 2
where a 1 and a 2 are constants. Multiplying each side by d , gives:
F d = a 1 d 2 + a 2 d 3
This equation has units of energy. The term on the left can be related to the indenter energy, which is the integral of the applied force times distance penetrated during the chipping process. The a 1 term represents a surface energy term related to fracture surface. The a 2 term is a volume energy term related to deformation volume. A quadratic equation of this form (with surface and volumetric energy terms) has previously been successfully applied as far back as 1941 to brittle material hardness data, but with indentation load and indentation size as the variables. The quadratic is a much better fit and offers improved material insights and interpretation than the commonly used Meyer law, which is a simple power law like Eq. (2) . Refs. have a comprehensive exposition of Eqs. (3) and (4) as applied to edge chipping.
Several other parameters to characterize edge chipping resistance have been devised. One is the edge strength , a term proposed by Watts et al. , which denotes the force necessary to create a chip at an arbitrary distance away from the edge. Edge strength with units of N may be represented by the symbol S E (0.5) where the 0.5 denotes a distance of 0.5 mm, a clinically relevant distance. Alternative distances may be specified. The numerical value of the edge strength , S E (0.5) with units of N is exactly one half the numerical value of the edge toughness , T e , (Eq. (1) ) which has units of N/mm, but only if the data fits a linear trend. The edge toughness , T e is included in the two draft standards . The power law Eq. (2) , the quadratic Eq. (3) , and the edge strength , S E (0.5) are all included in the draft ASTM standard . The CEN standard also allows chipping measurements to be made at a prescribed distance, but specifies that the output should be reported as edge chip resistance , R eA which is the ratio of force to distance with units of N/mm.
2
Materials and methods
The 32 materials have been described previously. 1
1 Commercial products and equipment are identified only to specify adequately the experimental procedures and does not imply endorsement by the authors, institutions or organizations supporting this work, nor does it imply that they are necessarily the best for the purpose.
They include feldspathic porcelains , leucite porcelains , porcelain veneers , glass ceramics , dental and structural aluminas , dental and structural zirconias , filled resin-composites , a new resin nano-filled composite, laminated composite alumina-zirconia ceramics , and even polymethyl methacrylate based denture materials . Test specimens for the various materials varied in size and shape from 3 mm by 4 mm cross section sized bend bar fragments to larger square blocks of 10–20 mm length per side and 5–6 mm thick. The most convenient shape was a wear test type rectangular block. Care is needed to grind the surfaces to make well-defined, reproducible edges. Additional details are in the original references. Several newer materials and data sets not included in the earlier publications are included. These include Ivoclar-Vivadent e.max press and e.max CAD lithium disilicate glass ceramics, and Ivoclar-Vivadent filled resin-composite Tetric EvoCAD. Also included are two batches of Vita Enamic, a “hybrid ceramic” made up of interconnected ceramic and polymer phases, that were obtained in March 2012 and in May 2013. New data on a high-purity structural alumina obtained with the Rockwell C indenter are included here for comparison to earlier sharp conical 120° indenter data .
A commercial edge chipping machine (Engineering Systems Model CK 10, Nottingham, UK) The 1000 N load cell readout resolution was 0.1 N. A reference mass with a certificate traceable to NIST standards was used to verify the accuracy of the load cell. The apparatus had a moveable head with the diamond indenter, a locating microscope, and an X – Y stage to position the test piece. The edge distance, d , was carefully set to a prescribed value prior to each chip test. All distances were from the specimen edge to the center of the point of load application. Most researchers use this convention especially since analytical fracture mechanics models that are relevant to the edge chipping problem usually are based on the axis of load application. The minimum edge distance was 0.10 mm. Usually twenty to thirty five-chips were made per material-indenter combination at distances from 0.10 mm to 0.60 mm. Force, F , was gradually applied in displacement control at 1 mm/min or 3 mm/min until fracture. For most of the materials, the chips popped off suddenly with an audible snap. All testing was done in laboratory ambient conditions. When a chip popped off, a sudden force drop off was detected by the break-load detection circuitry of the machine and the indenter extracted automatically and the peak load recorded. One problem detected in some of our early work, was “overchipping.” Since indenter extraction was not instantaneous, additional damage and a larger indentation were made in the test piece compared to the condition at the instant before the chip popped off. Overchipping severely affects measurements of the edge distances by posttest examination.
Although we favored the sharp tip (radius less than 5 μm) conical 120° indenter, we also experimented with 120° conical Rockwell C, Vickers, Knoop, and sharp conical indenters with 90°–140° angles. The Rockwell C indenter may seem sharp, but it actually has a blunt rounded tip with a 200 μm radius and, at small forces, only the rounded tip contacts the test piece.
It is preferable to collected data over a broad range of distances and forces in order to ascertain the full trend. One goal has been to evaluate whether the force distance data was linear (as assumed in most of the early work), or if nonlinear, whether a power law or a new quadratic function was best. If the trend is linear, then:
F = T e d
where F is the chipping force and d is the distance from the edge. The slope of the fitted line (usually in terms of force in Newtons per millimeter distance) has been defined as the edge toughness , M or T e , (N/mm). T e is numerically equivalent to the force necessary to create a chip at a distance of 1 mm. A power law is sometimes is used:
F = A d n
Although this function fits much of the data, the significance of the constants A and n are problematic. The units of A (N/mm n ) are hard to rationalize. The physical significance of a non-integer exponent n is also hard to justify and our previous results have shown that exponents can vary from 1 to 2 . An indentation mechanics model has been proposed , but only for the case of n = 1.5.
A better newer quadratic relationship based on a simple phenomenological model was derived in 2014 :
F = a 1 d + a 2 d 2
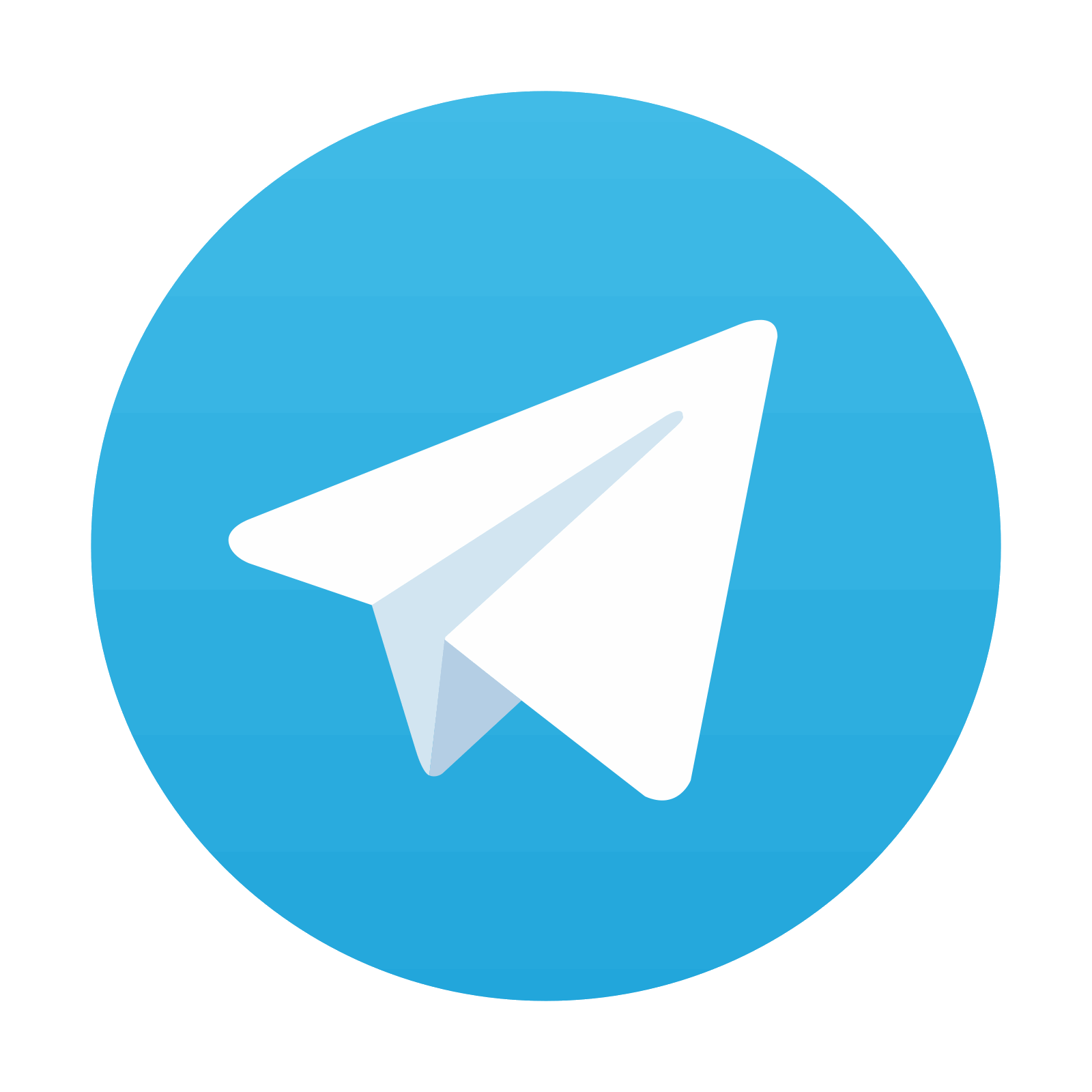
Stay updated, free dental videos. Join our Telegram channel

VIDEdental - Online dental courses
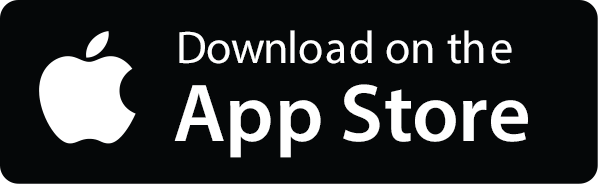
