Abstract
The authors describe the novel use of a selective laser sintering (SLS) machine, commonly used in the aerospace industry, to produce an accurate model of an orbital blowout fracture. Standard stereolithographic apparatus (SLA) technology failed to reproduce either orbital floor of a patient with a blowout fracture. The use of SLS technology using the same CT dataset to produce a superior model, highlights potential limitations of routine SLA technology and the high accuracy of SLS models. A custom-made titanium implant was constructed by hand using the SLS model as a template, it was positioned surgically and the patient’s symptoms resolved uneventfully.
Orbital floor blowout fractures may occur following blunt trauma to the globe. The orbital floor is very thin and relatively weak, allowing any forces applied to the globe to be dissipated inferiorly. This natural crumple zone has evolved to protect the globe from severe trauma that may lead to its rupture, and the orbital floor preferentially blows out. There may be associated inferior rectus muscle entrapment, manifesting with diplopia on upward gaze, and evidence of hypoglobus (inferior globe displacement) and enophthalmos (posterior globe displacement).
Techniques to repair orbital floor fractures are varied and there is no current consensus about the ‘gold standard’ approach. A previously described technique involves rapid prototyping of a model with stereolithographic apparatus (SLA) technology using the 3D CT dataset. The orbital floor fracture is assessed and restored with wax to reproduce a similar (mirrored) contour to the non-injured side. A silicone impression of the restored orbit is taken, and a hard stone model made from this. Medical-grade titanium in sheet or mesh form 0.25–0.5 mm thick, is swaged onto the stone model, and a custom-made titanium plate constructed. The present case study reports a variation of this technique using an aerospace selective laser sintering (SLS) machine routinely used to construct aerospace parts and prototypes.
Case report
A 29-year-old male sustained a left-sided orbital blowout fracture following a blow to the face whilst snowboarding. His medical status was unremarkable and he was of average build. There was no history of head trauma and his visual acuity was previously normal, not necessitating correction with lenses. A CT scan ( Fig. 1 ) demonstrated a significant blowout of the inferior rectus muscle into the maxillary sinus with entrapment. He had symptoms of severe diplopia on upward gaze, which greatly affected his work as an aerospace engineer. This was his chief complaint, along with cosmetically obvious hypoglobus and enophthalmos.

The 2D data were converted to 3D data using Mimics ® software (Materialise NV, Leuven, Belgium) and sent for rapid prototyping using SLA. The SLA model ( Fig. 2 ) failed to reproduce either orbital floor, due to the thin nature of the bone so a prosthesis could not be made using this template.

The patient, an aerospace engineer, had access to an SLS machine ( SinterStation HiQ / HS , 3D Systems) at work, routinely used for rapid prototyping of aeroplane parts and prototypes. On seeing the poor quality of the SLA model, he requested a copy of the same 3D CT data. He used this to produce a vastly superior model in sintered nylon (glass-filled nylon; GF Duraform , 3D Systems) on his aerospace SLS machine ( Fig. 3 ). This enabled the maxillofacial technician to construct the titanium prosthesis, facilitating surgical repair of the blowout fracture ( Fig. 4 ), with a successful clinical outcome ( Fig. 5 ).
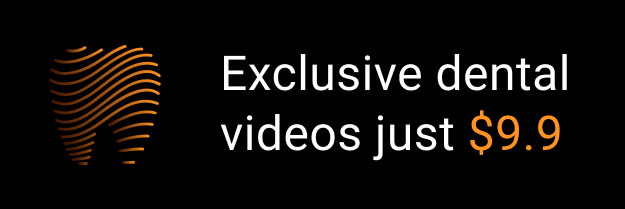