12
Nickel-Titanium Metallurgy
Ya Shen and Markus Haapasalo
Summary
An awareness and knowledge of the properties of nickel-titanium (NiTi) endodontic instruments and their association with the metallurgical properties is useful for clinicians to understand their behaviour in root canals and help them to make decisions regarding which instruments are appropriate for root canal treatment under certain clinical conditions. This chapter summarises the metallurgical properties of NiTi endodontic instruments, with a special focus on the latest generation of NiTi instruments. The impact that these modifications have on their mechanical properties is discussed.
12.1 Introduction and Classification of Current NiTi Alloy Phases
Nickel-titanium instruments were described 30 years ago by Walia and colleagues and brought a major breakthrough to root canal instrumentation, which has reduced most iatrogenic instrumentation complications often associated with stainless steel files [1, 2]. The composition of endodontic NiTi instruments is 56% nickel and 44% titanium by weight, also expressed as a 1 : 1 atomic ratio between the elements [3]. The crystal structure of NiTi can exist in three different states (austenite, martensite, and R-phase), which influences the physical properties of the alloy [3, 4]. Nickel-titanium alloy has special characteristics of superelasticity and shape memory [3, 5]. Superelasticity is associated with the occurrence of a phase transformation of the alloy upon application of stress above a critical level, which takes place when the ambient temperature is above the so-called austenite finish (Af) temperature of the material. This stress-induced martensitic transformation reverses spontaneously upon release of the stress; the material then returns to its original shape and size [5]. This reversible thermoelastic martensitic transformation is the main reason for increased flexibility of NiTi instruments over traditional stainless steel instruments and facilitates instrumentation of curved root canals [3]. Superelasticity occurs in association with a reversible phase transformation between austenite and martensite. Therefore, the transformation temperatures have a critical influence on the mechanical properties, and the behaviour of NiTi, which can be altered by small changes in composition, impurities, and heat treatments during the manufacturing process [6]. This distinct property of NiTi alloys has created a revolution in the manufacture of endodontic instruments.
The first commercially available NiTi rotary instruments came to market in the 1990s [7]. An increasing number of superelastic NiTi endodontic files with various geometrical designs has emerged during the last 20 years [7–9]. Even though there have been considerable improvements in the file design and manufacturing methods on endodontic rotary instruments made of NiTi alloys, intracanal fracture of rotary instruments caused by cyclic fatigue remains a concern, especially in root canals with severe curvatures [10–14]. The mechanical behaviour of NiTi alloy is determined by the relative proportions and characteristics of the microstructural phases. Heat treatment (thermal processing) affects the fatigue resistance of NiTi instruments and is one of the fundamental ways to adjust the transition temperatures of NiTi alloys [15–20].
Novel NiTi instruments fabricated by proprietary thermomechanical processes such as M-Wire files (e.g. ProFile GT Series X [Dentsply Tulsa Dental Specialties, Tulsa, OK, USA] and ProFile Vortex [Dentsply Tulsa Dental Specialties]), controlled memory (CM) files (e.g. HyFlex CM [Coltene Whaledent, Cuyahoga Falls, OH, USA] and Typhoon Infinite Flex NiTi [Clinician’s Choice Dental Products, Milford, CT, USA]), and R-phase wire (e.g. Twisted files [TF] [SybronEndo, Orange, CA, USA] and K3XF [SybronEndo]) have been introduced and have been reported to have improved flexibility and cyclic fatigue resistance compared to the traditional superelastic NiTi files [19–24]. New NiTi instrument systems manufactured from NiTi alloy heat treated in a specific manner have a surface layer of titanium oxide (ProFile Vortex Blue [Dentsply Tulsa Dental Specialties], WaveOne Gold [Dentsply Sirona, York, PA, USA] and Reciproc Blue [VDW, Munich, Germany]) (Table 12.1), and an increased fatigue resistance, besides greater flexibility than those made of conventional NiTi alloy.
Table 12.1 Overview of thermomechanically treated NiTi instruments.
Alloy | Representative NiTi instruments | Treatment methods | Phase composition | Properties |
---|---|---|---|---|
M-Wire | ProFile Vortex | Heat treated before machining the file flutes | Austenite phase with small amounts of martensite and R-phase at body temperature |
More flexible than the conventional NiTi files Increased fatigue resistance |
WaveOne ProTaper Next |
Post-manufacturing thermal process | |||
Blue heat-treated |
Vortex Blue Reciproc Blue |
A complex heating and cooling treatment after machining | A mixture of austenite and martensite structure |
Shape memory Enhanced flexibility Increased fatigue resistance |
Gold wire |
ProTaper Gold WaveOne Gold |
|||
R-phase | Twisted file | Using the twisting method when the R-phase is identified | Austenite phase at room temperature |
Increased fatigue resistance A lower torsional resistance |
CM wire |
TYPHOON Infinite Flex Hyflex CM |
A complex heating and cooling treatment after machining |
Martensitic with varying amounts of austenite and R-phase |
Shape memory Greater flexibility than M-Wire Excellent fatigue resistance Increased tendency of permanent plastic deformation during use |
Hyflex EDM | CM alloy via an electrodischarge machining process | Martensite and rhombohedral R-phase at body temperature (no austenite phase) | ||
Max-Wire |
XP-endo Shaper XP-endo Finisher |
Heat treatment, form pressing | Martensitic (20°C); austenitic (35°C) (company claimed) |
Shape memory Superelasticity |
T-wire | 2Shape | Heat treatment | Not available |
More flexibility Increased fatigue resistance |
C-wire | One Curve | Heat treatment | Not available |
Shape memory Increased fatigue resistance |
The majority of commercially available files that are utilised to shape root canals are manufactured out of NiTi and are mechanically driven in continuous rotation. In 2008, Yared identified precise unequal clockwise/counterclockwise angles that would enable a single reciprocating size 25, .08 taper ProTaper instrument (Dentsply Maillefer, Ballaigues, Switzerland) to optimally shape virtually any canal [25]. Although this specific reciprocation technique stimulated considerable interest, this ProTaper F2 file was never designed to be used in this manner. In 2011, both WaveOne (Dentsply Sirona) and Reciproc (VDW) were launched as single-file shaping techniques. Both files are made out of M-Wire. The benefits of reciprocation include decreased formation of intradentinal cracks and decreased risk of fracture by fatigue when compared to continuous rotation [26–28]. Reciprocating movements result in the file experiencing fewer complete rotations and fewer tensile-compressive stress cycles compared to the continuous rotation, which may account for the increased cyclic fatigue resistance [26]. Years later, heat-treated reciprocating files, WaveOne Gold (Dentsply Sirona) and Reciproc Blue (Figure 12.1), were released and demonstrated increased flexibility compared to their predecessors [29, 30].

Figure 12.1 Scanning electron micrographs of reciprocating instruments. There are dimensional and design differences between the WaveOne and WaveOne Gold primary files. The Reciproc Blue instrument has a design that features identical geometries as Reciproc.
12.2 Properties of Each Phase (Austenitic, Martinsitic, R-phase)
The differences in mechanical properties between NiTi endodontic instruments lie in the properties of the phases that exist in the alloy. The austenite phase (parent phase, with the B2 cubic crystal structure) exists at higher temperatures and is stronger (about 80–90 GPa) and stiffer than the martensite phase (with a monoclinic B19ʹ structure), which exists at lower temperatures and is softer (about 30–40 GPa) and more flexible [3, 31]. When martensitic NiTi is heated past the austenite transformation start temperature (As), the NiTi’s crystal structure begins to change to austenite and will become fully austenite once heated past the higher Af (Austenite finish) temperature. The heat-induced transformation of martensite to austenite is the basis of NiTi’s shape memory characteristic. Conversely, as austenite cools it will begin to change to martensite at the martensite transformation start temperature (Ms) and will complete the transition to martensite at the martensite transformation finish temperature (Mf). The phase transformation from austenite to martensite can also be stress-induced (such as instrument bending), as seen in superelastic NiTi alloys, which allows the NiTi to accommodate a greater amount of stress without an increase of strain [3, 32]. The superelasticity of NiTi allows deformations of as much as 8% strain to be fully recoverable, in comparison with a maximum of less than 1% with other alloys such as stainless steel [3]. To best utilise the superelastic property of NiTi alloys, these alloys should be in the austenitic state [33]. Many conventional NiTi endodontic files are made of superelastic NiTi alloy, which are in the austenitic state at body temperature. They can be inserted easily in the root canals due to the high elasticity and flexibility, and when an external stress is applied due to the torsion stress and the file friction against the canal walls, the stress-induced martensitic transformation occurs, giving rise to a more elastic material with a high ultimate tensile strength [34, 35]. In this way, the files work with a constant cutting stress, even in a much-curved canal. It is the reason why NiTi files are advantageous in maintaining the shape of root canals compared to stainless-steel files [2].
When the NiTi alloy is deformed in the martensite state, it undergoes a strain, which is completely recoverable upon heating. This behaviour is called the shape memory effect. Deformation via martensite reorientation may be observed at temperatures below As, the critical starting temperature for the reverse transformation of martensite on heating [33] and is completed at Af. This process is thermally driven and influenced by the transformation temperatures. Peters et al. [23] found that instruments in the martensitic phase can be easily deformed (e.g. from the straight file into a curved one) and will recover their shape when heated beyond the transformation temperature (Figure 12.2). The martensite phase of the NiTi alloy is a low-temperature phase with monoclinic structure (B19ʹ), which possesses a lower Young’s modulus and yield strength than the austenite [36, 37]. This indicates that the martensite is easily deformed at quite a low stress, whereas the austenite has a much higher yield and flow stresses. Besides being more flexible than austenite, the martensite phase favors reducing the risk of file fracture under high stress because it can be plastically deformed rather than broken. Therefore, much effort has been devoted to introduce martensite into commercial NiTi endodontic instruments such as M-Wire and CM endodontic instruments. The M-Wire NiTi endodontic instruments including ProFile Vortex, ProFile Vortex Blue, WaveOne, and Reciproc are manufactured from the superelastic NiTi wires containing martensite at room temperature. Several studies on the performance of the commercial instruments made from M-Wire NiTi suggested enhanced flexibility and fatigue resistance [21–23]. The CM files such as Hyflex CM file and Typhoon Infinite Flex NiTi files are used in the martensitic state when used clinically and possess the shape memory effect. These files can return to their original shape by autoclaving after use in curved canals [23].

Figure 12.2 Controlled memory files: HyFlex size 25, 0.06 taper (a) and EDM size 50, .03 taper, size 60, .02 taper (b) instruments. Photos courtesy of Artendo Enterprises Inc.
The martensite to austenite and austenite to martensite phase transformations can occur in either one or two stages, where the two-stage transformation involves the formation of an intermediate R-phase [33]. The R-phase is a rhombohedral phase that is incommensurate with the cubic B2 phase [38]. The R-phase transformation occurs prior to the B2-B19′transition and exhibits the characteristics of thermoelastic martensitic transformation, i.e. shape memory and superelasticity effects. Thus, the R-phase transformation can be temperature-induced and stress-induced in NiTi alloys. Compared with the martensite/austenite transformation in NiTi, the recoverable strain of the R-phase/austenite transformation (approximately 0.5%) is smaller and the temperature hysteresis is extremely small [33]. Moreover, the cyclic stability of the R-phase/austenite transformation is excellent [39] and the Young’s modulus of the R-phase is typically lower than that of austenite. The appropriate choice of thermomechanical treatments can make the R-phase transformation occur due to the fact that the R-phase transformation tends to occur when precipitates or dislocations exist in the crystalline structure. The aging of Ni-rich NiTi alloy at the proper temperature may cause the precipitation of the Ti3Ni4 phase, and thermomechanical treatment (heat treatment after cold working) of NiTi alloy may create rearranged dislocated structures [19]. Therefore, utilisation of the R-phase transformation in the design and fabrication of NiTi endodontic instruments has the potential to produce new, innovative endodontic instruments. Twisted files are manufactured by twisting the NiTi rod instead of conventional grinding. Twisting is made possible because the TF file is manufactured using a twisting method with the R-phase alloy; it exhibits a higher fatigue fracture resistance than ground files as reported in preliminary studies [40–43]. K3XF is another product that takes advantage of R-phase technology and was developed by the same company as TF files (SybronEndo).
Conventionally, superelastic NiTi instruments existed in the austenite phase at room and body temperature (Figure 12.3), which limits their use in severely curved canals due to the instrument’s stiffness and low fatigue resistance [16, 44]. Heat treatment produces a more flexible and fatigue-resistant NiTi instrument by releasing the internal strain of the alloy and increasing the NiTi’s phase transformation temperatures, resulting in a more martensitic alloy at clinically relevant temperatures [16, 20, 45].

Figure 12.3 Differential scanning calorimetry curves of NiTi instruments. The austenite-finish (Af) temperature shown with blue dotted line is 17°C for a ‘conventional’ superelastic NiTi file (a) and 55°C for heat-treated NiTi file shown with red dotted line (b). The blue bar represents the range between room temperature and body temperature.
12.3 Surface Treatment of NiTi Alloys
Surface enhancement of NiTi instruments minimises inherent defects and increases surface hardness and flexibility resistance to fatigue and cutting efficiency [46–51]. A number of studies have aimed to enhance superelastic NiTi instruments by boron implantation [46], thermal nitridation [47], thermal metal organic chemical vapour deposition [49], and physical vapour deposition of titanium nitride [50].
Microcracks often are first formed on the surface of the instrument, signifying the very first stage of the fatigue phenomenon [52]. Thus, treatment that improves the surface smoothness would be expected to inhibit the crack-initiation process and enhance the fatigue resistance. Electropolishing is a method for finishing metallic products to a high gloss. It is performed by immersing the part in a specially formulated, usually acidic, electrolyte solution and passing a direct electric current to facilitate a selective dissolution of the material (i.e. at sharp edges or ‘peaks’ of an irregular surface in which the current density is higher than for relatively smooth or recessed areas) [51]. The resistance to corrosion should also be enhanced [53]. This process is widely used for finishing and passivating NiTi medical appliances and implantable stents. A couple of manufacturers (e.g. RaCe [FKG Dentaire, La Chaux-de-Fonds, Switzerland], EndoSequence [Brasseler, Savannah, GA, USA], and K3XF) have claimed to have electropolished their NiTi instruments. Electropolishing has been shown to improve the fatigue resistance of NiTi instrument in some studies [54–56]; however, others have shown that the positive effects of electropolishing may vary depending on instrument type, design, and in particular, cross-sectional area [57, 58].
Electropolishing only affects the surface of the NiTi material. The unaltered core contains inclusion particles such as titanium carbonitride and nickel-titanium oxide from the manufacturing process of NiTi alloy. Inclusions are unavoidable during the manufacturing process [59]. Modern commercially produced NiTi materials are designed to contain fewer inclusions (both oxides and carbides) that would never approach the 10–20% range [60]. The critical inclusion size for fatigue failure of superelastic austenitic NiTi is around 15–50 µm if the inclusion is near the surface [61]. The size of inclusion on the smooth surface of NiTi instruments (only 2–8 µm) was below the critical flaw size for outright fracture [24, 62] (Figures 12.4 and 12.5). Therefore, these small inclusions do not contribute to the failure but can serve as a local stress/strain discontinuity from which the crack can nucleate [24, 62].

Figure 12.4 (a) Longitudinal examination of the electropolished instrument showing the presence of inclusion bodies (arrows). (b) A higher magnification view of inclusion.

Figure 12.5 A photomicrograph of a fracture surface of NiTi instruments with the region of crack propagation and dimple area outlined (dashed line): (a) K3XF in air, (b) from a high magnification view of the crack origination from a below-critical flaw-sized inclusion (arrows), (c) K3XF under water, and (d) from a high magnification view of the crack origination from a below-critical flaw-sized inclusion (arrows).
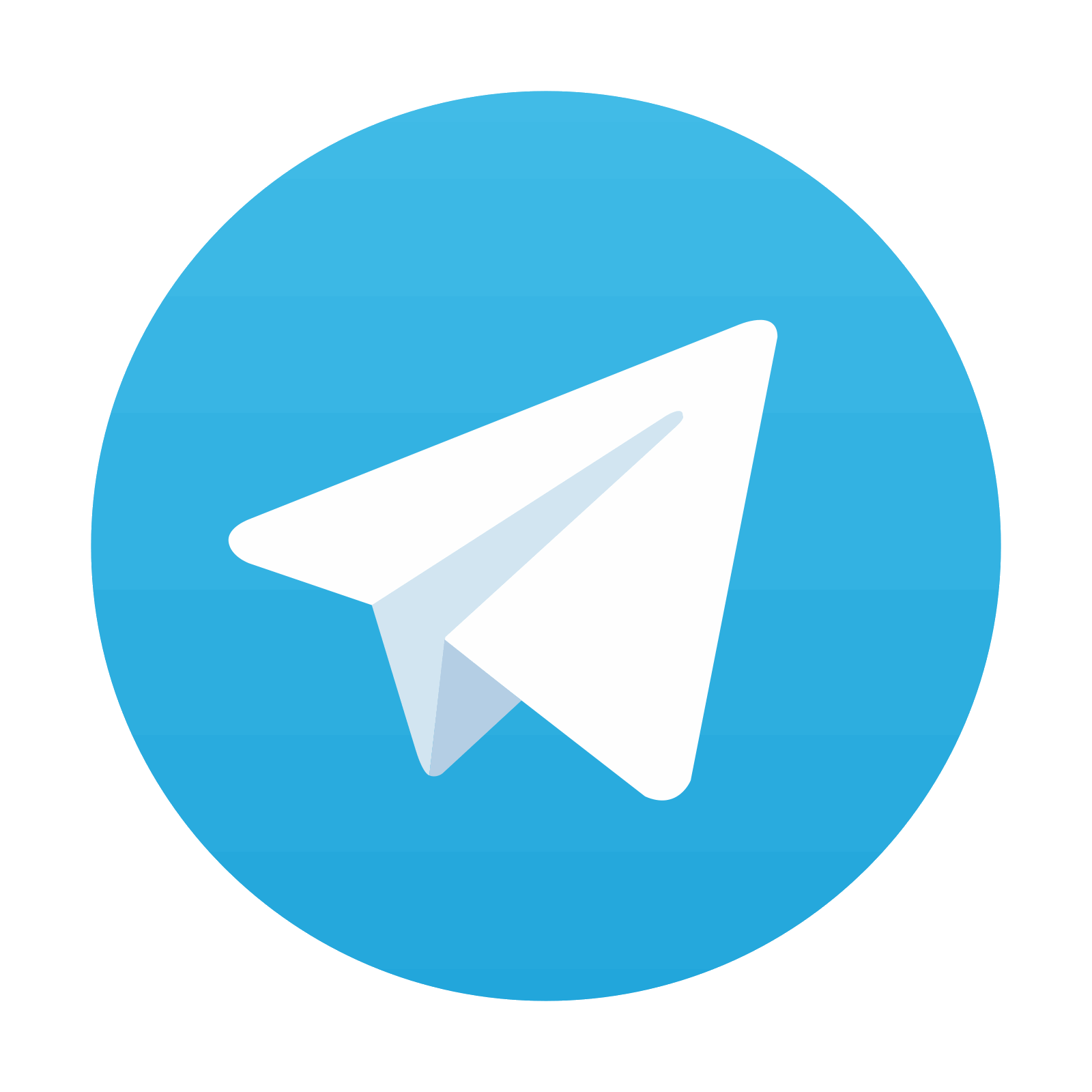
Stay updated, free dental videos. Join our Telegram channel

VIDEdental - Online dental courses
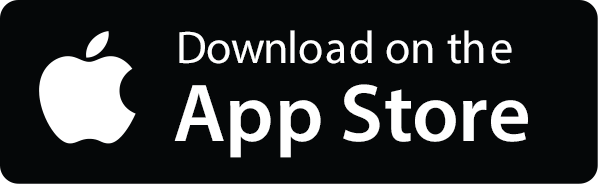
