Graphical abstract
Highlights
- •
Mono or polycrystalline alumina particles were added to a dental porcelain.
- •
Particle coating was carried out by heat treatment of a silica precursor.
- •
The addition of monocrystalline particles yielded a more translucent hybrid ceramic.
- •
Polycrystalline alumina particles worked as nanoclusters.
- •
Glass bridging from porcelain to alumina particles suggested chemical interaction between the two phases.
Abstract
Objectives
This study evaluated the effect of addition of alumina particles (polycrystalline or monocrystalline), with or without silica coating, on the optical and mechanical properties of a porcelain.
Methods
Groups tested were: control (C), polycrystalline alumina (PA), polycrystalline alumina-silica (PAS), monocrystalline alumina (MA), monocrystalline alumina-silica (MAS). Polycrystalline alumina powder was synthesized using a polymeric precursor method; a commercially available monocrystalline alumina powder (sapphire) was acquired. Silica coating was obtained by immersing alumina powders in a tetraethylorthosilicate solution, followed by heat-treatment. Electrostatic stable suspension method was used to ensure homogenous dispersion of the alumina particles within the porcelain powder. The ceramic specimens were obtained by heat-pressing. Microstructure, translucency parameter, contrast ratio, opalescence index, porosity, biaxial flexural strength, roughness, and elastic constants were characterized.
Results
A better interaction between glass matrix and silica coated crystalline particles is suggested in some analyses, yet further investigation is needed to confirm it. The materials did not present significant differences in biaxial flexural strength, due to the presence of higher porosity in the groups with alumina addition. Elastic modulus was higher for MA and MAS groups. Also, these were the groups with optical qualities and roughness closer to control. The PA and PAS groups were considerably more opaque as well as rougher.
Significance
Porcelains with addition of monocrystalline particles presented superior esthetic qualities compared to those with polycrystalline particles. In order to eliminate the porosity in the ceramic materials investigated herein, processing parameters need to be optimized as well as different glass frites should be tested.
1
Introduction
Advanced ceramics used in some highly specialized applications require both optical and mechanical properties for an excellent performance. Amongst these applications is the use of ceramics as dental biomaterials, which need to be constructed into complex and stable-during-sintering shapes, and are subjected to long-term sliding fatigue under mastication in a corrosive/moist environment . Furthermore, dental ceramics are expected to survive for decades in the oral environment, without breaking or loosing the esthetical natural-tooth-looking appearance . The ceramic materials used in dentistry that try to fulfill these expectations usually have a glass matrix with varying crystalline content . Final properties of such materials are affected by the amount of crystalline phase, size and type of crystals, and their dispersion within the glass matrix .
In general terms, increase in the crystalline content leads to mechanical reinforcement . In addition to that, an effective interfacial interaction between matrix and reinforcing crystalline particles is required for improved properties . The presence of a gap between phases would prevent dissipation of stresses from the matrix to the tougher particles . Such gaps would also act as pores and therefore further compromise the material mechanical properties, as well as increase its opacity due to light scattering . When crystalline particles are nucleated and crystalized from the glass matrix, the phases are chemically alike and prone to a chemically stable interfacial interaction . On the other hand, the development of hybrid-ceramic materials by means of addition of second-phase crystalline particles into the glass powder before sintering allows the use of non-silicate tough crystalline oxides, like zirconia or alumina, as reinforcement phase. Because these oxides have such a distinct chemical composition compared to that of the glass, the final mechanical reinforcement can only be achieved if these particles are functionalized to produce an effective interaction with the glass matrix.
To date, only two hybrid-ceramic materials with addition of second-phase crystalline particles are commercially available for dental applications, both having zirconia particles added as crystalline phase into a lithium silicate glass-ceramic system: Vita Suprinity (VITA Zahnfabrik, Bad Säckingen, Germany) and Celtra DeguDent (DeguDent, Hanau, Germany). Despite the current appeal of zirconia, alumina is a technologically important material widely used in numerous applications , yet it is not being used in the tailoring of hybrid-ceramics for dental applications. Alumina is believed to exist in more than 15 different crystallographic phases , which can determine distinct microstructures and properties if applied in hybrid-ceramics. Crystalline alumina has also been given a lot of attention in its transparent monocrystalline state, known as artificial sapphire . The refractive index mismatch between phases is usually the most important aspect to be considered to estimate translucency for hybrid-materials . However, no evidence was found on whether the inherent microstructure, thus inherent translucency of these alumina particles would affect final properties of hybrid-ceramic materials.
To the best of the authors’ knowledge, neither monocrystalline alumina powder nor functionalization of the surface of non-silicate particles with a silicon-rich film have been described in the scientific literature for the development of hybrid-ceramic materials. Therefore, this study was designed to apply nanostructured polycrystalline or translucent monocrystalline alumina particles in the modeling of optical and mechanical properties of a dental ceramic. A silica coating (core-shell) method was used aiming at an effective interfacial interaction between the alumina particles and the glass matrix in the tailoring of hybrid-ceramic materials as dental biomaterials.
2
Materials and methods
2.1
Materials
The dental ceramic used as matrix for the hybrid-ceramic materials in this study is commercially available under the brand name Cerabien (Noritake Dental, Aichi, Japan). The manufacturer classifies this material as porcelain, yet they do not disclose information about its composition. This porcelain was chosen because it has a coefficient of thermal expansion that matches that of alumina, and therefore less residual stresses concentrate near the interface between the two phases. Two types of alumina particles were used in the modeling of the properties of the porcelain: polycrystalline alumina sintered by means of a polymeric precursor method, and monocrystalline alumina commercially available under the brand name Sapphire Powder (GoodFellow, Huntingdon, England). The alumina particles were either silica coated or kept without any coating before being added to the porcelain powder. Coating was carried out using tetraethylorthosilicate (TEOS) as silica precursor (Sigma–Aldrich, St. Louis, MO, USA). In total, five experimental groups were tested: porcelain only (control, C), porcelain + polycrystalline alumina (PA), porcelain + polycrystalline alumina coated with silica (PAS), porcelain + monocrystalline alumina (MA), and porcelain + monocrystalline alumina coated with silica (MAS).
2.2
Synthesis of polycrystalline alumina by a polymeric precursor method
The nanostructured alumina powder was produced by using a variation of a previously described method . Briefly, 1 M aluminum nitrate (Al(NO 3 ) 3 ·9H 2 O) P.A. (Synth, São Paulo, SP, Brazil) and 3 M anhydrous citric acid (C 6 H 8 O 7 ) P.A. (Synth) were dissolved in water at 50 °C for 1 h for the formation of aluminum citrate. Ethylene glycol (C 2 H 6 O 2 ) P.A. (Synth) was added at a 60:40 mass ratio of the citric acid/ethylene glycol. This mixture was then stirred at 80 °C for 1 h, and the temperature was then increased to 130 °C to promote polymerization and remove excess solvents. The resin was then heat-treated in an atmospheric air furnace, with 10 °C/min heating rate up to 300 °C dwell temperature for 2 h in order to burn the organic components, resulting in a black solid mass. This material was finely hand-ground by using mortar and pestle. The powder obtained is referred as the “precursor”. In the furnace, the precursor was heat-treated at 10 °C/min heating rate up to 1100 °C, had dwelled for 2 h in air on an alumina boat, and then cooled to room temperature. The final product was a whitish nanostructured α-alumina powder.
2.3
Silica coating of mono and polycrystalline alumina particles
The alumina particles were used either as-received (monocrystalline) or as-synthesized (polycrystalline) and were coated with a silica layer applied by a sol–gel method. For silica coating, the particles were dispersed in an aqueous solution of 0.1 M hydrochloric acid p.a. (Synth). The suspension was kept in vigorous magnetic stirring for 15 min to favor disaggregation. TEOS was added to the suspension in the proportion of 5 mol% relative to the particles molar mass. Vigorous magnetic stirring was maintained and the temperature risen to 60 °C to evaporate the aqueous content. After drying, the particles were heat-treated in an atmospheric air furnace at 5 °C/min heating rate up to 900 °C dwell temperature for 2 h.
2.4
Microstructural and chemical characterization of the ceramic powders
The micromorphology of the alumina particles with and without silica coating was analyzed by scanning electron microscopy – SEM (JSM 6610, JEOL, Tokyo, Japan). For elemental chemical composition, the alumina powders were analyzed using energy-dispersive spectroscopy – EDS (JSM 6610, JEOL, Tokyo, Japan). Crystalline spectra were determined by X-ray diffraction–XRD (XRD-6000; Shimadzu, Tokyo, Japan) with CuKα radiation at 40 kV and 40 mA, 4°/min scan rate, 10–80° 2 θ , at room temperature.
2.5
Homogenous dispersion/mixture of the hybrid-ceramic powders
A dispersant solution was prepared by solubilizing 0.5 M citric acid (Synth) in deionized water and stirring for 10 min. To this solution, 2 M triethylamine (Synth) was added and magnetic stirring was kept for 2 h, resulting in a solution with pH = 7. This solution was used as dispersant for the addition of the alumina particles to the porcelain powder. It is important to note that type of solution does not leave residues within the material after sintering. Also, it does not cause any erosion of the acid sensitive porcelain particles, and it produces an efficient electrostatic repulsion among ceramic particles . In order to incorporate 10 wt% of alumina particles into the porcelain powder in a homogenous, well dispersed way, these two powders (10 wt% alumina + 90 wt% porcelain) were disaggregated together in a suspension containing isopropyl alcohol with 5% solid content (total powders). To that suspension, 10 wt% of the aforementioned dispersion solution was poured. The suspension was sonicated at 9 W for 10 min in pulse mode (1 s cycles), and then placed into a round-bottom flask and taken to a rotary evaporator (RV10; IKA, Staufen, Germany) at 40 °C under vacuum until complete elimination of the liquid content. The powder was kept in incubation at 150 °C for 2 h to ensure complete solvent removal. After this process, the final material was a hybrid-ceramic powder ready for use. For the control group, the porcelain powder without the addition of alumina was processed similarly to the others as described herein.
2.6
Fabrication of hybrid-ceramic specimens by heat-pressing
The fabrication of both the control and hybrid-ceramic specimens followed the lost-wax technique and heat-pressing method for glass-based ceramics. For each group, five pre-sintered rod-shaped ingots (20 mm height, 12 mm diameter) were obtained by uniaxially pressing 4.5 g of each of the previously prepared (hybrid-)ceramic powders with 2 mL of distilled water at 3 ton, for 30 s. The green-bodies were heat-treated at 45 °C/min heating rate from 600 °C to 750 °C under vacuum, 1 min dwell at 750 °C with vacuum, and 1 min at 750 °C without vacuum. Rod-shaped wax patterns (10 mm height, 12 mm diameter) were produced using a silicone mold. Each wax pattern was individually attached to a pressing ring using a 3 mm round wax sprue and a freshly vacuum mixed investment material was cast on a vibrating table. Following chemical setting time (45 min), the investment ring was transferred to a preheated furnace at 750 °C and left for 1 h to burn out the wax.
A pre-sintered ceramic ingot was placed in the ring and transferred to the heat-pressing furnace (Kerampress; Kota, São Paulo, SP, Brazil), which was programmed according to the following sintering cycle: heating rate of 50 °C/min from 700 °C to 970 °C, dwell 20 min + 8 min pressing at 3 bar (all under vacuum) + 1 min at 970 °C without vacuum.
In order to achieve higher density and translucency, pilot studies were conducted testing ideal sintering temperature and maximum percentage of alumina particles added; sintering temperature ranged from 960 °C (indicated by the manufacturer of the porcelain) to 1000 °C, while particle fractions varied between 5 wt% and 30 wt%. One should consider that the addition of particles changes the viscous flow behavior of the porcelain above the Tg during the heat-pressing process. After divesting and cleaning, the sintered rods were transversely sectioned using a precision circular saw coupled to a diamond-coated wafering blade under water cooling to produce disc-shaped specimens (1.1 mm thickness, 12 mm diameter). The specimens were polished down to 1 μm on both sides to a final thickness of 1 ± 0.05 mm.
2.7
Microstructural and chemical characterization of the hybrid-ceramics
The micromorphology of the sintered hybrid ceramic specimens was analyzed by SEM. The specimens were imaged both on their polished surface as well as after acid etching with 5% hydrofluoric acid for 10 s for better view of the crystals. Elemental chemical composition and mapping was carried out by EDS. The crystalline phases present in each group were determined by XRD as previously described. Surface roughness was analyzed by a contact profiler (SJ-410, Mitutoyo, Tokyo, Japan); roughness was quantified by the amplitude parameter Ra with the following test conditions: cut-off length 0.8 mm, resolution 0.0001 μm (8 μm range), speed 0.5 mm/s, and total length 4 mm. Pore percentage and characterization of porosity were evaluated by using Skyscan 1272 micro-CT (computer tomography) scanner . The following parameters were set for the scanning of all specimens: filter Al 0.5 & Cu 0.038; source voltage 90 kV; source current 111 μA; image pixel size 10 μm; 81 slices; lower grey threshold 60; upper grey threshold 190. A cylinder of ∼4 mm 3 about the center of each scanned specimen was selected for 3D reconstruction and pore evaluation. Total percentage of porosity, percentage of open pores, and percentage of closed pores were measured. In addition, 3D images contrasting dense mass of the ceramic and void spaces of pores were collected.
2.8
Optical properties
Optical properties were evaluated with a spectrophotometer (CM 3700d; Konica-Minolta, Tokyo, Japan), operating in the wavelength range of visible light (400–700 nm), both in reflectance and transmittance modes. Contrast ratio (CR) was calculated from the spectral reflectance of the light of the specimen ( Y ) on a black background ( Y b ) and on a white background ( Y w ) , according to the equation:
CR = Y b / Y w
Translucency parameter (TP) was evaluated by calculating the color difference of the specimens on black and white backgrounds by using the equation:
TP = [ ( L b * − L w * ) 2 + ( a b * − a w * ) 2 + ( b b * − b w * ) 2 ] 1 / 2
where subscript b refers to color coordinates on the black background and subscript w refers to color coordinates on the white background. Opalescence parameter (OP) was estimated as a difference in the chromaticity between the reflected and transmitted colors , according to the equation:
OP = [ ( a t * − a r * ) 2 + ( b t * − b r * ) 2 ] 1 / 2
where subscripts t and r indicate the transmitted and the reflected color, respectively.
2.9
Elastic constants
The Poisson’s ratio ( ν ) and elastic modulus ( E ) were determined by the ultrasonic pulse-echo method using a 200 MHz ultrasonic pulser-receiver (5900 PR; Panametrics, Waltham, MA, USA), 20 MHz longitudinal and shear transducers with a delay material, and a coupling paste (Panametrics) applied between the specimen and transducer. The time of flight of ultrasonic pulse was measured with an oscilloscope (TDS 1002; Tektronix, Shanghai, China) and the thickness of the specimen was measured with a digital micrometer (Mitutoyo). Sonic velocities were calculated as two times the thickness divided by the time of flight, since in the pulse-echo method only one transducer (longitudinal or shear mode) was used to emit and capture the back-reflected wave. ν and E values were calculated using the equations:
ν = 0.5 V l 2 − 2 V t 2 V l 2 − V t 2
E = ρ 3 V t 2 V l 2 − 4 V t 4 V l 2 − V t 2
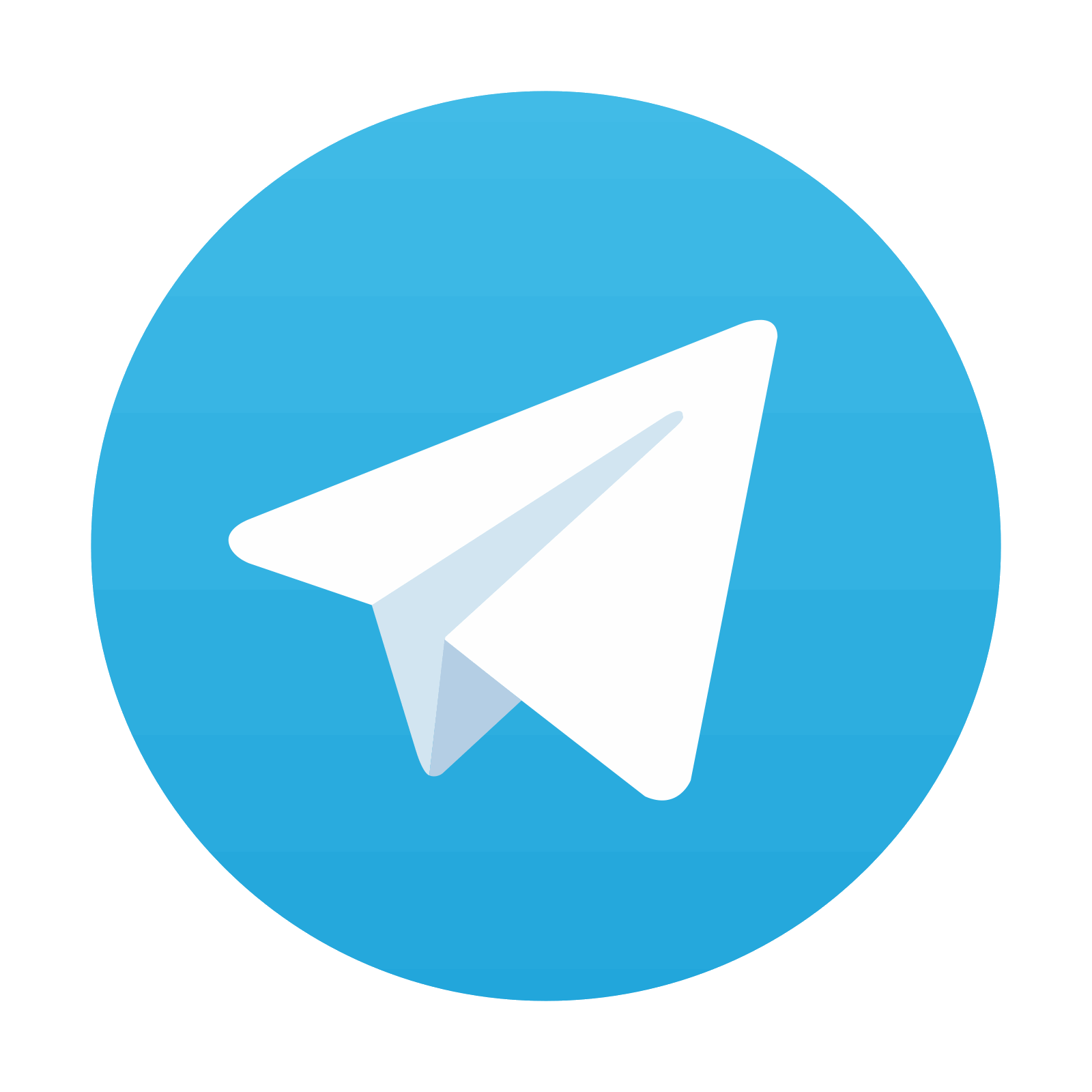
Stay updated, free dental videos. Join our Telegram channel

VIDEdental - Online dental courses
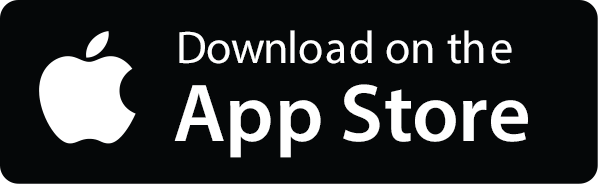
