Outline
What Are Mechanical Properties?
Stress-Strain Properties
Other Strength Test Methods
Fracture of Restorations
Properties of Surface Interactions
Strength of Tooth Structure
Selection of Dental Materials
Key Terms
Brittle Relative inability of a material to deform plastically before it fractures.
Deformation Change in dimension caused by force application. If the deformation recovers when the force is removed, it is called elastic deformation. If deformation does not recover completely when the force is removed, the amount of deformation that does not recover is called permanent or plastic deformation.
Ductility The amount of plastic deformation a material can sustain under tension before fracture. This property is reported quantitatively as percent elongation.
Elastic limit Magnitude of elastic stress above which plastic deformation occurs.
Elastic modulus (also modulus of elasticity and Young’s modulus) Resistance to elastic deformation of a material by force that is calculated as the ratio of elastic stress to elastic strain.
Fracture toughness The critical stress-intensity factor at the point of rapid crack propagation in a solid containing a crack of known shape and size.
Hardness Resistance of the surface of a material to plastic deformation, which is typically produced by forcing a pointed or spherical indenter on the surface.
Malleability Ability to be hammered or compressed plastically into thin sheets without fracture.
Pressure Force per unit area acting on the surface of a material. This is different from stress, which refers to the distribution of force within the material.
Proportional limit Magnitude of elastic stress below which stress remains proportional to strain on a stress-strain curve.
Resilience The amount of elastic energy per unit volume that is sustained on loading and released on unloading of a test specimen.
Strain Change in dimension per unit initial dimension. In mechanical testing, the change in length is used. There are elastic strain and plastic strain.
Strain hardening (work hardening) Increase in strength and hardness and decrease in ductility of a metal that result from plastic deformation.
Strength (1) Stress at the point the material fractures; depending on method of loading, there are tensile, compressive, shear, torsional, flexural, and impact strengths. (2) Maximum stress that a structure can withstand without sustaining a specific amount of plastic strain; this is known as yield strength or proof stress .
Stress Force per unit area within a structure subjected to a force; depending on the direction of force relative to the object, there are tensile, compressive, and shear stresses.
Stress concentration Area or point of significantly higher stress that occurs because of a structural discontinuity such as a crack or pore or a marked change in dimension.
Stress intensity (stress intensity factor) Relative increase in stress at the tip of a crack of given shape and size when the crack surfaces are displaced in the opening mode (also known as fracture toughness ).
Toughness Ability of a material to absorb elastic energy and deform plastically before fracturing; measured as the total area under a plot of tensile stress versus strain.
Tribology The study and application of the principles of friction, wear, and lubrication.
True stress Ratio of applied force to the actual (true) cross-sectional area; however, for convenience, stress is often calculated as the ratio of applied force to the initial cross-sectional area.
Yield strength The stress at which a test specimen exhibits a specific amount of plastic strain.
We learned in Chapter 1, Indirect Restorative Materials , that partially edentulous patients may receive removable partial dentures (RPDs) when the construction of a fixed bridge is not the best treatment option. You will learn later that RPDs are retained and supported by abutment teeth, to which they are attached by clasps, which are often made of alloys as the frameworks ( Figure 1-12 ). Figure 4-1 illustrates the stages of seating a clasp to an abutment tooth. The dotted patches represent the cross sections of the clasp as it is being seated. The greatest convexity or bulge, farthest from the axis of the tooth, is called the height of contour of the tooth. The area that is recessed relative to the height of the contour of the tooth or recessed relative to any part of the tooth surface is known as the undercut. The clasp that engages an undercut area on the abutment tooth for the purpose of retention is known as a retentive clasp. The clasp opposite the retentive clasp, which engages the surface area occlusal to the height of contour of the tooth, is known as the reciprocal clasp. Greater than 180° encirclement of the abutment tooth allows for stabilization of the RPD.

During the insertion of the device, the patient positions the clasps above their respective abutment teeth (position A in Figure 4-1 ) and forces the device to seat completely, which requires the clasp to traverse. This design means that the retentive clasp arm must flex open to slide past the height of contour of the tooth (position B in Figure 4-1 ), and then flexes back to engage the undercut area (position C in Figure 4-1 ). Meanwhile, the reciprocal clasp will properly engage the tooth above the height of contour (position C in Figure 4-1 ).
After wearing the device over some period of time, the patient begins to notice that the RPD is no longer retentive and moves up and down during chewing. The dentist will recognize that most likely, the retentive clasp has lost adaptation to the tooth surface because of deformation, resulting from repeated insertion and removal followed by chewing on the device. For metallic clasps, the dentist will use a pair of pliers to adjust the clasp to the original position by bending. The process can be repeated whenever the device becomes loose again, but there is a limit to the number of times the clasp can be bent. Eventually, the clasp breaks during adjustment.
This sequence of events illustrates how a material responds to applied force through changes of configuration. First, the clasp flexes slightly to slide over the height of contour and returns to the initial dimension to engage the undercut. A material is an elastic solid, or is said to behave elastically, when it exhibits the ability to deform (change in configuration) under an applied force and regain the original shape and size when the force is removed. When the clasps become loose because of permanent deformation after a period of service, they are adjusted to restore their original configuration. Plasticity is the ability of solids to change shape permanently when subjected to forces without rupture, whereas the quantity of permanent deformation the clasp can sustain before rupture is known as ductility. This sequence can also be demonstrated by flexing an orthodontic wire (elastic deformation), bending the wire further to make a 90° angle (plastic deformation), and bending back and forth several times at the same bend until the wire breaks.
The focus of this chapter is to describe the mechanical characteristics of these materials and discuss the basic principles behind these mechanical properties.
What Are Mechanical Properties?
We can perform the same exercises on a series of solid materials of any size and shape and label them as stiff or flexible, hard or soft, brittle or ductile, and fragile or tough , based on the materials’ responses. A brittle material is one that fractures without exhibiting plastic deformation. These descriptions are known as mechanical properties because they characterize a material’s resistance to elastic deformation, plastic deformation, or fracture under an applied force. However, these are qualitative terms that do not indicate how similar or dissimilar materials of the same type may be. To enable clinicians to select appropriate materials, their mechanical properties must be defined and quantified. For this purpose, the direction of force being applied, along with the magnitude of the force and the area of contact with the material, must be known. We also need to define the parameters measuring the deformation exhibited by the material and the resistance of the material to plastic deformation or fracture under a force. The parameters used for these purposes are stress, strain, and strength.
Stress
Force, as defined in Chapter 1, What Is Force , is the interaction of one object with another during actions of push or pull, and the quantity of force is measured using the unit of newton (N). Take the bending clasp as an example; our hand is one object bending the clasp (second object) to induce plastic deformation (adjustment) of the clasp. We can treat that action like we apply a force on an object. Newton’s third law of motion states that when an external force acts on a solid, a reaction occurs to oppose this force, which is equal in magnitude but opposite in direction to the external force. That reaction force from the material is the resistance we feel during the interaction.
In Figure 4-2, A , a block of material weighing 20 kg is hung to the ceiling by a wire with a cross-sectional area of 7 mm 2 . The weight stretches the wire slightly, which generates internal forces between atoms. The gravitational force exerted on the wire with a mass of 1 kg is about 9.8 N. We can reasonably assume that the distribution of the internal forces over the cross section of the wire is uniform. The stress (σ), by definition, is the exerted force per unit area perpendicular to the force direction:
=12⋅σ2E⋅V

The International System (SI) unit of stress is N/m 2 and is known as a pascal (Pa). Because the unit of Pa, as defined, is very small, MPa for megapascal (= 10 6 pascals) is customarily used. In the present example, the stress in the wire is 28 MPa in tensile mode. The weight of the wire is insignificant relative to the force applied and is usually ignored in the calculation.
When the same block is placed on a supporting post with a cross-sectional area of 140 mm 2 ( Figure 4-2, B ), calculation shows that the stress within the post is 1.4 MPa in compression mode. The force applied at the top of the post divided by the contact area has the same value as the stress, but this value is known as pressure (p) because this is the force or load that is exerted on the outer surface and not within the supporting post.
The stresses developed according to the nature of the applied forces and the object’s shape are tensile, compressive, and shear stresses ( Figure 4-2 ).
Tensile Stress
Figure 4-2, A shows the mode of tension along the long axis of a wire where a pair of forces is pulling away along the wire axially. The two forces are the weight of the block and the reaction force from the ceiling. The stress generated in the wire is tensile stress and should be the same throughout the entire wire if the cross-sectional area is uniform. You can roll up a sheet of rubber dam and generate tensile stress within the roll by pulling at both ends.
Compressive Stress
When the post is resting on a surface, there is a reaction force from the surface pushing upward ( Figure 4-2, B ), which illustrates the mode of compression along the long axis of the post. The stress generated within the post is known as compressive stress. The contact area of the supporting surface is also under compressive loading from the post, except that the compressive stress generated within the supporting material is dispersed beyond the area of contact, laterally and vertically. The stress is higher under the area of contact and decreases with distance from the area of contact. This pattern is known as stress distribution or stress gradient . When a patient bites a bolus of food between an upper and a lower tooth, both teeth are exposed to compressive load and undergo compressive stress.
Shear Stress
When a bar is fixed at one end of a panel ( Figure 4-2, C ) and downward force perpendicular to the long axis of the bar is applied along the surface of the panel, there is an upward reaction force from the panel, which acts on the bottom of the bar. Note that the direction of the reaction force is opposite to that of the applied force but not along the same path. This is a characteristic of shear force. The shear stress of the section of the bar that is experiencing the shear force is divided by the cross section of the area. In orthodontic treatment, the wire delivers forces to brackets; the horizontal component of the force relative to the bonded enamel surface will generate shear stress within the bracket and within the resin bonding cement. Debonding may occur by shear-stress failure of the bonding cement. Debonding of the brackets can also be achieved by twisting the bracket with orthodontic pliers. This mode of action is called torsion, where the plier functions as a lever. This action is the torque that debonds the bracket. Note that the force applied through the pliers is to rotate the bracket, and the length of the pliers enhances the tendency to twist the bracket. Therefore, the tendency is not measured by force but moment, which is the force multiplied by the length of the pliers. Moment and torque are like forces that can cause the objects to move; the difference is that they can be amplified with the help of a longer lever.
If the downward force applied on the bar is away from the panel, the stress developed within the bar is no longer purely shear stress but also includes additional tensile and compressive stresses as the bar bends. More on this phenomenon is discussed in the section on flexure tests.
Combined Stresses
For complex objects, such as three-unit fixed dental prostheses (FDPs; Figure 4-3, A ) and two-unit cantilever FDPs ( Figure 4-3, B ), the stresses generated in these devices are different from those in the simple objects shown in Figure 4-2 . As the patient chews, the masticatory load causes the pontic to bend toward the tissue even though the change is not visually detectable. In the three-unit FDP, the bending causes the pontic to become concave (contract slightly) and the tissue side to become convex (stretch slightly). Therefore there is compressive stress on the occlusal side and tensile stress on the tissue side. Both stresses concentrate at the connector because of the smaller cross-sectional area than that of the pontic. In the case of cantilevered FDPs, the unsupported end will bend the most, leaving the occlusal surface convex and the tissue side concave. Therefore there is tensile stress on the occlusal side and compressive stress on the tissue side. Both stresses will also concentrate at the connector area. Note that there is a moment acting on the abutment tooth in the occlusal-gingival direction that could result in failure of the cement and loosening of the prosthesis. A longer span of the FDP will place more burden on the cementing medium.

Dental restorations and devices in the oral cavity may be subjected to tension, compression, shear, torsion, or bending. The types of stresses developed within the restoration or devices would likely be a combination of tensile, compressive, and shear stresses.
Strain
Materials respond to forces through changing shape or dimension. Deformation resulting from tensile or compressive forces is one dimension that can be measured directly. The ratio of the change in length, ΔL, divided by the original length, L 0 , is the strain (ε) of that material under a given load. If the wire in Figure 4-2, A is 100 mm long before loading and increases by 0.5 mm (ΔL = 0.5 mm) when loaded, the strain is as follows:
ε=ΔLL0=0.5mm100mm=0.005=0.5%
We can conclude that the wire reaches a stress of 28 MPa with a tensile strain of 0.5%. When the load is removed, and the length of wire recovers to 100 mm, the wire exhibits all elastic strain under the weight. If the wire does not recover completely when the load is removed and registers a length of 100.2 mm (ΔL = 0.2 mm), the strain value will be 0.2%, which is the plastic strain the weight caused. The difference between the two values is 0.3%, which is the maximum elastic strain of the wire. Maximum elastic strain is also called flexibility and is discussed in detail later in the chapter.
When we add more weight to the wire until the breaking point, and the total length of the two broken wires is 101.3 mm (ΔL = 1.3 mm), this means that the wire sustained 1.3% of plastic deformation at fracture. Keep in mind that when the wire breaks, the elastic strain vanishes because there is no stress in either piece of the wire. The value obtained is also called elongation or ductility. The clinical relevance of this property is discussed later in the chapter. Note that strain is a dimensionless quantity; units such as meter per meter or centimeter per centimeter are often used to remind one of the system of units employed in the actual measurement. The accepted equivalent in the English system is inch per inch, foot per foot, and so forth.
By now you should realize that whenever there is a stress applied on a material, the material should exhibit a corresponding strain. The relationship between stress and strain during the elastic deformation is the elastic property of the material and is discussed in detail in the next segment.
Strength
The stress and strain of a material under load was defined earlier. The challenging nature of the oral cavity, to which dental materials are subjected, was presented in Chapter 1 (Challenges of Dental Materials in the Oral Cavity) . How can it be known if dental materials can survive in this harsh environment? Clinicians must use a material and decide on the dimensions of the restoration or prosthesis in such way that the material will safely withstand various occlusal-loading conditions. For specific dental materials, we are equally interested in the maximum stress that a structure can sustain before this material becomes plastically deformed and subsequently fractures. For this purpose, having information regarding the elastic properties and strength characteristics of materials under various stress conditions, which were discussed earlier, is imperative. Strength is the stress necessary to cause either a specified amount of plastic deformation (i.e., yield strength) or fracture (i.e., breaking strength) of the material. The term elastic properties refers to the stress-strain relationship during elastic deformation. Hooke’s law of elasticity, also known as Hooke’s law, states that the stretching of a solid body (e.g., metal, wood) is proportional to the force applied to this structure when the material behaves elastically. There is, however, a limit for each material, and this linear relationship is known as the proportional limit. These strength properties will be discussed in detail, along with their clinical significance, later in the chapter.
Information on the elastic properties and strength of materials can be obtained only through experimental investigations that use well-defined, well-configured, and standardized specimens, and subject these to comparatively simple stress conditions. Testing machines are designed to induce certain typical deformations of test specimens, such as tension, compression, shear, torsion, and bending (flexure). They also record the forces applied and the deformation the test specimens can sustain until fracture occurs. The maximum load recorded before the fracture of the specimen and the original dimension of the specimen are used to calculate tensile strength, compressive strength, shear strength, torsional strength, and flexural strength. For each dental material where strength values are needed as part of the specification, there are testing protocols established by TC 106−Dentistry of the International Organization for Standardization (ISO). Following these protocols is important for the standardization of testing methods.
Figure 4-4 shows a material represented by six rows of atoms under different states of shear stress. The zigzag line indicates the plane where the movement between rows of atoms would occur and is called the slip plane. The atoms on either side of the slip plane are shaded differently for contrast. Figure 4-4, A shows the relative locations of labeled atoms without stress. When a pair of forces from opposite directions acts on the top and bottom rows of the material, thereby subjecting the material to shear forces ( Figure 4-4, B ), the positions of the atoms shift in response to the shear stress generated within the material. Note the change in position between atoms a and b; atoms 1, 2, and 3; and atoms 4, 5, and 6. The overall change is the elastic shear strain, which will return to zero when the shear force is removed ( Figure 4-4, A ). If the shear force is increased sufficiently to move the atoms in row “a” farther to a new stable position, and then removed, a permanent slip (plastic deformation) along the slip plane occurs ( Figure 4-4, D ).

If the pair of forces is applied to the row of atoms directly above and below the slip plane ( Figure 4-2, C ), the relative position shift of atoms a and b will appear similar to the displacement seen in Figure 4-4, B , but the relative positions of atoms farther above the slip plane, such as 1, 2, and 3, and atoms farther below the slip plane, such as 4, 5, and 6, will remain the same ( Figure 4-4, C ). As the shear force is increased and then removed when the row of atoms moves to the next stable position, the arrangement of atoms will register the same permanent deformation ( Figure 4-4, D ). Recall the discussion of moment of force. When the force is applied at a distance from the interface ( Figure 4-4, B ), the moment increases; therefore less force is needed to induce the same plastic deformation. This is the reason most shear tests for bonding systems do not truly measure shear bond strength.
Stress-Strain Properties
Figure 4-5 shows a stress-strain graph for a stainless-steel orthodontic wire that has been subjected to a tensile force. The solid orange line shows the stress (σ) obtained from forces divided by the cross-sectional area as the strain (ε) increases from stretching. The shape of the curve is typical for a tensile test. As the test begins, the stress-strain curve moves linearly toward the upper right, then starts to deviate from a straight line after passing the proportional limit (PL). The upward or y -axis movement is further reduced as the graph moves past the yield strength (YS). As the movement continues farther to the right, the line reaches a plateau at the ultimate tensile strength (UTS) and eventually breaks at a lower stress at the breaking strength (BS).

Imagine that we are in control of the tensile testing machine and observe the stress-strain plot recording in real time on the screen. Let us stop the experiment before the stress reaches PL and unload the wire; we will observe that the curve traces back to the zero stress and strain as the wire completes the elastic recovery to the original length. The linear segment of the curve is the graphical illustration of Hooke’s law of elasticity. We can restart the test, and then stop immediately after the stress-strain curve has passed the proportional limit and unload. We still observe complete elastic recovery of the wire, which indicates that Hooke’s law does not apply beyond the proportional limit, but the material deformation at that stress level remains elastic only. This process can be repeated with increasing stress levels and soon reach a point where the wire still exhibits elastic recovery but does not revert back to the original length, thereby exhibiting plastic deformation. Meanwhile, the rate of stress increase with respect to the strain reduces substantially. Normally, we describe that the stress has exceeded the elastic limit of the material, which is the stress level when plastic deformation occurs. Unfortunately, there is no notable feature on the curve that enables us to identify the stress level of the elastic limit. To find a convenient and practical substitute, we commonly draw a line parallel to the straight portion of the curve, starting at a value of 0.2%, along the strain axis and extend it until this line intersects with the curve. This stress value is designated the 0.2% offset yield strength or proof stress. The significance of yield strength will be discussed later. From this point on, more plastic deformation of the wire develops after each stretch and unload. The stress then reaches a maximum value at the ultimate tensile strength, and the wire begins to show signs of necking, which is a reduction of the diameter in one area of the wire (specimen illustration in Figure 4-5 ). As stretching continues, the level of stress decreases until the wire fractures at the breaking strength, with all the plastic deformation that occurred after the ultimate tensile strength concentrating around the area of necking.
Proportional Limit, Elastic Limit, and Yield Strength (Proof Stress)
When a wire is stretched steadily in tension, the wire eventually fractures. However, in dentistry, we are also interested in the stress at which plastic deformation begins to develop, which is called the yield point. Softer metals and thermoplastic polymers show a pronounced yield point ( Figure 4-6 ). This occurs at slightly higher stress levels than the elastic limit. At the yield point, the material shows a sudden increase of strain with no increase in stress. Materials specific for dental applications do not usually exhibit this behavior ( Figure 4-5 ); thus a different approach is needed to determine the yield point.

For a material that satisfies Hooke’s law, the elastic stress must be directly proportional to the elastic strain. Graphically, the initial region of the stress-strain plot must be a straight line, as shown in Figure 4-5 . In fact, a small portion of the elastic deformation appears to be nonlinear before the onset of plastic deformation, which is demonstrated by the curve deviation from the straight line. The point of deviation is called the proportional limit, which represents the maximum stress above which stress is no longer proportional to strain.
When a small tensile stress is induced in a wire, the wire will return to the original length when the load is removed. If the load is increased progressively in small increments, and then released after each increase in stress, a stress value will be reached at which the wire does not return to the original length after the load is removed. At this point, the wire has been stressed beyond the material’s elastic limit, which is the greatest stress to which the material can be subjected to where the material will return to the original dimensions when the force is released. The value of the elastic limit, when available, is used as the yield point of the material. As discussed earlier, a stress-strain curve, such as that shown in Figure 4-5 , does not show the stress of the elastic limit. However, for certain materials, experiments have shown that the stress values of the elastic limit are very close to their respective proportional limits. For those materials, the use of the values of the proportional limit as the yield point is customary.
Yield strength is a commonly reported property for metals and alloys but not for ceramics. Why is it not possible to measure the yield strength of ceramics or other purely brittle materials? Use a stress-strain plot to explain your answer.
For materials such as stainless steel, a good portion of the elastic deformation appears nonlinear, so the use of the proportional limit as the yield point is inappropriate. In addition, irregularities along the straight-line region of the stress-versus-strain plot may represent minor deviations from Hooke’s law and cause some uncertainty in determining the appropriate point at which the selected line deviates from linearity (proportional limit). Thus a different property, yield strength, is used in cases where the proportional limit cannot be determined with sufficient accuracy.
Yield strength is a property that represents the stress value at which a small amount of plastic strain has occurred. A value of either 0.1% or 0.2% of the plastic strain is often selected and is referred to as the percent offset. As in Figure 4-5 , the yield strength for 0.2% offset is illustrated. If yield-strength values for two materials tested under the same conditions are to be compared, identical offset values should be used. For brittle materials such as dental ceramics, the stress-strain plot is a straight line with no appreciable plastic region. Thus a determination of yield strength is not practical at either a 0.1% or 0.2% strain offset because there is no plastic strain.
Proportional limit, elastic limit, and yield strength (proof stress) are defined differently for the respective phenomena that occur during mechanical testing. However, they have been used interchangeably when referring to the yield point. Their values are usually very close but can be different in some cases. The elastic limit is the true yield point when this value is available. The proportional limit is used as the yield point when the proportional limit is well defined on the stress-strain curve and known to be close to the elastic limit. The yield strength is easy to obtain from a stress-strain curve with a preset amount of plastic deformation. Remember that the yield strength is defined with some plastic deformation in mind, but the proportional and elastic limits cover elastic deformation only. As shown in Figure 4-5 , the yield strength (proof stress) is greater than the proportional limit. These values are important in the selection of dental materials because they represent the stress at which permanent deformation of the structure begins. If stresses generated during chewing exceed these values, the restoration or appliance may become distorted and no longer function as originally designed.
Imagine a patient biting on a bolus of food, as shown in Figure 4-3 , exerting enough load to generate tensile stresses at the area noted as tension of the bridge alloy. As the patient gradually applies the load, the tensile stress in these areas will increase proportionally to the magnitude of the load applied. If the stress generated is below the elastic limit and up to the proportional limit, the removal of the load will always result in an elastic recovery of the bridge from the slight bending that occurs. If the patient at any time exerts a load that creates stresses in the tension area that are equal to or exceed the elastic limit of the material used, the bridge will be permanently deformed, and then break. Accordingly, one must choose materials with adequately high elastic limits for the construction of a dental bridge. If the size of the connector is too small, greater tensile stress is generated. A properly designed restoration is also important.
Elastic Modulus (Young’s Modulus or Modulus of Elasticity)
Hooke’s law states that stress and strain change proportionally within the region of elastic deformation. Mathematically, there is a constant between the stress and the strain. We call this constant the elastic modulus, modulus of elasticity, or Young’s modulus, designated by the letter E . The elastic modulus (E) of the orthodontic wire used in Figure 4-5 can be calculated as follows using the proportional limit (1018 MPa) and the elastic strain (0.0053) of this material:
E=StressStrain=σε=1018MPa0.0053=192,075MPa=192GPa
Because the elastic modulus represents the ratio of the elastic stress to the elastic strain, we can reason that the lower the strain recorded for a given stress, the greater the value of the modulus. For example, if wire A is much more difficult to bend than wire B of the same shape and size, considerably higher stress must be induced before a desired elastic deformation can be produced. As such, wire A is considered to have a comparatively higher modulus of elasticity than wire B. Thus wire A, with a higher modulus of elasticity, stretches less than wire B under the same stress. Elastomeric impression materials have a greater stiffness (elastic modulus) than alginate-based impression materials. Thus a greater force is needed to remove an elastomeric impression tray from undercut areas in the mouth. The modulus of elasticity of most dental biomaterials is given in units of either MPa or GPa (gigapascals; 1 GPa = 1000 MPa).
In general usage, the term elasticity also implies “being easily stretched or expanded,” which contradicts what we just learned: that a material with a high elastic modulus requires more force to deform. In fact, elasticity in solid mechanics describes the ability of a strained body to recover this body’s original size and shape after deformation. This statement does not imply if straining the material is easy or difficult based on the stress applied. Therefore the elastic modulus is a parameter that quantifies the elastic behavior. We can also state that the elastic modulus describes the relationship between stress and strain within the elastic region. Some would state that the elastic modulus is the slope of the initial straight portion of the stress-strain curve. The steeper the line, the higher the elastic modulus and the stiffer the material. As such, the elastic modulus has been considered a measurement of the stiffness or rigidity of a material.
Recall Figure 2-2, A , in which bond force is defined as the attraction between two atoms, and Figure 4-4, B , which shows the distance between atoms under the influence of shear stress, such as the distance between atoms 2 and 3 and between atoms 4 and 5. The zero resultant force at equilibrium represents the material that is not under stress. The change in distance between atoms increases with respect to the external force applied and should follow the curve of resultant force in Figure 2-2 . The slope of resultant force drawn from the equilibrium position will have the same meaning as the slope of the stress-strain curve. Because the force needed to change the distance between atoms depends on the bond strength between atoms, the value of the elastic modulus reflects the atomic bond strength of the material, which remains constant and independent of mechanical treatment, such as the stress applied, and the plastic deformation incurred during the test.
Figure 4-7 shows a stress-strain graph for enamel and dentin that have been subjected to compressive stress. These curves were constructed from the typical values of elastic moduli, proportional limit, and ultimate compressive strength reported in the scientific literature. Variations in the values of the proportional limit, elastic modulus, and ultimate compressive strength have been reported for enamel and dentin relative to the area of the tooth from which the test specimens were obtained. Note that the proportional limit, ultimate compressive strength, and elastic modulus of enamel are greater than the corresponding values for dentin ( Figure 4-7 ). The elastic modulus of enamel is about three times that of dentin in this study. Dentin can sustain more plastic deformation than enamel under compressive loading before dentin fractures. Thus enamel is a stiffer and more brittle material than dentin, and unsupported enamel is more susceptible to fracture. Conversely, dentin is more flexible and tougher. Although there is no quantifiable measurement for the brittleness of a material, we often describe materials as being more brittle or less brittle. We refer to more brittle materials as having less elastic deformation before fracture and less brittle materials as having more elastic deformation before fracture.

Recall Figure 3-2 , which shows a Newtonian fluid exhibiting a linear relationship between the shear stress and strain rate of the fluid, and the slope of the curve is defined as the viscosity of the liquid. Figure 4-5 shows that there is a linear relationship between the tensile stress and strain of a solid, and the slope defines the elastic modulus of a solid. Both terms are derived from the stress and strain relationship; they represent two different properties. The elastic modulus is the quantity that dictates how much the material will deform elastically for a given stress and remain at that state forever unless the stress is removed, at which time, the material returns to its initial shape. The viscosity is the analogous quantity that shows how fast the material will flow and the change of strain in proportion to the duration that the stress is applied.
How can the ultimate tensile stress (ultimate strength) sometimes be less than the maximum tensile stress?
Ultimate Strength and True Strength
Ultimate strength for tensile, compressive, and shear tests is calculated by dividing the maximum force recorded before fracture by the original cross-sectional area of the material. The specimen configuration shown in Figure 4-5 demonstrates that the cross section of the wire decreases as the wire lengthens under tensile stress. Because of the reduction in area, the force required to increase deformation decreases. Thus the stress calculated past the ultimate tensile strength decreases, leading to a breaking strength that is lower than the ultimate tensile strength. Figure 4-8 shows a stress-strain plot of a metal rod that has been subjected to a tensile test. The stress is calculated using the original cross-sectional area (orange line) and the actual cross-sectional area (green line). The stress value, calculated as the force divided by the actual cross-sectional area at each measured strain value, is known as true stress. The green line shows that the ultimate tensile strength and breaking strength are the same. The original dimension is always used to calculate the various strength values reported—and for good reason. The failure of a restoration or device means that either yielding or rupture has occurred, whichever came first. Damage has occurred at a lower load, and therefore a higher and more precise value of true ultimate strength is not meaningful.

Figure 4-8 demonstrates that after a metal rod has been stressed beyond this material’s yield point, the stress needs to increase to continue exerting plastic deformation until fracture of the specimen occurs. One may think that the material has a fixed yield point; once the stress applied has overcome that barrier, the same level of stress should be enough to induce further plastic deformation until the specimen fractures. The true stress of Figure 4-8 shows that the material that has been plastically deformed is resisting further yielding because more stress is required. Indeed, the material becomes stronger with respect to resisting further plastic deformation, as it is plastically deformed until it fractures, and this phenomenon is known as strain hardening, work hardening, or cold working . We will learn the mechanism of material strengthening by plastic deformation in Chapter 9, Dislocation Movement in Polycrystalline Alloys .
Flexibility and Ductility
From the stress-strain curve, we know that for each stress value, there is a corresponding strain value. Having a material with sufficient strength to resist plastic deformation or fracture is not the only consideration for selection. However, there are instances where elastic and plastic deformation are critical. For example, in an orthodontic appliance, a spring is often extended a considerable distance under the influence of a small stress. In such a case, the structure is said to be flexible and possesses the property of flexibility. Flexibility is defined as the elastic strain shown on a stress-strain curve ( Figure 4-8 ) or the reversible flexural strain of a bending test. Ductility represents the amount of permanent deformation a material can sustain under a tensile load up to the point of fracture, which is the deformation from the proportional limit to the breaking strength in Figure 4-8 . Malleability is the amount of permanent deformation a material can sustain without rupture under compression, such as hammering or rolling a metal rod into a thin sheet. Gold is the most ductile and malleable pure metal, followed by silver. Of the metals of interest in dentistry, platinum ranks third in ductility, and copper ranks third in malleability.
Ductility can be determined in one of three ways: (1) the percent elongation after fracture as seen in Figure 4-8 , (2) the reduction in area of tensile test specimens, and (3) the maximum number of bends performed in a cold-bend test before the wire fractures. The first method involves taking the information directly from a stress-strain curve. The second method involves necking at the fractured end of a ductile metal wire after rupture under a tensile load. The percent decrease in cross-sectional area of the fractured end in comparison with the original area of the wire or rod is referred to as the relative reduction in area. The third method is known as the cold-bend test . We can bend several orthodontic wires back and forth individually until they all break. The wire that takes the greatest number of bends to break is the most ductile wire.
Burnishing of a cast metal margin to reduce the width of a gap between the crown margin and the tooth surface is a good example of flexibility and ductility at work. Figure 4-9 shows a burnishing procedure of an open metal margin ( Figure 4-9, A ), where a smooth, dull instrument is used as a burnishing tool to press the metal margin against the tooth ( Figure 4-9, B ) and close the marginal gap. This movement is possible as a result of the elastic plus plastic strain of the metal. After the instrument is removed, the margin springs back an amount equal to the total elastic strain ( Figure 4-9, C ). Because at least 25 μm of space must be provided for the cement between the tooth and the crown, total burnishing on the tooth or die is usually adequate because the amount of elastic strain recovery is relatively small. Pushing the margin further while pressing against the tooth to compensate for the anticipated elastic recovery may be required. Naturally, the metal should have relatively high ductility to prevent fracture of the margin during burnishing and moderate yield strength to facilitate the procedure.

Resilience and Toughness
Work is the product of the force times the amount of deformation (distance) through which the force acts. When work is performed on a body, energy is imparted to this body. Consequently, when a dental restoration is deformed, the restoration absorbs energy. If the induced stress is less than the proportional limit (i.e., the oral structure is not permanently deformed), only elastic energy is stored in the structure until the applied force is removed. Resilience ( U r ) is the ability of a material to absorb energy when it is deformed elastically ( Figure 4-8 ). The modulus of resilience is the amount of strain energy that can be absorbed per unit volume without permanent distortion and can be determined by the area of the elastic region:
Ur=12σε=12⋅σ2E⋅
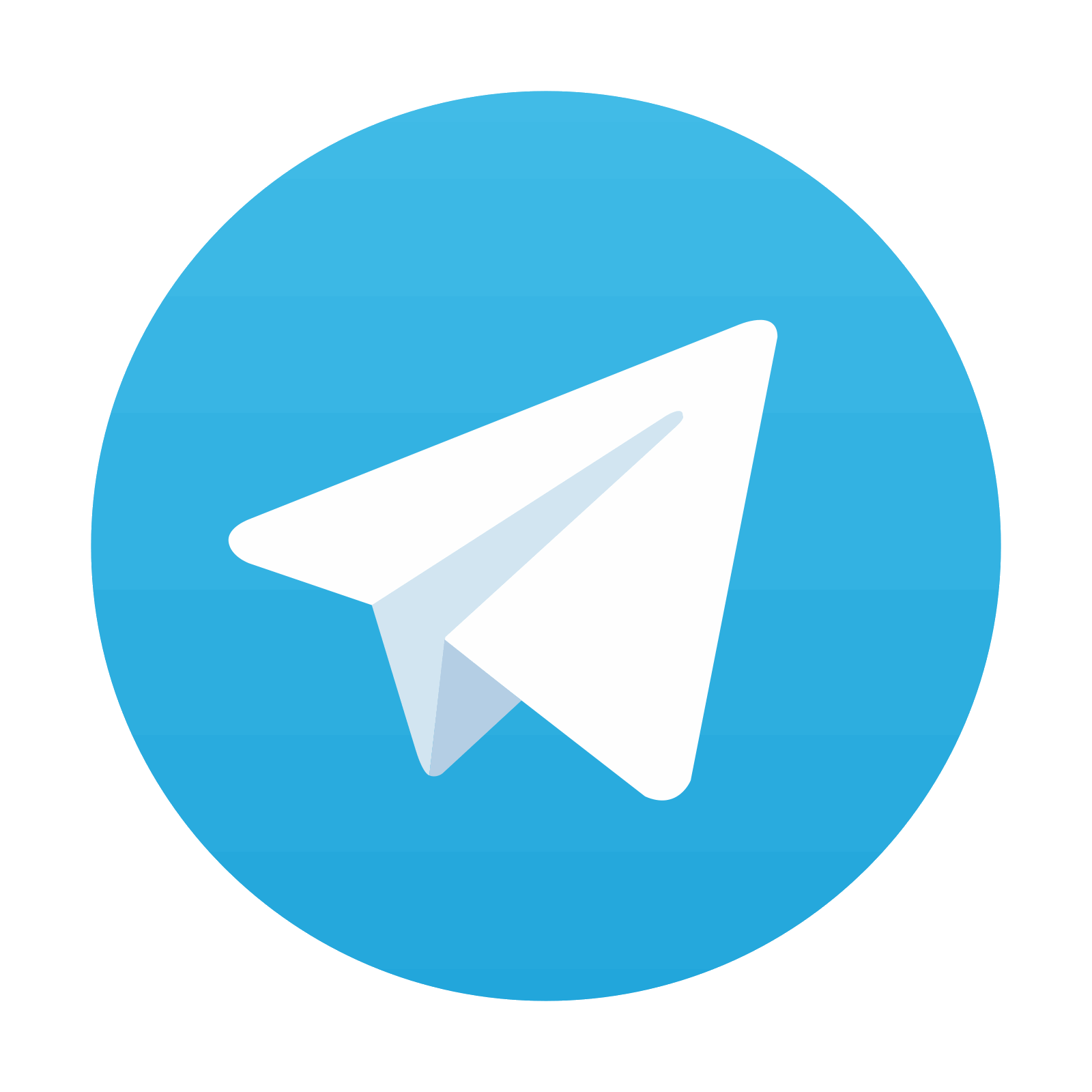
Stay updated, free dental videos. Join our Telegram channel

VIDEdental - Online dental courses
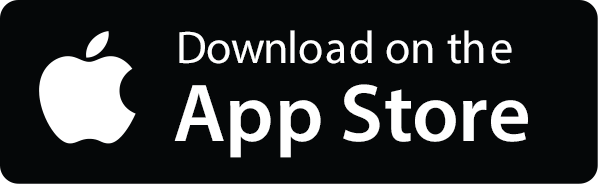

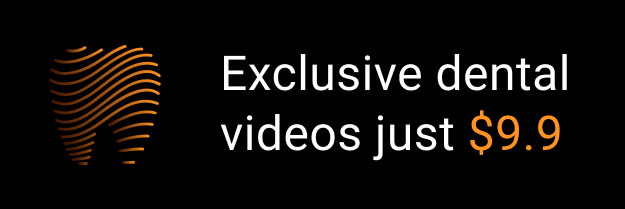