Abstract
Objectives
To investigate the effects of N-vinylcaprolactam (NVC)-containing terpolymers on the fracture toughness, microhardness, and flexural strength of conventional glass-ionomer cements (GIC).
Methods
The terpolymer of acrylic acid (AA)–itaconic acid (IA)–N-vinylcaprolactam (NVC) with 8:1:1 (AA:IA:NVC) molar ratio was synthesized by free radical polymerization and characterized using 1 H NMR and FTIR. Experimental GIC samples were made from a 50% solution of the synthesized terpolymer with Fuji IX powder in a 3.6:1 P/L ratio. Specimens were mixed and fabricated at room temperature. Plane strain fracture toughness ( K Ic ) was measured in accordance with ASTM Standard 399-05. Vickers hardness was determined using a microhardness tester. Flexural strength was measured using samples with dimensions of 2 mm × 2 mm × 20 mm. For all mechanical property tests, specimens were first conditioned in distilled water at 37 °C for 1 day or 1 week. Fracture toughness and flexural strength tests were conducted on a screw-driven universal testing machine using a crosshead speed of 0.5 mm/min. Values of mechanical properties for the experimental GIC were compared with the control group (Fuji IX GIC), using one-way ANOVA and the Tukey multiple range test at α = 0.05.
Results
The NVC-modified GIC exhibited significantly higher fracture toughness compared to the commercially available Fuji IX GIC, along with higher mean values of flexural strength and Vickers hardness, which were not significantly different.
Significance
It was concluded that NVC-containing polymers are capable of enhancing clinically relevant properties for GICs. This new modified glass-ionomer is a promising restorative dental material.
1
Introduction
Glass-ionomer cements (GICs) were invented by Wilson and Kent at the Laboratory of the Government Chemist in 1970 . GICs are well known for properties such as direct adhesion to tooth structure and base metals , anticariogenic properties due to release of fluoride , minimized microleakage at the tooth–enamel interface due to low shrinkage, thermal compatibility with tooth enamel and dentin due to low coefficient of thermal expansion similar to that of tooth structure , biological compatibility, and low cytotoxicity . Besides their advantages they have some disadvantages such as brittleness and inferior mechanical properties. Significant improvements have been made since the invention of the original GIC formulations, and further improvements are required in order to enhance their physical properties .
It has been shown that very close attachments of carboxylic acid groups to the acid polymer backbone result in a very rigid matrix, which causes steric hindrance . During setting of the GIC, not all the carboxylic acid groups will convert to carboxylate groups, and greatly reduced polysalt bridge (Ca 2+ di- and Al 3+ tricarboxylate complexes) formation takes place. In order to overcome this problem, recent studies have incorporated different monomers such as NVP (N-vinylpyrrolidone) and amino acid derivatives as spacers between the carboxylic acid groups. This made the polymeric backbone more flexible and allowed greater access for acid/base reaction (hence greater freedom for COOH groups to react with Al 3+ and Ca 2+ ions), resulting in improved filler–polymer interaction and more complete polysalt bridge formation.
Xie et al. reported that glass-ionomers containing poly(acrylic acid–itaconic acid)–N-vinylpyrrolidone with a 7:3:1 molar ratio showed 85% higher flexural strength compared to Ketac-Molar (a commercially available GIC), with a practical working viscosity. Culbertson and Xie et al. synthesized poly(AA–IA)–NVP with a 7:3:1 molar ratio of monomers and studied the effects of NVP-containing polymers on the fracture toughness and Knoop hardness values of a conventional GIC (Fuji II GC). This group reported that the fracture toughness ( K Ic ) for NVP-containing GIC and Fuji II samples (control group) were 0.607 and 0.557 Mn/m 1/2 , respectively. Additionally, the NVP-containing samples exhibited significantly higher Knoop hardness (KHN) values (84.3 kg/mm 2 ) compared to the Fuji II control group (77.3 kg/mm 2 ) .
N-vinylcaprolactam (NVC) is a chemical analogue of N-vinylpyrrolidone (NVP). Applications of NVC in biomedical materials, stabilization of proteases, and controlled drug delivery and drug release have been published . N-vinylcaprolactam (NVC), which has a ring that consists of seven carbon atoms (one carbon atom more than the NVP ring), can be incorporated in the GIC polyacid structure . Recently, a novel N-vinylcaprolactam (NVC)-containing terpolymer was synthesized and incorporated into a conventional dental GIC (Fuji IX), and the effects of this NVC-containing terpolymer on compressive strength (CS), diametral tensile strength (DTS), and biaxial flexural strength (BFS) were observed ( Table 1 ) . It was shown that incorporation of NVC-containing terpolymers into this GIC formulation had the ability to significantly enhance the strength (CS, DTS and BFS) compared to the unmodified cement . Thus, it was concluded that NVC-containing GIC is a promising restorative dental material. However, it is important to investigate additional clinically relevant mechanical properties for this modified GIC. The present study provides further information about the synthesis and characterization of the terpolymer of acrylic acid, itaconic acid and N-vinylcaprolactam, along with an evaluation of the effects of the NVC-containing terpolymers on fracture toughness, flexural strength and microhardness of the GICs.
GIC group | Compressive strength (MPa) | Diametral tensile strength (MPa) | Biaxial flexural strength (MPa) |
---|---|---|---|
Fuji IX | 1 day: 236 (41.5) | 1 day: 19.6 (11.4) | 1 day: 41.3 (10.5) |
1 week: 248 (36.4) | 1 week: 23.8 (9.8) | 1 week: 42.7 (12.0) | |
(AA-IA-NVC) | 1 day: 303 (32.8) | 1 day: 38.3 (10.9) | 1 day: 82.2 (12.8) |
1 week: 319 (34.1) | 1 week: 44.0 (8.5) | 1week: 84.6 (13.2) |
2
Materials and methods
2.1
Materials
AA (acrylic acid), IA (itaconic acid), NVC (N-vinylcaprolactam), ammonium persulfate [(NH 4 ) 2 S 2 O 8 ], ethyl acetate and methanol were used as received from Sigma–Aldrich Chemical Co. (Milwaukee, WI, USA). The glass powders and polyacid from a commercially available GIC (Fuji IX, GC International, Tokyo, Japan) were used.
2.2
Terpolymer synthesis and characterization
A terpolymer of AA, IA and NVC ( Fig. 1 ) was synthesized by free radical polymerization, following previous methodology that was reported by Yamazaki et al. , Crisp et al. , and Moshaverinia et al. .
0.4 mol (27.43 mL) of AA (1.05 g/cm 3 density), 0.05 mol (6.5 g) of IA and 0.05 mol (6.96 g) of NVC (1.045 g/cm 3 density) were dissolved in 70 mL of distilled water. Ammonium persulfate (2 wt.%) was used as an initiator, and the molar ratio for AA–IA–NVC was 8:1:1. The solution was stirred vigorously and heated to 95–100 °C under a constant flow of nitrogen. Polymerization was allowed to proceed overnight. The terpolymers were diluted and dissolved in anhydrous methanol (Sigma–Aldrich), and precipitated from anhydrous ethyl acetate (Sigma–Aldrich) to remove residual monomers. The synthesized polymer was characterized by 1 H NMR (Burker Analytik GmbH, Germany) and FTIR spectroscopy (PerkinElmer, Shelton, CT, USA).
Structural transformation during heating of the synthesized terpolymer was investigated by differential scanning calorimetry (DSC, Q100, TA Instruments, Wilmington, DE, USA). The test sample was placed in an aluminum pan in one DSC cell, and an empty aluminum pan in the other cell served as the inert control material; nitrogen was used as the purge gas. DSC analyses were performed from −10 to 150 °C at a heating rate of 10 °C/min. The computer software (TA Universal Analysis 2000) for the DSC apparatus plotted and analyzed the thermal analysis curves, and values of heat flow were normalized to sample weight in units of (W/g).
The molecular weight of the terpolymers was measured by gel permeation chromatography (GPC, Class VP, Version 4.2, Shimadzu Corporation, Kyoto, Japan), using two Plgel 5 mm Mixed-D 300 mm × 7.5 mm columns (Polymer Laboratories Inc., Amherst, MA, USA). The values of molecular weight obtained were relative to the polystyrene standards. In order to measure the viscosity of the polymers, 1:1 (wt/wt) mixtures of polymer and distilled water were first prepared. The viscosities of polymers were measured at 25 °C with a cone #6 and plate viscometer (BEL CAP 2000, Brookfield Engineering Laboratories Inc., Stoughton, MA, USA).
2.3
Preparation of glass-ionomer specimens for mechanical testing
Synthesized terpolymers were dissolved in distilled water in a ratio of 1:1 (wt./wt.). As previously noted, Fuji IX GIC glass powder and liquid were utilized, and the powder-to-liquid (P/L) ratio of 3.6/1 recommended by the manufacturer was employed. Specimens were prepared at room temperature following the manufacturers’ instructions. For microhardness testing five samples were made from each material for each storage time at 37 °C (24 h and 1 week). Cylindrical samples ( N = 8) with 6 mm diameter and 3 mm thickness were prepared using a PTFE mold. The molds were filled with the uncured cement mixture and covered with PTFE tape and glass slides, flattened, and gently pressed by hand to remove air bubbles. For flexural strength testing, PTFE rectangular molds were used to prepare specimens with dimensions of 2 mm × 2 mm × 20 mm ( N = 7). The specimens were removed from the molds after 20 min and conditioned in distilled water at 37 °C for 24 h and 1 week. For the fracture toughness measurements, mini-compact disc-shaped specimens with a pre-crack introduced by using a razor blade and having 8 mm diameter × 2 mm thick dimensions were prepared for the NVC-containing glass-ionomer samples and the Fuji IX control group, using a PTFE split mold. The specimen were removed from the molds after 20 min and conditioned in distilled water at 37 °C for 24 h or 1 week.
2.4
Microhardness measurements
The Vickers hardness of the NVC-containing glass-ionomer samples was determined according to the method reported by Gladys et al. and Xie et al. , using a microhardness tester (Model MVK-E, M 400, Leco, St. Joseph, MI, USA). A diamond indenter with 100 g load and a dwell time of 10 s were employed. Each of the five samples was indented two times, and the Vickers hardness number for each sample was calculated according to the following equation:
VHN = 2 L × sin ( / 2 ) d 2
where L = applied load (kg), = angle of 136°, and d = mean diagonal length (mm). Since sin( /2) = 1.8544, the preceding equation is simplified as follows:
VHN = 1.8544 × L d 2
where the Vickers hardness number (VHN) has units of kg/mm 2 . The Vickers hardness values of the Fuji IX samples (commercially available GIC) were evaluated and used as controls.
2.5
Fracture toughness measurements
Plane strain fracture toughness ( K Ic ) was measured using the technique described by Kovarik and Muncy and more recently by Yamazaki et al. , which is in accordance with ASTM Standard 399-05 . Fracture toughness testing was conducted using a screw-driven universal testing machine (Model 4202, Instron Corp., Canton, MA, USA) at a crosshead speed of 0.5 mm/min . The fracture toughness ( K Ic ) of each sample was calculated using the following equation:
K Ic = P c ⋅ f ( a / W ) B ⋅ W 0.5
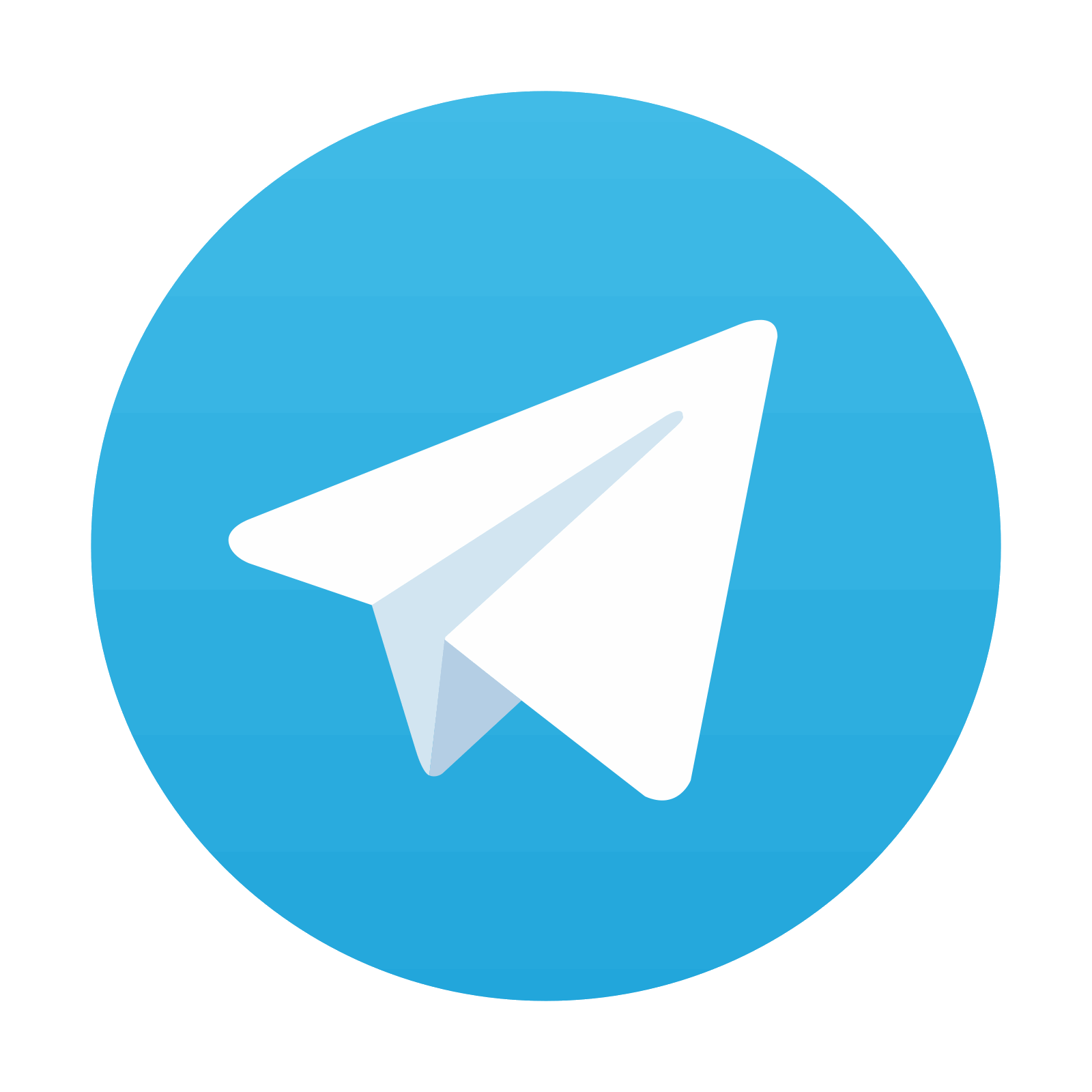
Stay updated, free dental videos. Join our Telegram channel

VIDEdental - Online dental courses
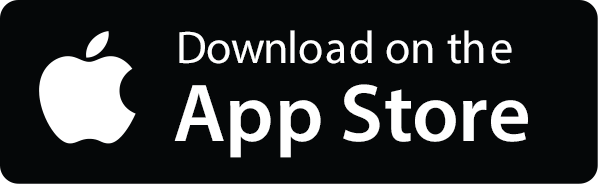
