Abstract
Objectives
Determination of material and fractographic properties of a dental indirect resin composite material.
Methods
A resin composite (Paradigm, 3M-ESPE, MN) was characterized by strength, static elastic modulus, Knoop hardness, fracture toughness and edge toughness. Fractographic analyses of the broken bar surfaces was accomplished with a combination of optical and SEM techniques, and included determination of the type and size of the failure origins, and fracture mirror and branching constants.
Results
The flexure test mean strength ± standard deviation was 145 ± 17 MPa, and edge toughness, T e , was 172 ± 12 N/mm. Knoop hardness was load dependent, with a plateau at 0.99 ± 0.02 GPa. Mirrors in the bar specimens were measured with difficulty, resulting in a mirror constant of approximately 2.6 MPa m 1/2 . Fracture in the bar specimens initiated at equiaxed material flaws that had different filler concentrations that sometimes were accompanied by partial microcracks. Using the measured flaw sizes, which ranged from 35 to 100 μm in size, and using estimates of the stress intensity shape factors, fracture toughness was estimated to be 1.1 ± 0.2 MPa m 1/2 .
Significance
Coupling the flexure tests with fractographic examination enabled identification of the intrinsic strength limiting flaws. The same techniques could be useful in determining if clinical restorations of similar materials fail from the same causes. The existence of a strong load-dependence of the Knoop hardness of the resin composite is not generally mentioned in the literature, and is important for material comparisons and wear evaluation studies. Finally, the edge toughness test was found promising as a quantitative measure of resistance to edge chipping, an important failure mode in this class of materials.
1
Introduction
Resin composites are becoming increasingly important in dentistry, with expanding application resulting from processing and material innovations . Many of the improvements in this class of materials, particularly those stemming from filler particle type and loading increases, are based on material property measurements. Among the published dental composite strength values, however, there is little associated fractographic analysis. This is important, as measured material strength alone is not necessarily indicative of the causes of restoration failure or clinical longevity .
For brittle materials outside the dental field, systematic correlations of strength test values and component performance commonly use fractographic analyses . A study of commercial glass-ceramics, a class of materials widely used in dentistry, determined that different batches had identical elastic moduli, fracture toughnesses, densities and microstructures, but very different failure loads due to a variation in flaw type . Similar examples can be found for alumina-based ceramics . Fractographic examination is essential for critical flaw determination and component strength predictions for brittle materials.
Among brittle materials, highly filled resin composites are somewhat neglected in fractographic analyses . This class of materials falls “in between” polymers and ceramics. Fractographic specialists in either field find features difficult to discern when they are masked by rough microstructures that are often typical in failed composite components . An important but overlooked resource is a 1989 book on fractography of polymers and composites by Roulin-Moloney which includes a chapter on unfilled and filled epoxy resins.
In this study, mechanical property testing and fractographic analysis was applied to a commercial dental composite. The well-characterized stress configuration of a simple bend bar can be very helpful in relating fractographic markings to behavior, especially in an unfamiliar “fractographically difficult” material. The translucency of the material evaluated in the present study initially made examination difficult, but with proper illumination, the relevant features became easy to detect and interpret. Once the correct fracture origin areas were identified by optical microcopy, then scanning electron microscopy was used to characterize the fracture origins. The very fine size of the filler particles also helped since the fracture surface was not too rough. Coarse- or medium-sized fillers lead to very rough fracture surfaces that can mask critical fractographic markings. Property tests also included edge chipping characterization, an important failure mechanism for composite dental restorations . The emphasis of the resin composite property tests and fractography of this study is on practical analyses that could be relevant to failure investigations of resin composite restorations. Our null hypothesis is that fractographic analysis can be used to identify key features associated with the mechanical properties.
2
Materials and methods
2.1
Material
Dental resin composite mill blocks (Paradigm, 3 M ESPE, St. Paul, MN) 1
1 Commercial products and equipment are identified only to specify adequately experimental procedures and does not imply endorsement by the authors, institutions or organizations supporting this work, nor does it imply that they are necessarily the best for the purpose.
were donated by the manufacturer for the property tests. The company literature [e.g., ] lists the material as containing 0.85 mass fraction spherical sol gel derived particles comprising nanocrystalline zirconia in silica. The spherical particles averaged 0.6 μm in size, but had a broad size distribution, within a highly cross-linked polymeric matrix of bis-GMA and TEGDMA. A silane aided bonding to the filler. The flexural strength, σ f , is reported to be 145 ± 15 MPa; fracture toughness, K Ic is 1.3 ± 0.1 MPa m 1/2 ; and a Young’s modulus in compression of about 7 GPa and a flexural modulus of about 12 GPa. The company literature does not include a statement of uncertainty with the material description.
2.2
Strength
Bars ( n = 18) were professionally machined (BOMAS, Somerville, MA) and finished according to the recommendations in ASTM C1161 , which is intended for use with brittle ceramics, but is also useful for brittle filled composites. Because of limitations in the length of the original resin composite cylinder blanks, the final bar sizes of 3 mm × 4 mm × 18 mm were much shorter than the > 40 mm specimen size B specimen lengths in the referenced standard. Small bevels were applied to all four long edges to eliminate any edge damage. Short, stubby bend bars should not be tested in 4-point bending because excessive errors can result , (e.g., from tiny fixture misalignments or wedging stresses at the contact points) so in this instance 3-point was preferred, albeit at the cost of exposing only a tiny portion of the bar to the full tensile stresses. The bars were broken on an Instron Universal Testing Machine (Model 1122, Canton, MA) in 3-point flexure with a crosshead speed of 0.5 mm/min. The semi-articulating, self-aligning fixture had a 16 mm outside roller span and the rollers were free to roll to eliminate friction errors. The fracture stress, σ f , was calculated by the formula:
σ f = 3 P L 2 ( width × heigh t 2 )
where P is the break load and L is the 16 mm span. The specimen widths and heights were measured with a micrometer with a resolution of 0.001 mm. The Weibull parameters were estimated by maximum likelihood estimation (MLE) 2
2 MLE analysis is favored by many and used in many international standards since the confidence band intervals on Weibull parameter estimates are tighter than those from linear regression analysis.
in accordance with ASTM C 1239 .
2.3
Elastic modulus
This property was evaluated by measuring the deflection of the flexural strength bars. The machine compliance was obtained by inserting a large alumina block in the fixtures and repeatedly loading to 100 N. The resulting displacement measurement was assumed to be due entirely to the machine, load cell and fixtures, and was subtracted from the displacement measured in the flexural tests for the same load increment, Δ P , to obtain the displacement solely due to specimen flexure. The static elastic modulus, E , of the resin composite could then be calculated by:
E = Δ P × L 3 4 ( width × heigh t 3 × specimen displacement )
where Δ P is the load differential for a finite specimen displacement taken at midspan.
2.4
Hardness
Knoop hardness values (HK) were obtained using a Wilson/Instron Tukon Model 300 Hardness Machine (Canton, MA). Hardness values of brittle materials generally increase as indentation forces decrease, a phenomenon known as the indentation size effect (ISE) . Because of the ISE, a specified force or functional relationship over a test range is necessary to accurately compare the hardness of brittle dental materials. Hardness measurements were made at forces ranging from 0.25 to 9.8 N, with ten indentations at each force. The hardness at the three highest forces (4.9, 6.9 and 9.8 N) showed no significant difference using Tukey’s multiple pairwise comparison at 99% family confidence level. The combined data from these three loads constitute the reported load-independent hardness. The hardness readings were made in air under room conditions, but ten indentations at 9.8 N were also made on a specimen surface wet with distilled water to determine whether the surface environment and short time exposure to water had any influence on hardness.
2.5
Edge toughness
Edge toughness (also known as edge strength or edge flaking resistance) measures the susceptibility of a material to edge chipping . In this test, an increasing force is applied near the edge of a specimen until a chip is formed. At greater distances from the specimen edge, higher forces are required for chip formation. A plot can be constructed by plotting the force necessary to form a chip against the distance from the specimen edge. The slope of a straight line resulting from such a plot constitutes the edge toughness, T e , although a power law often better fits the edge toughness plot for glasses and porcelains . High values of T e , or steep plots, indicate a material is highly resistant to edge chipping. Low T e values indicate that large chips form at low loads, and the material chips easily. Other indenter shapes are now in use, but we prefer to use a sharp conical indenter since they are inexpensive, easy to replace, and the indentation shape is self similar as indentation load is increased. An Engineering Systems Model CK 10 edge-chip machine (Nottingham, UK), fitted with a conical 120° diamond scribe indenter, was used to form chips and measure forces in this study. The tip was sharp, with a radius of less than 10 μm. More detailed descriptions and photographs of the equipment that was used in the edge chipping test are included in Ref. .
2.6
Fractography
Fractographic examination and measurements were made with a scanning electron microscope (SEM) (JEOL 5300, Peabody, MA) at up to 1500× and a stereoptical microscope (Leica MZ16, Wetzlar, Germany) at up to 92×. The translucency and internal light scattering hampered conventional reflected light optical observation of fracture surface markings so special illumination procedures were required. For optical examinations of the bar specimen fracture surfaces, transillumination was particularly helpful in identifying fracture origins, and oblique lighting on gold-coated surfaces aided fracture mirror boundary delineation. It was critical to have directed illumination from one or two fiber optic light guides (as opposed to a ring light) for these examinations. The optical microscope was equipped with a traveling stage enabling size measurements with a resolution of 1 μm. Additional information about the fractographic techniques and equipment may be found in Ref. .
Fracture mirrors were detected and their sizes measured after the specimen surfaces were gold coated to make the fracture surface easier to interpret. Mirror sizes are related to the fracture stress by Orr’s equation :
σ f = A ( R ) − 1 / 2
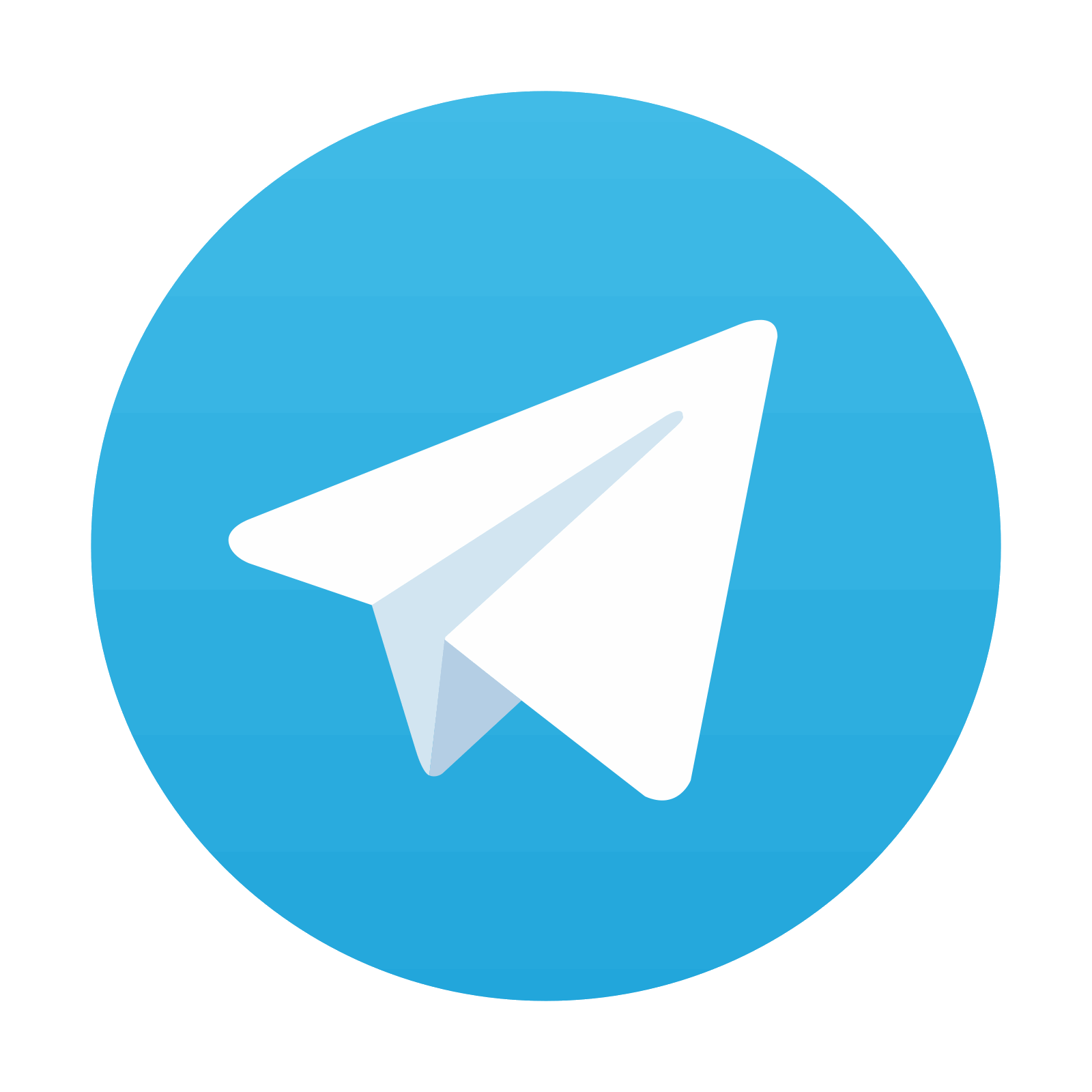
Stay updated, free dental videos. Join our Telegram channel

VIDEdental - Online dental courses
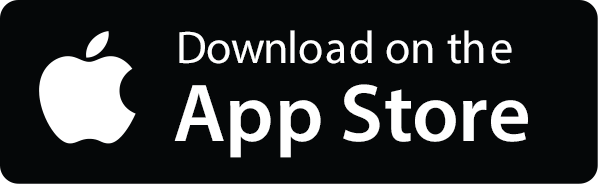
