Abstract
Objective
Chipping failures observed clinically in bilayer systems of porcelain and zirconia restorations should be coupled with a monoclinic to tetragonal phase transformation in the zirconia layer due to the high compressive stress.
Methods
Phase transformations were mapped using 2D micro X-ray diffraction of 1083 frames at 100 μm × 100 μm spacing automatically positioned along the core layer of a sectioned fractured crown.
Results
Yttria–zirconia tetragonal phase transformations to monoclinic zirconia and monoclinic yttria were observed, mostly at the impacted area. A simple map of (1 0 1) tetragonal d -spacing strain reveals stress relaxation during phase transformation was detected at inner section of lingual side, because the initial state of compressive residual stress assists this phase transformation at the inter section of lingual side of the core while initial tensile stress at the outer sides under the veneer relaxes under compression and initially prevents phase transformation.
Significance
This study implements an experimental method to map the phase transformation, after applying local compressive load until fracture. Such fractures resemble clinically observed chipping failure.
1
Introduction
With favorable compressive strength, appealing esthetics, chemical inertness, and biocompatibility ceramics have become widely used as dental restoration materials. With both esthetics and better mechanical properties expectancy continuing, layered structures of high compressive strength core polycrystalline yttrium stabilized zirconia with a porcelain veneer has become a dominant restoration material . Concentrated stresses at the leading edge of crack tips in stabilized tetragonal zirconia result in phase transformation to a monoclinic phase. The resulting volume expansion induces compressive stress at the crack tip arresting the crack by this toughening mechanism .
Recent interest of researches in this field is focused on producing more reliable crowns since a restoration’s service life is limited to a few years until catastrophic fatigue cracking . The most common failure mode in the system of porcelain veneered zirconia involves chipping and crack propagation in porcelain or along the interface at the porcelain side with little tendency to run through the zirconia core . When cooling from the high temperature, pure zirconia (ZrO 2 ) transforms from tetragonal to the monoclinic phase at 1043 °C along with a 3% volumetric change in crystal structure. This results in micro crack formation within the lattice during dense bulk fabrication. A small amount of Y 2 O 3 is the most common oxide to stabilize the tetragonal structure down through room temperature . The room temperature yttrium stabilized tetragonal zirconia phase transformation to monoclinic is an irreversible process accompanied by lowering of the Gibbs energy of the system. In general, the driving forces for this transformation are externally applied stress, internal grain-to-grain residual stress, or residual stress due to thermal expansion coefficient mismatch between composite layers . External applied load or residual stress normally provides a motivation for zirconia tetragonal to monoclinic phase transformation, but the actual occurrence of the phase transformation requires crystal plane rotation up to 9° about a typical crystal axis . Unlike their high strength under compression, ceramics are brittle under high tensile loading. 3D finite element simulations have been used to determine the stress distribution in all ceramic crowns and bridges for virtual CAD generated models or a geometry reconstructed by X-ray micro-tomography . FEA models predict high stress concentration in dental restoration due to residual stress caused by coefficient of thermal expansion mismatch during manufacturing or by virtual simulation of loading . Up to now, there have been no studies using 3D FEA to determine the effect of stress induced phase transformation in zirconia on stress distributions. Importing the phase transformation mechanism in models has not been limited by complexity, but there is no proposed method to fairly validate the predicted results and use their feedback to improve the models. This present study implements an advanced procedure using micro X-ray diffraction with a 2D area detector and precise positioning stage to map the phase transformation over the large complex cross-sectional area of a fractured crown.
2
Materials and methods
A standard polycrystalline yttria stabilized tetragonal zirconia ceramic crown core covered by porcelain veneer was subjected to single load to failure. A 1.9 mm tungsten carbide ball indenter was used to apply load to failure using a customized frame. The chipped region due to failure at one of the cusps was sectioned in two halves using a low speed water cooled diamond saw and was mounted onto an aluminum plate with high strength epoxy glue as shown in Fig. 1 a.
X-ray diffraction was performed with Cu-K α radiation at tube parameters of 40 kV/40 mA using a Bruker D8 Discover XRD 2 micro-diffractometer equipped with the General Area Diffraction Detection System (GADDS) and Hi-Star 2D area detector. The detector distance to the center of diffraction was kept at 29.95 cm which covers approximately the area of 20° in 2 and 20° in χ with 0.02° resolution. To map many spots, a motorized five axis ( X , Y , Z (translation), χ (tilt), φ (rotation)) stage was used for positioning which can move the measurement spot to the instrument center within 12.5 μm position accuracy and 5 μm repeatability.
The mapping X-ray diffraction scans were performed on the flat surface of the crown zirconia layer using a 0.2 mm pinhole collimator in reflection mode. Although the use of a 200 μm pinhole collimator in comparison with an available 50 μm monocapillary beam decreases the intensity of X-ray beam on the sample, it provides better crystallite statistics in this case where the size of grains on average were 0.1–0.3 μm. This beam size can provide information from several grains in a single exposure eliminating the need for averaging several scans. Fig. 1 b demonstrates a graphical representation of the grid over which X-ray diffraction frames were collected. It illustrates how the total area was reduced to eight sub-grid regions named A, B, … and H. In each sub region, an XRD map was collected just for area between the two surfaces and not outside locations. Using a sequential list, the system automatically brings each predetermined point to the diffractometer center and performs final height adjustments automatically in the out-of-plane direction with an auto video-laser positioning system before each exposure. In fact, diffraction frames were only collected on the zirconia surface, which is polycrystalline while the porcelain region was ignored because it is amorphous and excluded as “not diffracting” by a threshold on the number of detector counts.
Initial grid points at the region F and selected points for diffraction are shown in Fig. 2 a, and b respectively. Frames on overlapped area between F and G regions were collected twice to monitor reproducibility. This result reveals an acceptable repeatability within a ±2% difference interval. The exposure times were 120 s/frame without rotation, tilt, or XY stage oscillation. The separation step between two grid points was 100 μm in both X and Y directions. A fixed X-ray beam incident angle 1 = 14 and detector angle of 2 = 14 were used to collect 1083 frames with a 2 interval of 18–38°.
2
Materials and methods
A standard polycrystalline yttria stabilized tetragonal zirconia ceramic crown core covered by porcelain veneer was subjected to single load to failure. A 1.9 mm tungsten carbide ball indenter was used to apply load to failure using a customized frame. The chipped region due to failure at one of the cusps was sectioned in two halves using a low speed water cooled diamond saw and was mounted onto an aluminum plate with high strength epoxy glue as shown in Fig. 1 a.
X-ray diffraction was performed with Cu-K α radiation at tube parameters of 40 kV/40 mA using a Bruker D8 Discover XRD 2 micro-diffractometer equipped with the General Area Diffraction Detection System (GADDS) and Hi-Star 2D area detector. The detector distance to the center of diffraction was kept at 29.95 cm which covers approximately the area of 20° in 2 and 20° in χ with 0.02° resolution. To map many spots, a motorized five axis ( X , Y , Z (translation), χ (tilt), φ (rotation)) stage was used for positioning which can move the measurement spot to the instrument center within 12.5 μm position accuracy and 5 μm repeatability.
The mapping X-ray diffraction scans were performed on the flat surface of the crown zirconia layer using a 0.2 mm pinhole collimator in reflection mode. Although the use of a 200 μm pinhole collimator in comparison with an available 50 μm monocapillary beam decreases the intensity of X-ray beam on the sample, it provides better crystallite statistics in this case where the size of grains on average were 0.1–0.3 μm. This beam size can provide information from several grains in a single exposure eliminating the need for averaging several scans. Fig. 1 b demonstrates a graphical representation of the grid over which X-ray diffraction frames were collected. It illustrates how the total area was reduced to eight sub-grid regions named A, B, … and H. In each sub region, an XRD map was collected just for area between the two surfaces and not outside locations. Using a sequential list, the system automatically brings each predetermined point to the diffractometer center and performs final height adjustments automatically in the out-of-plane direction with an auto video-laser positioning system before each exposure. In fact, diffraction frames were only collected on the zirconia surface, which is polycrystalline while the porcelain region was ignored because it is amorphous and excluded as “not diffracting” by a threshold on the number of detector counts.
Initial grid points at the region F and selected points for diffraction are shown in Fig. 2 a, and b respectively. Frames on overlapped area between F and G regions were collected twice to monitor reproducibility. This result reveals an acceptable repeatability within a ±2% difference interval. The exposure times were 120 s/frame without rotation, tilt, or XY stage oscillation. The separation step between two grid points was 100 μm in both X and Y directions. A fixed X-ray beam incident angle 1 = 14 and detector angle of 2 = 14 were used to collect 1083 frames with a 2 interval of 18–38°.
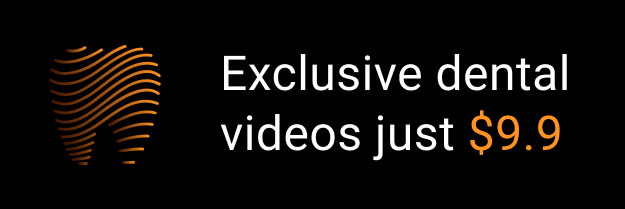