Abstract
Fluorapatite glass-ceramics have been shown to be excellent candidates as scaffold materials for bone grafts, however, scaffold production by sintering is hindered by concurrent crystallization of the glass. Objective, our goal was to investigate the effect of Ca/Al ratio on the sintering behavior of Nb-doped fluorapatite-based glasses in the SiO 2 –Al 2 O 3 –P 2 O 5 –MgO–Na 2 O–K 2 O–CaO–CaF 2 system. Methods, glass compositions with Ca/Al ratio of 1 (A), 2 (B), 4 (C) and 19 (D) were prepared by twice melting at 1525 °C for 3 h. Glasses were either cast as cylindrical ingots or ground into powders. Disk-shaped specimens were prepared by either sectioning from the ingots or powder-compacting in a mold, followed by heat treatment at temperatures ranging between 700 and 1050 °C for 1 h. The density was measured on both sintered specimens and heat treated discs as controls. The degree of sintering was determined from these measurements. Results and Significance XRD showed that fluorapatite crystallized in all glass-ceramics. A high degree of sintering was achieved at 775 °C for glass-ceramic D (98.99 ± 0.04%), and 900 °C for glass-ceramic C (91.31 ± 0.10). Glass-ceramics A or B were only partially sintered at 1000 °C (63.6 ± 0.8% and 74.1 ± 1.5%, respectively). SEM revealed a unique microstructure of micron-sized spherulitic fluorapatite crystals in glass-ceramics C and D. Increasing the Ca/Al ratio promoted low temperature sintering of fluorapatite glass-ceramics, which are traditionally difficult to sinter.
1
Introduction
Apatite-based glass-ceramics have long attracted interest as synthetic materials for bone replacement . They are used in bulk form, powders, coatings, and more recently have been investigated as macroporous scaffolds . The excellent biocompatibility of hydroxyapatite and fluorapatite glass-ceramics is classically related to their chemical and crystallographical similarities with the apatite phase present in bone . Compared to bioinert ceramics such as alumina, the main potential advantage of apatite-based glass-ceramics is the formation of a chemical bond at the ceramic–bone interface . High resolution TEM studies have clearly demonstrated the formation of de novo apatite crystals by epitaxial growth on the surface of hydroxyapatite-containing ceramics . Moreover, apatite crystallization in apatite-mullite glass-ceramics has been shown to elicit an excellent bone tissue response after implantation in rat femurs, while the corresponding amorphous glass induced an inflammatory response . These findings raise the important issue of the role of topography and microstructural features in the pace of in vivo integration of apatite-based glass-ceramics and implant materials . Meanwhile, our previous work has revealed that fluorapatite glass-ceramics doped with small amounts of niobium oxide crystallized into a very fine dual microstructure composed of submicrometer fluorapatite spherical crystals, together with forsterite polygonal crystals . This microstructure is strongly influenced by the conditions of crystallization heat treatment, namely duration, temperature and cooling rate . Further work revealed that the surface topography associated with this type of microstructure led to excellent attachment, proliferation and differentiation of human mesenchymal stem cells . Recent investigations on the crystallization mechanisms of apatite-mullite glass-ceramics also demonstrated that control of crystal morphology to form arrays of apatite nanocrystals is achievable in this system, through modulations of the glass composition and heat treatment regime .
As mentioned earlier, bioactive glass-ceramics are available in various forms and shapes. The present work focuses on the preparation of fluorapatite glass-ceramics for the production of macroporous scaffolds. Inspired by progress in the fabrication of open-celled ceramics, several processing techniques have been developed to prepare macroporous ceramic scaffolds for bone replacement . Amongst these techniques, one of the most common is the impregnation of a open-cell polymer foam with a ceramic slurry that is later dried and sintered while the polymeric template is eliminated . This polymer foam impregnation technique is an attractive method for producing glass-ceramic scaffolds from bioactive compositions, including hydroxyapatite, fluorapatite and β-TCP-containing glass-ceramics . However, hydroxyapatite and fluorapatite ceramics are traditionally difficult to sinter, even as mixtures of powders . Low temperatures result in high porosity and incomplete sintering, while high temperatures in excess of 1000 °C may lead to decomposition, loss of hydroxyls or fluorine and formation of pyrophosphates . Additionally, in glass-ceramic systems, crystallization may occur during sintering and hinder the densification process . Indeed, it is well established that independently of the nature of the crystalline phases forming, chemical compositional changes in the remaining glassy matrix are likely to induce changes in viscosity, which in turn may prevent adequate sintering . Concurrently, several studies have shown that adequate sintering is only possible if sintering precedes crystallization . One way to improve sinterability for a given composition is therefore to extend the working range to allow viscous flow sintering prior to crystallization. This can be done by fine-tuning the glass composition and replacing intermediate oxides such as alumina with alkaline-earth modifiers such as calcium oxide . Moreover, studies in multicomponent bioactive silicate glasses revealed that when introduced as calcium fluoride, and in the presence of phosphorous pentoxide, calcium causes a decrease in the glass transition temperature, together with an increase in the crystallization temperature, thereby efficiently increasing the processing window . Calcium is also a key component in the development of bioactivity in bioactive glasses . Meanwhile, aluminum oxide has been shown to be detrimental to the bioactivity of calcium silicate glasses . The purpose of the present study was to investigate the effect of calcium to aluminum ratio on the sintering and crystallization behavior of fluorapatite glass-ceramics. The hypothesis tested was that increasing the amount of calcium oxide at the expense of aluminum oxide would increase sinterability by extending the processing range prior to crystallization of fluorapatite.
2
Materials and methods
2.1
Specimen preparation
Four glass compositions with increasing calcium to aluminum atomic ratio were prepared by mixing reagent grade oxides and carbonates ( Table 1 ). Fluoride was introduced as calcium fluoride and was added in excess as 50% losses by volatilization were anticipated. Batch ingredients were melted at 1525 °C for 3 h in platinum crucibles. After quenching in deionized water, the glass frits were powdered and melted again at 1525 °C for 3 h. The molten glasses were cast to form cylindrical rods (10 mm in diameter; 60 mm in length). The rods were furnace-cooled from 685 °C to room temperature and sectioned into disks (10 mm in diameter; 1 mm thick) using a low speed diamond saw. Specimens were heat treated in the temperature range 700–1050 °C for 1 h at a heating rate of 2 °C/min. Glass frits from the same compositions were prepared as described earlier. Frits were powdered and sieved to a particle size of 45 micrometers or less. Disk-shaped specimens (10 mm in diameter; 1 mm thick) were produced by uniaxial pressure using a polyvinylsiloxane mold. Specimens were sintered in air at temperatures ranging between 700 and 1050 °C for 1 h.
Composition | A | B | C | D |
---|---|---|---|---|
SiO 2 | 33.9 | 33.1 | 32.3 | 31.5 |
MgO | 22.9 | 22.3 | 21.8 | 21.2 |
Nb 2 O 5 | 0.3 | 0.2 | 0.2 | 0.2 |
CaO | 8.6 | 13.9 | 19.0 | 23.9 |
Na 2 O | 2.5 | 2.4 | 2.4 | 2.3 |
K 2 O | 4.1 | 4.0 | 3.9 | 3.8 |
Al 2 O 3 | 10.4 | 7.1 | 3.9 | 0.9 |
CaF 2 | 12.0 | 11.8 | 11.5 | 11.2 |
P 2 O 5 | 5.4 | 5.2 | 5.1 | 5.0 |
2.2
Crystallization behavior
The crystallization behavior was investigated by differential scanning calorimetry (Q600 DSC/TGA, TA Instruments). Analyses were performed on glass frit particles placed in matched platinum–rhodium crucibles under nitrogen gas flow. Aluminum oxide powder (99.99%) served as a reference standard. First, the optimum nucleation temperature (ONT) was determined for each glass composition. This temperature is defined as the “temperature at which the most number of stable nuclei form per volume element” . ONT was investigated by DSC after 1 h nucleation holds at various temperatures, followed by full crystallization, according to the method proposed by Marotta et al. . The ONT was determined as the hold temperature leading to the lowest temperature for the first crystallization exotherm. Further DSC experiments were conducted at heating rates of 10, 20, 30 and 40 °C/min on samples nucleated at the ONT. The activation energy of crystallization ( E C ) for fluorapatite was calculated from the slope of the classical Kissinger plot, using the Kissinger equation :
E C R T P = ln T P 2 v
where T P is the temperature of the crystallization exotherm and v is the heating rate.
The coefficient of thermal expansion and softening point were determined by dilatometry on glass bars sectioned from the cast ingots (Orton dilatometer, Model 1600D). Crystalline phases were characterized by X-ray diffraction on powdered and bulk specimens. Scans were performed in the two-theta range 10–60°, at a scanning rate of 1 °C/min (Miniflex II diffractometer, Rigaku Americas). Additionally, specimens sintered at 800 °C/1 h were analyzed at a scanning rate of 0.2°/min in the two theta range 3–90° at 40 kV and 44 mA in Bragg-Brentano configuration (SmartLab, Rigaku Americas). Peak positions were determined using PDXL-2 analysis software (Rigaku Corporation) after calibration using silicon powder standard (NIST, 640d). The microstructure was investigated by scanning electron microscopy under secondary electron imaging (Hitachi S-4800 field emission SEM). Specimens were polished to a 0.5 μm finish using as series of abrasives ending with diamond polishing pastes. They were etched with diluted hydrofluoric acid and gold coated prior to SEM examination. A variable pressure scanning electron microscope (VP-SEM, Model 3400, Hitachi High Technologies America, Inc.), coupled with a back-scattered electron detector, was used to perform semi-quantitative Energy Dispersive Spectroscopic analyses on uncoated specimens. X-rays were detected at an accelerating voltage of 15 kV and a working distance of 10 mm (Bruker AXS Microanalyzer). ZAF matrix correction factors were applied in instrumental software calculations.
2.3
Sintering behavior
The density of bulk glass-ceramic specimens as well as sintered specimens was measured by Archimedes’ method. The degree of sintering was calculated assuming 100% theoretical density for bulk heat treated glass-ceramic specimens. The sintering behavior was also assessed by scanning electron microscopy on both as-sintered and sintered and polished specimens.
2.4
Statistical methods
Results were analyzed by ANOVA and Tukey’s test to detect statistically significant differences. A p -value of less than 0.05 was considered statistically significant.
2
Materials and methods
2.1
Specimen preparation
Four glass compositions with increasing calcium to aluminum atomic ratio were prepared by mixing reagent grade oxides and carbonates ( Table 1 ). Fluoride was introduced as calcium fluoride and was added in excess as 50% losses by volatilization were anticipated. Batch ingredients were melted at 1525 °C for 3 h in platinum crucibles. After quenching in deionized water, the glass frits were powdered and melted again at 1525 °C for 3 h. The molten glasses were cast to form cylindrical rods (10 mm in diameter; 60 mm in length). The rods were furnace-cooled from 685 °C to room temperature and sectioned into disks (10 mm in diameter; 1 mm thick) using a low speed diamond saw. Specimens were heat treated in the temperature range 700–1050 °C for 1 h at a heating rate of 2 °C/min. Glass frits from the same compositions were prepared as described earlier. Frits were powdered and sieved to a particle size of 45 micrometers or less. Disk-shaped specimens (10 mm in diameter; 1 mm thick) were produced by uniaxial pressure using a polyvinylsiloxane mold. Specimens were sintered in air at temperatures ranging between 700 and 1050 °C for 1 h.
Composition | A | B | C | D |
---|---|---|---|---|
SiO 2 | 33.9 | 33.1 | 32.3 | 31.5 |
MgO | 22.9 | 22.3 | 21.8 | 21.2 |
Nb 2 O 5 | 0.3 | 0.2 | 0.2 | 0.2 |
CaO | 8.6 | 13.9 | 19.0 | 23.9 |
Na 2 O | 2.5 | 2.4 | 2.4 | 2.3 |
K 2 O | 4.1 | 4.0 | 3.9 | 3.8 |
Al 2 O 3 | 10.4 | 7.1 | 3.9 | 0.9 |
CaF 2 | 12.0 | 11.8 | 11.5 | 11.2 |
P 2 O 5 | 5.4 | 5.2 | 5.1 | 5.0 |
2.2
Crystallization behavior
The crystallization behavior was investigated by differential scanning calorimetry (Q600 DSC/TGA, TA Instruments). Analyses were performed on glass frit particles placed in matched platinum–rhodium crucibles under nitrogen gas flow. Aluminum oxide powder (99.99%) served as a reference standard. First, the optimum nucleation temperature (ONT) was determined for each glass composition. This temperature is defined as the “temperature at which the most number of stable nuclei form per volume element” . ONT was investigated by DSC after 1 h nucleation holds at various temperatures, followed by full crystallization, according to the method proposed by Marotta et al. . The ONT was determined as the hold temperature leading to the lowest temperature for the first crystallization exotherm. Further DSC experiments were conducted at heating rates of 10, 20, 30 and 40 °C/min on samples nucleated at the ONT. The activation energy of crystallization ( E C ) for fluorapatite was calculated from the slope of the classical Kissinger plot, using the Kissinger equation :
E C R T P = ln T P 2 v
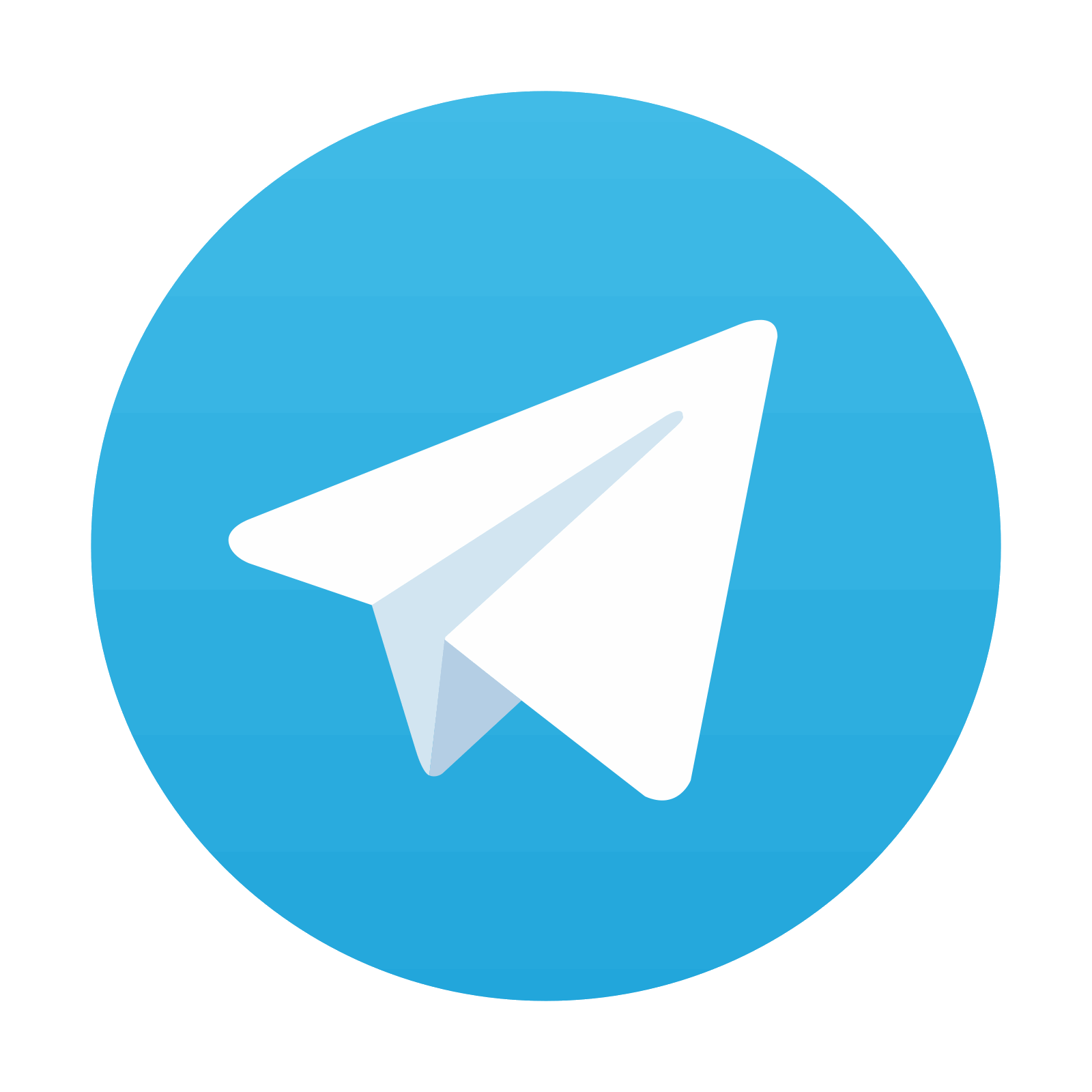
Stay updated, free dental videos. Join our Telegram channel

VIDEdental - Online dental courses
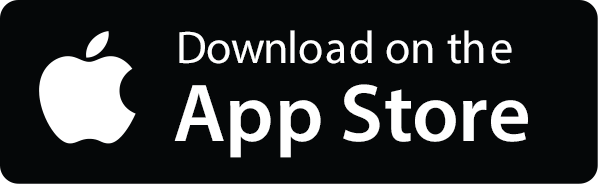
