Abstract
Objective
To evaluate the fatigue life of zirconia-veneered and metal-ceramic crowns comprised by an even thickness or a modified framework design when loaded on marginal ridges.
Methods
Eighty marginal ridges were present after fabrication of forty molar crowns cemented onto composite-resin replicas and divided (n = 20/each), in the following groups: metal-ceramic with even thickness (MCev) or with a modified framework design (MCm, lingual collar with proximal struts); porcelain-fused to zirconia with even thickness (PFZev) or with the modified framework design (PFZm). Each marginal ridge (mesial and distal) was subjected to cyclic loading separately with a lithium disilicate indenter for 10 6 cycles or until fracture. Kruskal–Wallis and Wilcoxon matched pair test (p < 0.05) evaluated both marginal ridges. Every 125,000 cycles, the test was interrupted for damage inspection. Weibull distribution (90% confidence bounds) determined the probability of survival (reliability).
Results
Weibull 2-parameter contour-plot showed significantly higher fatigue life for PFZev compared to MC, and comparable with PFZm. A significant decrease in reliability was observed between groups from 625,000 until 10 6 cycles. Metal-ceramic groups presented significantly lower probability of survival at 10 6 cycles (MCev = 0.66% and MCm = 4.73%) compared to PFZm (23.41%) and PFZev (36.68%). Fractographic marks showed a consistent fracture origin and direction of crack propagation. Reliability was higher for porcelain-fused to zirconia than for metal ceramic crowns, regardless of framework design.
Significance
Zirconia-veneered crowns presented decreased fracture rates compared to metal ceramics, even when loaded at marginal ridges, regardless of framework design.
1
Introduction
All-ceramic materials continue to be investigated in both laboratory and clinical settings in a constant quest to accumulate supportive data for their safe use. In general, these materials are still prone to fractures of multiple nature including bulk fractures or chipping within the veneering porcelain given their inherent brittleness. The most common complications include veneering material fractures, loss of retention, endodontic treatment, and bleeding on probing. However, for crown applications and material such as porcelain fused to zirconia, it seems that the rates of such complications are comparable to those of metal ceramics, according to a recent systematic review . Yet, such observations have been made on a relatively small number of studies, seldom of randomized controlled design that warrants further investigation in the field.
It is unequivocal that inconsistencies are present in reporting the extent of failures occurring clinically in all-ceramic materials, even when standardized evaluation systems are used (e.g., USPHS), which eventually results in uncertainties upon decision making towards replacement or repair for continued function . In spite of its extension, a finding of clinical significance comprises where the failure is located. When at any free surface area (e.g., buccal, lingual or occlusal) access for repair is straightforward and may allow for successful repair. However, when at the proximal areas, not only access, but proper isolation may be hindered by adjacent teeth. Interestingly, a clinical study has shown that when occlusal contacts are present on mesial or distal ridges, fractures in porcelain-fused to zirconia prostheses demand restoration replacement due to their extension leading to esthetics and/or function impairment .
Because the marginal ridges are a common location for occlusal contacts in natural dentition in maximal intercuspation, regardless of Angle occlusal scheme (class I, II, and III), it is speculated that such areas may be more prone to failures when compared to contacts at the central fossa . Finite element analysis investigations evaluating the stresses in marginal ridges and proximal areas have shown a high tensile stresses specially in molars and second premolars .
The prevalence of contacts between the cusp and marginal ridge is 34.60% . It may be present at only one marginal ridge or two simultaneously . Teeth that have the widest range of these contacts are the first molars, presenting up to six simultaneous occlusal contacts . Furthermore, one to three contacts are common at molars in intercuspal position. The explanation for this variety is given by the largest occlusal surface compared to other teeth .
Factors associated with failure rates of porcelain fused to polycrystalline zirconia crowns are multifaceted and attempts to reduce failures include modification of core design , improved CTE matching between core and porcelain , cooling rate of the porcelain , and others. By core design modification, an additional support for veneering ceramic is provided when compared to the standard design core with implications including an increase in probability of survival and and a reduction in the extent of porcelain veneer fracture . However, virtually all investigations simulate the occlusal contact at the cusp inclines where the lingual collar provided additional support, rather than on marginal ridges where some failures have shown to occur clinically . Therefore, whether failure rates can be decreased or not at the marginal ridges when a framework is designed to improve support is yet to be investigated.
The present study sought to investigate the fatigue life and failure modes of porcelain fused to zirconia (Y-TZP—yttria-stabilized tetragonal zirconia polycrystal) and metal-ceramic crows with an even thickness or a modified framework design. The following null hypotheses tested were that fatigue life would not be improved: (1) by framework design modification and (2) by material used to fabricate crowns.
2
Materials and methods
An artificial mandibular first molar was positioned in a mannequin for full crown preparation that included 2.0 mm occlusal reduction, 1.5 mm axial reduction and a 1.2 mm shoulder margin with rounded internal angles . Replicas of the prepared tooth (n = 40) were obtained by an impression with polyvinyl siloxane material (Express—3 M Oral Care, St. Paul, MN, USA) followed by incremental packing and light-curing (Ultralux, Dabi Atlante, Ribeirão Preto, SP, Brazil) of composite resin (Z100, 3 M Oral Care, St. Paul, MN, USA). These replicas were stored into a distilled water recipient for 30 days to provide hygroscopic expansion and minimize dimensional alteration . The replicas were removed from the recipient, vertically positioned into a polyvinyl siloxane matrix (Express—3 M ESPE) to standardize embedding and pouring of acrylic resin (Jet, Clássico Artigos Odontológicos, São Paulo, SP, Brazil) in a 25 mm diameter PVC tubes.
Replicas were randomly assigned to two groups (n = 20 each) according to the crown system used; metal ceramic (MC) or porcelain fused to zirconia (PFZ). Subsequently, each group was subdivided (n = 10 each) according to framework design comprising either a core with an even thickness (MCev and PFZev) or a modified design (MCm and PFZm). The even thickness groups presented a 0.5 mm thickness coping ( Fig. 1 A and C) and the modified core design comprised a 0.5 mm even thickness with a 1 mm thick lingual collar and 2.0 mm of height, connected to proximal struts of 3.5 mm height ( Fig. 1 B and D) .
For fabrication of MC crowns, an impression of each composite resin replica was made (Pentamix—3 M Oral Care, St. Paul, MN, USA) with polyether material (Impregum F—3 M Oral Care, St. Paul, MN, USA) and poured, resulting in a total of 20 stone dies. The even thickness and modified metal cores (cobalt–chromium, Fit Cast Cobalto, Metal Talmax, Curitiba, PR, Brazil) were manufactured by means of lost wax technique and cast according to manufacturer. The IPS d.SIGN Transpaneutral (Ivoclar Vivadent AG, Schaan, Liechtenstein) veneering ceramic was hand layered and the firing schedule followed the manufacturer’s recommendation. The veneering ceramic transparency was chosen to facilitate crack inspection throughout fatigue cycles.
The Y-TZP cores (IPS e.max ZirCAD—Ivoclar Vivadent AG, Schaan, Liechtenstein) were milled from pre-sintered e.max ZirCAD blocks (shade MO 0 and block size 15C) in a CAD/CAM system (Cerec InLab, Sirona Dental System, Bensheim, Germany). The prepared tooth received a contrast layer (IPS Contrast Spray—Ivoclar Vivadent AG, Schaan, Liechtenstein) to allow its digital scanning (InEos Blue Desktop Scanner). The software (Cerec Software 4.0) created a 3D core image with 0.5 mm thickness (PFZev). To obtain the PFZm files for milling, the prepared tooth image saved in the software was correlated with the coping and preparation of the MCm group positioned on it for scanning. The correlation option of the software was performed to create the 3D image of PFZm core. After milling, the cores were sintered in the Sintramat furnace at 1500 °C for 8 h. The IPS e.max Ceram Transpaclear (Ivoclar Vivadent AG, Schaan, Liechtenstein) veneering ceramic was hand layered according with the manufacturer’s recommendations. The PFZ veneering porcelain and glaze firing schedule is presented in Fig. 2 .
A gypsum matrix of the occlusal surface of a molar tooth was fabricated and fixed on a verticulator in order to standardize the occlusal anatomy during porcelain veneering. Porcelain thickness was 1.0 mm on the axial walls, 1.5 mm on the occlusal surface ( Fig. 3 A). No internal adjustments were necessary for any crowns on prepared composite resin replicas. Crowns were glazed and the MC group had the intaglio surface sandblasted with 240 mesh alumina, cleaned by sonicating in ethanol and air dried. The PFZ groups had their cementation surface cleaned with 35% phosphoric acid (Ultra-Etch, Ultradent, South Jordan, USA) for 60 s and then rinsed with water for 30s. All crowns were cemented on the composite resin replicas with a self-adhesive resin cement (RelyX U200–3 M Oral Care, St. Paul, MN, USA) under a 50 N static occlusal load for 10 min. Samples were stored in 37 °C distilled water between 24–48 h before testing. Consequently, the marginal ridges (mesial and distal) of each group (n = 20) were obtained from the crown fabrication.
The fatigue equipment (Model MSFM – Elquip – São Carlo, SP, Brazil) delivered r-ratio cyclic loading without lateral movement at a 30–300 N load range for 10 6 cycles at 2 Hz until failure or suspension, under distilled water at 37 °C (±2 °C) . Loading was applied at the marginal ridges of the occlusal surface with a spherical glazed monolithic lithium disilicate (IPS e.max Press HT High Translucency – Ivoclar Vivadent – Schaan/Liechtenstein) indenter of 3.18 mm radius, positioned in contact with marginal ridges, which was replaced every 500,000 cycles. Fatigue loading was initiated on the mesial marginal ridge until failure or 10 6 cycles; fatigue was subsequently conducted following the same methodology on the distal marginal ridge ( Fig. 3 E and F). This sequence of loading was sequentially altered after every five samples to initiate on the distal ridge and then on the mesial to minimize bias. Every 125,000 cycles the fatigue test was interrupted for crowns and ceramic indenter surface damage inspection under a stereomicroscope (Leica Zeiss MZE, Mannheim, Germany) illuminated by an external light source (Leica CL5 150D, Mannheim, Germany). The specimens and indenters were repositioned and checked by double-sided occlusal marking film for fatigue of additional 125,000 cycles until next inspection. The second location of fatigue testing in a sample, which occurred at the opposite marginal ridge, was only performed when damage (fracture or detectable cracks) was confined to the first fatigued marginal ridge.
Porcelain cohesive fracture or delamination of veneering ceramic, or core bulk fracture were used as criteria for failure, whereas the marginal ridges that presented only cracks or quasi-plastic mode were deemed suspended after 10 6 cycles. After mechanical testing, the marginal ridges classified as failure were inspected at the scanning electron microscope (SEM) and the suspended samples were embedded in epoxy resin (Resina Epoxica RD6921, Redelease, São Paulo, Brazil), and serially polished along crack extension with increasingly finer grit silicon carbide papers (100, 240, 320, 400, 500, 600 grits), under copious water irrigation, followed by 6 and 3 μm diamond pastes (Arotec, São Paulo, Brazil) applied on wet cloths. Subsurface damage was inspected by means of a stereomicroscope (Leica Zeiss MZE, Mannheim, Germany).
In an attempt to determine if there was any difference between cycling on the mesial and distal marginal ridge in the same crown the Kruskal–Wallis and Wilcoxon matched pair test with an α set to 0.05 significance level was performed. The number of cycles for failure during fatigue were recorded for Weibull analysis (Synthesis 9, Weibull 9++; Reliasoft, Tucson, AZ, USA). A probability Weibull plot was used to illustrate data distribution as a function of elapsed cycles. For fatigue life differences between groups, a contour plot was created using Weibull modulus ( m ) vs. characteristic value Eta (cycles) (90% 2-sided confidence bounds). Non-overlap of contour plots indicates a significant difference between groups. Finally, the probability of survival at accumulated fatigue intervals used for sample inspection (every 125,000 cycles) was calculated and also presented in a plot. Reliability predictions beyond 1 million cycles were made only for groups with a probability of survival ≥10% at the end of tests.
2
Materials and methods
An artificial mandibular first molar was positioned in a mannequin for full crown preparation that included 2.0 mm occlusal reduction, 1.5 mm axial reduction and a 1.2 mm shoulder margin with rounded internal angles . Replicas of the prepared tooth (n = 40) were obtained by an impression with polyvinyl siloxane material (Express—3 M Oral Care, St. Paul, MN, USA) followed by incremental packing and light-curing (Ultralux, Dabi Atlante, Ribeirão Preto, SP, Brazil) of composite resin (Z100, 3 M Oral Care, St. Paul, MN, USA). These replicas were stored into a distilled water recipient for 30 days to provide hygroscopic expansion and minimize dimensional alteration . The replicas were removed from the recipient, vertically positioned into a polyvinyl siloxane matrix (Express—3 M ESPE) to standardize embedding and pouring of acrylic resin (Jet, Clássico Artigos Odontológicos, São Paulo, SP, Brazil) in a 25 mm diameter PVC tubes.
Replicas were randomly assigned to two groups (n = 20 each) according to the crown system used; metal ceramic (MC) or porcelain fused to zirconia (PFZ). Subsequently, each group was subdivided (n = 10 each) according to framework design comprising either a core with an even thickness (MCev and PFZev) or a modified design (MCm and PFZm). The even thickness groups presented a 0.5 mm thickness coping ( Fig. 1 A and C) and the modified core design comprised a 0.5 mm even thickness with a 1 mm thick lingual collar and 2.0 mm of height, connected to proximal struts of 3.5 mm height ( Fig. 1 B and D) .
For fabrication of MC crowns, an impression of each composite resin replica was made (Pentamix—3 M Oral Care, St. Paul, MN, USA) with polyether material (Impregum F—3 M Oral Care, St. Paul, MN, USA) and poured, resulting in a total of 20 stone dies. The even thickness and modified metal cores (cobalt–chromium, Fit Cast Cobalto, Metal Talmax, Curitiba, PR, Brazil) were manufactured by means of lost wax technique and cast according to manufacturer. The IPS d.SIGN Transpaneutral (Ivoclar Vivadent AG, Schaan, Liechtenstein) veneering ceramic was hand layered and the firing schedule followed the manufacturer’s recommendation. The veneering ceramic transparency was chosen to facilitate crack inspection throughout fatigue cycles.
The Y-TZP cores (IPS e.max ZirCAD—Ivoclar Vivadent AG, Schaan, Liechtenstein) were milled from pre-sintered e.max ZirCAD blocks (shade MO 0 and block size 15C) in a CAD/CAM system (Cerec InLab, Sirona Dental System, Bensheim, Germany). The prepared tooth received a contrast layer (IPS Contrast Spray—Ivoclar Vivadent AG, Schaan, Liechtenstein) to allow its digital scanning (InEos Blue Desktop Scanner). The software (Cerec Software 4.0) created a 3D core image with 0.5 mm thickness (PFZev). To obtain the PFZm files for milling, the prepared tooth image saved in the software was correlated with the coping and preparation of the MCm group positioned on it for scanning. The correlation option of the software was performed to create the 3D image of PFZm core. After milling, the cores were sintered in the Sintramat furnace at 1500 °C for 8 h. The IPS e.max Ceram Transpaclear (Ivoclar Vivadent AG, Schaan, Liechtenstein) veneering ceramic was hand layered according with the manufacturer’s recommendations. The PFZ veneering porcelain and glaze firing schedule is presented in Fig. 2 .
A gypsum matrix of the occlusal surface of a molar tooth was fabricated and fixed on a verticulator in order to standardize the occlusal anatomy during porcelain veneering. Porcelain thickness was 1.0 mm on the axial walls, 1.5 mm on the occlusal surface ( Fig. 3 A). No internal adjustments were necessary for any crowns on prepared composite resin replicas. Crowns were glazed and the MC group had the intaglio surface sandblasted with 240 mesh alumina, cleaned by sonicating in ethanol and air dried. The PFZ groups had their cementation surface cleaned with 35% phosphoric acid (Ultra-Etch, Ultradent, South Jordan, USA) for 60 s and then rinsed with water for 30s. All crowns were cemented on the composite resin replicas with a self-adhesive resin cement (RelyX U200–3 M Oral Care, St. Paul, MN, USA) under a 50 N static occlusal load for 10 min. Samples were stored in 37 °C distilled water between 24–48 h before testing. Consequently, the marginal ridges (mesial and distal) of each group (n = 20) were obtained from the crown fabrication.
The fatigue equipment (Model MSFM – Elquip – São Carlo, SP, Brazil) delivered r-ratio cyclic loading without lateral movement at a 30–300 N load range for 10 6 cycles at 2 Hz until failure or suspension, under distilled water at 37 °C (±2 °C) . Loading was applied at the marginal ridges of the occlusal surface with a spherical glazed monolithic lithium disilicate (IPS e.max Press HT High Translucency – Ivoclar Vivadent – Schaan/Liechtenstein) indenter of 3.18 mm radius, positioned in contact with marginal ridges, which was replaced every 500,000 cycles. Fatigue loading was initiated on the mesial marginal ridge until failure or 10 6 cycles; fatigue was subsequently conducted following the same methodology on the distal marginal ridge ( Fig. 3 E and F). This sequence of loading was sequentially altered after every five samples to initiate on the distal ridge and then on the mesial to minimize bias. Every 125,000 cycles the fatigue test was interrupted for crowns and ceramic indenter surface damage inspection under a stereomicroscope (Leica Zeiss MZE, Mannheim, Germany) illuminated by an external light source (Leica CL5 150D, Mannheim, Germany). The specimens and indenters were repositioned and checked by double-sided occlusal marking film for fatigue of additional 125,000 cycles until next inspection. The second location of fatigue testing in a sample, which occurred at the opposite marginal ridge, was only performed when damage (fracture or detectable cracks) was confined to the first fatigued marginal ridge.
Porcelain cohesive fracture or delamination of veneering ceramic, or core bulk fracture were used as criteria for failure, whereas the marginal ridges that presented only cracks or quasi-plastic mode were deemed suspended after 10 6 cycles. After mechanical testing, the marginal ridges classified as failure were inspected at the scanning electron microscope (SEM) and the suspended samples were embedded in epoxy resin (Resina Epoxica RD6921, Redelease, São Paulo, Brazil), and serially polished along crack extension with increasingly finer grit silicon carbide papers (100, 240, 320, 400, 500, 600 grits), under copious water irrigation, followed by 6 and 3 μm diamond pastes (Arotec, São Paulo, Brazil) applied on wet cloths. Subsurface damage was inspected by means of a stereomicroscope (Leica Zeiss MZE, Mannheim, Germany).
In an attempt to determine if there was any difference between cycling on the mesial and distal marginal ridge in the same crown the Kruskal–Wallis and Wilcoxon matched pair test with an α set to 0.05 significance level was performed. The number of cycles for failure during fatigue were recorded for Weibull analysis (Synthesis 9, Weibull 9++; Reliasoft, Tucson, AZ, USA). A probability Weibull plot was used to illustrate data distribution as a function of elapsed cycles. For fatigue life differences between groups, a contour plot was created using Weibull modulus ( m ) vs. characteristic value Eta (cycles) (90% 2-sided confidence bounds). Non-overlap of contour plots indicates a significant difference between groups. Finally, the probability of survival at accumulated fatigue intervals used for sample inspection (every 125,000 cycles) was calculated and also presented in a plot. Reliability predictions beyond 1 million cycles were made only for groups with a probability of survival ≥10% at the end of tests.
3
Results
The probability Weibull plot shows a narrower scatter in data for metal ceramic groups (failures occurring in a more homogeneous range of cycles) relative to PFZ resulting in a more steep confidence line for the former ( Fig. 4 a). The contour plot, presented in Fig. 4 b depicts the number of cycles vs. Weibull modulus (which indicates the amount of cycles at which 63.2% of the specimens of each group would fail) for group comparison ( Table 1 ). Note that, although the PFZev group showed the broadest cycle distribution, its contour overlapped with that of the PFZm group and therefore were not statistically different. MCev and MCm groups also overlapped but only the latter overlapped with PFZm. For this reason, a detailed probability of survival characterization was made to detect the cycle interval where differences between groups started to occur ( Table 2 ). A significant decrease in probability of survival between groups started to occur at 625,000 cycles, and it was observed only for MCev (9.84%) compared to PFZev (43.69%). At 750,000, 875,000, and 1 million cycle intervals, MCev presented a significantly lower probability of survival compared to both PFZ groups, whereas MCm presented intermediate values. Since survival probability was less than 10% at 1 million cycles for both metal ceramic groups, predictions at 1,5 and 2 million cycles were only made for porcelain fused to zirconia crowns, which presented a non-significant decrease neither as a function of cycles nor of framework design (confidence bound overlap). The reliability plot ( Fig. 4 c) depicts the data shown in Table 2 where the probability of survival sequentially decreases for groups PFZev, PFZm, MCm, and MCev, respectively.
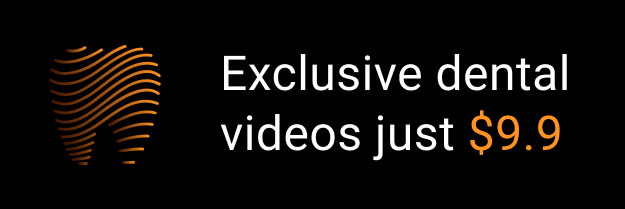