Abstract
Objective
Novel root-end filling materials are composed of tricalcium silicate (TCS) and radiopacifier as opposed to the traditional mineral trioxide aggregate (MTA) which is made up of clinker derived from Portland cement and bismuth oxide. The aim of this research was to characterize and investigate the hydration of a tricalcium silicate-based proprietary brand cement (Biodentine™) and a laboratory manufactured cement made with a mixture of tricalcium silicate and zirconium oxide (TCS-20-Z) and compare their properties to MTA Angelus™.
Methods
The materials investigated included a cement containing 80% of TCS and 20% zirconium oxide (TCS-20-Z), Biodentine™ and MTA Angelus™. The specific surface area and the particle size distribution of the un-hydrated cements and zirconium oxide were investigated using a gas adsorption method and scanning electron microscopy. Un-hydrated cements and set materials were tested for mineralogy and microstructure, assessment of bioactivity and hydration. Scanning electron microscopy, X-ray energy dispersive analysis, X-ray fluorescence spectroscopy, X-ray diffraction, Rietveld refined X-ray diffraction and calorimetry were employed. The radiopacity of the materials was investigated using ISO 6876 methods.
Results
The un-hydrated cements were composed of tricalcium silicate and a radiopacifier phase; zirconium oxide for both Biodentine™ and TCS-20-Z whereas bismuth oxide for MTA Angelus™. In addition Biodentine™ contained calcium carbonate particles and MTA Angelus™ exhibited the presence of dicalcium silicate, tricalcium aluminate, calcium, aluminum and silicon oxides. TCS and MTA Angelus™ exhibited similar specific surface area while Biodentine™ had a greater specific surface area. The cements hydrated and produced some hydrates located either as reaction rim around the tricalcium silicate grain or in between the grains at the expense of volume containing the water initially present in the mixture. The rate of reaction of tricalcium calcium silicate was higher for Biodentine™ than for TCS-20-Z owing to its optimized particle size distribution, the presence of CaCO 3 and the use of CaCl 2 . Tricalcium calcium silicate in MTA hydrated even more slowly than TCS-20-Z as evident from the size of reaction rim representative of calcium silicate hydrate (C-S-H) around tricalcium silicate grains and the calorimetry measurements. On the other hand, calcium oxide contained in MTA Angelus™ hydrated very fast inducing an intense exothermic reaction. Calcium hydroxide was produced as a by-product of reaction in all hydrated cements but in greater quantities in MTA due to the hydration of calcium oxide. This lead to less dense microstructure than the one observed for both Biodentine™ and TCS-20-Z. All the materials were bioactive and allowed the deposition of hydroxyapatite on the cement surface in the presence of simulated body fluid and the radiopacity was greater than 3 mm aluminum thickness.
Significance
All the cement pastes tested were composed mainly of tricalcium silicate and a radiopacifier. The laboratory manufactured cement contained no other additives. Biodentine™ included calcium carbonate which together with the additives in the mixing liquid resulted in a material with enhanced chemical properties relative to TCS-20-Z prototype cement. On the other hand MTA Angelus™ displayed the presence of calcium, aluminum and silicon oxides in the un-hydrated powder. These phases are normally associated with the raw materials indicating that the clinker of MTA Angelus™ is incompletely sintered leading to a potential important variability in its mineralogy depending on the sintering conditions. As a consequence, the amount of tricalcium silicate is less than in the two other cements leading to a slower reaction rate and more porous microstructure.
1
Introduction
Mineral trioxide aggregate (MTA) is composed of Portland cement clinker (80%) and bismuth oxide (20%) . As a consequence the main constituent and most reactive phase of mineral trioxide aggregate (such as ProRoot MTA) is tricalcium silicate which comprises about 68% of the Portland cement component . The percentage of tricalcium silicate in Portland cement can vary largely between brands due to the manufacturing process and the type of raw material used. Moreover the raw materials used in Portland cement production and the type of fuels used for the kiln contain minor elements that can be incorporated to tricalcium silicate leading to the stabilization of different polymorphs that hydrate with different kinetics. As a consequence, daily variations between cement batches can lead to different reactivity and final properties. Conversely dental cements only based on tricalcium silicate are likely to be more reliable. Indeed adequate quantities of tricalcium silicate can be manufactured with pure raw materials in controlled conditions leading to constant properties.
Tricalcium silicate has been used as a bone cement and has shown adequate biocompatibility and bioactivity . The apatite forming ability is enhanced with the addition of calcium fluoride . Composite materials based on tricalcium silicate, which include calcium and sodium carbonate , calcium sulphate hemihydrate and monocalcium phosphate monohydrate result in accelerated cement with improved physical properties.
Tricalcium silicate is bioactive and hydrates into calcium silicate hydrate (C-S-H) and calcium hydroxide (Portlandite) which reacts in the presence of physiological fluids producing hydroxyapatite mostly at the surface of the tricalcium silicate paste . Tricalcium silicate paste is biocompatible and induces differentiation of human dental pulp cells in a similar method as calcium hydroxide . The addition of calcium chloride to tricalcium silicate used for a dental application resulted in an accelerated cement which exhibited enhanced bioactivity and biocompatibility when exposed to L929 cells . Attempts at replacing the Portland cement component of MTA with tricalcium silicate resulted in a material of adequate physical properties .
Dental materials based on tricalcium silicate have been developed. These materials are synthesized in the laboratory from high purity raw materials unlike the Portland cement in MTA. One such formulation is Biodentine™ (Septodont) which was developed as dentin replacement material. Other uses for this material include restoration of deep and large coronal carious lesions, restoration of deep cervical and radicular lesions, pulp capping and pulpotomy, repair of root perforations, furcation perforations, perforating internal resorptions, external resorption, apexification and root-end filling in endodontic surgery. Biodentine™ is presented as a powder consisting of tricalcium silicate (main component), dicalcium silicate (second main component) and calcium oxide; calcium carbonate (filler material); and zirconium oxide as a radiopacifier. The liquid for mixing with the cement powder consists of calcium chloride (decreases the setting time) and a hydrosoluble polymer (water reducing agent) in order to keep a good flowability with a low water/solid ratio . Biodentine has been shown to be biocompatible . Biodentine™ caused the uptake of Ca and Si in the adjacent root canal dentin in the presence of physiological solution .
The aim of this research was to characterize MTA Angelus™, Biodentine™ and a laboratory made radiopacified tricalcium silicate cement named TCS-20-Z and then to investigate their hydration in order to first, define the difference between clinker based dental materials compared to tricalcium silicate based ones and secondly, compare Biodentine™ that is an optimized tricalcium silicate-based dental material to laboratory made mixture of tricalcium silicate and zirconium oxide. These results are expected to demonstrate the advantage of using tricalcium silicate-based dental cement as these systems can be efficiently tuned to achieve the required performance on account of all research that has been conducted on this mineral in the field of cement chemistry for more than one century.
2
Methodology
The materials used in this study included:
- –
Tricalcium silicate (Mineral Research Processing, Meyzieu, France);
- –
A prototype laboratory made cement made with 80% tricalcium silicate (Mineral Research Processing, Meyzieu, France) and 20% zirconium oxide (ZrO 2 ; Sigma–Aldrich, Buchs, Germany) – TCS-20-Z. TCS-20-Z was prepared by mixing both constituents for several minutes to get a homogenized powder.
- –
Biodentine™ (Septodont, Saint-Maur-des-fossés Cedex, France);
- –
MTA Angelus™ (Angelus Soluções Odontológicas, Londrina PR, Brazil);
The TCS-20-Z was mixed with pure water (water/tricalcium silicate ratio of 0.35) and Biodentine™ and MTA Angelus™ were mixed according to manufacturer’s instructions.
2.1
Assessment of un-hydrated cements
The quantitative chemical composition was performed by X-ray fluorescence (XRF) on pellets made with lithium tetra-borate using Bruker S4 spectrometer. Before performing XRF analysis, the samples were heated to 1000 °C to check if the sample contained carbonated or hydrates minerals in order to correct the XRF analysis accordingly.
Phase analysis was carried out on un-hydrated powders and set cements. A Bruker D8 diffractometer with Co Kα radiation (1.78 Å) was used. The X-ray patterns were acquired in the 2 θ (5–60°) with a step of 0.019° and 3 s per step. Phase identification was accomplished by use of search-match software utilizing ICDD database (International Center for Diffraction Data, Newtown Square, PA, USA). In addition Rietveld refinement was performed on the un-hydrated cements in order to determine their phase composition quantitatively. These results were cross checked with the XRF analysis.
Powders were mounted in resin (Araldite, Huntsman Advanced Materials, Duxford, Cambridge, UK) and polished using a series of diamond discs and polishing cloths of reducing abrasiveness. The resin blocks were carbon coated and were then viewed in back-scatter mode under the scanning electron microscope (SEM; Hitachi S4300 SE/N, Bunkyo-ku, Tokyo, Japan). Elemental analysis by X-ray energy dispersive analysis (EDX) was also performed mostly to determine if some foreign elements were present in calcium silicate phases in conjunction to the stabilization of different polymorphs. The mineralogy was also used to investigate the sintering conditions (mostly using the size of the crystals of the clinker and by checking if small amounts of unreacted constituents were still present).
The specific surface area of the un-hydrated cements and zirconium oxide was determined by the BET (Brunauer–Emmett–Teller) gas adsorption method using extended pressure sorption analyser (Micromeritics ASAP 2010, Micromeritics Instruments Corporation, Norcross, GA, USA). Nitrogen gas was used at different pressures to determine the physical adsorption of gas molecules on a solid surface. SEM observations on polished section also gave a qualitative assessment of the particle size distribution of the different constituents of the cement.
2.2
Assessment of hydrated cement pastes
The kinetics of hydration of the cement paste was followed by isothermal calorimetry performed on paste at 37 °C. The heat flux released by the chemical reaction was monitored over time and enabled the estimation of the beginning of setting and the rate of increase of the mechanical performance of the cement paste. The calorimeter used was a home-made calorimeter using fluxmeters that allowed the calorimeter to equilibrate in less than 2 min after the cells were placed in it. Thus, it was possible to record the heat flux released till the hydration beginning even if the mixing of the cement paste was performed outside the calorimeter. Microscopy and EDX analysis were also performed on the cement paste after 1 day. After 1 day, the samples recovered from the calorimetry experiments were dried in acetone ether rinse before being oven dried at 40 °C for 1 week. The reaction rims around the remaining un-hydrated minerals and the radiopacifier phase were observed. Hydration characteristics of the cement were assessed by plotting the calcium to silicon ratios of the cement particle and the reaction rims. The inclusion of the radiopacifier phase in the cement hydration process was assessed by plotting the radiopacifier to calcium ratio plots of the radiopacifier phase and surrounding cement matrix.
Additional experiments were performed on set cement pastes that were stored in gelatinized Hank’s balanced salt solution (HBSS) for 1 day and 28 days prior to testing using X-ray diffraction (XRD). The composition of HBSS was 0.4 M KCl, 0.06 M KH 2 PO 4 anhydrous, 0.35 M NaHCO 3 , 8.0 M NaCl, 0.05 M Na 2 HPO 4 anhydrous, and 1.0 M d -glucose. The HBSS was gelatinized by adding 20% porcine gelatin (Fluka Biochemika, Fluka Chemie GmbH, Buchs, Germany) and heating continuously until boiling. Once cooled the gelatinized HBSS was poured over the unset specimens and allowed to set. The specimens were cured for 28 days at 37 °C in an incubator. The diffractometer (Rigaku, Tokyo, Japan) used Cu Kα radiation at 40 mA and 45 kV. The detector was rotated between 15° and 45°, a sampling width of 0.05° and 2°/min scan speed was used. The cement pastes were crushed using a mortar and pestle prior to testing. Phase identification was accomplished by use of search-match software utilizing ICDD database.
Surface topography of the hydrated cements immersed in gelatinized HBSS at 37 ± 1 °C after 1 day was also performed in order to investigate the bioactivity potential of the materials.
Radiopacity evaluation was performed using ISO 6876 recommendations . Three specimens 10 ± 1 mm in diameter and 1 ± 0.1 mm thick were used. A total of 15 specimens were prepared. They were radiographed after 1 day and 28 days. In the interim the specimens were kept in gelatinized HBSS at 37 °C. At each time point the specimens were placed directly on a photo-stimulable phosphor (PSP) plate adjacent to a calibrated aluminum step wedge (Everything X-ray, High Wycombe, UK) with 3 mm increments. A standard X-ray machine (GEC Medical Equipment Ltd., Middlesex, UK) was used to irradiate X-rays onto the specimens using an exposure time of 0.48 s at 10 mA, tube voltage at 65 ± 5 kV and a cathode-target film distance of 300 ± 10 mm. The radiographs were processed (Clarimat 300, Gendex Dental Systems, Medivance Instruments Ltd., London, UK) and a digital image of the radiograph was obtained. The gray pixel value on the radiograph, of each step in the step-wedge was determined using an imaging program, Microsoft Paint (Microsoft Corp., Redmond, WA, USA) as a number between 0 and 255 with 0 representing pure black and 255 pure white. A graph of thickness of aluminum vs. gray pixel value on the radiograph was then plotted and the best-fit logarithmic trend line was plotted through the points. The equation of the trend line gave the gray pixel value of an object on the image as a function of the object’s thickness in mm of aluminum. This equation was inverted so as to express the object’s thickness as a function of its gray pixel value on the radiograph. The gray pixel values of the cement specimens were then determined using the imaging program, and plugged into this equation to calculate the equivalent radiopacity of the cement sample, expressed in mm of aluminum.
2
Methodology
The materials used in this study included:
- –
Tricalcium silicate (Mineral Research Processing, Meyzieu, France);
- –
A prototype laboratory made cement made with 80% tricalcium silicate (Mineral Research Processing, Meyzieu, France) and 20% zirconium oxide (ZrO 2 ; Sigma–Aldrich, Buchs, Germany) – TCS-20-Z. TCS-20-Z was prepared by mixing both constituents for several minutes to get a homogenized powder.
- –
Biodentine™ (Septodont, Saint-Maur-des-fossés Cedex, France);
- –
MTA Angelus™ (Angelus Soluções Odontológicas, Londrina PR, Brazil);
The TCS-20-Z was mixed with pure water (water/tricalcium silicate ratio of 0.35) and Biodentine™ and MTA Angelus™ were mixed according to manufacturer’s instructions.
2.1
Assessment of un-hydrated cements
The quantitative chemical composition was performed by X-ray fluorescence (XRF) on pellets made with lithium tetra-borate using Bruker S4 spectrometer. Before performing XRF analysis, the samples were heated to 1000 °C to check if the sample contained carbonated or hydrates minerals in order to correct the XRF analysis accordingly.
Phase analysis was carried out on un-hydrated powders and set cements. A Bruker D8 diffractometer with Co Kα radiation (1.78 Å) was used. The X-ray patterns were acquired in the 2 θ (5–60°) with a step of 0.019° and 3 s per step. Phase identification was accomplished by use of search-match software utilizing ICDD database (International Center for Diffraction Data, Newtown Square, PA, USA). In addition Rietveld refinement was performed on the un-hydrated cements in order to determine their phase composition quantitatively. These results were cross checked with the XRF analysis.
Powders were mounted in resin (Araldite, Huntsman Advanced Materials, Duxford, Cambridge, UK) and polished using a series of diamond discs and polishing cloths of reducing abrasiveness. The resin blocks were carbon coated and were then viewed in back-scatter mode under the scanning electron microscope (SEM; Hitachi S4300 SE/N, Bunkyo-ku, Tokyo, Japan). Elemental analysis by X-ray energy dispersive analysis (EDX) was also performed mostly to determine if some foreign elements were present in calcium silicate phases in conjunction to the stabilization of different polymorphs. The mineralogy was also used to investigate the sintering conditions (mostly using the size of the crystals of the clinker and by checking if small amounts of unreacted constituents were still present).
The specific surface area of the un-hydrated cements and zirconium oxide was determined by the BET (Brunauer–Emmett–Teller) gas adsorption method using extended pressure sorption analyser (Micromeritics ASAP 2010, Micromeritics Instruments Corporation, Norcross, GA, USA). Nitrogen gas was used at different pressures to determine the physical adsorption of gas molecules on a solid surface. SEM observations on polished section also gave a qualitative assessment of the particle size distribution of the different constituents of the cement.
2.2
Assessment of hydrated cement pastes
The kinetics of hydration of the cement paste was followed by isothermal calorimetry performed on paste at 37 °C. The heat flux released by the chemical reaction was monitored over time and enabled the estimation of the beginning of setting and the rate of increase of the mechanical performance of the cement paste. The calorimeter used was a home-made calorimeter using fluxmeters that allowed the calorimeter to equilibrate in less than 2 min after the cells were placed in it. Thus, it was possible to record the heat flux released till the hydration beginning even if the mixing of the cement paste was performed outside the calorimeter. Microscopy and EDX analysis were also performed on the cement paste after 1 day. After 1 day, the samples recovered from the calorimetry experiments were dried in acetone ether rinse before being oven dried at 40 °C for 1 week. The reaction rims around the remaining un-hydrated minerals and the radiopacifier phase were observed. Hydration characteristics of the cement were assessed by plotting the calcium to silicon ratios of the cement particle and the reaction rims. The inclusion of the radiopacifier phase in the cement hydration process was assessed by plotting the radiopacifier to calcium ratio plots of the radiopacifier phase and surrounding cement matrix.
Additional experiments were performed on set cement pastes that were stored in gelatinized Hank’s balanced salt solution (HBSS) for 1 day and 28 days prior to testing using X-ray diffraction (XRD). The composition of HBSS was 0.4 M KCl, 0.06 M KH 2 PO 4 anhydrous, 0.35 M NaHCO 3 , 8.0 M NaCl, 0.05 M Na 2 HPO 4 anhydrous, and 1.0 M d -glucose. The HBSS was gelatinized by adding 20% porcine gelatin (Fluka Biochemika, Fluka Chemie GmbH, Buchs, Germany) and heating continuously until boiling. Once cooled the gelatinized HBSS was poured over the unset specimens and allowed to set. The specimens were cured for 28 days at 37 °C in an incubator. The diffractometer (Rigaku, Tokyo, Japan) used Cu Kα radiation at 40 mA and 45 kV. The detector was rotated between 15° and 45°, a sampling width of 0.05° and 2°/min scan speed was used. The cement pastes were crushed using a mortar and pestle prior to testing. Phase identification was accomplished by use of search-match software utilizing ICDD database.
Surface topography of the hydrated cements immersed in gelatinized HBSS at 37 ± 1 °C after 1 day was also performed in order to investigate the bioactivity potential of the materials.
Radiopacity evaluation was performed using ISO 6876 recommendations . Three specimens 10 ± 1 mm in diameter and 1 ± 0.1 mm thick were used. A total of 15 specimens were prepared. They were radiographed after 1 day and 28 days. In the interim the specimens were kept in gelatinized HBSS at 37 °C. At each time point the specimens were placed directly on a photo-stimulable phosphor (PSP) plate adjacent to a calibrated aluminum step wedge (Everything X-ray, High Wycombe, UK) with 3 mm increments. A standard X-ray machine (GEC Medical Equipment Ltd., Middlesex, UK) was used to irradiate X-rays onto the specimens using an exposure time of 0.48 s at 10 mA, tube voltage at 65 ± 5 kV and a cathode-target film distance of 300 ± 10 mm. The radiographs were processed (Clarimat 300, Gendex Dental Systems, Medivance Instruments Ltd., London, UK) and a digital image of the radiograph was obtained. The gray pixel value on the radiograph, of each step in the step-wedge was determined using an imaging program, Microsoft Paint (Microsoft Corp., Redmond, WA, USA) as a number between 0 and 255 with 0 representing pure black and 255 pure white. A graph of thickness of aluminum vs. gray pixel value on the radiograph was then plotted and the best-fit logarithmic trend line was plotted through the points. The equation of the trend line gave the gray pixel value of an object on the image as a function of the object’s thickness in mm of aluminum. This equation was inverted so as to express the object’s thickness as a function of its gray pixel value on the radiograph. The gray pixel values of the cement specimens were then determined using the imaging program, and plugged into this equation to calculate the equivalent radiopacity of the cement sample, expressed in mm of aluminum.
3
Results
3.1
Evaluation of un-hydrated cements
The results of the quantitative analysis by XRF are shown in Table 1 . All the materials were composed of oxygen, silicon and calcium. In addition MTA Angelus™ contained minor content of aluminum and minimal proportions of strontium, iron and magnesium. Biodentine™ had only traces of iron. The presence of Mg, Sr and Fe as minor elements in MTA Angelus™ indicated that the source of CaCO 3 was not pure CaCO 3 obtained by precipitation. Thus CaCO 3 certainly came from natural limestone of high purity. On the contrary Biodentine™ and TCS did not contain such minor elements indicating that these products are made from pure constituents. In addition MTA did not contain sulfur. The absence of the setting regulator in MTA may induce some flash setting depending on the amount of tricalcium aluminate. Also all cements did not contain Na or K that are common impurities in clinker of Portland cement. Biodentine™ and MTA Angelus™ included zirconium and bismuth as radiopacifiers respectively.
Elements identified | Material type | ||
---|---|---|---|
TCS | Biodentine | MTA Angelus | |
Oxygen | 34.9 | 41.7 | 34.2 |
Calcium | 52.9 | 45.3 | 43.4 |
Silicon | 12.2 | 9.2 | 7.6 |
Aluminum | – | Traces | 1.5 |
Magnesium | – | Traces | 0.1 |
Phosphorus | – | – | Traces |
Iron | – | 0.2 | 0.1 |
Bismuth | – | – | 12.8 |
Tantalum | – | – | – |
Zirconium | – | 3.5 | – |
Strontium | – | – | 0.2 |
Copper | – | – | Traces |
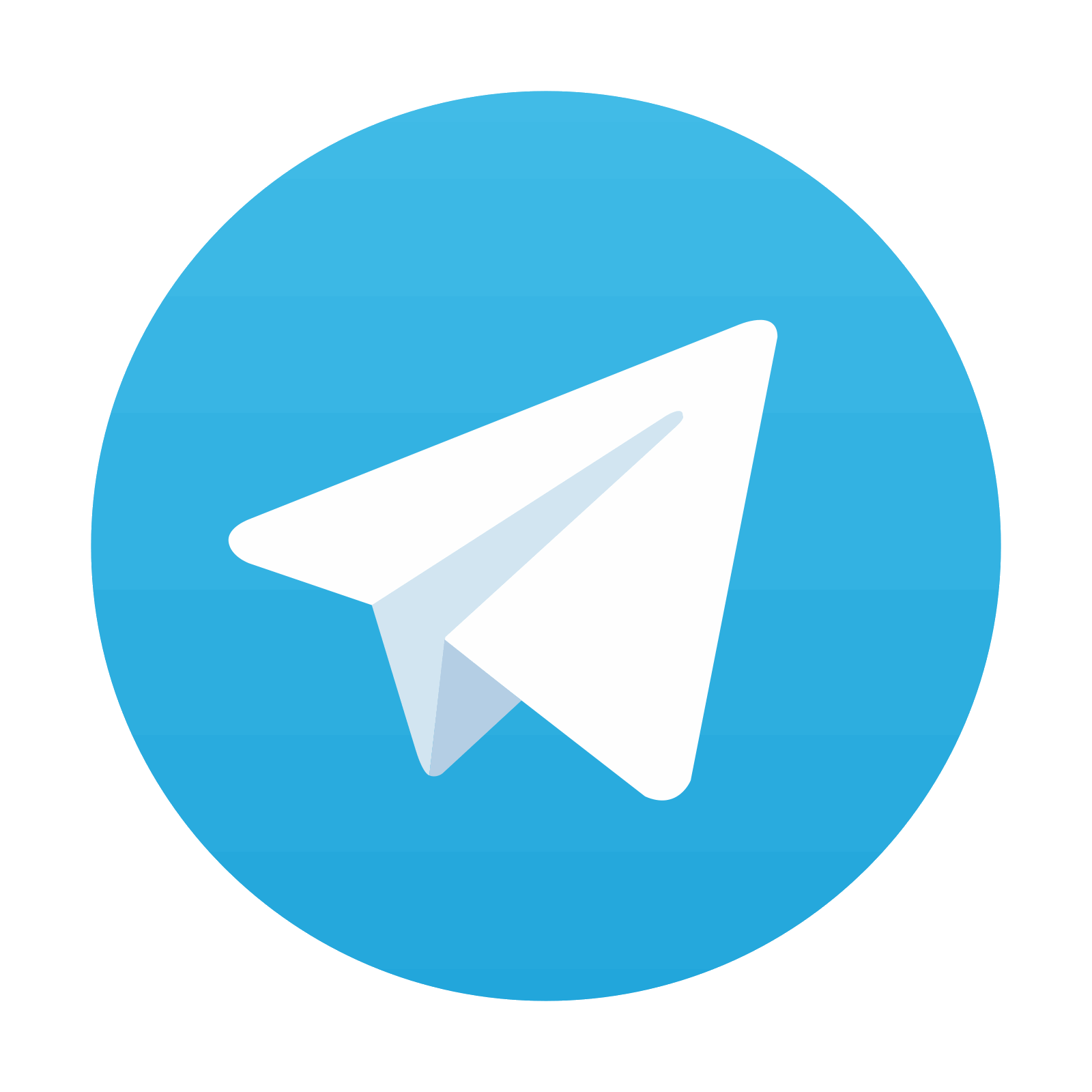
Stay updated, free dental videos. Join our Telegram channel

VIDEdental - Online dental courses
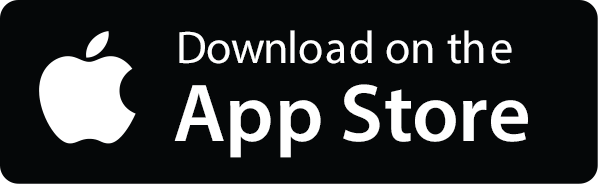

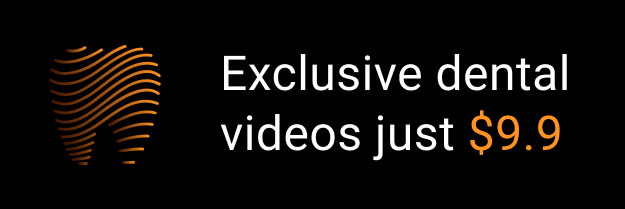