Highlights
- •
Effect of extensive adjustment on both ISO specimens and realistic crowns was assessed.
- •
Profilometric & Weibull analysis, REM, and finite element analysis were used.
- •
The results emphasize the necessity to avoid extensive intraoral adjustment in veneered (max. thickness 2 mm) zirconia restorations.
Abstract
Objectives
The purpose of this study was to assess the effect of surface treatment on the fracture resistance of zirconia-based all-ceramic anterior crowns.
Methods
Sixty-four zirconia-based all-ceramic anterior crowns, veneered by use of a press-on technique, were produced. For 48 crowns intraoral adjustment was simulated (A-group), 16 crowns remained unadjusted (WA-group). The adjusted area was then treated in three ways: 1. no further surface treatment; 2. polishing, with irrigation, using polishers interspersed with diamond grit for ceramics; and 3. polishing and glaze firing. Half of the specimens were loaded until fracture in an universal testing device without artificial ageing; the other crowns underwent thermocycling and chewing simulation before ultimate-load testing. Explorative statistical analysis was performed by use of non-parametric and parametric tests. In addition, fracture-strength tests according to ISO 6872 were performed for veneer ceramic subjected to the different surface treatments. Finite element analysis was also conducted for the crowns, and surface roughness was measured.
Results
Crowns in the A-group were more sensitive to aging than crowns in the WA-group ( p = 0.038). Although both polishing and glaze firing slightly improved the fracture resistance of the specimens, the fracture resistance in the WA-group (initial fracture resistance (IFR): 652.0 ± 107.7 N, remaining fracture resistance after aging (RFR): 560.6 ± 233.3 N) was higher than the fracture resistance in the A-group (polished: IFR: 477.9 ± 108.8 N, RFR: 386.0 ± 218.5 N; glaze firing: IFR: 535.5 ± 128.0 N, RFR: 388.6 ± 202.2 N). Surface roughness without adjustment was R a = 0.1 μm; for adjustment but without further treatment it was R a = 1.4 μm; for adjustment and polishing it was R a = 0.3 μm; and for adjustment, polishing, and glazing it was R a = 0.6 μm. Stress distributions obtained by finite element analysis in combination with fracture strength tests showed that fractures most probably originated from the occlusal surface.
Significance
To improve fracture resistance and reduce the incidence of failure, extensive occlusal adjustment of veneered anterior zirconia restorations should be avoided. Neither polishing nor glazing could restore the fracture resistance to the level maintained with unadjusted crowns.
1
Introduction
In recent years veneered fixed zirconia restorations (FDPs) have often been used for restoration of decayed teeth. In the anterior region, especially, the advantages of all-ceramic FDPs are striking—almost natural translucency and transparency, no visible metal parts in the cervical area of the restoration, and good biocompatibility encourage use of this material in this challenging area.
It has been shown, however, that cohesive and adhesive failure of the veneer (i.e. chipping and/or delamination) occur more frequently for all-ceramic restorations than for metal–ceramic restorations . Several methods have been investigated in attempts to reduce this type of failure: alteration of the firing procedure , production of CAD/CAM-manufactured veneer , and replacement of feldspathic ceramic with lithium disilicate ceramic in production of the veneer . In in-vitro studies these technical approaches have been proved to reduce cohesive and adhesive failure as a result of fatigue (thermocycling and chewing simulation) and to enhance fracture resistance . It has also been shown that the mechanical behaviour of bilayered all-ceramic (veneered zirconia) discs and bars is negatively affected by a rough veneer surface . The effect of several surface-treatment techniques (polishing, glaze firing) on the roughness and mechanical properties of such specimens has also been assessed . These investigations were, however, performed on standardized specimens, for example discs or bars. Thus, the effect of geometry and dimensions has not been assessed experimentally. Geometry and dimensional aspects are crucial, however, because, for example, the design of the core material affects the in-vitro performance of crowns , and the ratio of the thickness of the core to that of the veneer might affect the mechanical behaviour of bilayered ceramic specimens and the residual thermal stress within the restorations . Kelly et al. recently concluded that in-vitro tests should “more closely simulate clinical conditions”. Simple “crash the crown” study designs without further stress analysis are not recommended, however. In this study, therefore, we have tried to combine the advantages of both in-vitro experiments and finite element analysis, as recommended by Anusavice et al. .
Information about the effect of surface treatment on the performance of all-ceramic restorations is highly important to the dentist, because occlusal adjustment—resulting in rough surfaces—before cementation is very common. This approach introduces flaws into the restoration, however, and it would be helpful for dentists to know how to reduce the risk of failure as a result of these flaws.
The hypothesis of this study was that additional glaze firing after such adjustment would result in significantly higher loads than use of polishing procedures.
2
Material and methods
2.1
Manufacturing and testing of the crowns
An artificial upper central incisor (KaVo cast teeth) was prepared (0.8 mm chamfer, incisal reduction 2.4 mm, circumferential reduction 0.8 mm). A plaster cast containing this incisor was fabricated, and the artificial incisor was duplicated 64 times in CoCrMo alloy by use of the prepared die. The duplicated incisors were embedded in aluminium moulds by use of cold-curing resin (Technovit 4071; Heraeus Kulzer GmbH, Hanau, Germany). For these artificial incisors, 64 identical zirconia copings (Cercon base, DeguDent, Hanau-Wolfgang, Germany) with 0.4 mm wall thickness were constructed and milled. The veneer was designed by use of commercial dental CAD/CAM software (DentalDesigner; 3Shape, Copenhagen, Denmark), and later modified at the incisor edge (Rapidform Dental; INUS Technology, Seoul, Korea). Two modifications were performed: first, the oral part of the veneer beneath the edge of the incisor was made planar; subsequently an ellipsoidal bump (4 mm × 1.5 mm × 0.5 mm, cf. Fig. 1 a) was placed at the location of the planned load application point. Veneer for 48 crowns was then milled with this raised height and veneer for 16 crowns was milled without the raised height, by use of Cercon base cast (DeguDent). Cercon base cast is a polyurethane blank for fabrication of copings that burns off without leaving a residue.
The copings were abraded with airborne particles (P-G400; Harnisch&Rieth, Winterbach, Germany; aluminium oxide, 110 μm, 2.0 bar) and steam-cleaned. The copings with the adjusted resin veneer were inserted (Cergo fit speed, DeguDent), the resin veneer was burnt off at 850 °C for 60 min. (KaVo furnace, type 5646), and the copings were pressed over in a Cergo Press (DeguDent) furnace by use of a Cercon ceram press (DeguDent). Conditions used for pressing the veneer were: start temperature, 700 °C; rate of temperature increase, 60°/min; final temperature, 940 °C; pressing time, 10 min; holding time, 20 min; pressure, 5 bar. After pressing and removal, the sprues were removed by use of a high-speed turbine (Bien-air Dental-SA, Sirius Dental Innovations, Bienne, Switzerland), with irrigation (50 ml/min). Finally, the crowns were glaze-fired (desiccation, 123 °C for 2 min; preheating, 450 °C; rate of temperature increase, 55°/min; final temperature, 800 °C for 1 min, cooling time, 6 min).
All crowns with ellipsoidal height increases ( n = 48) underwent simulated occlusal adjustment by use of a high-speed turbine (Bien-air Dental), with irrigation; a bur (grain size: 46 μm; Brasseler, #836KREF.314.012; cylinder with round edge) was used to remove the height increases. For each adjustment a new bur was used. The direction of preparation was perpendicular to the incisal edge of the crown. After occlusal adjustment, these crowns had the same geometry as the specimens without bumps (WA-group, n = 16) for which there had been no surface treatment. The adjusted crowns (A-group) were divided into three subgroups ( n = 16 each) with:
- A1
polishing of the adjusted area (10,000 revolutions per minute), with irrigation, by use of polishers interspersed with diamond grit for ceramics (Brasseler, #4313B.204).
- A2
polishing as above and additional glaze firing.
- A3
no additional surface treatment.
One dentist and one dental technician were involved in the manufacturing of all specimens, each one taking care of the same processes as done in clinical praxis, e.g., adjustment and polishing were performed by the dentist, whereas crown fabrication and additional glazing were done by the dental technician.
The surfaces of some exemplary crowns were studied by scanning electron microscopy (Amray 1810 scanning electron microscope). In addition, the surface roughness of typical crowns from each subgroup ( n = 2) was measured by use of a Perthometer M2 (Mahr, Goettingen, Germany) equipped with NHT 6-100 calipers and MarSurf XR20 software. The measurement length was 1.75 mm, the measurement velocity was 0.5 mm/s, and measurement was repeated five times for each specimen.
The inner surface of all copings was abraded with airborne particles (P-G400; Harnisch&Rieth, Winterbach, Germany; aluminium oxide, 50 μm, 2.0 bar). All copings were then ultrasonically cleaned for 2 min with 95% isopropyl alcohol (Sonorex super RK 102H; Bandelin, Berlin, Germany). The crowns were adhesively luted to the dies by use of Panavia 21 (Kuraray, Japan). For each test group ( n = 16 crowns), half of the specimens were directly destroyed in fracture tests (initial fracture resistance) whereas the others were exposed to artificial ageing consisting of 10,000 thermocycles (6.5 °C and 60 °C, dwell time 90 s; TC 1; Willytec, Graefelfing, Germany) and 1.2 million chewing cycles (purely vertical movement, maximum force magnitude F max = 108 N, water storage, and Willytec CS3 modified with a spring-damper system for controlled force overshoot in respect of the static load), with subsequent monitoring by light microscopy (Stemi SR; Carl Zeiss, Oberkochen, Germany), to identify cracks, flaws, etc., before fracture tests of all surviving crowns (to determine remaining fracture resistance).
In chewing simulation and fracture tests, loads were applied by use of a steel sphere ( d = 6 mm) 1.3 mm in the apical direction from the centre of the incisal edge (cf. Fig. 1 b) at an angle of 90° to the buccal side of the tooth. Fracture tests were performed with an universal testing machine (Universal-Pruefmaschine-Z005; Zwick, Ulm, Germany), at a cross-head speed of 0.5 mm min −1 .
2.2
Fracture-strength tests
Specimens of dimensions 3 mm × 4 mm × 36 mm were manufactured from the veneer ceramic by use of the press technique. Similar to the crowns, the groups ( n = 10–12) were subjected to different surface treatment:groups without adjustment:
- (1)
surface treatment according to ISO 6872 (final polishing with 15 μm diamond suspension).
- (2)
surface treatment according to ISO 6872 + glaze firing.
groups with adjustment: samples provided an additional ceramic layer (height 0.2 mm) in the mid third of the lower side of the beam, which was ground (EvaWinkelstueck, 46 μm grain size, grinding direction perpendicular to the bar axis).
- (3)
no further adjustment.
- (4)
polishing.
- (5)
polishing + glaze firing.
The three-point bending test ( R = 1.6 mm, L = 32 mm) was performed with a crosshead speed of 0.5 mm/min.
Finally, Weibull strength was determined for each group.
2.3
Finite element analysis
By use of ANSYS 14.0, a finite element model (FEM; cf. Fig. 1 c) of the test setup was constructed by reverse engineering of the stl-files obtained from the CAD/CAM processing. Hexahedral elements with quadratic shape functions were used to mesh the model (55,000 elements, 223,000 nodes). With press-on technique, cooling of the crowns takes place while they are enclosed by investment material, leading to small temperature gradients within the crowns when, e.g., compared to those found for cooling after firings with layering technique . Hence, we assumed a homogeneous temperature within the crown when glass transition temperature was reached. For analysis of the distribution of thermal residual stress (as a result of cooling from the glass transition temperature to 20 °C), statically determined boundary conditions were chosen, whereas for analysis of load stress the complete inner surface of the cement layer was restricted (the metal stump was assumed to be rigid) and an area to area formula describing the contact between the steel sphere and the crown’s surface was used. Material properties used for computations of linear–elastic behaviour are given in Table 1 .
Material | Young’s modulus (GPa) | Poisson’s ratio (–) | Coefficient of thermal expansion (10 −6 K −1 ) | Glass transition temperature (°C) |
---|---|---|---|---|
Zirconia | 210 | 0.26 | 10.5 | – |
Veneer ceramic | 70 | 0.20 | 10.0 * | 540 * |
Resin cement | 6 | 0.40 | – | – |
Steel | 210 | 0.30 | – | – |
2.4
Statistics
Descriptive statistics were used for analysis of means, standard deviations, and medians.
To assess the effect of the surface-treatment procedures the following explorative data analysis was performed: non-parametric tests were used for the crowns (Kruskal-Wallis-test and post-hoc Mann–Whitney U -test with α = 0.05 as significance level) and parametric tests for the bending tests ( t -tests with α = 0.05 as significance level). The results were depicted by use of whisker–boxplots.
2
Material and methods
2.1
Manufacturing and testing of the crowns
An artificial upper central incisor (KaVo cast teeth) was prepared (0.8 mm chamfer, incisal reduction 2.4 mm, circumferential reduction 0.8 mm). A plaster cast containing this incisor was fabricated, and the artificial incisor was duplicated 64 times in CoCrMo alloy by use of the prepared die. The duplicated incisors were embedded in aluminium moulds by use of cold-curing resin (Technovit 4071; Heraeus Kulzer GmbH, Hanau, Germany). For these artificial incisors, 64 identical zirconia copings (Cercon base, DeguDent, Hanau-Wolfgang, Germany) with 0.4 mm wall thickness were constructed and milled. The veneer was designed by use of commercial dental CAD/CAM software (DentalDesigner; 3Shape, Copenhagen, Denmark), and later modified at the incisor edge (Rapidform Dental; INUS Technology, Seoul, Korea). Two modifications were performed: first, the oral part of the veneer beneath the edge of the incisor was made planar; subsequently an ellipsoidal bump (4 mm × 1.5 mm × 0.5 mm, cf. Fig. 1 a) was placed at the location of the planned load application point. Veneer for 48 crowns was then milled with this raised height and veneer for 16 crowns was milled without the raised height, by use of Cercon base cast (DeguDent). Cercon base cast is a polyurethane blank for fabrication of copings that burns off without leaving a residue.
The copings were abraded with airborne particles (P-G400; Harnisch&Rieth, Winterbach, Germany; aluminium oxide, 110 μm, 2.0 bar) and steam-cleaned. The copings with the adjusted resin veneer were inserted (Cergo fit speed, DeguDent), the resin veneer was burnt off at 850 °C for 60 min. (KaVo furnace, type 5646), and the copings were pressed over in a Cergo Press (DeguDent) furnace by use of a Cercon ceram press (DeguDent). Conditions used for pressing the veneer were: start temperature, 700 °C; rate of temperature increase, 60°/min; final temperature, 940 °C; pressing time, 10 min; holding time, 20 min; pressure, 5 bar. After pressing and removal, the sprues were removed by use of a high-speed turbine (Bien-air Dental-SA, Sirius Dental Innovations, Bienne, Switzerland), with irrigation (50 ml/min). Finally, the crowns were glaze-fired (desiccation, 123 °C for 2 min; preheating, 450 °C; rate of temperature increase, 55°/min; final temperature, 800 °C for 1 min, cooling time, 6 min).
All crowns with ellipsoidal height increases ( n = 48) underwent simulated occlusal adjustment by use of a high-speed turbine (Bien-air Dental), with irrigation; a bur (grain size: 46 μm; Brasseler, #836KREF.314.012; cylinder with round edge) was used to remove the height increases. For each adjustment a new bur was used. The direction of preparation was perpendicular to the incisal edge of the crown. After occlusal adjustment, these crowns had the same geometry as the specimens without bumps (WA-group, n = 16) for which there had been no surface treatment. The adjusted crowns (A-group) were divided into three subgroups ( n = 16 each) with:
- A1
polishing of the adjusted area (10,000 revolutions per minute), with irrigation, by use of polishers interspersed with diamond grit for ceramics (Brasseler, #4313B.204).
- A2
polishing as above and additional glaze firing.
- A3
no additional surface treatment.
One dentist and one dental technician were involved in the manufacturing of all specimens, each one taking care of the same processes as done in clinical praxis, e.g., adjustment and polishing were performed by the dentist, whereas crown fabrication and additional glazing were done by the dental technician.
The surfaces of some exemplary crowns were studied by scanning electron microscopy (Amray 1810 scanning electron microscope). In addition, the surface roughness of typical crowns from each subgroup ( n = 2) was measured by use of a Perthometer M2 (Mahr, Goettingen, Germany) equipped with NHT 6-100 calipers and MarSurf XR20 software. The measurement length was 1.75 mm, the measurement velocity was 0.5 mm/s, and measurement was repeated five times for each specimen.
The inner surface of all copings was abraded with airborne particles (P-G400; Harnisch&Rieth, Winterbach, Germany; aluminium oxide, 50 μm, 2.0 bar). All copings were then ultrasonically cleaned for 2 min with 95% isopropyl alcohol (Sonorex super RK 102H; Bandelin, Berlin, Germany). The crowns were adhesively luted to the dies by use of Panavia 21 (Kuraray, Japan). For each test group ( n = 16 crowns), half of the specimens were directly destroyed in fracture tests (initial fracture resistance) whereas the others were exposed to artificial ageing consisting of 10,000 thermocycles (6.5 °C and 60 °C, dwell time 90 s; TC 1; Willytec, Graefelfing, Germany) and 1.2 million chewing cycles (purely vertical movement, maximum force magnitude F max = 108 N, water storage, and Willytec CS3 modified with a spring-damper system for controlled force overshoot in respect of the static load), with subsequent monitoring by light microscopy (Stemi SR; Carl Zeiss, Oberkochen, Germany), to identify cracks, flaws, etc., before fracture tests of all surviving crowns (to determine remaining fracture resistance).
In chewing simulation and fracture tests, loads were applied by use of a steel sphere ( d = 6 mm) 1.3 mm in the apical direction from the centre of the incisal edge (cf. Fig. 1 b) at an angle of 90° to the buccal side of the tooth. Fracture tests were performed with an universal testing machine (Universal-Pruefmaschine-Z005; Zwick, Ulm, Germany), at a cross-head speed of 0.5 mm min −1 .
2.2
Fracture-strength tests
Specimens of dimensions 3 mm × 4 mm × 36 mm were manufactured from the veneer ceramic by use of the press technique. Similar to the crowns, the groups ( n = 10–12) were subjected to different surface treatment:groups without adjustment:
- (1)
surface treatment according to ISO 6872 (final polishing with 15 μm diamond suspension).
- (2)
surface treatment according to ISO 6872 + glaze firing.
groups with adjustment: samples provided an additional ceramic layer (height 0.2 mm) in the mid third of the lower side of the beam, which was ground (EvaWinkelstueck, 46 μm grain size, grinding direction perpendicular to the bar axis).
- (3)
no further adjustment.
- (4)
polishing.
- (5)
polishing + glaze firing.
The three-point bending test ( R = 1.6 mm, L = 32 mm) was performed with a crosshead speed of 0.5 mm/min.
Finally, Weibull strength was determined for each group.
2.3
Finite element analysis
By use of ANSYS 14.0, a finite element model (FEM; cf. Fig. 1 c) of the test setup was constructed by reverse engineering of the stl-files obtained from the CAD/CAM processing. Hexahedral elements with quadratic shape functions were used to mesh the model (55,000 elements, 223,000 nodes). With press-on technique, cooling of the crowns takes place while they are enclosed by investment material, leading to small temperature gradients within the crowns when, e.g., compared to those found for cooling after firings with layering technique . Hence, we assumed a homogeneous temperature within the crown when glass transition temperature was reached. For analysis of the distribution of thermal residual stress (as a result of cooling from the glass transition temperature to 20 °C), statically determined boundary conditions were chosen, whereas for analysis of load stress the complete inner surface of the cement layer was restricted (the metal stump was assumed to be rigid) and an area to area formula describing the contact between the steel sphere and the crown’s surface was used. Material properties used for computations of linear–elastic behaviour are given in Table 1 .
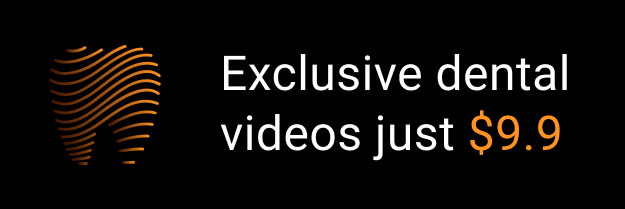