Abstract
Objective
Stress development at the tooth/restoration interface is one of the most important reasons for failure of adhesive restorations. The aim of this study was to evaluate the influence of BisGMA/TEGDMA (B/T) and UDMA/TEGDMA (U/T) ratios on polymerization stress (PS) and on the variables related to its development: degree of conversion (DC), polymerization maximum rate (Rp max ), volumetric shrinkage (VS), elastic modulus ( E ), stress relaxation (SR) and viscosity of experimental composites.
Method
Composites were formulated containing B/T or U/T in mol% ratios of 2:8, 3:7, 4:6, 5:5, 6:4, 7:3 and 8:2, and 15 wt% of fumed silica. PS was determined with a universal testing machine. VS was measured with a linometer. E and SR were obtained in three-point bending. DC and Rp max were determined by real time NIR spectroscopy and viscosity was measured in viscometer. Data were submitted to one-way ANOVA, Tukey test ( α = 0.05%) and regression analyses.
Results
PS, VS, E and DC decreased and viscosity and Rp max increased with base monomer content in both series. PS showed strong correlation with VS, DC and viscosity. PS, VS and DC were higher and viscosity was lower for UDMA-based materials.
Significance
Reduced viscosity, kinetics parameters and molecular characteristics led UDMA-based composites to elevated conversion and relatively lower PS at lower TEGDMA contents, compared to B/T composites.
1
Introduction
The vast majority of commercially available dental resin composite materials rely on dimethacrylate compositions, for which the polymerization stress is still a matter of concern. It was widely demonstrated that the 2–5% volumetric shrinkage that accompanies the polymerization poses a challenge to the bonded interface . The determinants in polymerization stress – degree of conversion, reaction kinetics, volumetric shrinkage and elastic modulus – have already been identified, though their relative contribution to stress development remains undetermined due to complex interactions among the parameters . The role of reaction kinetics in the final polymerization stress is controversial . Some authors reported reduced stress with the use of “soft-start” photoactivation methods without prejudice to the conversion . Others have shown that, although the rate of stress development can be reduced, the final stress is not influenced , since most of the stress develops at later stages in conversion (above 50%) . Being viscoelastic materials, resin composites have potential for stress relaxation both during polymerization and in the fully cured material . The ability to withstand cyclic loading, as well as the magnitude of stress generated during the polymerization, are determined by polymer network characteristics, such as crosslink density and monomer backbone features and intermolecular interactions as well as filler reinforcement of the matrix. These characteristics are determined by the design of monomer blends in the organic matrix, as well as by the inorganic filler content.
In monomeric matrices containing BisGMA/TEGDMA or UDMA/TEGDMA, the incremental additions of the lower molecular weight, lower viscosity monomer (TEGDMA) leads to higher conversion and volumetric shrinkage . TEGDMA contributes to decrease the initial viscosity of the mixture, improving reaction media mobility, which favors conversion . With polymerization, the van der Waals forces that tie the monomers together are replaced by covalent bonds through the vinyl reactive groups (C C) and, in the case of methacrylates, that represents a 23 mL/mol coefficient of molar shrinkage . Therefore, the increase in volumetric shrinkage comes not only from the increased conversion, but also from the increased initial molar concentration of reactive groups given by TEGDMA’s lower molecular weight. The increase in conversion/shrinkage does not correlate linearly with TEGDMA concentration, however, and this is particularly true for BisGMA, since conversion is also related with kinetics . The UDMA monomer is more reactive than BisGMA, due to increased molecular flexibility and chain transfer reactions through the –NH group . This allows for higher rates of polymerization and for a higher conversion to be achieved before the onset of gelation , besides a higher degree of crosslinking .
Varying monomer ratios may significantly affect composite elastic modulus as well. However, when inorganic content is kept constant final rigidity is distributed in a relatively narrow range of values . To date, studies on modulus development during the polymerization are scarce due to instrumentation challenges, which make it difficult to predict how modulus development would influence stress. The stress relaxation behavior in the fully cured material can give insight into its potential for stress relaxation during conversion . There has been evidence of increased polymerization stress with reduced BisGMA concentration in mixtures with TEGDMA, which has been directly correlated to volumetric shrinkage and static elastic modulus obtained at the end of photoactivation .
The objective of this study was to evaluate the effects of using monomer mixtures with different reactivities and backbone characteristics on polymerization stress and stress relaxation. The parameters determining stress (conversion, reaction kinetics, volumetric shrinkage, elastic modulus and initial viscosity) were also evaluated. The hypothesis of this study was that composites with increased TEGDMA contents and/or those using UDMA as base monomer would show increased polymerization stress values due to a higher degree of conversion which, in turn, would increase their volumetric shrinkage and elastic modulus, and decrease stress relaxation.
2
Materials and methods
2.1
Composite formulations
Fourteen experimental composites were prepared containing 15 wt% of pirogenic silica treated with dimethyldichlorosilane, a non-functional organosilane (Aerosil R972, average size: 16 nm, Evonik Degussa GbmH, Frankfurt, Germany), and matrix composed of a base monomer either BisGMA (2,2bis[4-(2-hydroxy-3-methacryloxypropoxy)phenyl]-propane, Esstech, Essington, PA, USA) or UDMA (diurethane dimethacrylate, Sigma–Aldrich, Milwaukee, WI, USA) combined with TEGDMA (triethyleneglycol dimethacrylate, Esstech) in molar ratios of 2:8, 3:7, 4:6, 5:5, 6:4, 7:3 and 8:2. The photoinitiatior system was composed of camphorquinone (Sigma–Aldrich) and 2-(dimethylamino)ethyl methacrylate (Sigma–Aldrich), 2 mol% each. The materials were stored under refrigeration until 2 h before use.
2.2
Polymerization stress
The polymerization stress test ( n = 5) was performed as previously described in the literature . Poly(methyl methacrylate) (PMMA) rods (diameter, 6 mm; 13 or 28 mm in length) were used as the bonding substrate for the composite. One of the flat surfaces of the short rod was mirror-polished while the opposite surface was sandblasted with 250 μm alumina. For the long rod, one of the flat surfaces was also sandblasted. Methyl methacrylate was applied to the sandblasted surfaces as this procedure was shown to improve the wetting of the PMMA by the subsequent layer of unfilled resin (Scotchbond Multi-purpose, 3 M ESPE, Saint Paul, MN, USA). After light-curing the unfilled resin (400 mW/cm 2 × 30 s), the rods were clamped to the opposite chucks of a universal testing machine (Instron 5565, Canton, MA, USA), with the long axis perpendicular to the load cell and the treated surfaces facing each other. Composite ( h = 1 mm) was inserted between them, shaped into a 6-mm diameter cylinder and photoactivated with a quartz–tungsten–halogen light-curing unit (VIP Junior, Bisco, Schaumburg, IL, USA), resulting in a radiant exposure of 16 J/cm 2 (500 mW/cm 2 × 32 s). Specimen height was kept constant within 0.1 μm accuracy with the use of an extensometer (model 2630-101, Instron). Contraction force development was followed for 15 min and maximum nominal stress (PS) was calculated by dividing the maximum contraction force by the cross area of the rod (28.3 cm 2 ). Stress rate was calculated as the first derivative of the stress × time curve (i.e., variation in stress divided by the variation in time) .
2.3
Degree of conversion and rate of polymerization
Polymerization kinetics and conversion was monitored by near-infrared spectroscopy (2 scans per spectrum, 4 cm −1 resolution) during a 15 min interval by following the decrease in the area under the first overtone absorption band of the vinyl bond at 6165 cm −1 using a Nexus 670 (Thermo Nicolet, Waltham, MA) equipped with an extended KBr beam splitter and a MCT/A detector. Specimens were placed in silicone rubber molds (0.8 mm thick and r = 2.5 mm), sandwiched between glass slides and then photoactivated with 16 J/cm 2 . The polymerization rate was calculated as the first derivative of the conversion vs. time curve , and from that set of data, kinetic parameters like maximum rate of polymerization Rp max (in %/s), degree of conversion at Rp max and rate of polymerization at 10% conversion (Rp 10% , in %/s) were determined. This last parameter provides insight on the early stages of polymerization and allows for more meaningful rate comparisons among materials, since it takes into account values of Rp obtained at the same point in conversion.
2.4
Volumetric shrinkage
The volumetric shrinkage ( n = 3) during polymerization was followed for 15 min with a linometer (ACTA, Netherlands). Approximately 35 mg of material was placed on an aluminum disc sitting on top of the probe in the linometer. A glass slide was placed over the specimen and photoactivation (16 J/cm 2 ) was conducted. As described in previous study , the linear shrinkage (LS) was calculated based on specimen thickness ( L ) and displacement of the aluminum disc (Δ L ), according the formula:
LS = Δ L L − Δ L × 100
Linear shrinkage was converted to volumetric shrinkage by the equation:
2.5
Elastic modulus and stress relaxation
Bar-shaped specimens (10 mm × 2 mm × 1 mm, n = 10) were photoactivated at 16 J/cm 2 using a stainless steel split mould and stored for 15 min prior to testing. Bars were subjected to three-point bending at a crosshead speed of 1 mm/min in a universal testing machine (Instron 5565) with an 8-mm span between the supporting rollers. The flexural modulus was determined by extracting data from the initial linear portion of the load × displacement curve and applying to the formula :
E = C L 3 4 b h 3 d × 10 − 3
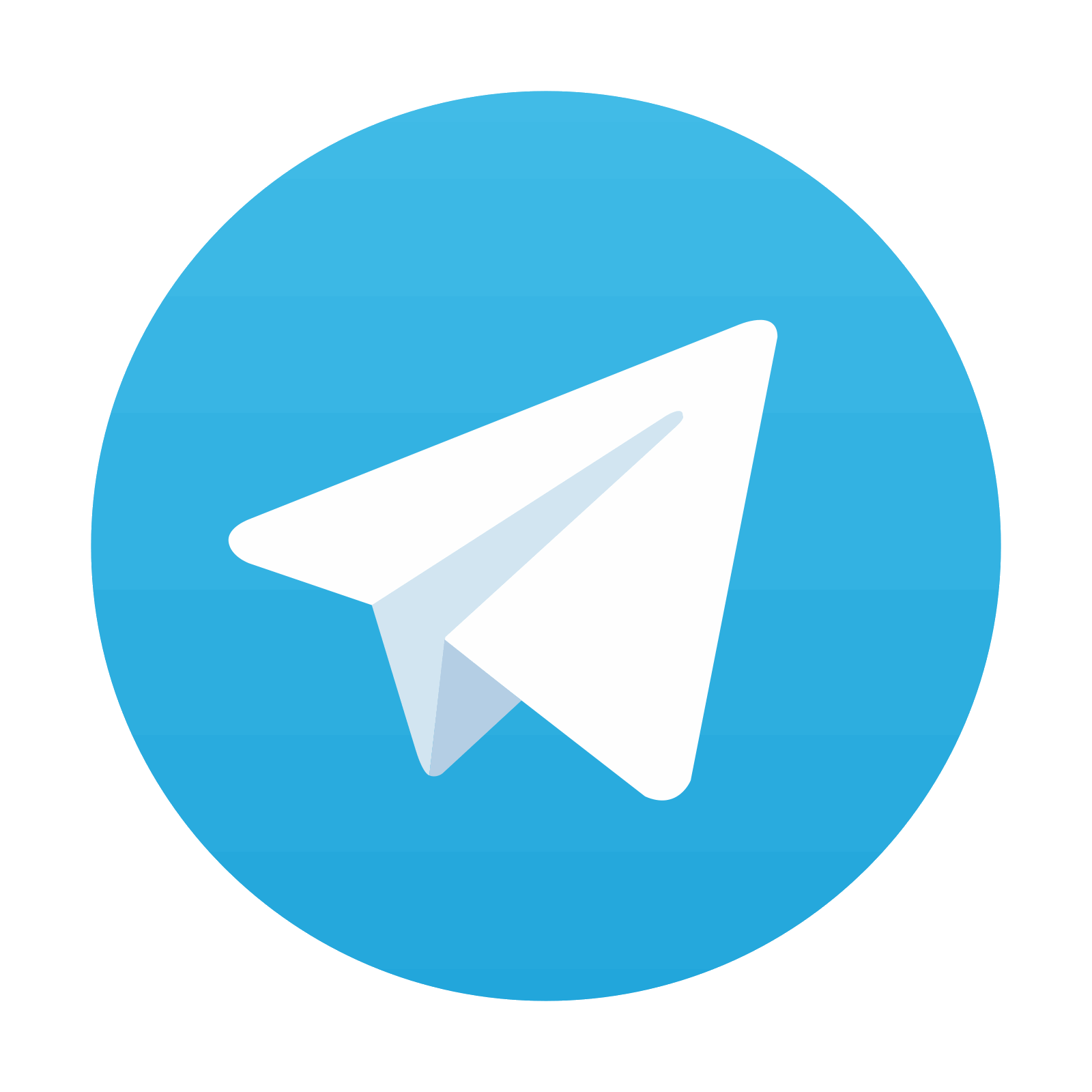
Stay updated, free dental videos. Join our Telegram channel

VIDEdental - Online dental courses
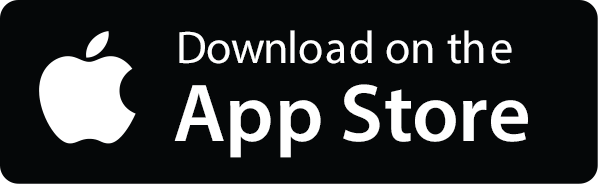
