Highlights
- •
The effect of machining on fatigue strength of CAD/CAM ceramics was evaluated.
- •
Machining reduces the flexural fatigue strength of CAD/CAM ceramics.
- •
Y-TZP showed the greatest reduction in the fatigue strength due to machining.
- •
Either soft machining or hard machining can be deleterious.
- •
Higher values of roughness may be expected after machining.
Abstract
Objectives
To assess the effect of machining on the flexural fatigue strength and on the surface roughness of different computer-aided design, computer-aided manufacturing (CAD/CAM) ceramics by comparing machined and polished after machining specimens.
Methods
Disc-shaped specimens of yttria-stabilized polycrystalline tetragonal zirconia (Y-TZP), leucite-, and lithium disilicate-based glass ceramics were prepared by CAD/CAM machining, and divided into two groups: machining (M) and machining followed by polishing (MP). The surface roughness was measured and the flexural fatigue strength was evaluated by the step-test method (n = 20). The initial load and the load increment for each ceramic material were based on a monotonic test (n = 5). A maximum of 10,000 cycles was applied in each load step, at 1.4 Hz. Weibull probability statistics was used for the analysis of the flexural fatigue strength, and Mann-Whitney test ( α = 5%) to compare roughness between the M and MP conditions.
Results
Machining resulted in lower values of characteristic flexural fatigue strength than machining followed by polishing. The greatest reduction in flexural fatigue strength from MP to M was observed for Y-TZP (40%; M = 536.48 MPa; MP = 894.50 MPa), followed by lithium disilicate (33%; M = 187.71 MPa; MP = 278.93 MPa) and leucite (29%; M = 72.61 MPa; MP = 102.55 MPa). Significantly higher values of roughness (Ra) were observed for M compared to MP (leucite: M = 1.59 μm and MP = 0.08 μm; lithium disilicate: M = 1.84 μm and MP = 0.13 μm; Y-TZP: M = 1.79 μm and MP = 0.18 μm).
Significance
Machining negatively affected the flexural fatigue strength of CAD/CAM ceramics, indicating that machining of partially or fully sintered ceramics is deleterious to fatigue strength.
1
Introduction
Recent improvements in the mechanical properties of dental ceramic systems and the implementation of computer-aided design, computer-aided manufacturing (CAD/CAM) technology in restorative dentistry have widely contributed to the increase in the use of all-ceramic restorations as an alternative for satisfying the high esthetic demand of patients .
A great variety of ceramic materials are available for CAD/CAM, with each differing in microstructure, mechanical behavior, and also machining mode . Feldspar-, leucite-, and lithium disilicate-based ceramics are commonly available in a full sintered stage for hard machining . These materials contain high volumes of glassy phases and, consequently, have a lower fracture toughness compared to that of polycrystalline ceramics . In lithium disilicate glass ceramics, the presence of lithium disilicate crystals promotes crack deflection, which improves its fracture strength . Therefore, this material is recommended not only for the manufacture of veneers, inlays, onlays, and anterior and posterior crowns, as with leucite glass ceramics , but also for implant superstructures of single-tooth restorations .
Yttria-stabilized polycrystalline tetragonal zirconia (Y-TZP) can be milled either from pre-sintered blocks (soft machining) followed by sintering at high temperature, or from fully-sintered blocks (hard machining) . Soft machining is the most used process to manufacture Y-TZP restorations, since hard machining is more time consuming and requires tougher cutting devices . Y-TZP ceramics exhibit a transformation toughening mechanism that acts to resist crack propagation. It involves the transformation of metastable tetragonal crystallites to the monoclinic phase at the crack tip, which, accompanied by a volumetric expansion, induces compressive stresses, hindering further crack propagation . It may be used as infrastructure for crowns and fixed dental prostheses (FDPs) covered by glass-ceramic or as monolithic full-contour restorations , besides being indicated for implant abutments .
Despite the promising clinical success rates, framework fracture of all-ceramic restorations is still a technical problem , which may warrant additional costs to the patient and to the dentist for the replacement of the restoration. In a recent systematic review, with the inclusion of 67 clinical studies, 5-year framework fracture rates of up to 18.4%, 5.5%, and 1.7% were reported for single crowns made of feldspathic ceramic, reinforced glass ceramic (including both leucite- and lithium disilicate-based glass ceramics), and densely sintered zirconia, respectively . When multiple-unit fixed dental prostheses were considered, these rates increased up to 15.3% for reinforced glass ceramic and up to 3.2% for densely sintered zirconia . There seem to be a remarkable difference between leucite- and lithium disilicate-reinforced ceramics in terms of mechanical behavior, which is reflected in the survival rates of the restorations. For a mean period of 4.5 years, the fracture rate of leucite-based single crowns was estimated in 3.8%, with molars showing the highest fracture rate (6.7%) ; while the fracture rate of lithium disilicate single crowns was 1.22%, over a period of 3.5 years .
Due to the brittle nature of ceramics, their fracture strength is strongly influenced by the presence of defects, which can be considered particularly critical when located at the zones of tensile stress concentration . Fractographic analysis of clinically failed all-ceramic restorations and finite element analysis showed that the cementation surface of all-ceramic crowns concentrates tensile stress, and that defects on this surface may be the origin of fracture in failed restorations . Besides, the cervical margins of all-ceramic restorations seem to have an important role in the fracture initiation, as indicated by fractographic studies . Therefore, procedures that affect the intaglio surface and the cervical margins of all-ceramic restorations must be investigated regarding their impact on the ceramic strength.
Despite reducing processing defects, once the CAD/CAM blocks are produced in a standard process, machining induces a complex network of events in the ceramic, resulting in radial and lateral cracks, chipping, subsurface damage, and residual stresses . Hard machining resulted in damage to the ceramic surface, and reduced the biaxial flexural strength of a leucite glass ceramic by approximately 27% . Soft machining also resulted in surface damage and significantly reduced the strength of zirconia, which may result in unexpected failures at stresses much lower than the ideal strength of the material . Kelly et al. reported that the defects introduced by the CEREC ® (Sirona Dental Systems Gmbh, Germany) CAD/CAM system appeared to be the origin of the failure in ceramics subjected to a uniaxial bending test.
It is important to consider that in the oral environment, all-ceramic restorations are subject to many challenges, such as cyclic loads, humidity, pH, and temperature variations. Consequently, failure tends to occur due to fatigue . Ceramics are susceptible to a slow and stable crack growth (SCG) when subjected to stresses below the critical value, especially in the presence of water. This phenomenon can eventually lead to strength degradation over time, decreasing the lifetime of dental prostheses and appears to be most related to the ceramic microstructure .
Therefore, considering the increasing use of CAD/CAM technology in restorative dentistry, in which the machining process introduces new features in the cementation surface of ceramic restorations, and the susceptibility of ceramic materials to fatigue, this study aimed to assess the effect of CAD/CAM machining on the biaxial flexural fatigue strength and on the surface roughness of a leucite-based glass ceramic, a lithium disilicate-based glass ceramic, and a yttria-stabilized polycrystalline tetragonal zirconia (Y-TZP). The experimental hypothesis was that, for all ceramics investigated, machining would result in lower values of biaxial flexural fatigue strength and in higher values of roughness when compared to polishing after machining.
2
Materials and methods
Table 1 describes the materials used in this study with manufacturers data for chemical composition and physical properties .
Ceramic | Brand name; Manufacturer | Chemical composition a | Vickers hardness a | Fracture toughness a | Machining | |
---|---|---|---|---|---|---|
(GPa) | (MPa√m) | Set of bur | Manufacturer | |||
Leucite-based glass ceramic | IPS Empress CAD; IvoclarVivadent |
SiO 2 60–65 wt% Al 2 O 3 16–20 wt% K 2 O 10–14 wt% Na 2 O 3.5–6.5 wt% other oxides 0.5–7 wt% pigments 0.2–1 wt% |
6.2 fully sintered | 1.3 | Step bur 12S (left side of the Cerec machine) Cylinder pointed bur 12S(right side of the Cerec machine) |
Sirona Dental Systems |
Lithium disilicate-based glass ceramic | IPS e.max CAD; IvoclarVivadent |
SiO 2 57–80 wt% Li 2 O 11–19 wt% K 2 O 0–13 wt% P 2 O 5 0–11 wt% ZrO 2 0–8 wt% ZnO 0–8 wt% other and coloring oxides 0–12 wt% |
5.4 partially crystallized 5.8 fully crystallized |
2.0–2.5 | Step bur 12S (left side of the Cerec machine) Cylinder pointed bur 12S (right side of the Cerec machine) |
Sirona Dental Systems |
Yttria-stabilized polycrystalline tetragonal zirconia (Y-TZP) |
Vita In-Ceram 2000 YZ for inLab; Vita Zahnfabrik |
ZrO 2 91–94 wt% Y 2 O 3 4–6 wt% HfO 2 2–4 wt% Al 2 O 3 < 0.1 wt% SiO 2 < 0.1 wt% Na 2 O < 0.1 wt% |
11.77 fully sintered | 5.9 | Step bur 20 (left side of the Cerec machine) Cylinder pointed bur 20 (right side of the Cerec machine) |
Sirona Dental Systems |
2.1
Machining of ceramic discs by CAD/CAM
Disc-shaped ceramic specimens were prepared by machining in a CEREC inLab MC XL milling unit (Sirona Dental Systems Gmbh, Germany), according to the methodology described by Fraga et al. ( Fig. 1 ), using three different ceramic materials: leucite-based glass ceramic (IPS Empress CAD, C14, Ivoclar Vivadent AG, Liechtenstein) milled in a fully-sintered stage; lithium disilicate-based glass ceramic (IPS e.max CAD, LT, C14, Ivoclar Vivadent AG, Liechtenstein) milled in a pre-crystallized stage (“blue stage”); and Y-TZP (Vita In-Ceram YZ, Vita Zahnfabrik, Germany) milled in a partially-sintered stage.

Two sets of diamond burs were used in the machining of each type of ceramic material ( Table 1 ). Fifty discs were obtained from lithium disilicate and from Y-TZP blocks, and the set of burs was changed after machining with 25th disc. Forty discs were obtained from leucite-based glass ceramic material, and the set of burs was changed after machining with the 20th disc. Ten discs of lithium disilicate and Y-TZP were used in a monotonic strength test. Less specimens of leucite-glass ceramic were produced, since the monotonic strength data were taken from Fraga et al. . The machining order and the set of burs used were recorded for each individual disc and the effect of these variables on the surface roughness and on the flexural fatigue strength of each material was evaluated afterwards.
Each block of leucite (12.0 mm × 14.0 mm × 18.0 mm) and lithium disilicate (12.4 mm × 14.5 mm × 18.0 mm) resulted in one disc, while each block of Y-TZP (15.5 mm × 19 mm × 39 mm) resulted in two discs. Immediately after machining, the leucite and lithium disilicate discs measured approximately 13.5 mm in diameter and 1.4 mm in thickness; the no-sintering Y-TZP discs measured approximately 18 mm in diameter and 1.8 mm in thickness, since the software (CEREC inLab 3D, version 4.0, Sirona Dental Systems Gmbh, Germany) automatically compensated the sintering shrinkage expected for Y-TZP (approximately 20–25%).
2.2
Experimental groups
After machining, the discs of each ceramic material were randomly divided into two groups, using the software Random Allocator ( www.random.org ): (1) machining (M) and (2) machining followed by polishing (MP). Therefore, the present study consisted of six experimental groups, assigned according to the material (leucite glass ceramic, lithium disilicate glass ceramic and Y-TZP) and the treatment performed on the bottom surface of the discs (machining – M, and machining followed by polishing – MP).
In the MP groups, polishing was performed manually under water-cooling on the bottom surface of the discs by a single trained operator, using 400, 600, and 1200 grit silicon carbide paper for leucite and lithium disilicate, and 1200 grit silicon carbide paper for Y-TZP. It was removed a thickness of 80 μm from the machined surface to eliminate the irregularities introduced by machining . A micrometer (210 MAP, Starrett, USA) was used to control the depth of removal.
The final thickness of all specimens was adjusted on the upper surface of the discs, using 240, 400, 600, and 1200 grit silicon carbide paper for leucite glass ceramic and lithium disilicate (grounded until 1.2 mm thickness), and 1200 grit silicon carbide paper for Y-TZP (grounded until 1.5 mm thickness).
After these procedures, lithium disilicate specimens were submitted to heat treatment in a Vita Vacumat 6000 MP furnace (Vita Zahnfabrik, Germany) to promote full crystallization and Y-TZP specimens were densely sintered in Vita Zyrcomat furnace, following the protocols indicated by the manufacturers. The final diameter of the discs was 13.5 mm, and the final thickness was 1.31 ± 0.01 mm for leucite glass ceramic, 1.30 ± 0.01 mm for lithium disilicate, and 1.29 ± 0.01 for Y-TZP discs.
2.3
Measurement of the surface roughness
The roughness of the bottom surface of each disc was measured prior to the mechanical tests, using a contact stylus profilometer (SJ-410, Mitutoyo, Japan).
The average surface roughness (Ra, μm) and the arithmetic mean peak-to-valley height (Rz, μm) values were determined using the average of three measurements, transversal to the machining path. The sampling length was equivalent to a value fivefold the cut-off value (λc), as defined according to ISO 4287:1997 , using the Ra values recorded at a first reading as a reference. Thereafter, the roughness of the MP leucite glass ceramic specimens was evaluated using λ c = 0.25 mm (tabulated value for 0.02 < Ra ≤ 0.1 mm), resulting in a sampling length of 1.25 mm. The roughness of the other groups was measured using λ c = 0.8 mm (tabulated value for 0.1 < Ra ≤ 2.0 mm), resulting in a sampling length of 4 mm. In addition to the use of the correct cut-off value, a Gaussian filter was employed to differentiate between shape defects and roughness profile.
2.4
Monotonic biaxial flexural strength
Prior to the fatigue test, the monotonic biaxial flexural strength was determined for lithium disilicate and Y-TZP specimens, in both conditions: machining (M) and machining followed by polishing (MP) (n = 5). For the leucite groups (M and MP), the data regarding the monotonic biaxial flexural strength were taken from Fraga et al. .
The test was performed using a piston-on-three ball assembly, according to the ISO 6872:2008 , in a universal testing machine (DL-1000 Emic, Brazil), without water. The bottom surface of the disc—referred to as the M or MP surface—was positioned on the top of the three steel spheres (2.5 mm in diameter, 120° apart, and forming a circle of 10 mm diameter), with a load applied at a rate of 1 mm/min, perpendicular to the center of the top surface of the disc, by a circular cylinder steel piston with a 1.4 mm diameter flat tip. The fracture strength, in MPa, was calculated using Eqs. (1)–(3) .
X = ( 1 + ν ) ln ( B / C ) 2 + [ ( 1 − ν ) / 2 ] ( B / C ) 2
Y = ( 1 + v ) [ 1 + ln ( A / C ) 2 ] + ( 1 − v ) ( A / C ) 2
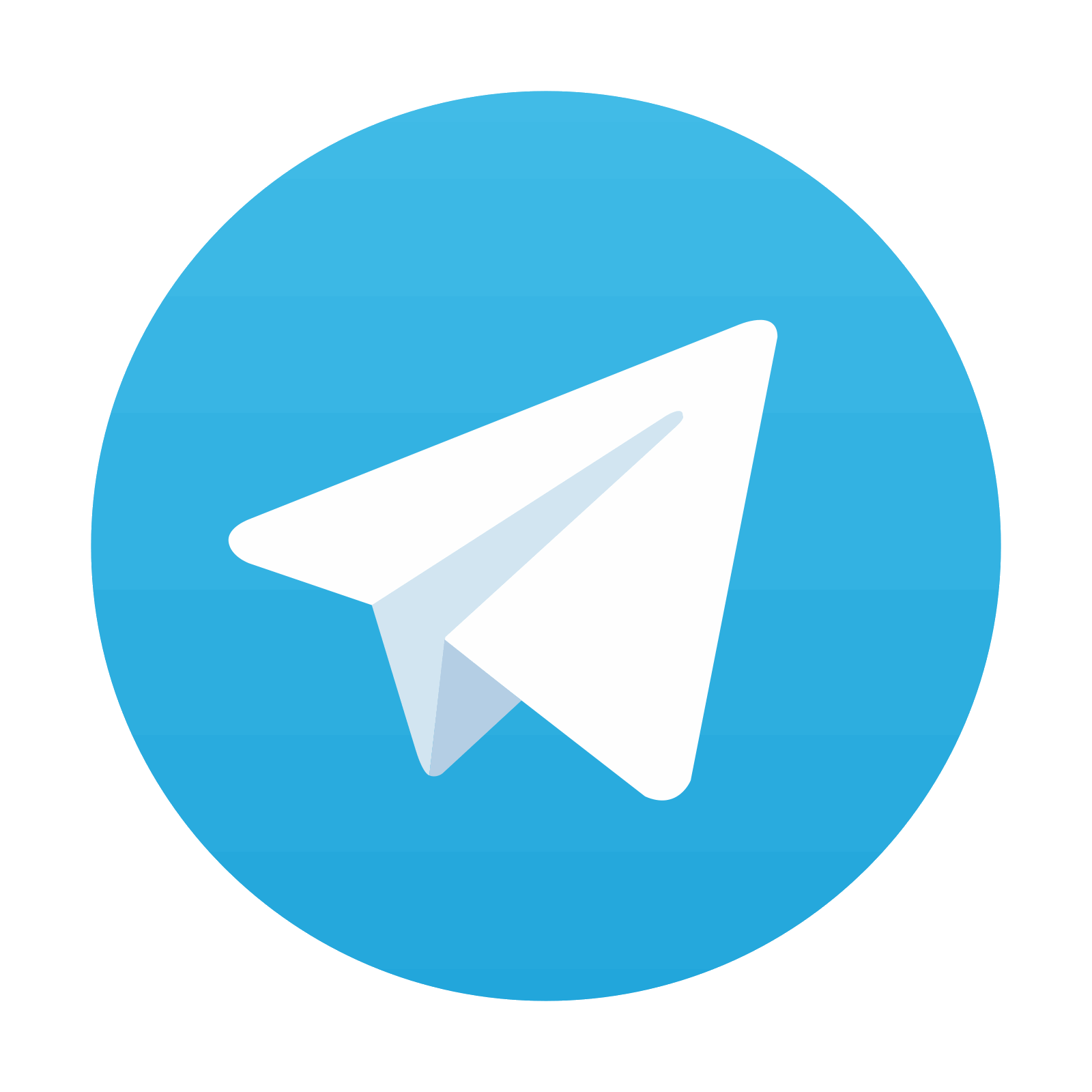
Stay updated, free dental videos. Join our Telegram channel

VIDEdental - Online dental courses
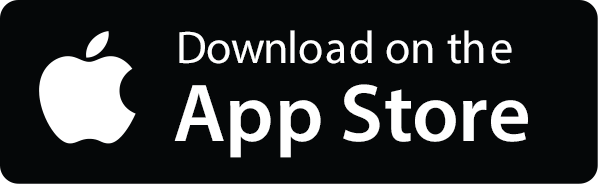
