Abstract
Objective
This study was conducted to determine selected mechanical/physical properties of and monomer release from high-temperature high-pressure (HT/HP) polymerized urethane dimethacrylate (UDMA).
Methods
Flexural strength ( σ f ), hardness, fracture toughness ( K IC ), and density ( ρ ) were determined for five UDMA resin blocks produced via different polymerization protocols. High performance liquid chromatography (HPLC) was used to determine monomer release from the five polymers. One way ANOVA, Scheffé multiple means comparisons ( α = 0.05), and Weibull statistics (for σ f ) were used to analyze the results.
Results
The results showed that HT/HP polymerization resulted in a significant ( p < 0.05) increase in σ f and ρ , along with an increase in Weibull modulus. No significant differences were found in hardness and K IC between the two HT/HP polymerized materials. A significantly lower ( p < 0.05) monomer release was detected for the HT/HP polymerized groups.
Significance
The results of this study suggest that HT/HP polymerization affects the network structure and leads to UDMA polymers with improved mechanical/physical properties and with dramatically reduced monomer release. The low elution of monomers from HT/HP and HP polymerized materials suggests the achievement of a higher degree of conversion and a lesser degree of inhomogeneity with regards to microgel domains. The results, however, cannot fully explain the dramatic increase in mechanical/physical properties reported previously for RCB, improvements that may be due to a better filler-matrix interaction afforded by HT/HP polymerization.
1
Introduction
It took 40 years for computer-aided design/computer aided manufacturing (CAD/CAM) to become a widely spread technology in dentistry . From the dental laboratory perspective, it offers several advantages, including automation of fabrication procedures, increased quality, minimized inaccuracies, and faster delivery . Ceramic and resin composite blocks for CAD/CAM-produced indirect dental restorations is a fast growing segment of the dental material market .
While ceramic blocks, due to their superior aesthetics and mechanical properties have been the most used materials for CAD/CAM, easier machinability, considerable reduction in manufacturing time and wear on cutting tools, purportedly easier repair, and lower cost lead to the development of resin composite blocks (RCB) as a viable alternative . The three main constituents of dental resin composites are the matrix, the filler, and a coupling agent that provides bonding between them. Commonly used monomers in the resin matrix are bisphenol A-glycidyl methacrylate (Bis-GMA) and urethane dimethacrylate (UDMA), combined with triethylene glycol dimethacrylate (TEGDMA) to adjust viscosity. As part of the continuous effort to improve the mechanical properties of RCB, we have recently reported on the dramatic effect of high-temperature high-pressure (HT/HP) polymerization on the properties of commercial and experimental resin composites .
The aim of this study was to assess the effect of HT/HP polymerization on the mechanical properties of and monomer release from the polymer alone, in order to better understand the results obtained for resin composites. Due to concerns related to the toxicity of bis-phenol A (BPA), we decided to base our experimental composites on UDMA . Other advantages of UDMA over Bis-GMA are its lower molecular weight (and consequently higher concentration of double bonds) as well as lower viscosity due to the presence of flexible urethane or carbamate linkages and absence of aromatic groups, which may improve toughness of the polymer/composite . The null hypotheses tested were: (1) mechanical/physical properties of and monomer release from HT/HP polymerized UDMA are not different from those of control thermo-cured or light-cured UDMA polymers; (2) mechanical/physical properties of and monomer release from HP/HT polymerized UDMA are not affected by the presence/absence of an initiator.
2
Materials and methods
The monomer used in this study was UDMA ( MW = 470.56; CAS 72869-86-4; Esstech, Germany). Table 1 summarizes the materials, the polymerization parameters, and the group designation of the five UDMA polymers made, while the experimental details are given below.
Group | Manufacturer | Polymer * | Initiator # | Polymerization parameters |
---|---|---|---|---|
LC | Laboratory | 100% UDMA | 0.5% CQ+ 1% 4, N , N -TMA + 100 ppm MEHQ | Light-cured |
TC | Laboratory | 100% UDMA | 0.5% PBO | 90 °C, 0.1 MPa for 4 h |
90I300 | Laboratory | 100% UDMA | 0.5% PBO | 90 °C, 300 MPa for 4 h |
190I300 | Laboratory | 100% UDMA | 0.5% PBO | 190 °C, 300 MPa for 1 h |
190NI300 | Laboratory | 100% UDMA | None | 190 °C, 300 MPa for 1 h |
* UDMA is urethane dimethacrylate.
# BPO is benzoyl peroxide; CQ is camphoroquinone; TMA is 4, N , N -trimethylanilin; HQME is hydroquinone monomethyl ether.
2.1
Control, light-cured UDMA (group LC)
The monomer was mixed with 100 ppm hydroquinone monomethyl ether (HQME, Fluka, France), 0.5% (weight) camphoroquinone (CQ, Aldrich, Germany), and 1% (weight) 4, N , N -trimethylanilin (TMA, Aldrich, Germany) in a planetary mixer (Thinky AR 250, Tokyo, Japan). The mix was left at room temperature for 1 day before being cast into (2 × 4 × 20) mm silicone molds. Light-curing was performed three times (ones in the middle of the sample and once on each extremity of the sample) for 40 s each, with a LED curing unit (Radii, SDI, Victoria, Australia) operated at a power density of 1200 mW/cm 2 (measured with a curing radiometer, Dentsply Caulk, Milford, USA).
2.2
Control, thermo-cured UDMA (group TC)
The monomer was mixed with initiator, 0.5% benzoyl peroxide (BPO; Sigma Aldrich, Steinheim, Germany); 100 g was placed inside a flexible silicone tube (25 mm internal diameter) and was thermally cured at 90 °C, at ambient pressure (0.1 MPa), in a furnace (Memmert, Schwabach, Germany), for 4 h.
2.3
Experimental, HP cured UDMA (group 90I300)
The composition (monomer with 0.5% BPO) and curing temperature (90 °C) for this group was the same as that of the TC control group, the difference being the high pressure during curing. The monomer-initiator mix (100 g) was placed inside a flexible silicone tube (25 mm internal diameter) and cured at 90 °C under high pressure (300 MPa), in a custom-built autoclave, for 4 h.
2.4
Experimental, HT/HP cured UDMA (group 190I300)
The composition (monomer with 0.5% BPO) for this group was the same as that of the TC control group, the difference being the high temperature and high pressure during curing. This group differed from 90I300 group by the high temperature during curing. The monomer-initiator mix (100 g) was placed inside a flexible silicone tube (25 mm internal diameter) and cured at 190 °C under high pressure (300 MPa), in a custom-built autoclave, for 1 h.
2.5
Experimental, no initiator HT/HP cured UDMA (group 190NI300)
This group differed from the experimental 190I300 group by the absence of an initiator. The monomer (100 g) was placed inside a flexible silicone tube (25 mm internal diameter) and cured at 190 °C under high pressure (300 MPa), in a custom-built autoclave, for 1 h.
2.5.1
Thermo-polymerization under high pressure
A differential scanning calorimeter (DSC 823, Mettler Toledo, Greifensee, Switzerland) was used to determine the thermo-polymerization temperature of UDMA without initiator at atmospheric pressure (0.1 MPa). Since the determined polymerization temperatures were in the (160–190) °C range, it was decided to perform all the polymerization reactions at 190 °C. Thereafter, approximately 100 g of UDMA, with or without BPO, was placed inside a flexible silicone tube (25 mm internal diameter, 1 mm thickness), which was then introduced into a custom-built autoclave with pressure and temperature control (LabVIEW version 8.6, National Instruments, USA). A thermocouple was placed in the proximity of the sample to enable accurate monitoring and, via feed-back, control of the temperature. In the first stage, the pressure within the autoclave was increased to 300 MPa at a rate of 1 MPa/s at ambient temperature. In the second stage, the temperature was increased to 90 °C or to 190 °C, at a rate of 2 °C/min. The sample was then maintained at 300 MPa and 90 °C/190 °C for 60 min before being cooled off and the pressure released at a temperature inferior to 60 °C.
2.5.2
Flexural strength
One part of each polymer block was cut with an Isomet saw (Buehler) under water irrigation, into 30 rectangular bars (2 × 4 × 20) mm. Each bar was polished under water irrigation up to a final 4000 grit silicon carbide (SiC) paper and its dimensions were measured with a digital caliper (Mitutoyo Co., Kawasaki, Japan) before being tested. Flexural strength ( σ f ) was determined by loading the samples in a three point bending device (with a 16 mm span) at a cross-head speed of 1 mm/min, using a computer controlled (NexyGen ® , Lloyd, UK) Lloyd LRX (Lloyd, UK) universal testing machine. Flexural strength (in MPa) was calculated using the formula:
where F is the load (in N) at fracture, L the specimen span (in mm), h the specimen width (in mm), and c the specimen height (in mm).
2.5.3
Fracture toughness
One part of each polymer block was cut, with an Isomet saw under water irrigation, into eight rectangular bars (8 × 8 × 15) mm, which were then wet ground on 1200 grit SiC to obtain (6 × 6 × 6 × 12) mm equilateral triangular prisms. Fracture toughness ( K IC ) was determined using the notchless triangular prism (NTP) specimen K IC test. The prisms were secured into one half of the specimen holder and a sharp scalpel was used to create a small (<0.1 mm-deep) defect along the loading edge before securing the second half of the specimen holder. The specimens were loaded in tension, using a computer controlled (Bluehill 2, Instron) universal testing machine (Instron model 4301, Instron Canada Inc.), at a crosshead speed of 0.01 mm/min until crack arrest or fracture. The maximum load (in N) recorded before crack arrest or complete failure ( P max ) was used to calculate K IC in MPa.m 1/2 using the following equation, proposed by Barker and adopted by ASTM standard E1304:
where Y * min is the minimum dimensionless stress intensity coefficient (28 for NTP samples ) D the specimen holder diameter (12 mm), and W the specimen holder length (10.4 mm).
2.5.4
Hardness
Fractured σ f specimens were used for micro-hardness determinations. The specimens were surface coated with a thin (∼10 nm) gold layer, in a sputter-coater (SC500, Bio-Rad, UK), in order to improve reading. Surface micro-hardness was measured by means of a Vickers indenter (MH3, Metkon, Bursa, Turkey), with 10 N load and 20 s dwell time. Thirty determinations on 10 specimens were made for each material.
2.5.5
Density
Fractured K IC specimens were used for density determinations. The density of samples was determined based on Archimedes’ principle using a XS205 (Mettler Toledo, Greifensee, Switzerland) balance. They were weighed in air and in deionized water and the density (in g/cm 3 ) was then calculated using the following formula:
where ρ is the density of the sample (in g/cm 3 ), A the mass (in g) of the sample in air, B the mass (in g) of the sample in deionized water, ρ w the density (in g/cm 3 ) of deionized water determined from the measurement of water temperature, and ρ a the density of air (0.0012 g/cm 3 ). Thirty determinations on five specimens were made for each material.
2.5.6
Analysis of monomer release with high-performance liquid chromatography (HPLC)
From the tested 3 point bending specimens, 18 half-bars of each polymer were randomly selected, their surface area and weight were measured and recorded, and they were placed into three vials (six half-bars per vial). Each vial was then filled with 10 mL of 75% (volume) ethanol and 25% (volume) water, prepared from HPLC-grade ethanol and HPLC-grade water (Fisher Scientific, Bishop Meadow Road, UK). The vials were sealed and stored in an oven (Memmert, Schwabach, Germany) at 37 °C. After 1 d, 7 d, 14 d, and 28 d storage, three 20 μL aliquots of each vial were removed with a micro-syringe for HPLC analysis.
The HPLC analysis was conducted using an Agilent 1260 Infinity Quaternary LC (Agilent Technologies, Waldbronn, Germany), equipped with a quaternary pump (model G1311B) and a UV diode array detector (model G4212B). The column used was Poroshell 120 EC-C18 (Agilent Poroshell, USA) with an internal diameter of 4.6 mm, length of 50 mm, and a filler-particle size of 2.7 μm. The solvent was HPLC-grade 65% acetonitrile (Fisher Scientific, Bishop Meadow Road, UK) in HPLC water, used in isocratic conditions with a flow rate of 1 μL/min . The elution was performed at room temperature and monitored in the whole UV range. For quantification, the 210 nm spectra, where UDMA exhibits significant absorption, were used. Identification of the analyte, UDMA, was made based on the retention time of the UDMA peaks registered for the standard solutions (1.327 min).
For quantitative analysis, a calibration curve was constructed using seven 10 mL solutions of UDMA [(10 −3 ; 10 −4 ; 10 −5 ; 5 × 10 −6 ; 10 −6 ; 5 × 10 −7 ; and 10 −7 ) mol/L] which were obtained from the stock solution sequential dilution. The 1 × 10 −3 mol/L UDMA stock solution was prepared by dissolving the appropriate amount of UDMA in 75% (volume) ethanol and 25% (volume) water. These solutions were stored at ambient temperature. Linearity of the calibration curve, based on the quantitative determination of UDMA in the seven solutions, was assessed by linear regression analysis. The relationship obtained for the linear peak area ( A ) − concentration ( c ) for the analyte (UDMA) was: A = 2.03494 × 10 7 × c , with a correlation coefficient R 2 = 0.99168 and σ = 16.17527 (where A = peak area and c = concentration).
The limit of detection (LOD) and the limit of quantification (LOQ) were determined using calibration in the low concentration region [(1 × 10 −7 , 5 × 10 −6 , 1 × 10 −6 , 5 × 10 −5 , 1 × 10 −5 ) mol/L] . Their values were calculated from the calibration curve according to the formula:
where σ = standard residual deviation of intercept and S = the slope.
The accuracy of the procedure was checked using the standard addition method. One real sample was spiked with appropriate volumes of a standard solution of UDMA and satisfactory results for the recovery, ranging from 102.48% to 105.72%, confirmed that the method was accurate and appropriate for quantitative analysis.
2.5.7
Statistical analysis
The results were analyzed by one way ANOVA followed, if warranted, by Scheffé multiple means analysis, all performed at 0.05 level of significance.
Weibull statistics parameters were calculated for σ f results using the Weibull statistics option in Excel ® (Microsoft,USA). The description of the Weibull distribution is given by :
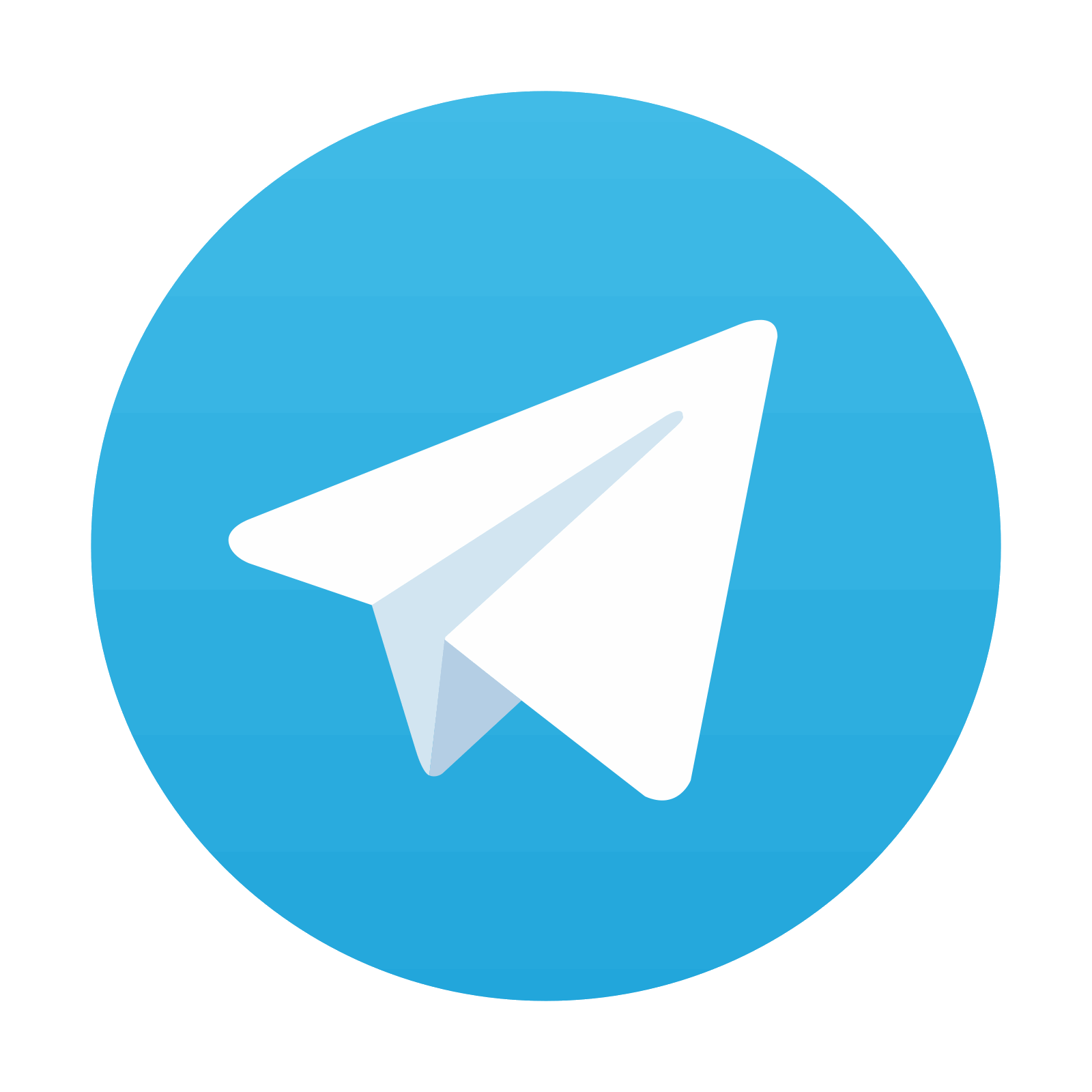
Stay updated, free dental videos. Join our Telegram channel

VIDEdental - Online dental courses
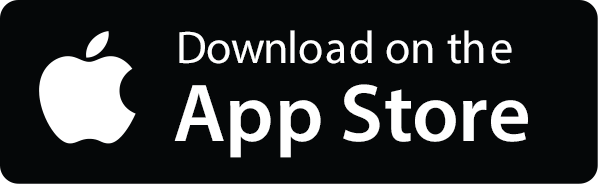
