Abstract
Objectives
The purpose of this study was to assess surface and subsurface damage on 4 CAD-CAM high-strength ceramics after grinding with diamond disks of 75 μm, 54 μm and 18 μm and to estimate strength losses based on damage crack sizes.
Methods
The materials tested were: 3Y-TZP (Lava), dense Al 2 O 3 (In-Ceram AL), alumina glass-infiltrated (In-Ceram ALUMINA) and alumina–zirconia glass-infiltrated (In-Ceram ZIRCONIA). Rectangular specimens with 2 mirror polished orthogonal sides were bonded pairwise together prior to degrading the top polished surface with diamond disks of either 75 μm, 54 μm or 18 μm. The induced chip damage was evaluated on the bonded interface using SEM for chip depth measurements. Fracture mechanics were used to estimate fracture stresses based on average and maximum chip depths considering these as critical flaws subjected to tension and to calculate possible losses in strength compared to manufacturer’s data.
Results
3Y-TZP was hardly affected by grinding chip damage viewed on the bonded interface. Average chip depths were of 12.7 ± 5.2 μm when grinding with 75 μm diamond inducing an estimated loss of 12% in strength compared to manufacturer’s reported flexural strength values of 1100 MPa. Dense alumina showed elongated chip cracks and was suffering damage of an average chip depth of 48.2 ± 16.3 μm after 75 μm grinding, representing an estimated loss in strength of 49%. Grinding with 54 μm was creating chips of 32.2 ± 9.1 μm in average, representing a loss in strength of 23%. Alumina glass-infiltrated ceramic was exposed to chipping after 75 μm (mean chip size = 62.4 ± 19.3 μm) and 54 μm grinding (mean chip size = 42.8 ± 16.6 μm), with respectively 38% and 25% estimated loss in strength. Alumina–zirconia glass-infiltrated ceramic was mainly affected by 75 μm grinding damage with a chip average size of 56.8 ± 15.1 μm, representing an estimated loss in strength of 34%. All four ceramics were not exposed to critical chipping at 18 μm diamond grinding.
Conclusions
Reshaping a ceramic framework post sintering should be avoided with final diamond grits of 75 μm as a general rule. For alumina and the glass-infiltrated alumina, using a 54 μm diamond still induces chip damage which may affect strength. Removal of such damage from a reshaped framework is mandatory by using sequentially finer diamonds prior to the application of veneering ceramics especially in critical areas such as margins, connectors and inner surfaces.
1
Introduction
High-strength ceramics like alumina (Al 2 O 3 ) and zirconia (3Y-TZP) are being used for restorative frameworks as an alternative to metal for over 15 years thanks to the CAD-CAM technology . The 3D machining of presintered ceramic blanks into the desired framework shape is followed by dense sintering. Manual grinding is however often performed in the laboratories post-sintering for shape adjustments of the sintered ceramic framework in critical areas such as margins, connectors or inner walls prior to veneering. The amount of reshaping with diamond burs post-sintering may vary from minor up to substantial depending on the computer generated 3D design of the framework, the precision milling of the CAD-CAM system and the shape and quality of the tooth preparation. Such reshaping procedure performed both by the laboratories and sometimes the dentist may have some critical mechanical consequences depending on the diamond bur grit used. As ceramics are intrinsically brittle and their mechanical properties largely influenced by their surface state, their flexural strength can be negatively affected by every treatment that increases surface roughness with the introduction of surface or subsurface flaws that may be subjected to tensile stresses. The damage process during grinding of ceramics by an abrasive particle has been described with the formation of mainly two types of cracks: parallel cracks (long or short semi-elliptical) formed parallel to the direction of grinding, or short orthogonal cracks perpendicular to the abrasive motion direction . Tangential forces may also apply during grinding which tend to increase tensile stresses normal to the direction of motion, favoring median crack propagation in the plane of motion .
The scientific literature is unanimous on the fact that grinding procedures often dramatically lower fracture resistance and fatigue behavior depending on the type of ceramic. For zirconia, the ground surface will show under XRD a localized phase transformation, which involves an increased resistance to crack propagation. Nevertheless, depending on the diamond grit size and shape and the time-dependence of the applied forces, deep reaching surface cracks will show both a reduction in strength and reliability . Grinding dense alumina will also induce surface residual compressive stresses which can enhance the average strength, but increasing the depth of cut will produce machining flaws in form of surface cracks penetrating deeper than the surface compressive layer lowering the reliability and strength . The grits of diamond burs commonly used in dental laboratories are color labeled and defined as supercoarse (black ring) (150–180 μm), coarse (green ring) (125–150 μm), standard (blue ring) (100–110 μm), fine (red ring) (45–50 μm), superfine (yellow ring) (15–30 μm). Depending on the amount of reshaping, dental laboratories will work with any of these grit sizes. The consequences of such grinding on surface and subsurface damage should therefore be well understood by the professional which reshape ceramics, i.e. dental technician and dentist. In that respect, extensive research was performed by Yin et al. reporting on edge chip damage of several dental ceramics created by grinding with diamond burs under controlled pressure, feed rate, grit size (180, 40, 10 μm) and water coolant. Her findings indicated that the average chip width decreased with the fracture toughness of the ceramic material except for a glass-infiltrated alumina. The severity of chip damage also correlated with the diamond grit size. The rougher the diamond grit the more severe the chip damage which will depend on the type of ceramic. Hence, a 180 μm coarse diamond mounted on a turbine at 260,000 rpm and 2 N load induced severe edge chip damage on a glass-infiltrated alumina but only minor to negligible chipping on zirconia . The threshold diamond grit size for negligible edge chip damage on a glass-infiltrated alumina was reported to be 40 μm . Fischer et al. estimated the strength reduction of several dental ceramics using fracture mechanics relationships by measuring under the SEM the maximal crack length developed after grinding a channel in a rod-shape ceramic specimen with a cylindrical 100 μm grit diamond bur mounted on a handpiece and compared it with the critical crack size known for the material. The highest strength reduction was reported for the glass-infiltrated alumina ceramic reaching 21%. Grinding induced surface/subsurface crack damage responsible for failure in bend test can also be visualized using none destructive optical techniques (stereo microscopy, Nomarski, SEM, TEM) in bonded interfaces . The damage extending from the ground surface into the subsurface can be measured for a variety of diamond grits and ceramics on the specimen’s mirror polished bonded interface. If one considers the worst grinding damage as a potential critical flaw (of crack length a ) located on a tensile zone (i.e. connector, internal angles, margins) and uses the materials’ reported fracture toughness ( K Ic ), one can calculate a fracture stress estimate using the classic fracture mechanics equation K Ic = Y σ f √ a (Eq. (1)) . This stress estimate can then be compared to the fracture strength reported by the manufacturer and an estimated “loss” in strength may be calculated for specific diamond grit induced grinding damage.
Thus, the objectives of this study are:
- 1.
To determine the extent of grinding damage induced with diamond grit sizes of 75 μm, 54 μm and 18 μm grain sizes on four high-strength ceramics (dense alumina, dense zirconia, alumina glass-infiltrated, alumina–zirconia glass-infiltrated) by measuring maximum and average damage depth on a bonded interface.
- 2.
To calculate using Eq. (1) a “stress estimate” using average and maximum damage depth (crack length a ) assuming these would be of a critical size, with corresponding Y factor and manufacturer’s K Ic values. By further comparing the “estimated stress” to the manufacturer’s reported strength values for each ceramic, potential “losses in strength” after grinding are calculated and discussed.
- 3.
To describe on the basis of SEM images, the crack propagation mode within the damage zone and the surface grinding removal mode (ductile, brittle, microcracking) for each ceramic.
Overall, this research on grinding damage will provide the dental technician and the dentist information about the surface/subsurface damage induced with diamonds ranging in the category of medium to fine and superfine (75, 54, 18 μm) grits and their possible loss in strength when alumina and zirconia framework adjustments are performed without further polishing and prior to veneering.
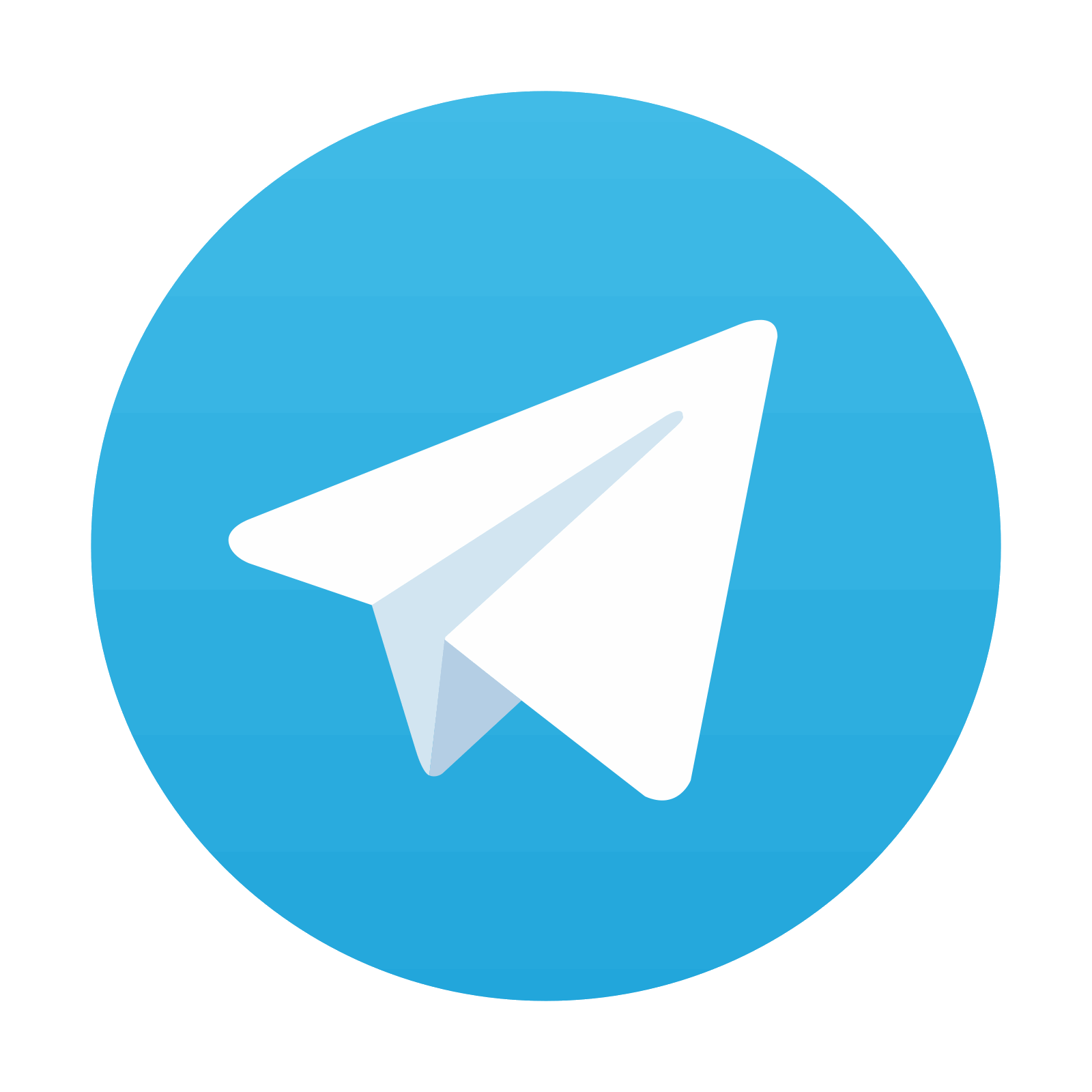
Stay updated, free dental videos. Join our Telegram channel

VIDEdental - Online dental courses
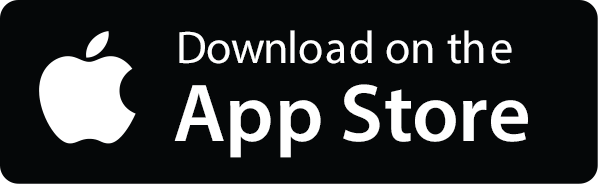
