Abstract
Objective
The aim of this paper is to validate the use of a finite-element (FE) based continuum damage mechanics (CDM) failure model to simulate the debonding and fracture of restored teeth.
Materials and methods
Fracture testing of plastic model teeth, with or without a standard Class-II MOD (mesial–occusal–distal) restoration, was carried out to investigate their fracture behavior. In parallel, 2D FE models of the teeth are constructed and analyzed using the commercial FE software ABAQUS. A CDM failure model, implemented into ABAQUS via the user element subroutine (UEL), is used to simulate the debonding and/or final fracture of the model teeth under a compressive load. The material parameters needed for the CDM model to simulate fracture are obtained through separate mechanical tests. The predicted results are then compared with the experimental data of the fracture tests to validate the failure model.
Results
The failure processes of the intact and restored model teeth are successfully reproduced by the simulation. However, the fracture parameters obtained from testing small specimens need to be adjusted to account for the size effect. The results indicate that the CDM model is a viable model for the prediction of debonding and fracture in dental restorations.
1
Introduction
The finite element method (FEM) is a numerical stress analysis technique which originated from the need for solving complex structural problems in civil and aeronautical engineering. Compared with analytical methods, FEM has fewer limitations in dealing with objects with complex geometries and non-linear inelastic material properties. Nowadays, it has become one of the most popular and powerful numerical tools in many research areas, including engineering and biomedical sciences. In the area of dentistry, for example, it has been used to simulate the bone remodeling process under mechanical load , to study the internal stresses in dentitions restored with different dental materials and restorative procedures , and to optimize the shape of dental restorations based on modern structural optimization techniques .
Increasingly, FEM is also being used as part of the design process to simulate failure of structures and components as a means to reduce the need for making prototypes and performing actual experiments that are usually expensive and time-consuming. Thus, principles of fracture mechanics or damage mechanics are implemented into FEM to analyze the failure processes of components. For example, various methods have been developed to simulate the creation and propagation of cracks using FEM . For brittle or quasi-brittle materials, cohesive models have been developed to simulate crack propagation by considering the cohesive forces at the crack tip . The first effort of combining a cohesive model with FEM was the work of Hillerborg et al. , which successfully predicted the difference between the bending strength and tensile strength of concrete, as well as the volume effect on the bending strength. Since then, numerous models and associated degradation mechanisms have been proposed for determining crack extension in brittle materials .
Studies have shown that biological materials such as bone and dentin also undergo a cohesive mode of failure . Because of the large inherent variations in their material properties and anatomy, mechanical testing involving biomaterials usually requires a large number of samples. A representative model which can simulate their failure process explicitly will therefore be very useful in the design of restorations for such materials. However, the application of cohesive models to the failure prediction of dental restorations has been very limited. The only effort reported so far seems to be the work of Ichim at al. , who used a rotating crack tip fracture model to study the failure of restored teeth with non-carious cervical lesion and other dental restorations . This failure model was initially developed for modeling discrete fracture in geomaterials under tensile and compressive stress fields . It assumes that the major principal stress controls the degradation mechanism, i.e., the direction of propagation of failure is made to remain orthogonal to the direction of the current major principal stress. Remeshing is therefore required at every step of the failure process. As would be expected, the rotating crack tip model is expensive computationally. Moreover, it is not suitable to simulate the debonding at interfaces between dissimilar materials, such as those between dental restorations and tooth tissues, since it is unable to define the interfacial fracture properties, such as strength and fracture toughness.
In this paper, a failure model based on continuum damage mechanics (CDM) is introduced for the failure prediction of restored teeth. The model was originally developed by Zou et al. for analyzing interfacial delamination in composite laminates. It has since been employed to predict the failure of monolithic brittle materials as well . It is therefore capable of simulating fracture in bulk dental materials as well as interfacial debonding between tooth tissues and restorations. With this failure model, an interface without thickness is introduced into the solid where potential crack surfaces may form. A damage parameter is employed and the interfacial constitutive law is expressed as a function of the damage parameter to account for the degradation of material along the crack path. Both conventional stress-based and fracture-mechanics-based failure criteria are included in this failure model, so it can predict both the initiation and propagation of cracks. The model has been implemented into the commercial FE software ABAQUS through a user-defined element (UEL) subroutine.
2
Materials and methods
2.1
The CDM failure model
The CDM model can be seen as an extension or generalization of the cohesive zone model . Using the ‘fictitious crack’ concept, an interface is introduced into the continuum solid where potential crack surfaces may form. The interface has no thickness and there is no gap within it before damage is incurred. Fig. 1 (a) schematically shows the transition of an interface, via a damage process zone, to fully formed crack surfaces. To derive the constitutive law for the interface, a dimensionless damage parameter ω is employed, namely:
where τ i are the tractions on the interface, δ i the relative displacements across the interface, and k0ik0i
k i 0
the constraint stiffness values of the interface. Subscript 1 indicates the direction normal to the interface and 2 the direction along the interface. ω = 0 indicates no damage, and ω = 1 indicates the fully cracked state. Incrementally,
d τ i = k i 0 ( 1 − ω ) d δ i − k i 0 δ i d ω , i = 1,2
A damage surface, which is based on both a stress-based ( τ i ) and a fracture-mechanics-based ( G i ) failure criterion, is constructed for establishing the damage evolution law as below:
F ( τ i , G i ) = τ 1 2 τ 1 C 2 + τ 2 2 τ 2 C 2 + G I G IC + G II G IIC n − 1 = 0
where G i are the strain energy release rates of the material, defined as Gi=∫δi0τidδiGi=∫δi0τidδi
G i = ∫ 0 δ i τ i d δ i
; G iC are the critical values of G i ; and n is a parameter which controls the rate of strain softening in the material.

When the combination of the interfacial stresses exceeds the damage surface, i.e., F ( τ i , G i ) > 0, damage will develop at the interface. Thereafter, infinitesimal changes of the traction forces will result in an infinitesimal change of the damage state as follows:
d F = ∑ i = 1 2 ∂ F ∂ τ i d τ i + ∂ F ∂ G i d G i = 0
Substituting for d τ i and d G i in terms of d δ i , this gives:
d ω = ∑ i = 1 2 [ ( ( ∂ F / ∂ τ i ) ( 1 − ω ) k i 0 ) + ( ( ∂ F / ∂ G i ) τ i ) ] d δ i ∑ j = 1 2 ( ∂ F / ∂ τ j ) k j 0 δ j
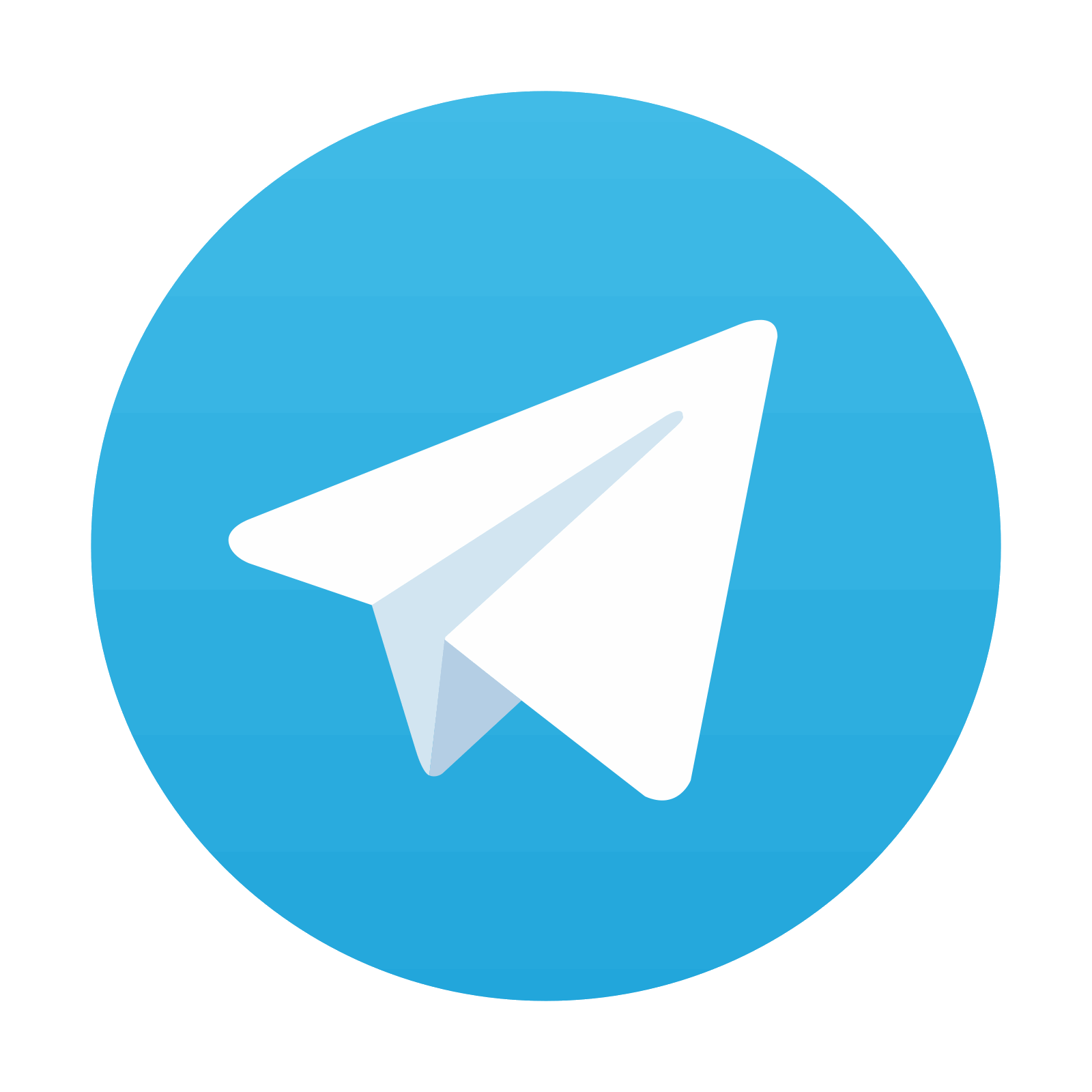
Stay updated, free dental videos. Join our Telegram channel

VIDEdental - Online dental courses
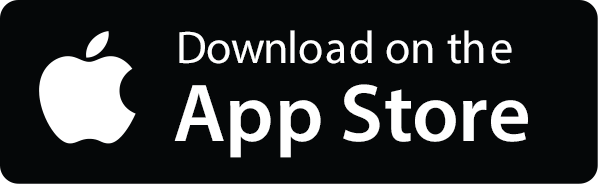
