Abstract
Objective
To evaluate the effect of the specimen design on the flexural strength ( σ f ) and failure mode of ceramic structures, testing the hypothesis that the ceramic material under tension controls the mechanical performance of the structure.
Methods
Three ceramics used as framework materials for fixed partial dentures (YZ – Vita In-Ceram YZ; IZ – Vita In-Ceram Zirconia; AL – Vita In-Ceram AL) and two veneering porcelains (VM7 and VM9) were studied. Bar-shaped specimens were produced in three different designs ( n = 10): monolithic, two layers (porcelain-framework) and three layers (TRI) (porcelain-framework-porcelain). Specimens were tested for three-point flexural strength at 1 MPa/s in 37 °C artificial saliva. For bi-layered design, the specimens were tested in both conditions: with porcelain (PT) or framework ceramic (FT) layer under tension. Fracture surfaces were analyzed using stereomicroscope and scanning electron microscopy (SEM). Young’s modulus ( E ) and Poisson’s ratio ( ν ) were determined using ultrasonic pulse-echo method. Results were statistically analyzed by Kruskal–Wallis and Student–Newman–Keuls tests.
Results
Except for VM7 and VM9, significant differences were observed for E values among the materials. YZ showed the highest ν value followed by IZ and AL. YZ presented the highest σ f . There was no statistical difference in the σ f value between IZ and IZ-FT and between AL and AL-FT. σ f values for YZ-PT, IZ-PT, IZ-TRI, AL-PT, AL-TRI were similar to the results obtained for VM7 and VM9. Two types of fracture mode were identified: total and partial failure.
Significance
The mechanical performance of the specimens was determined by the material under tension during testing, confirming the study hypothesis.
1
Introduction
The use of all-ceramic restorations has increased since the introduction of CAD–CAM technology in dentistry. Ceramic systems with high crystalline content have good fracture resistance but are highly opaque. Therefore, to obtain a natural-looking restoration the framework material should be veneered with porcelain, which presents better esthetics . Usually the mechanical behavior of veneer and framework materials is evaluated separately, providing important information on the fracture resistance of each component of the restoration. However, it is also important to understand how these materials interact in a multi-layer configuration. The study of layered structures can provide valuable information about the stress distribution, failure mode and origin, interfacial bonding and thermal stresses .
Interfaces can have significant influence on the mechanical performance of layered structures. For instance, the slow crack growth behavior can be affected by the interface fracture energy and the difference between the elastic modulus of the coupling materials . In addition, a mismatch in the coefficient of thermal expansion (CTE) between the ceramics produces residual stresses near the interface that could influence the fracture mode of these laminates . Other factors that are also related to the performance of these structures are the mechanical properties of the material subjected to maximum tensile stress during loading and the thickness ratio between layers . Hsueh et al. used finite element analysis (FEA) and reported that the location of the maximum tensile stress changes with the thickness ratio between the veneering and framework materials.
Investigations showed that the material subjected to tension during flexural testing and the interaction between the materials in ceramic structures have a significant effect in the strength and fracture mode of layered structures . When the framework material is under tension, in layered structures, the fracture strength values tend to be similar to the ones obtained by the monolithic specimens made of framework material . On the other side, the framework material has a small influence in the fracture strength of these structures when the porcelain is subjected to tension .
Multi-layered structures are also subjected to residual stresses from mismatches in the CTE between the materials and thermal gradients produced during cooling. The restoration veneering process involves high temperature sintering (750–900 °C) and subsequently cooling to room temperature. Usually, in both metal-ceramic and all-ceramic restorations, the porcelain CTE is slightly lower than the framework CTE, producing compressive stresses in the porcelain surface and compensatory tensile stresses in the framework surface . However, for all-ceramic restorations, the framework material is brittle and the risk of destructive stresses in the veneering layer is higher than in metal-ceramic restorations . Another limitation of all-ceramic restoration is the fact that structures produced with porcelain combined to a material with low thermal diffusivity, such as yttria partially stabilized zirconia ceramic (YZ), are more susceptible to the development of tensile stresses . These residual stresses are induced by the large temperature difference between layers during cooling and may result in cracks and porcelain chipping .
Although bi-layered structures have been studied in terms of fracture strength, failure mode and stress distribution, there are no studies evaluating tri-layered structures (porcelain/framework/porcelain), which is the real configuration of a FPD connector. Therefore, the objective of this study was to systematically evaluate the effect of the specimen design on the flexural strength and failure mode of ceramic materials, testing the hypothesis that the material under tension during testing influences the flexural strength values and failure behavior of these structures. In addition, the mechanical behavior of different materials used to produce all-ceramic FPDs was characterized.
2
Materials and methods
Three ceramics used as framework materials for FPDs and two veneering porcelains were studied. The materials used in this study are described in Table 1 . Three specimen designs were produced with the dimensions of 2 mm × 4 mm × 16 mm:
- (1)
monolithic (one material);
- (2)
two layers, 1 mm thickness of framework ceramic and 1 mm thickness of porcelain;
- (3)
three layers, 1 mm thickness of framework ceramic completely veneered with 0.5 mm thickness of porcelain.
Legend | Material a | Composition | Indication |
---|---|---|---|
YZ | Vita In-Ceram YZ | Yttria partially stabilized tetragonal zirconia polycrystal | Framework |
IZ | Vita In-Ceram Zirconia | Alumina-based zirconia-reinforced glass infiltrated ceramic | Framework |
AL | Vita In-Ceram AL | Alumina polycrystal | Framework |
VM7 | Vita VM7 | Feldsphatic porcelain | Veneer |
VM9 | Vita VM9 | Feldsphatic porcelain | Veneer |
a The materials were manufactured by Vita Zahnfabrik, Bad Sackingen, Germany.
YZ, IZ and AL bar-shaped specimens were obtained by cutting pre-sintered blocks using a diamond disc in a precision cutting machine (Isomet 1000, Buehler, Lake Bluff, USA) at 275 rpm. YZ and AL specimens were sintered in the Zyrcomat furnace (Vita Zahnfabrik, Germany). IZ material was infiltrated with glass (Zirconia Glass Powder, Vita Zahnfabrik, Germany). The infiltration cycle was performed in the Inceramat 3 furnace (Vita Zahnfabrik, Germany), and the excess glass was removed with burs. The glass infiltration cycle was performed at 1110 °C for 6 h, according to the manufacturer’s instruction. VM7 and VM9 specimens were fabricated by mixing ceramic powder with distilled water to form a slurry that was poured into a metallic mold and condensed with manual vibration. A Keramat I furnace (Knebel, Porto Alegre, Brazil) was used to perform the porcelain sintering. The porcelain specimens were sintered according to the following cycle: pre-drying at 500 °C for 6 min, heating to 910 °C at a rate of 55 °C/min under vacuum, heating at 960 °C for 1 min and cooled down to room temperature (6 min).
After YZ, AL, VM7 and VM9 sintering and IZ glass infiltration, monolithic specimens were ground to their final dimensions (2 mm × 4 mm × 16 mm), and the 4-mm wide face was polished to a 1 μm finish using a polishing machine (Ecomet 2, Buehler, Lake Bluff, USA). All edges were chamfered at a 0.1 mm wide chamfer, as proposed by ISO 6872:2008 .
For multi-layer structures (two- and three-layer specimens), the framework material was veneered with the porcelain recommended by the manufacturer: VM7 was used for IZ and AL, and VM9 was used for YZ. Framework bars were produced following the methodology described for monolithic specimens. For two-layer structures, the framework material (1 mm × 4 mm × 16 mm) was veneered with a 1 mm thickness of porcelain using a metallic mold. After sintering, half of the specimens ( n = 10) had the framework surface polished, and the other half had the porcelain surface polished. For tri-layered structures, framework ceramic bars with the dimensions of 1 mm × 3 mm × 15 mm were produced and all surfaces were veneered with a 0.5 mm thickness of porcelain. One of the 4-mm wide faces was also polished to a 1 μm finish. After polishing, all edges were chamfered. For YZ material, before veneering, a bonding agent (Effect Bonder, Vita Zahnfabrik, Germany) was applied to the specimen surfaces and sintered according to the manufacturer’s instructions.
Specimens were classified according to the number of layers (one, two or three layers) and to the flexural test configuration (porcelain or framework in tension) ( Table 2 ). Therefore, this study tested 14 experimental groups ( n = 10) for flexural strength.
Material | One layer | Two layers | Three layers | |
---|---|---|---|---|
Porcelain in tension | Framework in tension | |||
YZ | YZ | YZ-PT | YZ-FT | YZ-TRI |
IZ | IZ | IZ-PT | IZ-FT | IZ-TRI |
AL | AL | AL-PT | AL-FT | AL-TRI |
VM7 | VM7 | |||
VM9 | VM9 |
The mechanical testing was performed according to the ISO 6872:2008 with a three-point flexure fixture with 2-mm diameter rollers and 12.0 mm span. The fixture was immersed in 37 °C artificial saliva with the following composition: 100 mL of KH 2 PO 4 (2.5 mM); 100 mL of Na 2 HPO 4 (2.4 mM); 100 mL of KHCO 3 (1.50 mM); 100 mL of NaCl (1.0 mM); 100 mL of MgCl 2 (0.15 mM); 100 mL of CaCl 2 (1.5 mM); and 6 mL of citric acid (0.002 mM) . The flexural strength ( σ f ) was determined using a universal testing machine (Sintech 5G, MTS, São Paulo, Brazil) at a constant stress rate of 1 MPa/s.
The maximum tensile stress can be calculated using the following the equation :
where M is the moment of the load, Y is the distance from the neutral axis to the outermost fiber, and I is the moment of inertia of the cross-section about the central axis.
For the three-point flexural strength test of monolithic specimens: M = ( PL )/4, Y = t /2, and I = (1/12) wt 3 . By substituting into Eq. (1) , the following equation is developed :
where P is the fracture load (N), L is the span (12 mm), w is the specimen width (mm), and t is the specimen thickness (mm).
For bi-layered specimens the σ f was determined by the equation :
where K is calculated according to:
K = 4 + 6 t c t t + 4 t c t t 2 + E c E t t c t t 3 + E t t t E c t c
Replacing M and K (Eq. (4) ) in Eq. (3) , Eq. (5) is used to calculate the flexural strength ( σ f ):
σ f = 3 E t L P ( E c t c 2 + 2 E c t c t t + E t t t 2 ) 2 w ( E c 2 t c 4 + 4 E c E t t c 3 t t + 6 E c E t t c 2 t t 2 + 4 E c E t t c t t 3 + E 2 t t t 4 )
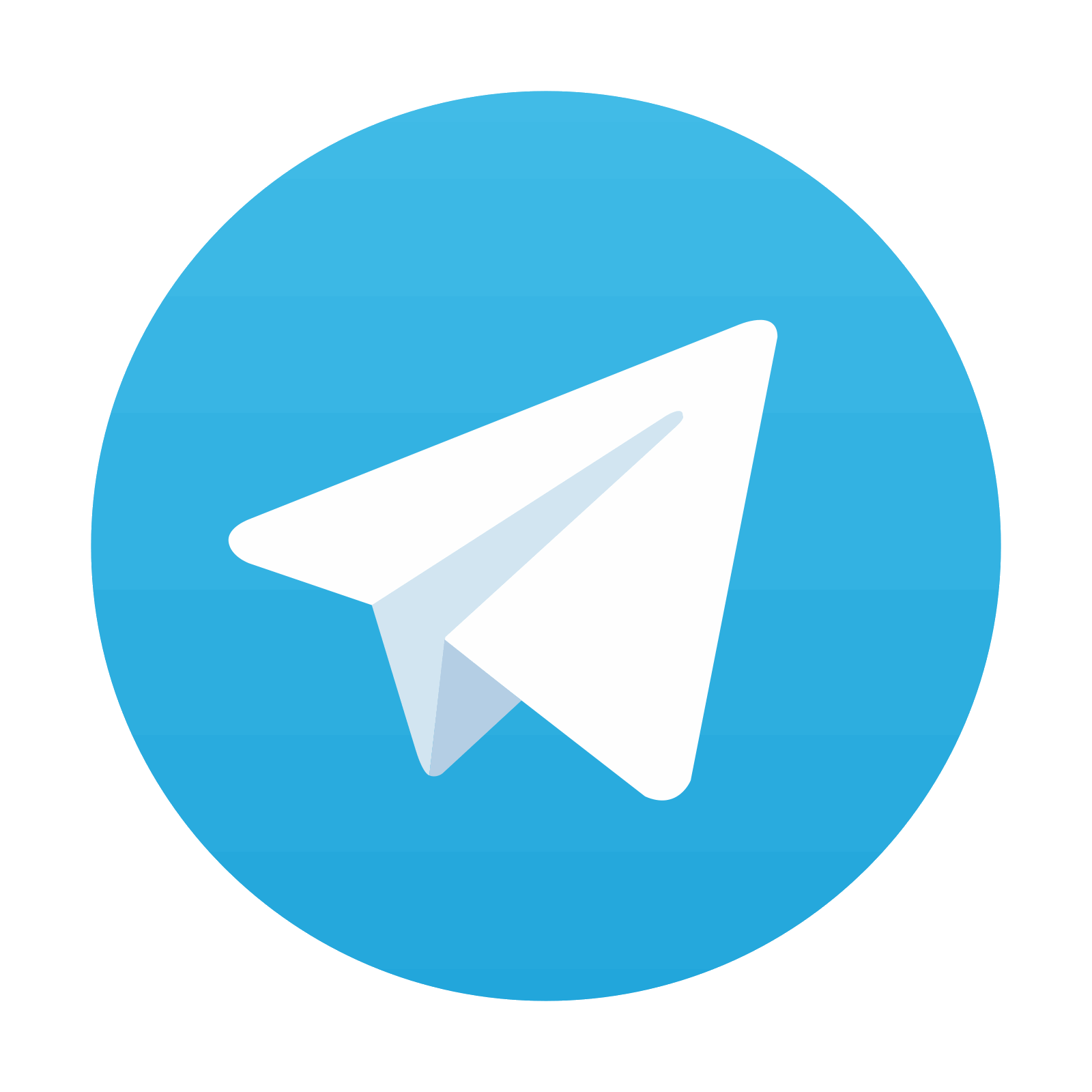
Stay updated, free dental videos. Join our Telegram channel

VIDEdental - Online dental courses
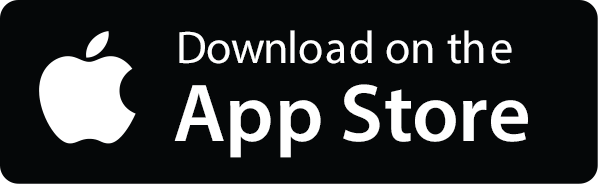
