Highlights
- •
Filler characteristics greatly vary among the 17 resin composites analyzed.
- •
Mechanical properties varied by up to a factor 3 among materials.
- •
Materials differed in their sensibility to incubation medium (water or EtOH/water).
- •
The filler content (W fillers ) was confirmed as major discriminatory characteristic.
- •
A simple classification and terminology can be suggested based solely on W fillers .
Abstract
Objective
The mechanical properties of dental resin-based composites (RBCs) are highly dependent on filler characteristics (size, content, geometry, composition). Most current commercial materials are marketed as “nanohybrids” (i.e. filler size <1 μm). In the present study, filler characteristics of a selection of RBCs were described, aiming at identifying correlations with physico-mechanical properties and testing the relevance of the current classification.
Methods
Micron/sub-micron particles (> or <500 nm) were isolated from 17 commercial RBCs and analyzed by laser diffractrometry and/or electron microscopy. Filler and silane content were evaluated by thermogravimetric analysis and a sedimentation technique. The flexural modulus (E flex ) and strength (σ flex ) and micro-hardness were determined by three-point bending or with a Vickers indenter, respectively. Sorption was also determined. All experiments were carried out after one week of incubation in water or 75/25 ethanol/water.
Results
Average size for micron-sized fillers was almost always higher than 1 μm. Ranges for mechanical properties were: 3.7 < E flex water < 16.3 GPa, 86 < σ flex water < 161 MPa and 23.7 < hardness water < 108.3HV0.2/30. Values generally decreased after storage in ethanol/water (Δmax = 86%). High inorganic filler contents (>75 wt%) were associated with the highest mechanical properties (E flex and σ flex > 12 GPa and 130 MPa, respectively) and lowest solvent sorption (∼0.3%).
Significance
Mechanical properties and filler characteristics significantly vary among modern RBCs and the current classification does not accurately illustrate either. Further, the chemical stability of RBCs differed, highlighting differences in resin and silane composition. Since E flex and sorption were well correlated to the filler content, a simple and unambiguous classification based on such characteristic is suggested, with three levels (ultra-low fill, low-fill and compact resin composites).
1
Introduction
The popularity of dental resin composites is driven by their versatility, aesthetic quality and reasonable clinical performance. The development of resin composite materials are relentlessly researched and tested by academia and industry in an attempt to enhance clinical longevity by reducing their perceived shortcomings such as polymerization stress , residual monomer content , inadequate depth of cure , handling and aesthetic characteristics . Most often, these issues are not entirely addressed and new concepts aggressively marketed as “low-shrink” or “bulk-fill” and such. The resin composite market is highly competitive between manufacturers, and the incredibly rapid and iterative product cycle leaves the general practitioner with a vast choice from an array of similar materials types. As a consequence, and particularly for resin composites, the usefulness of classification systems as a means for practitioners to compare material properties is limited.
An area of substantial development since the inception of resin composite materials relates to filler type, processing and morphology, and probably much more so than advancements in resin chemistry. Continuous material developments among researchers and manufacturers have led to the use of refined filler technologies and design choices. Following the evolution of processing techniques, the size of filler particles, typically ground glasses, have decreased from tens of micron to about 1 μm . With advancements such as jet-milling, sub-micron dimensions can be achieved with narrow distributions and microparticles averaging 0.5–1.0 μm are now used in some commercial composites. Pre-polymerized fillers (PPF) are also common and processed using ground cured composite, containing a variety of sub-micron particles. Such particles were introduced in part as a solution to reduce the stress resulting from polymerization and provide improved polishability compared with earlier hybrid types . Nanoparticles, originally introduced in an effort to improve aesthetic quality are used today in some modern materials in the form of nano-sized aggregates, aimed at improving mechanical properties, in particular strength . Discrete nano-sized fillers, smaller than the wavelength of visible light, represent an additional asset in light-curing materials, since refraction and scattering are reduced, which may offer significantly improved depth of cure .
The classification of dental composite has evolved over the years, but in general has mostly focused on filler-size distribution, filler content or composition. From “microfills ” or “nanofills ” , containing only micro or nanoparticles, respectively, most modern resin composites belong to a so-called “hydrid” category, and presently are commonly marketed as “nanohybrids ” . This terminology refers to materials containing a fraction of nanoparticles (<100 nm) and of sub-micron particles (≤1 μm, typically averaging 0.5–1.0 μm) ( Fig. 1 ). Compared to “microhybrids”, nanohybrids can be expected to contain a greater fraction of nanoparticles. However, a classification based on filler-size distribution does not reflect filler composition, morphology or filler specificities (e.g. the use of PPF). It is therefore doubtful for example that all nanohybrids would display the same properties and many commercial resin-based composites (RBCs) claiming to be “nanohybrids” will have a significant proportion of larger size (>1 μm) fillers .

There is in fact a vast bank of data documenting various mechanical and physical property comparisons. These properties vary greatly from one material, or test-center, to another. For example, the flexural modulus measured in-vitro ranging from 3 to 15 GPa or flexural strength, hardness or fracture toughness also varying, between 50–150 MPa , 19–80 HV0.5/20 and 1–2.5 MPa <SPAN role=presentation tabIndex=0 id=MathJax-Element-1-Frame class=MathJax style="POSITION: relative" data-mathml='m’>m−−√m
m
respectively. These properties are interrelated and dependent on filler characteristics (geometry, composition, surface coating, size distribution) and filler content (filler mass and volume content). Excellent studies have covered the topic and general rules are that both the modulus and surface hardness increase with increasing filler content with a concomitant decrease in volumetric shrinkage . At a given filler content, size and geometry, strength is influenced by the chemistry of the resin phase . A biomimetic approach would advocate similar properties of resin composites such as rigidity and strength compared with the tissue they replace, i.e. mostly dentin, for which the modulus and strength were placed in the range of 20–25 GPa (Young’s modulus) and 52–105 MPa (ultimate tensile strength) . Most difficult to achieve and embodying the major challenge of composites, such high moduli RBCs would also need to display similar toughness than dentin (1.5–2.7 MPa <SPAN role=presentation tabIndex=0 id=MathJax-Element-2-Frame class=MathJax style="POSITION: relative" data-mathml='m’>m−−√m
m
) at the risk of otherwise being too brittle. Also of some importance, the mechanical properties of composites should not degrade with time and should be chemically stable. In-vitro studies have repeatedly demonstrated that depending on materials characteristics, the response of RBCs to mechanical and chemical challenges vary. Recent work has highlighted the degradation of strength of commercial materials following fatigue tests to well below the 80 MPa limit set by ISO 4049 . In addition, great variations in the strength measured were observed between materials. Regarding chemical stability, solvent sorption has been extensively investigated as a tool to determine a material’s hydrophobicity. It has been suggested that solvent sorption is directly correlated to the extent of hydrolytic effects, altering mechanical properties . Characterizing a composite’s solvent uptake could therefore provide a tool to infer mechanical performance.
Some studies have investigated the mechanical properties of a panel of commercial resin composites in relation to filler content and morphology , however none have recently characterized filler distribution or related mechanical properties correlations. Consequently, the aim of the present study was to characterise the physical and mechanical properties of a wide selection of modern, “nanohybrid” dental composites in relation to filler content, filler morphology and distribution. A subsequent aim was to propose a new classification based on the correlations between these various characteristics.
2
Materials and methods
This work intended to include a list of “nanohybrids” composite materials as diverse in composition as possible. 17 different resin composites were selected for the present study ( Table 1a ).
Material/shade | Type/format | Batch n° | Organic matrix | Manufacturer |
---|---|---|---|---|
Admira Fusion/A3 | Nanohydrid ormocer/composite | V53177 | Ormocer | Voco GmbH |
Clearfil Majesty ES Flow/A3 | Nanohybrid/flowable | 1K0078 | Kuraray Dental | |
Clearfil Majesty Posterior/A3 | Nanohybrid/composite | BC0013 | Kuraray Dental | |
ELS Flow/A3op | Microhydrid/flowable | B810 | TegDMA & HEMA-free, low-shrink | Saremco Dental |
ELS/A3 | Microhydrid/composite | B797 | TegDMA & HEMA-free, low-shrink | Saremco Dental |
Exp. flow LC/A3 | Experimental flowable | V55226 | Voco GmbH | |
Exp. LC/A3 | Experimental composite | V53177 | Voco GmbH | |
Filtek Silorane/A3 | Microhybrid/composite | N462672 | Low-shrink | 3M ESPE |
Filtek Supreme XTE/A3 | Nanohybrid/composite | N609054 | 3M ESPE | |
Gaenial Anterior/A3 | Nanohybrid/composite | 1311281 | BisGMA-free, PPF | GC |
Grandio Slow/A3 | Nanohybrid/flowable | 1344366 | Voco GmbH | |
Grandio/A3 | Nanohybrid/composite | 1408240 | Voco GmbH | |
Kalore/A3 | Nanohydrid/composite | 1309051 | Low-shrink, PPF | GC |
Tetric Evo Ceram/A3 | Nanohybrid/composite | P11989 | PPF | Ivoclar Vivadent |
Venus Diamond Flow/A3 | Nanohybrid/flowable | 010102 | Heraeus Kulzer | |
Venus Diamond/A3 | Nanohybrid/composite | 010052 | Heraeus Kulzer | |
Venus Pearl/A3 | Microhybrid/composite | 010029 | PPF | Heraeus Kulzer |
Material | Filler content wt%/vol% | Filler specifications |
---|---|---|
Admira Fusion | 84/ NS | |
Clearfil Majesty Posterior | 92/82 | Glass ceramics/alumina micro particles (0.02–7.9 μm) |
Clearfil Majesty ES Flow | 75/59 | Barium glass/silica particles (0.18–3.5 μm) |
ELS | 74/49 | Barium glass/silica particles (0.004–3 μm) |
ELS Flow | 53/28 | Barium glass particles (0.05–3 μm) |
Exp. Flow LC | NS | |
Exp. LC | NS | |
Filtek Silorane | 76/55 | Quartz and Yttrium fluoride particles |
Filtek Supreme XTE | 78.5/63.3 | 0.6–10 μm zirconia/silica clusters, 20 nm silica (20 nm) and zirconia (4–11 nm) dispersed particles |
Gaenial Anterior | Two types of pre-polymerized particles ([400 nm Strontium glass and 100 nm lanthanoid fluoride] or [16 nm silica]) (16–17 μm), silica (850 nm) and fumed silica (16 nm) | |
Grandio | 87.0/71.4 | |
Grandio Flow | 80.2/65.7 | |
Kalore | 82/ NS | 17 μm pre-polymerized particles (400 nm strontium glass and 100 nm lanthanoid fluoride), strontium and fluoroaluminosilicate glasses (700 nm), silica (16 nm) |
Tetric Evo Ceram | 82.5/NS | 34 wt% pre-polymerized particles and 48.5 wt% Ytterbium fluoride, barium glass and mixed oxide particles (0.4–0.7 μm) |
Venus Diamond | 81/64 | Barium aluminium fluoride glass/highly discrete nanoparticles (5 nm–20 μm) |
Venus Diamond Flow | 65/41 | Barium aluminium fluoride silicate glass/Ytterbium fluoride and silicium oxide (20 nm–5 μm) |
Venus Pearl | 80/59 | Barium aluminium fluoride glass/highly discrete nanoparticles (5 nm–5 μm) |
2.1
Determination of filler content
The determination of inorganic content was carried out using two complementary methods, firstly, thermogravimetric analysis . Small amounts of material (typically 50–100 mg) were placed in a temperature-controlled chamber. The weight of material was monitored as temperature increased to 900 °C. Inorganic content ( W i , in wt%) was determined as the remaining weight of matter relative to the initial amount (n = 3). A transition located around 400 °C (typically between 380–480 °C) was also quantified and tentatively associated with the degradation of silanes (transition verified with Aerosil R 7200, Fig. 2 , also in line with other results ).
Given the limitations in filler processing techniques, it was assumed there would be a sharp step in filler distribution at about 500 nm, it being the lower bound in the range of sub-micron ground particles. Particles were separated around that threshold: fillers were extracted and their respective amounts determined by dissolving the resin composites in acetone and separating each filler type by gravimetry (>500 or <500 for particles with a size greater or smaller than 500 nm, respectively). Briefly, for one measurement, 0.3 g of resin composite was placed in 10 mL acetone (precision 0.0001 g). The tube was vortexed until all the material was fully dispersed. Two centrifugation cycles were employed, first to obtain the >500 fillers (3000 g for 1 min) followed by another (5000 g for 30 min) to collect <500 fillers. One should note that due to the limitation in centrifugation speed, some of the smallest non-aggregated nanoparticles may not have been collected. To completely remove any soluble content, once separated, the fillers were washed twice with acetone and re-centrifuged at high speed. Powders were recovered by allowing the suspensions to dry under a fume hood at room temperature for 24 h. Total weight filler content <SPAN role=presentation tabIndex=0 id=MathJax-Element-3-Frame class=MathJax style="POSITION: relative" data-mathml='(Wtotal)’>(Wtotal)(Wtotal)
( W t o t a l )
was then determined, corresponding to the sum of >500 and <500 fillers ( <SPAN role=presentation tabIndex=0 id=MathJax-Element-4-Frame class=MathJax style="POSITION: relative" data-mathml='W>500′>W>500W>500
W > 500
or <SPAN role=presentation tabIndex=0 id=MathJax-Element-5-Frame class=MathJax style="POSITION: relative" data-mathml='W<500′>W<500W<500
W < 500
respectively).
2.2
Filler size distribution and morphology
The separated fillers were characterized by laser diffraction and scanning electron microscopy (SEM). The first method informed on the size distribution of the >500 fillers and the second on the geometry of both filler types. For laser diffraction, >500 fillers were re-dispersed in ethanol, sonicated to maximise particle de-aggregation and analyzed using a particle size analyser (0.25–85 μm range, HELOS, Sympatec GmbH). The installed software (Windox 5, Sympatec GmbH) provided cumulative volume distributions <SPAN role=presentation tabIndex=0 id=MathJax-Element-6-Frame class=MathJax style="POSITION: relative" data-mathml='(Q(x))’>(Q(x))(Q(x))
( Q ( x ) )
, with x the particle size. To obtain distribution densities <SPAN role=presentation tabIndex=0 id=MathJax-Element-7-Frame class=MathJax style="POSITION: relative" data-mathml='(q(x))’>(q(x))(q(x))
( q ( x ) )
, which graphically are easier to interpret. Eq. (1) was used:
q ( x ) = d Q ( x ) d x
To transform the abscissa in a logarithmic scale. Eq. (2) was applied:
q ( ln ( x i − 1 ) , ln ( x i ) ) = Q ( x i ) − Q ( x i − 1 ) ln ( x i x i − 1 )
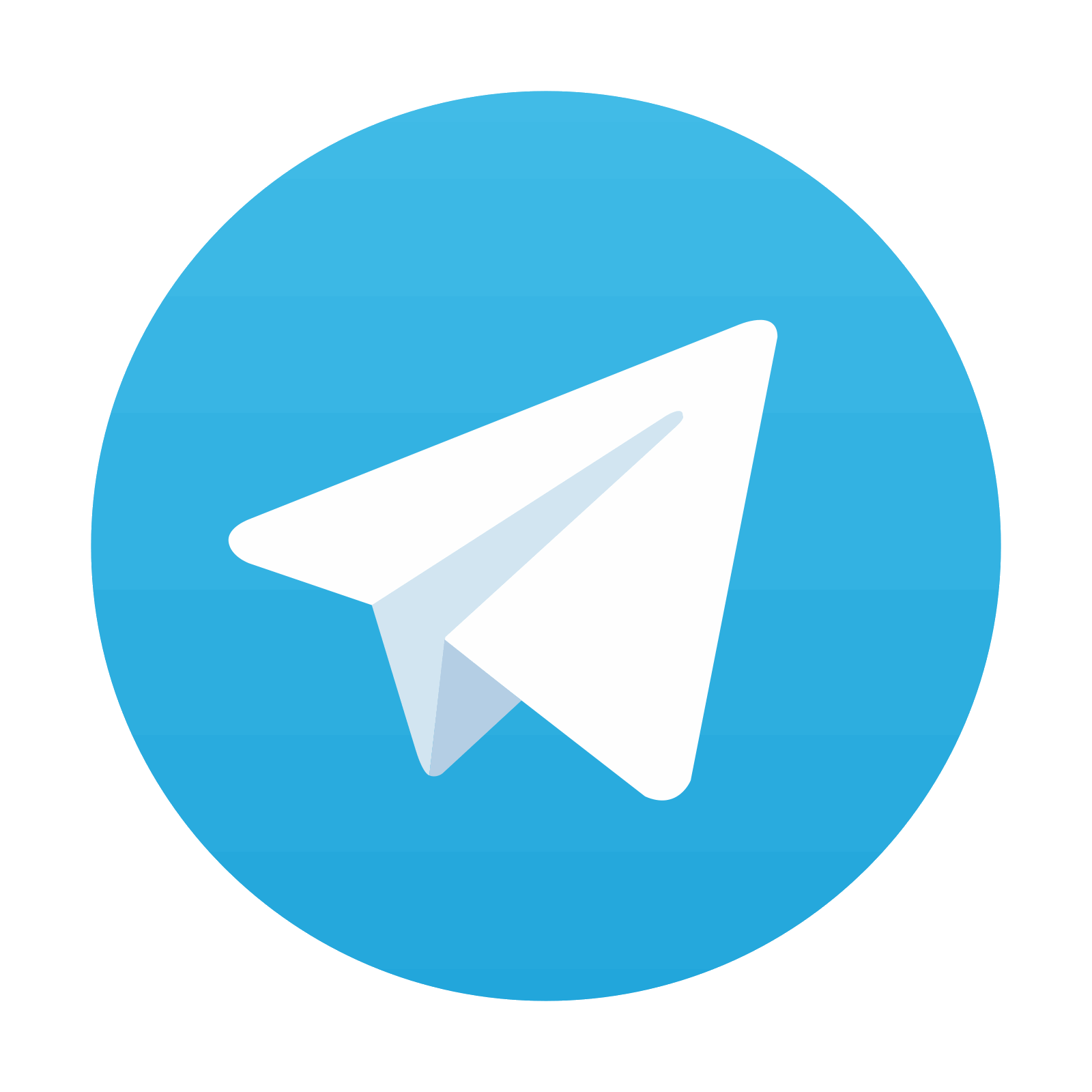
Stay updated, free dental videos. Join our Telegram channel

VIDEdental - Online dental courses
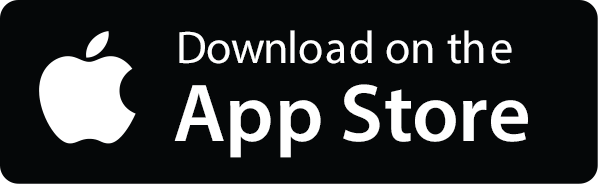
